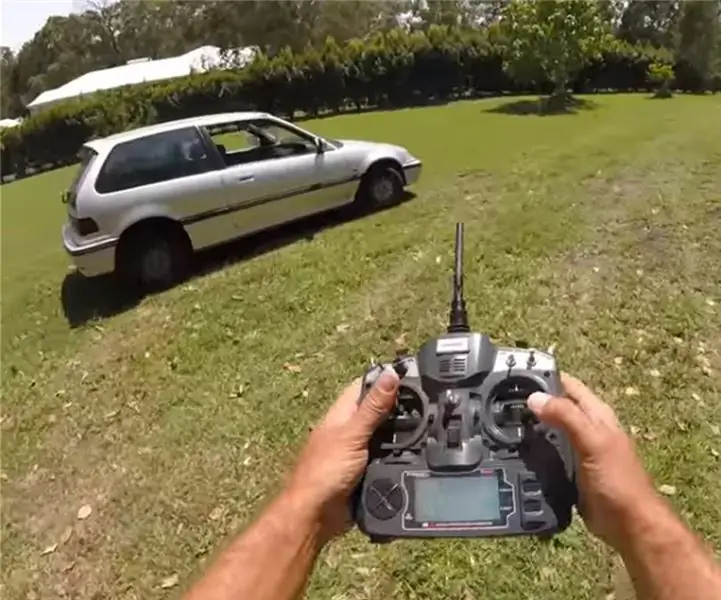
Sommario:
- Passaggio 1: sfondo
- Passaggio 2: competenze necessarie
- Passaggio 3: costo per costruire
- Passaggio 4: elenco delle parti
- Passaggio 5: componenti del sistema - Auto
- Passaggio 6: componenti del sistema - Configurazione della batteria ausiliaria (opzionale)
- Passaggio 7: componenti del sistema - Accensione
- Passaggio 8: componenti del sistema - Selettore marcia
- Passaggio 9: componenti del sistema - Freni
- Passaggio 10: componenti del sistema - Acceleratore
- Passaggio 11: componenti del sistema - Sterzo
- Passaggio 12: componenti del sistema - ricevitore/trasmettitore
- Fase 13: Programma finale
2025 Autore: John Day | [email protected]. Ultima modifica: 2025-01-23 14:49
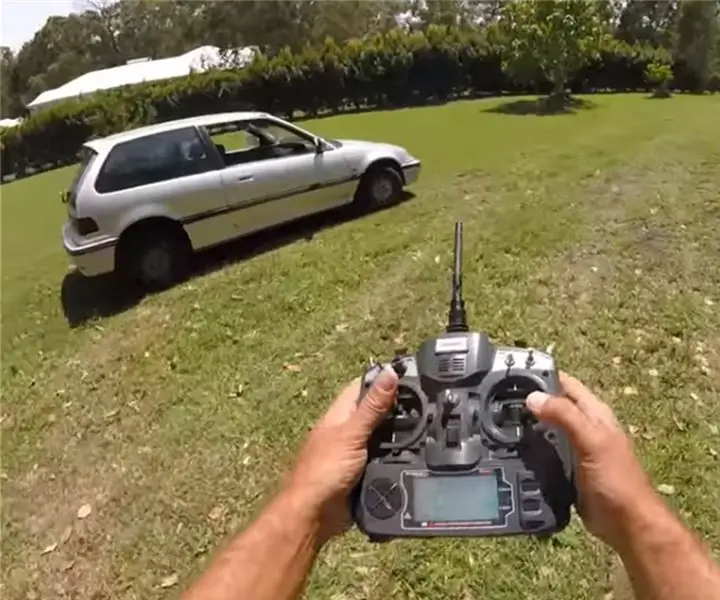
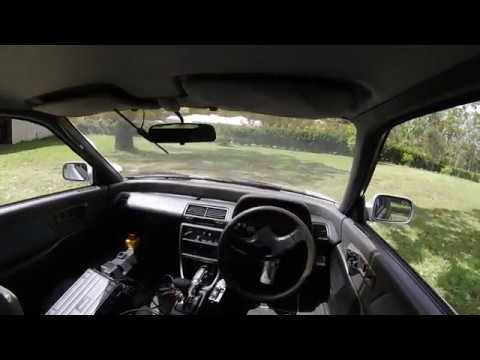
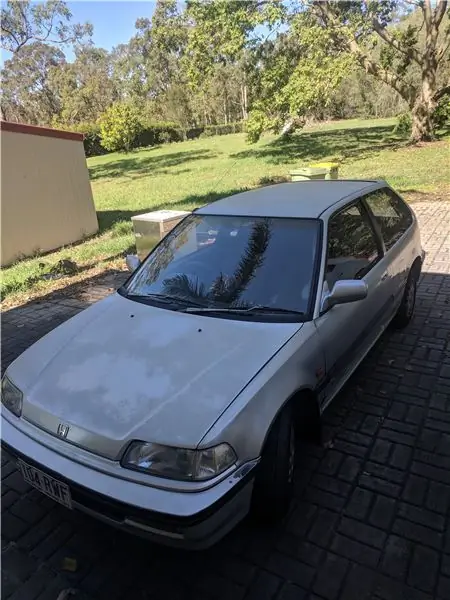
Che cos'è?
Pensi che le auto RC siano solo per bambini? Pensa di nuovo! Questo tutorial ti mostrerà come allestire e costruire un'auto RC 1: 1 a grandezza naturale. Dotare un'auto di questi controlli è una buona piattaforma di partenza per costruire la propria auto completamente autonoma (prossima fase).
NOTA: questa build si basa su un'auto non in stile "drive-by-wire". Se vuoi leggere il mio altro tutorial per un'auto "drive-by-wire", dai un'occhiata qui.
Passaggio 1: sfondo

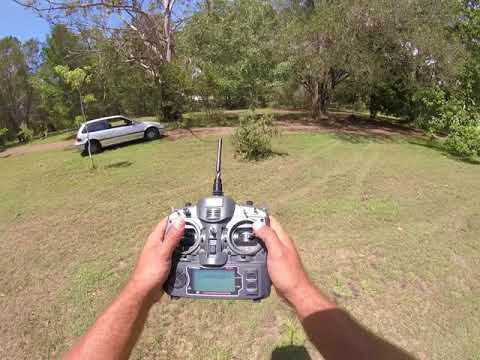
Ho sempre voluto costruire la mia auto a guida autonoma e non c'è modo migliore per iniziare che modificare una vecchia auto per gestire tutti i comandi senza un essere umano a bordo. Quindi, il primo passo è dotare un'auto di questi comandi e poi attivarli a distanza tramite RC.
Ho deciso di documentare questo processo per mostrare agli altri che la barriera all'ingresso per costruire un'auto autonoma è bassissima e non molto costosa (<$2k). Voglio che migliaia di persone costruiscano queste auto, così abbiamo molte più persone che hanno esperienza del mondo reale in meccatronica, informatica e ingegneria in generale.
Le mie abilità
- Costruito e restaurato oltre 8 auto e 10 moto
- Ho lavorato nella produzione per tutta la mia vita
- Montatore e tornitore qualificato
- Attrezzista qualificato
- Laurea in Informatica
- Fondatore di QRMV - specializzato in robotica industriale guidata dalla visione
- Co-fondatore/CTO di ollo wearables - cellulare a comando vocale per anziani/anziani (allerta vita moderna)
- Più brevetti (assegnati e provvisori) telefonia, geolocalizzazione e computer vision
Passaggio 2: competenze necessarie
Ho un background molto tecnico, ma penso che chiunque sia un po' pratico dovrebbe essere in grado di costruirne uno abbastanza facilmente. Se non hai tutte le competenze, la cosa facile da fare è chiedere ad altri che conosci di unirsi alla build. In questo modo puoi insegnarti a vicenda mentre procedi.
Meccanica: conosci la tua strada intorno a un'auto e ai suoi componenti e come funzionano insieme
Meccanico: essere in grado di utilizzare un'ampia varietà di utensili manuali ed elettrici (trapano, smerigliatrice, tornio, ecc.)
Elettronica: comprendere, progettare e costruire circuiti di base (selezione dei componenti, saldatura, ecc.)
Drafting - Essere in grado di disegnare componenti in CAD per essere lavorati da terze parti
Programmazione: essere in grado di creare semplici schizzi Arduino, utilizzare git, ecc
Passaggio 3: costo per costruire
In breve - <$ 2k. Il costo per costruire una di queste auto si riduce in realtà a quanto è possibile ottenere l'auto funzionante poiché è probabilmente la componente di costo più alta e più variabile nel progetto. Per la prima auto che ho costruito, sono riuscito a ritirare la mia piccola Honda Civic del 1991 per 300 dollari ed era ancora immatricolata.
Per tutti gli altri componenti di cui avrai bisogno sono per lo più "pronti allo scaffale", quindi i prezzi non varieranno troppo.
Passaggio 4: elenco delle parti
L'elenco completo delle parti e i fornitori/produttori sono disponibili qui.
- Auto (stile non drive-by-wire)
- Attuatore lineare (elettrico) - Selettore di marcia
- Attuatore lineare (elettrico) - Freni
- Servo (coppia elevata) - Acceleratore
- Modulo servosterzo elettronico - Sterzo
- Arduino Uno - Controlla l'integrazione del sistema
- Alimentatore regolato 5-6V ad alta corrente (5A) (per servo)
- Controller e ricevitore RC a 8/9 canali
- Batteria a ciclo profondo (opzionale)
- Batteria ausiliaria - Relè sensibile alla tensione (opzionale)
- Scatola batteria (opzionale)
- Isolatore di batteria
- Driver motore 60A (multidirezionale)
- Driver motore 2 x 32A (multidirezionale)
- 2 moduli relè da 30A 5V
- 2 x potenziometri scorrevoli
- 2 x potenziometri multigiro
- ~50A Interruttore o fusibile
- Pulsanti e contatti di arresto di emergenza
- Cavo (alta corrente per motori/batteria e multipolare per collegamento)
- Scatola dei fusibili per autoveicoli
- Barra piatta in acciaio (25x3mm e 50x3mm)
- Piastra in alluminio (3-4mm)
- Scatole in ABS per elettronica
- Manuale officina auto
Passaggio 5: componenti del sistema - Auto
Nota: per questo tutorial sto costruendo un'auto in stile non "drive-by-wire" essendo una Honda Civic del 1990. Se vuoi costruire su un'auto "drive-by-wire", rilascerò le mie informazioni sulla costruzione nei prossimi mesi.
Per l'auto che vuoi assicurarti che spunti quanto segue;
- L'auto si avvia, corre e può guidare (in caso contrario, falla funzionare)
- Ha il cambio automatico
- I freni funzionano
- L'alternatore è in buone condizioni
Passaggio 6: componenti del sistema - Configurazione della batteria ausiliaria (opzionale)
In questo tutorial utilizzerò una seconda batteria ausiliaria a ciclo profondo, ma questa è facoltativa. Ho scelto di farlo nella mia build poiché la batteria originale dell'auto era super piccola e c'era un accordo per ottenere una batteria a ciclo profondo con una configurazione del relè della batteria ausiliaria allo stesso prezzo di un'altra batteria. La cosa fondamentale qui è che si desidera una buona batteria funzionante e un alternatore nell'auto in grado di fornire corrente elevata quando necessario.
Innanzitutto, scollega la batteria dell'auto poiché lavoreremo su entrambi i terminali. Installare una batteria ausiliaria nell'auto è piuttosto semplice. Innanzitutto, trova un luogo adatto/sicuro per montare la seconda batteria all'interno dell'auto, del bagagliaio o, se hai spazio sufficiente, sotto il cofano.
Montare il relè sensibile alla tensione il più vicino possibile alla batteria di avviamento.
Utilizzare un filo di grosso spessore (6 AWG) per passare dal terminale positivo del connettore della batteria di avviamento al relè sensibile alla tensione. Quindi eseguire un altro pezzo del cavo di grosso spessore dal relè sensibile alla tensione alla batteria ausiliaria e collegare saldamente un terminale della batteria ad esso.
Il relè sensibile alla tensione dovrebbe avere un filo negativo che deve essere collegato alla massa dell'auto. Assicurati che questo filo/connettore abbia un buon contatto di terra.
Alla batteria ausiliaria, fai passare un filo di grosso spessore (6 AWG) dal terminale negativo a una parte del corpo metallico dell'auto e assicurati che abbia una massa solida (metallo nudo). Mettere connettori appropriati su entrambe le estremità e verificare che la messa a terra sia corretta.
Nota: assicurati che la batteria ausiliaria sia montata saldamente e non si muova durante la guida. Consiglio di metterlo in un vano batteria per tenerlo al sicuro e in ordine.
Consiglio vivamente di utilizzare un isolatore di batteria nel sistema per consentire un isolamento semplice e rapido dell'alimentazione. Posiziona questo in linea dall'alimentazione della batteria alla scatola dei fusibili del controller
Passaggio 7: componenti del sistema - Accensione

La maggior parte delle auto inizia con una chiave ruotata nell'accensione. Questo quindi applica energia a diversi componenti all'interno dell'auto, tra cui ECU, solenoide di avviamento, radio, ventole, ecc. Sostituiremo il sistema di chiavi con relè che possiamo attivare dal nostro Arudino.
Avrai bisogno degli schemi elettrici delle auto per eseguire questo lavoro ma normalmente puoi trovarli online facendo una rapida ricerca su Google o semplicemente acquistandone uno online. Ti consiglierei di ottenere il manuale di officina completo dell'auto in quanto includerà anche altre informazioni, inclusi eventuali suggerimenti/trucchi sulla rimozione di determinati componenti. Inoltre, è sempre bello avere a portata di mano le informazioni per diagnosticare e risolvere qualsiasi altro problema con l'auto che potresti incontrare.
Vorrei anche rimuovere completamente il piantone dello sterzo (compreso il barilotto di accensione, il gambo dell'indicatore, ecc.) essere lasciato in macchina.
Guarda gli schemi elettrici delle auto per l'accensione e determina il filo/i che alimentano l'accensione. Normalmente ci sarà un filo di alimentazione costante positivo fuso dalla batteria (IN) e poi un mucchio di altri fili che si alimentano per alimentare i componenti dell'auto nelle diverse fasi del ciclo di accensione/spegnimento dell'auto (Off, ACC, IGN1/Run, IGN2/Avvio). Calcola quali sono i cavi, poiché nella maggior parte delle auto più vecchie ti serviranno solo il cavo positivo Main IN, i cavi IGN1/Run e IGN2/Start per far funzionare l'auto, ma questo varia da auto a auto.
Per l'auto che avevo avevo bisogno solo di 3 fili in totale, ma fornivano corrente elevata, quindi avevo bisogno di alcuni relè pesanti per commutare il carico. I relè che ho finito per usare sono moduli da 30A 5V che ho trovato online. Volevo qualcosa in grado di gestire l'alta corrente ~ 30 A e che potesse essere commutato semplicemente da un segnale a 5 V.
Collegare i cavi di accensione ai relè secondo necessità. Controlla sempre che i relè funzionino prima di montarli poiché ho avuto più relè "morti all'arrivo" nella mia vita di costruzione di cose che mi sono letteralmente costate giorni della mia vita per trovare guasti.
Vorrai che questi relè funzionino in modi diversi. Il relè IGN1/Run nel mio sistema ha acceso tutte le centraline delle auto, la ventola del radiatore, il modulo di accensione che in un certo senso mi avrebbe permesso di accendere/spegnere le auto. Semplicemente, senza che l'alimentazione venga fornita al modulo di accensione, l'auto si avvia ma non si avvia mai. Il relè IGN2/Start era collegato direttamente al solenoide di avviamento che avrebbe effettivamente avviato il motore. Con questo relè vorresti solo averlo momentaneamente acceso per far funzionare l'auto, ma una volta che è in funzione vorresti disattivarlo in modo da non uccidere il motorino di avviamento.
test
Circuito: crea un semplice interruttore (IGN1/Run Relay) e un circuito a pulsante momentaneo (IGN2/Start) come input per il tuo Arduino
Programmazione - Scrivere un semplice script di test per testare il funzionamento di entrambi i relè senza la batteria di avviamento collegata. Una volta che sei sicuro del tuo circuito e del tuo script, collega la batteria di avviamento e provala. A questo punto dovresti essere in grado di avviare e fermare la tua auto.
Pietra miliare
A questo punto dovresti avere;
- IGN1/Run relè cablato
- Relè IGN2/Start cablato
- controllo di entrambe le operazioni di accensione/spegnimento dei relè tramite Arduino
- circuito di prova per controllare i relè
- essere in grado di avviare la macchina
- poter spegnere l'auto
Passaggio 8: componenti del sistema - Selettore marcia

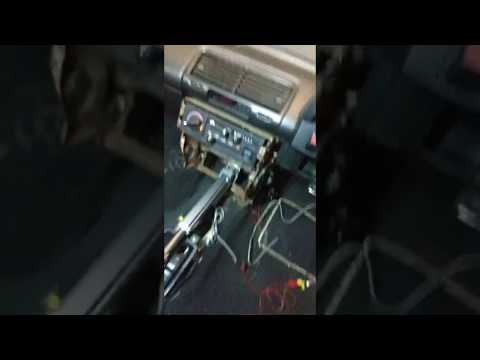
Poiché in questa versione utilizziamo un'auto con cambio automatico, è relativamente facile cambiare marcia poiché è sufficiente spostare la leva con un movimento lineare in determinati punti.
Nota: ho deciso di utilizzare la leva esistente e di non collegarmi direttamente al cavo di trasmissione poiché volevo mantenere l'auto dall'aspetto originale e gli interni il più normali possibile.
L'unica cosa difficile a cui potresti pensare è che la maggior parte delle trasmissioni automatiche richiede di premere un pulsante prima di poter spostare la leva di trasmissione. Poiché utilizziamo un attuatore lineare dotato di una vite senza fine, possiamo utilizzare la sua capacità di autobloccaggio per tenere in posizione la leva di trasmissione quando non la muove. Quindi, per quanto riguarda il pulsante, puoi bloccarlo permanentemente nello stato "depresso".
L'attuatore lineare qui utilizzato doveva avere una corsa sufficiente per passare dalla posizione di parcheggio a retromarcia, folle e quindi a marcia. Nel caso della mia auto era a circa 100 mm da dove stavo montando l'attuatore. La forza richiesta per spostare la leva era molto piccola (<5 kg), quindi ho finito per utilizzare un attuatore di 150 mm di corsa/70 kg di forza come era in stock.
Per montare la base dell'attuatore, ho saldato una staffa e l'ho fissata a una parte del telaio in acciaio che è stata utilizzata nella console centrale. Ciò gli ha permesso di ruotare leggermente mentre si estendeva / si ritraeva durante la sua corsa.
Per l'attacco alla leva di trasmissione ho solo tagliato un paio di pezzi di barra piatta in acciaio e ho usato un paio di bulloni per tenerla in posizione. Non è serrato con forza attorno alla leva, la sta solo contenendo. Ciò gli consente di muoversi e di non legarsi mentre si muove.
Per determinare la posizione dell'attuatore ho usato un potenziometro a scorrimento che avrebbe inviato un segnale analogico al mio Arduino. Ho realizzato un supporto personalizzato per il vaso sull'attuatore con una barra piatta. Ho quindi piegato le linguette del cursore delle pentole attorno al bullone della staffa di attacco della leva di trasmissione. Funziona ma dovrei cambiarlo per essere un accessorio migliore per il cursore dei vasi.
Per alimentare l'attuatore ho utilizzato un driver del motore che può andare avanti e indietro ed essere controllato tramite un microcontrollore. Ho usato un driver per motore Sabertooth 2x32A di Dimension Engineering, ma sentiti libero di usare qualsiasi cosa che funzioni in modo simile. Il primo canale sarà utilizzato per controllare l'attuatore del cambio e il secondo controllerà l'attuatore del freno. Il cablaggio e la configurazione di questo driver del motore sono semplici e ben documentati. Collegare il positivo e il negativo della batteria come etichettato e collegare i cavi degli attuatori all'uscita del motore 1. Collegare lo 0V alla messa a terra di Arduino e il cavo S1 a un pin di uscita digitale.
Nota: ho usato la semplice configurazione seriale su questa build e sembra funzionare abbastanza bene. Dimension Engineering ha anche creato un paio di librerie per rendere estremamente semplice la comunicazione con i propri autisti. Hanno anche alcuni semplici esempi per farti funzionare rapidamente.
test
Circuito - Per muovere avanti e indietro l'attuatore realizzare un semplice circuito con due pulsanti momentanei come ingressi. Uno per estendere l'attuatore e l'altro per ritrarre l'attuatore. Questo ti darà quindi un certo controllo sul posizionamento dell'attuatore nelle posizioni dell'ingranaggio.
Programmazione - Scrivere un semplice script per spostare l'attuatore avanti e indietro ed emettere il valore dal potenziometro scorrevole. Quando si esegue lo script, prendere nota dei valori del potenziometro per le posizioni del cambio Park, Reverse, Neutral e Drive. Avrai bisogno di questi per dire all'attuatore di spostarsi in queste posizioni nel codice completo.
Pietra miliare
A questo punto dovresti avere;
- attuatore montato saldamente in auto
- attacco attorno al selettore/attuatore del cambio
- driver del motore cablato con attuatore e Arduino
- controllo dell'estensione/retrazione dell'attuatore tramite Arduino
- circuito di prova per controllare l'estensione/retrazione dell'attuatore
- conoscere i valori/posizioni del potenziometro per ogni posizione di marcia
Nota: puoi anche utilizzare un circuito interruttore multiposizione per testare l'ingresso del selettore di marcia sul tuo Arduino una volta che conosci le posizioni. In questo modo sarai in grado di copiare il codice del selettore delle marce direttamente nella base del codice dell'auto in esecuzione completata.
Passaggio 9: componenti del sistema - Freni
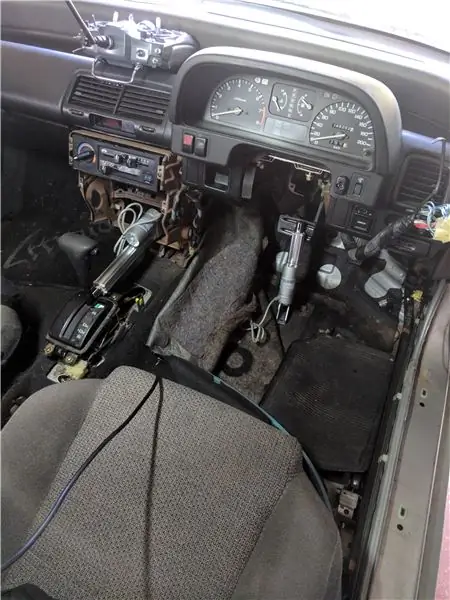
Fermare l'auto è piuttosto importante, quindi devi assicurarti di fare bene questa cosa. I freni di un'auto sono normalmente azionati dal tuo piede che può applicare una grande quantità di forza quando richiesto. In questa build stiamo usando un altro attuatore lineare che agirà a piedi. Questo attuatore doveva avere un'elevata quantità di forza (~30kg) ma necessitava solo di una corsa breve ~60mm. Sono stato in grado di ottenere un attuatore con corsa da 100 mm/forza da 70 kg poiché era in stock.
Trovare il posto giusto per montare l'attuatore è stato un po' difficile, ma con alcuni tentativi ed errori ho trovato una posizione sicura. Ho saldato un pezzo di barra piatta d'acciaio sul lato del braccio del pedale del freno e ho praticato un foro attraverso di esso dove ho inserito un bullone dalla parte superiore dell'attuatore. Ho quindi saldato una staffa di montaggio a perno sull'altra estremità dell'attuatore alla planimetria dell'auto.
Per determinare la posizione dell'attuatore ho usato un potenziometro a scorrimento (stessa configurazione dell'attuatore del selettore di marcia) che avrebbe inviato un segnale analogico al mio Arduino. Ho realizzato un supporto personalizzato per il vaso sull'attuatore con una barra piatta. Ho quindi piegato le linguette del cursore delle pentole attorno a una piccola linguetta piatta che ho montato all'estremità dell'attuatore.
Per alimentare l'attuatore ho utilizzato l'altro canale del Sabertooth Motor Driver 2x32A. Per controllare entrambi i motori è sufficiente utilizzare un solo filo (S1).
Nota: ho usato la semplice configurazione seriale su questa build e sembra funzionare abbastanza bene. Questo driver motore può essere configurato in diversi modi, quindi scegli un metodo che preferisci.
test
Posizionamento - Prima di collegare l'attuatore direttamente al pedale del freno, è necessario avere un'idea di quanto deve percorrere il pedale per applicare i freni. Ho premuto il piede sui freni per far fermare la macchina (mantenendo l'arresto, non tutti i freni). Ho quindi spostato l'attuatore per allineare il suo supporto di connessione con l'attacco del freno saldato. Ho registrato il valore di uscita del potenziometro, quindi ho conosciuto la mia posizione di massima depressione del freno.
Ho fatto lo stesso come sopra per la posizione di disattivazione del freno.
Circuito - Per muovere avanti e indietro l'attuatore realizzare un semplice circuito con due pulsanti momentanei come ingressi. Uno per estendere l'attuatore e l'altro per ritrarre l'attuatore. Questo ti darà quindi un certo controllo sul posizionamento dell'attuatore nelle posizioni dell'ingranaggio.
Programmazione - Scrivere un semplice script per spostare l'attuatore avanti e indietro ed emettere il valore dal potenziometro scorrevole. Quando si esegue lo script, prendere nota dei valori del potenziometro per le posizioni di attivazione e disattivazione del freno. Avrai bisogno di questi per dire all'attuatore di spostarsi in queste posizioni nel codice completo.
Pietra miliare
A questo punto dovresti avere;
- attuatore montato saldamente in auto
- attacco per il pedale del freno all'attuatore
- driver del motore cablato con attuatore e Arduino
- controllo dell'estensione/retrazione dell'attuatore tramite Arduino
- circuito di prova per controllare l'estensione/retrazione dell'attuatore
- conoscere i valori/posizioni del potenziometro per le posizioni di disattivazione e disattivazione del freno
Nota: nel codice finale utilizzo il segnale dei controller RC dal canale per controllare quanta pressione applicare al freno proporzionalmente alla sua posizione dello stick. Questo mi ha dato la gamma da completamente spento fino a completamente acceso.
Passaggio 10: componenti del sistema - Acceleratore
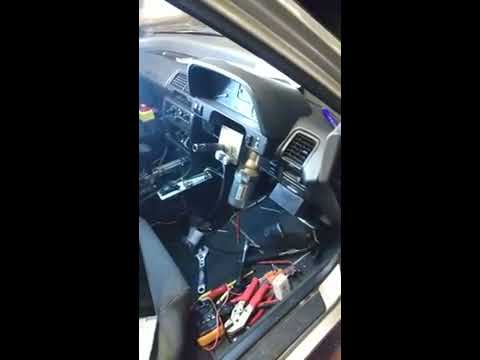
Ora mettiamo in moto quei motori e per farlo dobbiamo collegare l'acceleratore. Poiché stiamo utilizzando un'auto non "drive-by-wire", in realtà tireremo un cavo collegato al corpo farfallato. I corpi farfallati normalmente hanno una molla forte che chiude la farfalla molto velocemente quando si rilascia l'acceleratore. Per superare questa forza ho usato un servo ad alta coppia (~40kg/cm) per tirare il cavo.
Ho imbullonato questo servo su un pezzo di barra piatta in acciaio e l'ho montato sul lato della console centrale con alcune staffe ad angolo retto. Avevo anche bisogno di acquistare un cavo dell'acceleratore più lungo (2 m) poiché il cavo di serie utilizzato nell'auto era troppo corto. Questo mi ha anche dato molte più opzioni di montaggio che mi hanno fatto risparmiare molto tempo.
Tieni presente che questi servi a coppia elevata normalmente tirano più in alto della corrente normale, quindi assicurati di poterla fornire in modo appropriato. Ho usato un alimentatore regolato 5V 5A per questo che gli fornisce facilmente abbastanza corrente per funzionare a piena coppia. Il cavo del segnale dal servo è stato quindi riportato a un'uscita digitale dell'Arduino.
test
Programmazione: scrivi un semplice script per ruotare il servo dalla posizione di spegnimento dell'acceleratore a completamente (se sei un gioco). Ho aggiunto un parametro di configurazione dell'acceleratore che limiterebbe la quantità di movimento che il servo avrebbe dovuto permettermi di regolare rapidamente la sensazione dell'acceleratore.
Pietra miliare
A questo punto dovresti avere;
- servo montato saldamente
- cavo dell'acceleratore collegato dal corpo farfallato al braccio del servocomando
- alimentatore collegato per fornire corrente sufficiente al servo
- controllo della posizione del servo tramite Arduino
- posizioni note per servo per acceleratore spento e completamente acceso
Nota: nel codice finale utilizzo il segnale dei controller RC dal canale per controllare la quantità di movimento da applicare all'acceleratore proporzionalmente alla sua posizione dello stick. Questo mi ha dato l'intervallo da completamente spento fino a completamente acceso con il parametro di configurazione dell'acceleratore come limitatore.
Passaggio 11: componenti del sistema - Sterzo
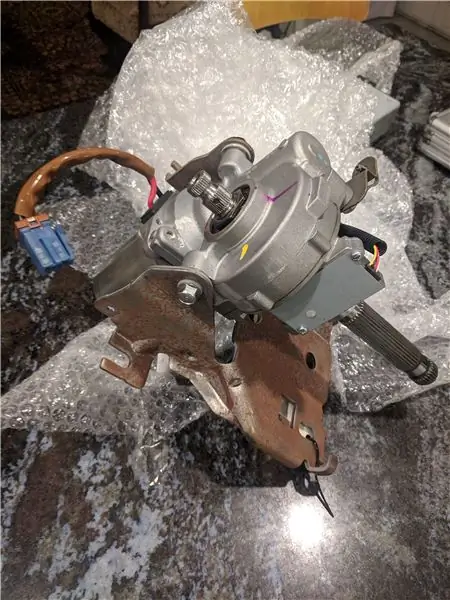

Essere in grado di guidare l'auto dove vogliamo che vada è piuttosto importante. La maggior parte delle auto prodotte in passato (pre ~ 2005) utilizzava il servosterzo idraulico per rendere la rotazione del volante molto leggera per l'utente. Da allora, a causa della tecnologia e delle richieste alle case automobilistiche di ridurre le emissioni, hanno sviluppato sistemi di servosterzo elettronico (EPS). Questi sistemi utilizzano un motore elettrico e un sensore di coppia per aiutare il conducente a girare le ruote. Rimuovendo la pompa del servosterzo idraulico, ora c'è meno sforzo sul motore che a sua volta consente all'auto di funzionare a regimi più bassi (riducendo le emissioni). Puoi leggere di più sui sistemi EPS qui.
Nella configurazione per guidare la mia piccola auto ho usato un sistema di servosterzo elettronico (EPS) di una Nissan Micra del 2009. L'ho acquistato da un demolitore di auto/scrapyard per $ 165. Ho montato questo modulo EPS sui bulloni di montaggio del piantone dello sterzo esistenti tramite un supporto che ho piegato su una barra piatta d'acciaio.
Avevo anche bisogno di acquistare l'albero inferiore del piantone dello sterzo (~ $ 65) per collegare l'EPS alla scanalatura della cremagliera dello sterzo. Per adattarlo alla mia auto ho modificato l'albero del piantone dello sterzo tagliando e saldando la scanalatura del piantone dello sterzo originale che ho ritagliato dalla Honda a questo albero.
Per alimentare/controllare il motore EPS a sinistra oa destra ho utilizzato un controller per driver motore Sabertooth 2x60A di Dimension Engineering. Ho usato solo uno dei canali, ma è necessario assicurarsi di utilizzare un driver del motore in grado di fornire continuamente ~60A+, lavorare in direzione avanti/indietro e può anche essere controllato tramite un microcontrollore.
Per conoscere la posizione dell'angolo di sterzata ho progettato un sensore di posizione dell'angolo di sterzata personalizzato. La maggior parte delle auto utilizza una versione digitale che funziona tramite il bus CAN che non potrei essere disturbato dal reverse engineering. Per il mio sensore di posizione analogico ho usato 2 potenziometri multigiro (5 giri), 3 pulegge per cinghie dentate, una cinghia dentata e una piastra in alluminio su cui montare i componenti. Ogni ingranaggio della distribuzione ho praticato e filettato fori per i grani e poi sulle pentole e sull'EPS ho lavorato dei piani per impedire agli ingranaggi di girare liberamente. Questi sono stati poi collegati tramite una cinghia di distribuzione. Quando il volante è stato centrato, i vasi sarebbero a 2,5 giri. Quando era al blocco dello sterzo completamente a sinistra sarebbe a 0,5 giri e al blocco completamente a destra sarebbe a 4,5 giri. Questi vasi sono stati poi collegati agli ingressi analogici dell'Arduino.
Nota: il motivo per l'utilizzo di due pentole era che se la cintura scivolava o si rompeva, potevo leggere le differenze tra le pentole e generare un errore.
test
Posizionamento - Prima di collegare l'EPS al piantone dello sterzo inferiore e alla cremagliera dello sterzo dell'auto, è meglio testare il codice per l'EPS e il sensore dell'angolo di sterzata scollegati.
Circuito - Per ruotare l'EPS a sinistra oa destra, creare un semplice circuito con due pulsanti momentanei come input. Uno per ruotare l'EPS a sinistra e l'altro per ruotare a destra. Questo ti darà quindi un certo controllo sul posizionamento dell'EPS nelle posizioni di guida.
Programmazione - Scrivi un semplice script per posizionare il volante al centro, a sinistra ea destra. Dovrai controllare la quantità di potenza che viene data al motore poiché ho scoperto che il 70% era più che sufficiente per girare le ruote mentre l'auto era ferma. L'erogazione di potenza all'EPS richiederà anche una curva di accelerazione/decelerazione per posizionare agevolmente lo sterzo.
Pietra miliare
A questo punto dovresti avere;
- Sistema di servosterzo elettronico (EPS) montato saldamente
- piantone dello sterzo inferiore modificato per guidare dall'EPS alla cremagliera dello sterzo
- sensore di posizione dell'angolo di sterzata che fornisce l'angolo della cremagliera di sterzo ad Arduino
- driver del motore cablato con EPS e Arduino
- controllo della rotazione dell'EPS tramite Arduino
- circuito di prova per controllare il senso di rotazione dell'EPS
- gira lo sterzo dell'auto completamente a sinistra in posizione di blocco, centrale e completamente a destra tramite Arduino
Passaggio 12: componenti del sistema - ricevitore/trasmettitore
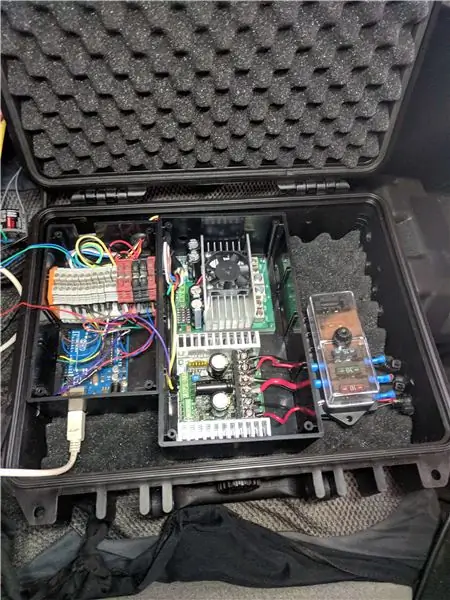
Passiamo ora alla parte divertente che lega tutto il lavoro che hai svolto finora. Il telecomando è la prima fase di rimozione della componente umana della guida poiché i comandi verranno ora inviati al ricevitore e quindi inseriti nell'Arduino per essere azionati. Nella seconda fase di questa serie sostituiremo il trasmettitore/ricevitore umano e RC con un computer e sensori per controllare dove va. Ma per ora vediamo come configurare il trasmettitore e il ricevitore RC.
Per controllare i componenti che abbiamo costruito all'interno dell'auto fino ad ora abbiamo bisogno di collegare i canali di uscita del ricevitore RC ad Arduino. Per questa build ho finito per utilizzare solo 5 canali (acceleratore e freno sullo stesso canale), sterzo, selettore marce (interruttore a 3 posizioni), stadio di accensione 1 (alimentazione/funzionamento dell'auto) e stadio di accensione 2 (avviamento dell'auto). Questi sono stati tutti letti da Arduino utilizzando la funzione PulseIn dove richiesto.
test
Programmazione - Scrivi un semplice script per leggere tutti i canali del ricevitore che stai utilizzando per controllare i tuoi sistemi all'interno dell'auto. Una volta che puoi vedere tutti i canali del ricevitore funzionare correttamente puoi iniziare ad integrare il codice che hai creato in precedenza con il codice del ricevitore. Un buon punto di partenza è con il sistema di accensione. Sostituisci la lettura degli ingressi dall'interruttore e dal pulsante nel circuito di prova che hai creato con i canali del ricevitore RC che hai impostato per controllare il sistema di accensione (IGN1/Run e IGN2/Start).
Nota: se usi il trasmettitore Turnigy 9x come ho fatto io, vorrai smontarlo e spostare un paio di interruttori. Ho scambiato l'interruttore momentaneo "Trainer" con l'interruttore "Throttle Hold" per controllare l'ingresso IGN2/Start. L'ho fatto perché non potevi programmare l'interruttore "Trainer" come interruttore ausiliario, ma potresti farlo con l'interruttore "Mantenimento del gas". Avere un interruttore momentaneo per l'ingresso IGN2/Start mi ha permesso di non distruggere il motorino di avviamento poiché avrebbe solo bloccato il relè in alto mentre
Pietra miliare
A questo punto dovresti avere;
- Tutte le uscite del ricevitore collegate ad Arduino
- Arduino in grado di leggere gli ingressi per ogni canale
- Ogni canale è in grado di controllare ogni componente dell'auto (freni, selettore marce ecc.)
Fase 13: Programma finale

Questo bit dipende da te, ma sotto troverai un link al mio codice che ti aiuterà come punto di partenza di base per far funzionare la tua auto.
Consigliato:
Come realizzare un BB8 a grandezza naturale con Arduino: 12 passaggi
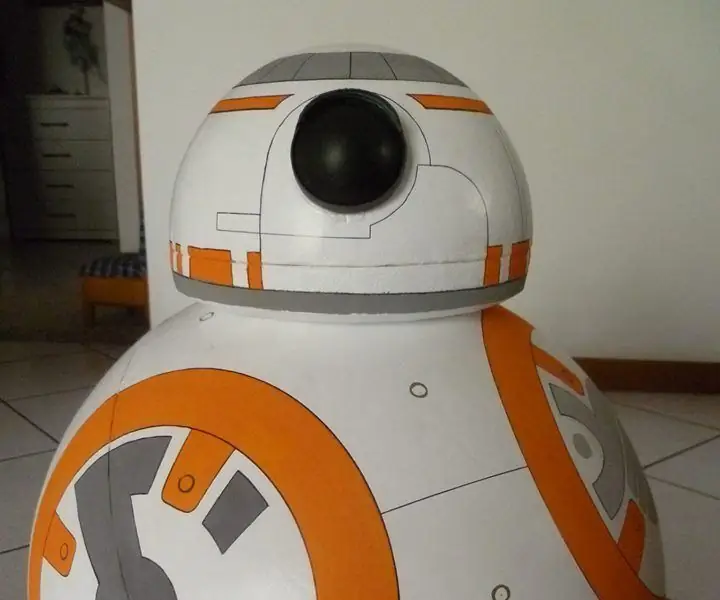
Come realizzare un BB8 a grandezza naturale con Arduino: Ciao a tutti, siamo due studenti italiani che hanno costruito un clone BB8 con materiali economici e con questo tutorial vogliamo condividere la nostra esperienza con voi! Abbiamo utilizzato materiali economici a causa della nostra limitata budget, ma il risultato finale è molto buono
Costruisci BB-8 fai da te in India -- Controllato da Android e loquace -- A grandezza naturale: 19 passaggi (con immagini)
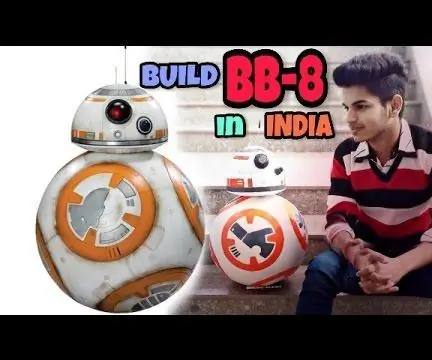
Costruisci BB-8 fai da te in India || Controllato da Android e loquace || A grandezza naturale: ISCRIVITI al mio canale per altri progetti. Questo progetto riguarda come costruire un droide Starwars BB-8 funzionante, a grandezza naturale, loquace e controllato da Arduino. useremo solo materiali domestici e un po 'di circuiti Arduino. In questo siamo
ASPIR: Robot umanoide a grandezza naturale stampato in 3D: 80 passaggi (con immagini)
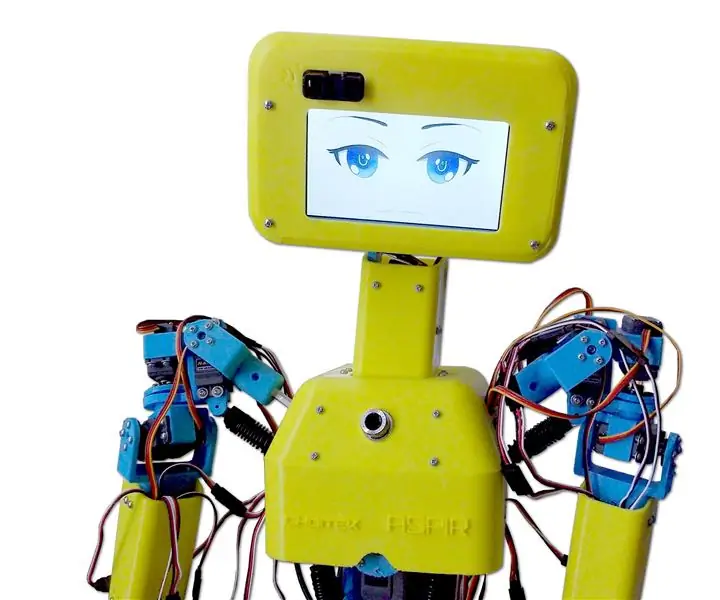
ASPIR: Robot umanoide stampato in 3D a grandezza naturale: Robot di supporto autonomo e ispirazione positiva (ASPIR) è un robot umanoide stampato in 3D open source a grandezza naturale di 4,3 piedi che chiunque può costruire con sufficiente grinta e determinazione. ho diviso questo enorme Instructable in 80 passaggi in 10 e
Modello a grandezza naturale Jason Vorhees/Venerdì 13 Halloween con Tv/dvd da 15,4 pollici e testa mobile Servo/arduino: 6 passaggi
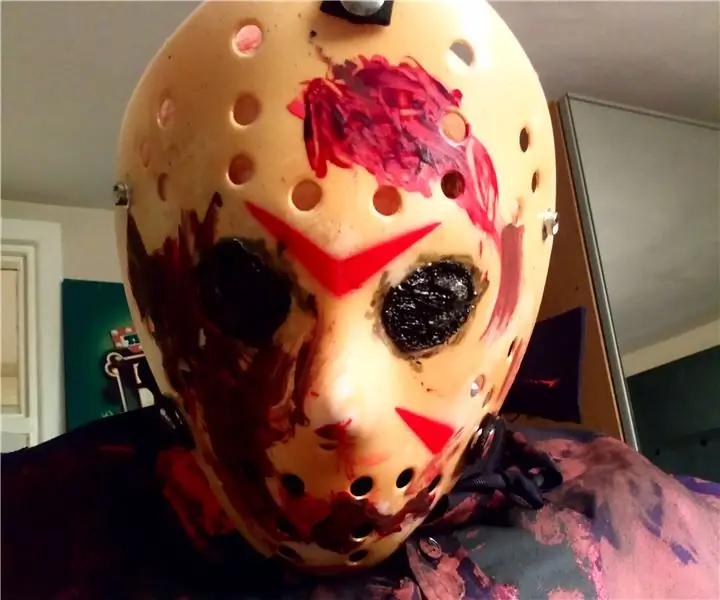
Jason Vorhees a grandezza naturale/modello di Halloween del venerdì 13 con stomaco da 15,4 pollici TV/dvd e servo/testa mobile arduino: piedistallo permanente/seduto a grandezza naturale Jason Vorhees con una combinazione tv/dvd integrata… anche un servo collo alimentato da arduino per realizzare Jason cerca la sua prossima vittima
Gioco operativo a grandezza naturale: 14 passaggi (con immagini)
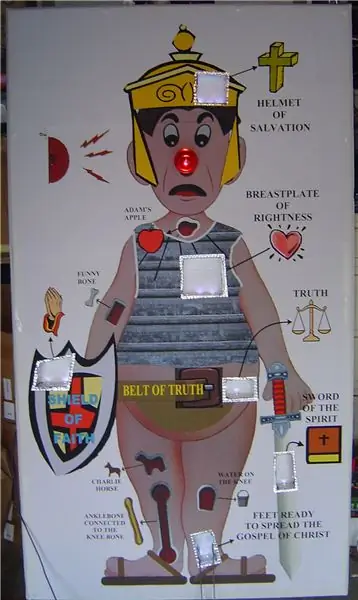
Gioco dell'operazione a grandezza naturale: da bambino adoravo il gioco dell'operazione Milton Bradley, il cicalino mi faceva sempre paura quando suonava, ma era divertente. Lo scopo del gioco Operazione è rimuovere una parte del corpo senza toccare con le pinzette i lati metallici che circondano l'oggetto