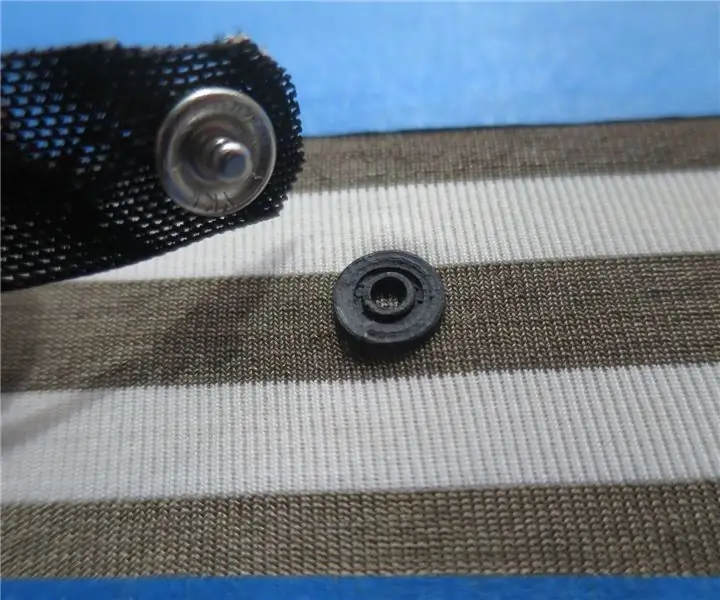
Sommario:
- Passaggio 1: file Fusion360
- Passaggio 2: test di stampa e configurazione
- Passaggio 3: stampa 3D su una traccia di tessuto conduttivo
- Passaggio 4: test di conduttività
- Passaggio 5: stampa su superfici diverse
- Passaggio 6: test di stampa multipla
- Passaggio 7: leggere la resistenza
- Passaggio 8: riattaccare gli snap con resina epossidica conduttiva
- Passaggio 9: conclusione e passaggi successivi
2025 Autore: John Day | [email protected]. Ultima modifica: 2025-01-23 14:50
Di rachelfreirewww.rachelfreire.comSegui altro dell'autore:
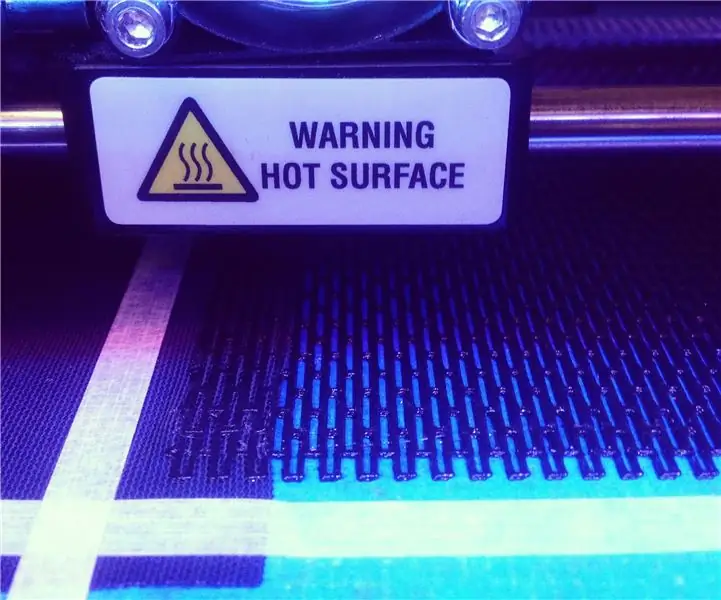
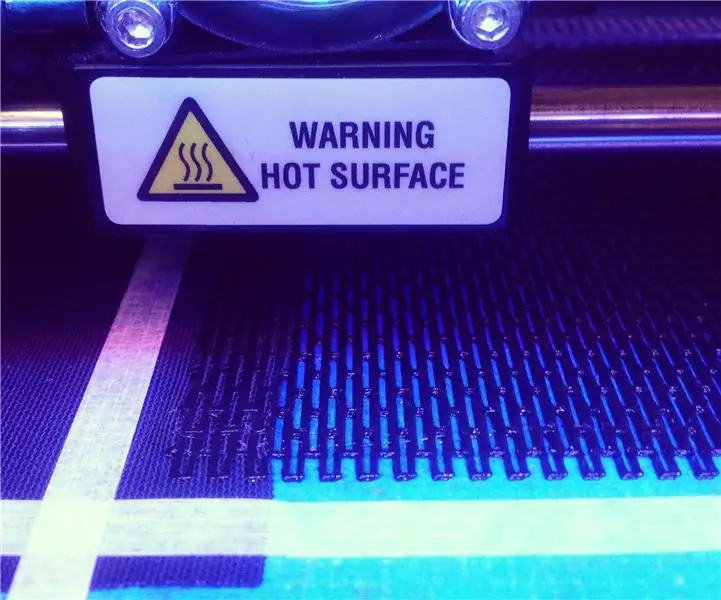
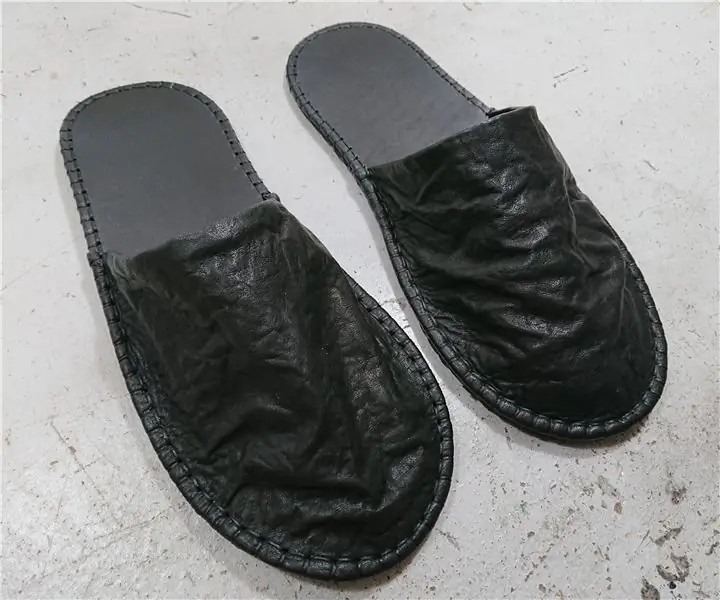
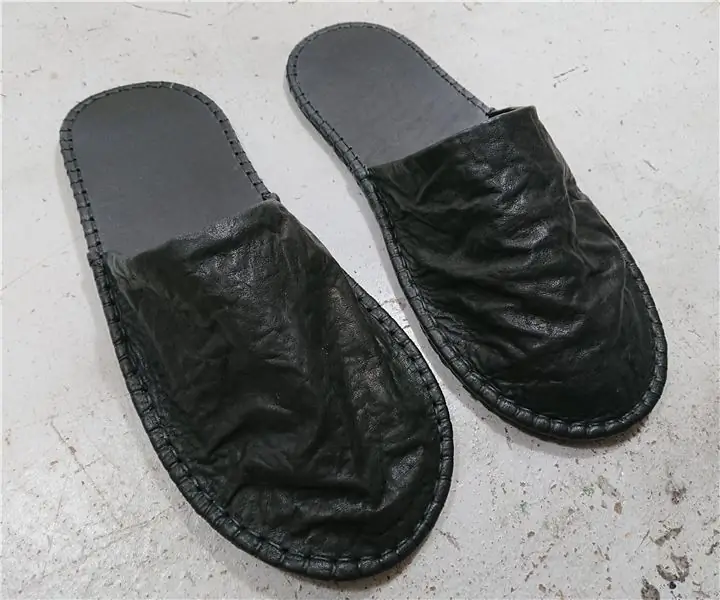
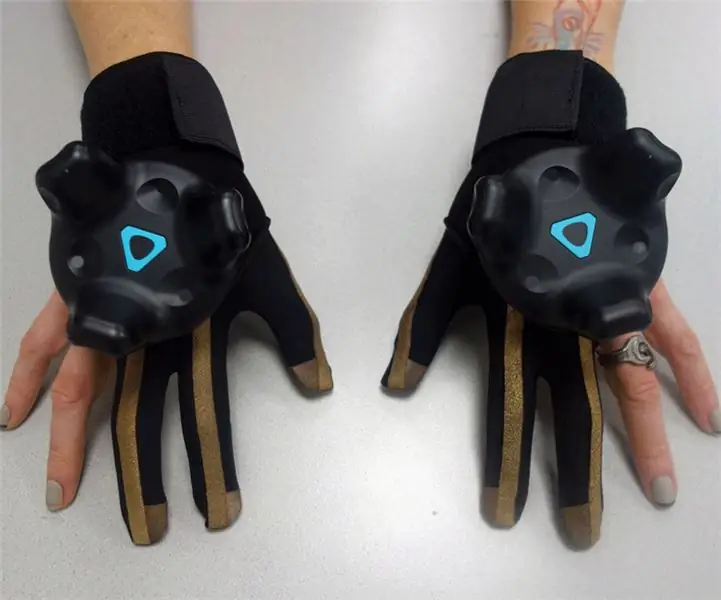
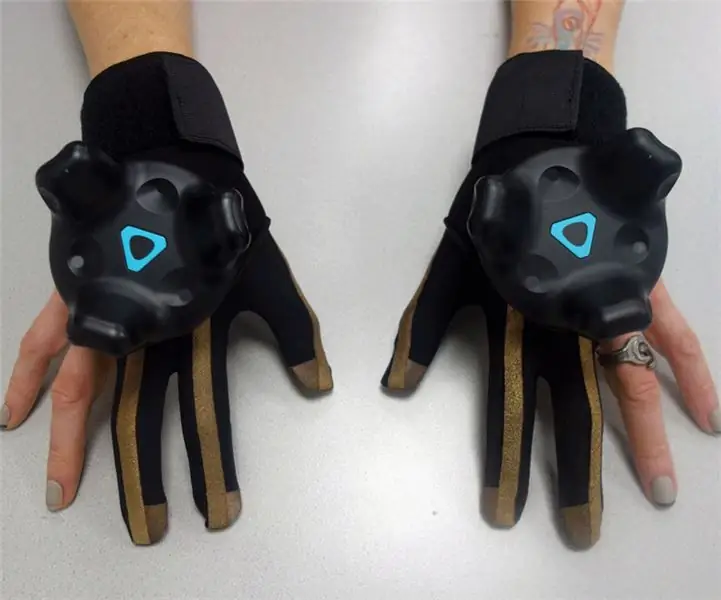
Informazioni su: designer, ninja in pelle, esploratore tecnologico, rovinatore di manicure Altro su rachelfreire »
Questa guida documenta il mio primo tentativo di stampare in 3D scatti conduttivi su tessuto. Volevo stampare in 3D uno scatto femmina che si collegasse a un normale scatto maschio in metallo.
Il file è stato modellato in Fusion360 e stampato su Makerbot Rep2 e Dremel utilizzando il PLA conduttivo di grafene 3D Black Magic.
I bottoni automatici sono bottoni automatici YKK "Snapet" aperti (taglia 12L) e hanno un diametro di 7,5 mm. Sono spesso utilizzati dai professionisti di eTextiles in quanto sono i più piccoli disponibili. Puoi acquistarli in diverse dimensioni da diversi fornitori, ma sembrano essere un design standardizzato. Acquista qui la taglia 12.
Il mio obiettivo è esplorare modi per realizzare un capo che sia conduttivo ed elastico e che preferibilmente non utilizzi parti metalliche dure. La realizzazione di connettori compatibili con gli snap acquistabili esistenti renderà più facile il test e l'iterazione.
Questo test ha funzionato sorprendentemente bene e vale la pena stampare il file, ma ha sicuramente bisogno di molte più modifiche. Per ora può essere stampato e testato così com'è, ma è sicuramente una prova di concetto piuttosto che uno snap perfettamente funzionante che può essere stampato in modo affidabile, ad es. il PLA tende a ridursi e gli snap hanno una durata limitata.
Se stampi questo file per favore lascia un commento e dimmi le tue scoperte!!
Altre immagini qui:
Queste esplorazioni fanno parte di un progetto più ampio chiamato Second Skin, una tuta di prototipazione per eTextiles. Caricherò tutti i file, i modelli e la documentazione non appena saranno completati. Puoi seguire il progetto qui, o tramite il mio sito web:
Dovresti anche dare un'occhiata a Rewear di Lara Grant. Ha lavorato su un sistema modulare per dispositivi indossabili basato su una breadboard di scatti stampati in 3D su tessuto. Si è anche concentrata sulla sostenibilità di queste tecniche che è qualcosa che vedo anche come parte integrante del loro sviluppo futuro. Presto integreremo i nostri esperimenti in un sito Web dedicato ai connettori etextile, quindi assicurati di controllare anche il sito Web di Lara e Instructables!
Passaggio 1: file Fusion360
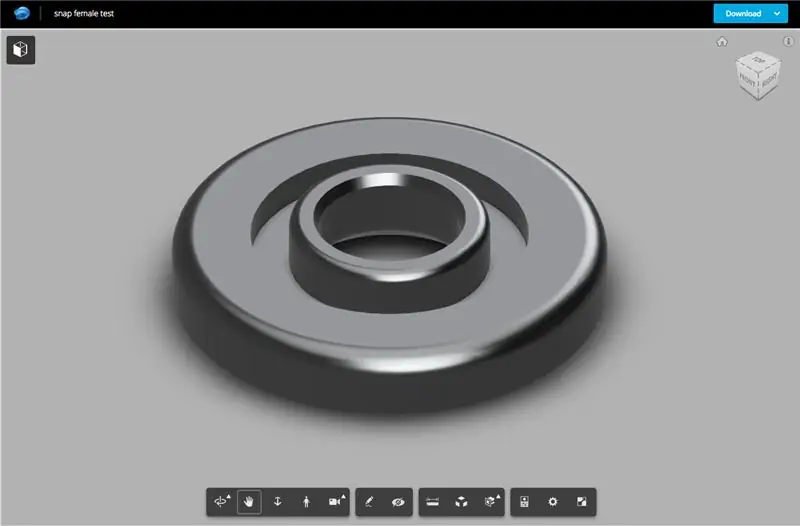
Il file è stato modellato abbastanza rapidamente utilizzando Fusion360.
Ho preso quante più misurazioni possibili da uno snap esistente e ho fatto un progetto approssimativo. Poiché lo snap è così piccolo, alcune delle proporzioni interne sono state realizzate utilizzando supposizioni e quindi avranno bisogno di più giochi.
Link per scaricare la versione corrente qui:
Il file allegato a questo Instructable è stato il mio primo tentativo. Ha funzionato abbastanza bene. Il file collegato (sopra) è stato ottimizzato, rendendo la base dello snap più solida. l'idea è che lo aiuterebbe ad aderire meglio al tessuto. Anche se questo ha aiutato in qualche modo, vale comunque la pena testare entrambi i file se si desidera stampare una versione di questo. Ho avuto successo e fallimenti con entrambi.
Sottolineerò anche che sono un totale principiante di Fusion e ho avuto l'aiuto di un ninja per modificare il file da JON-A-TRON. Dovresti assolutamente dare un'occhiata alle sue lezioni di stampa 3D!
Se si desidera utilizzare snap più grandi (come 15 mm che sono più comuni) mi aspetto che questo file possa essere ridimensionato e stampato con le dimensioni corrette e che si agganci anche a versioni più grandi di questo design a scatto. Non l'ho ancora provato perché sto cercando di rendere tutto il più piccolo possibile.
Questi snapets di metallo sono fantastici, ma spesso il dado è difficile da trovare. Uso le pinze Prym vario per applicare gli snap a mano ed è difficile trovare il dado a scatto adatto. Quindi ho creato un file di fusione stampabile per gli Snapets da 12 litri;) Ancora una volta, non è perfetto poiché le stampe 3D tendono a restringersi e deformarsi e alla fine si rompono. Ma ne ho appena stampati di nuovi quando ciò accade! I file sono allegati per l'interno (parte del connettore) e l'esterno (attacco dell'anello) die. Uno è una frazione più grande dell'altro. Se li usi al contrario, lo snap si incastrerà nel dado.
Passaggio 2: test di stampa e configurazione
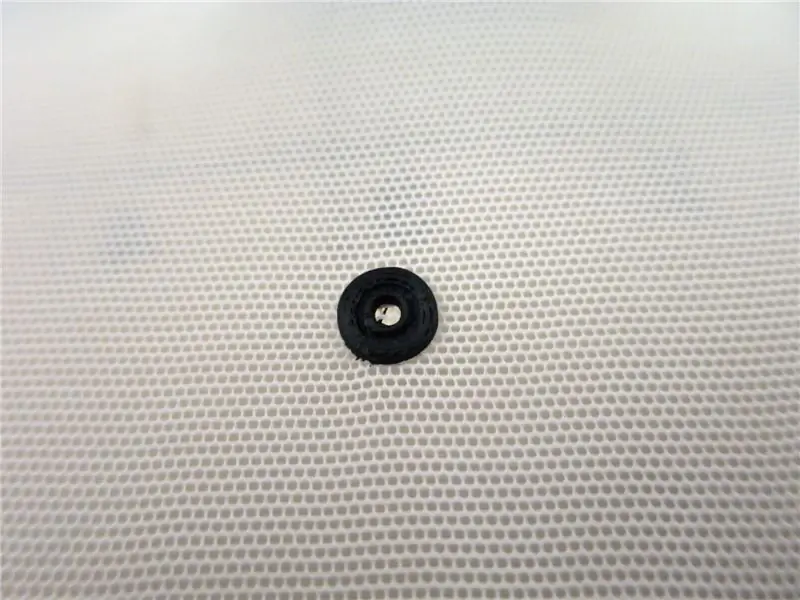
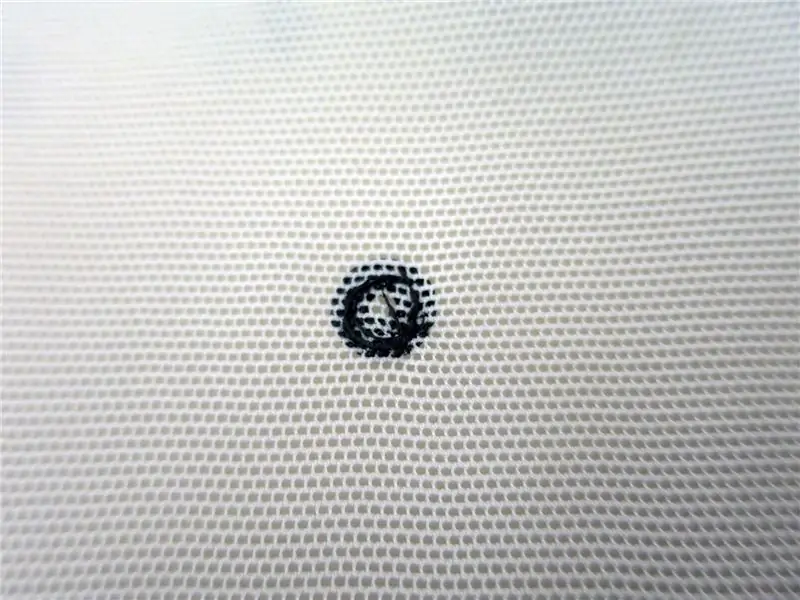
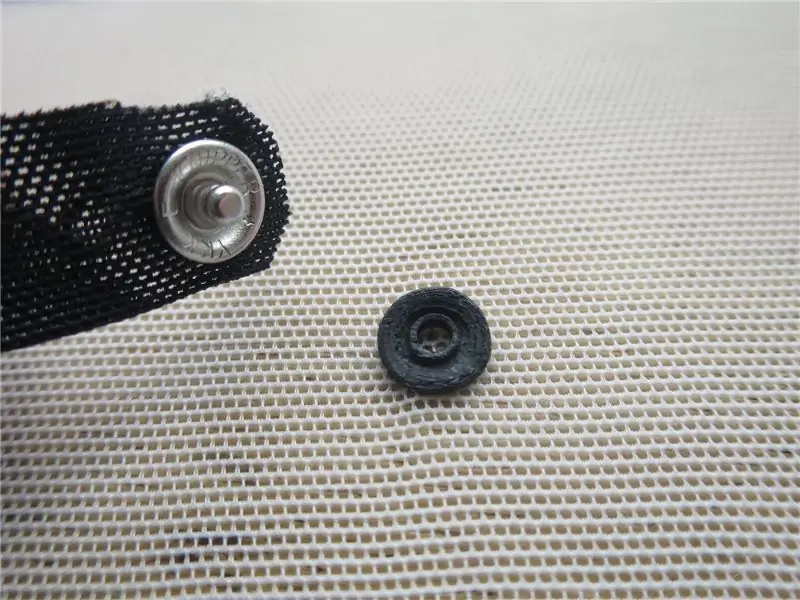
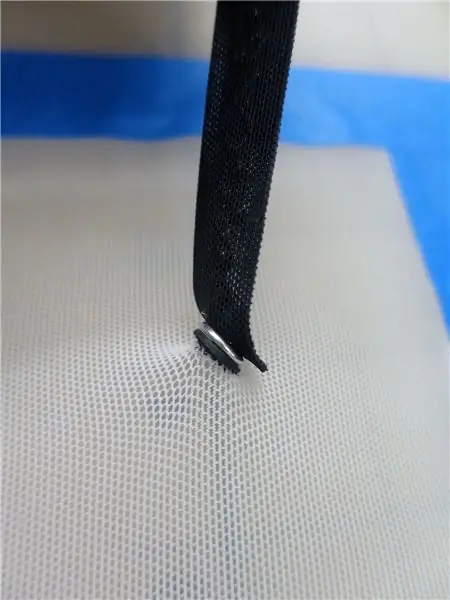
Questo primo scatto è stato stampato da Lara Grant. Sta lavorando a un progetto simile realizzando un tessuto a scatto e ha un ottimo Instructable sulla stampa 3D su tessuto. Dovresti anche dare un'occhiata alle sue classi di wearables
È un filamento di grafene Black Magic 3D ed è stato stampato su una Makerbot Rep 2 con la temperatura di stampa e l'estrusore impostati a 220°
Entrambi abbiamo testato una tecnica per cui si stampa uno strato di base di filamento, si mette in pausa la macchina per inserire il tessuto e poi si continua a stampare. Ciò significa che il filamento si scioglierà attorno al tessuto e creerà un sigillo. Puoi vederlo nella seconda immagine; c'è del filamento nella parte inferiore del tessuto. Questo strato è stato stampato prima sul letto, quindi la stampante è stata messa in pausa e il tessuto è stato inserito. La stampante è stata quindi riattivata e la stampa è proseguita.
Ha funzionato a meraviglia! Primo tentativo usando il file che avevo fatto 10 minuti prima.. E si è persino scattato molto bene!
Questo scatto che vedi qui è stato stampato su powernet. È un materiale che uso molto e che sto utilizzando per il progetto correlato Second Skin che utilizza circuiti elastici. È elasticizzato in 4 direzioni e viene utilizzato per lingerie e abbigliamento da ballo. Funziona bene perché è una maglia sintetica fine. Di solito è realizzato in poliammide, quindi il filamento fonde la superficie e aderisce bene ad essa. Il filamento può anche fondersi all'interno e intorno alla superficie della rete microfine stessa.
Powernet ha una buona resistenza alla trazione e se viene teso con del nastro adesivo quando lo adagi sul letto non viene impigliato dall'estrusore.
Passaggio 3: stampa 3D su una traccia di tessuto conduttivo
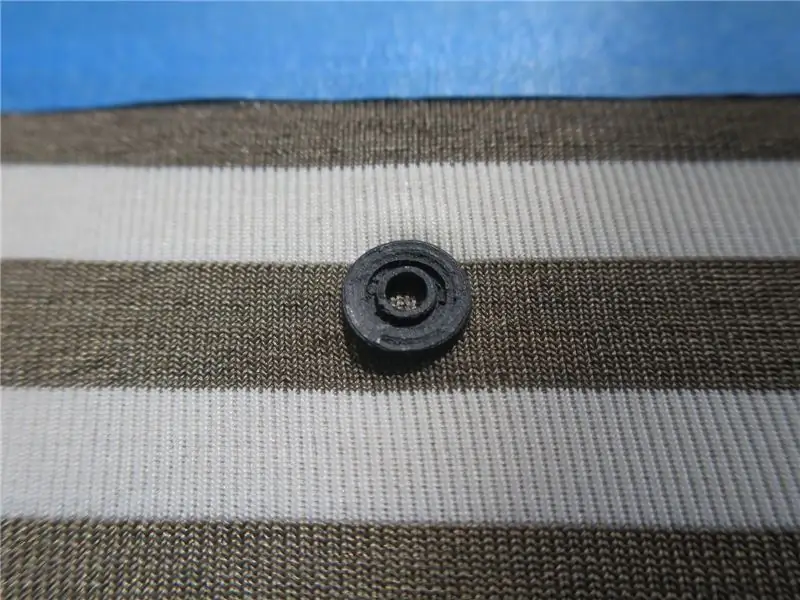
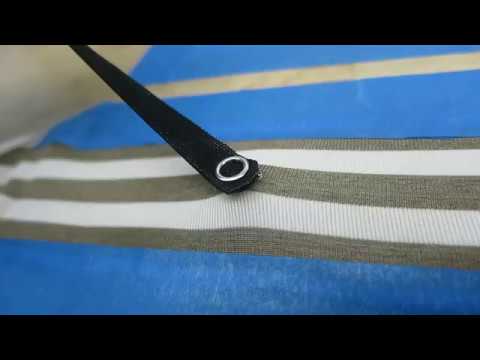
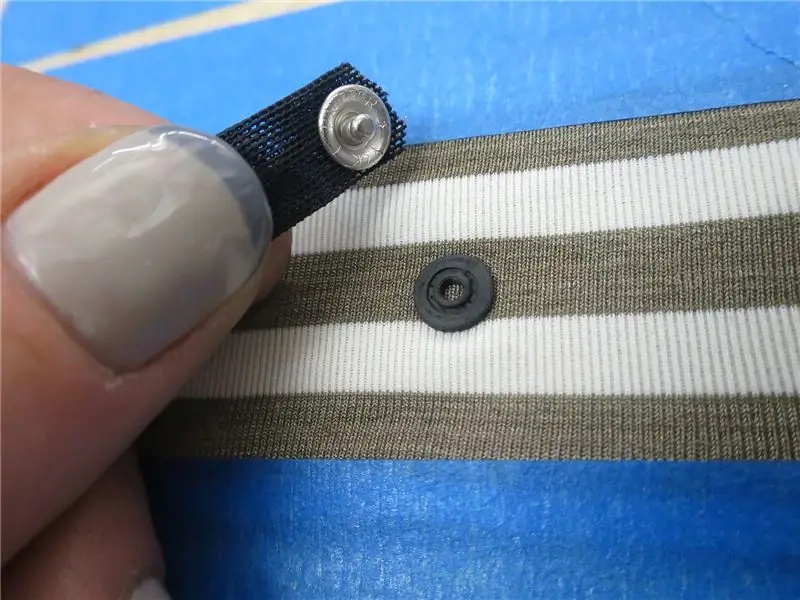
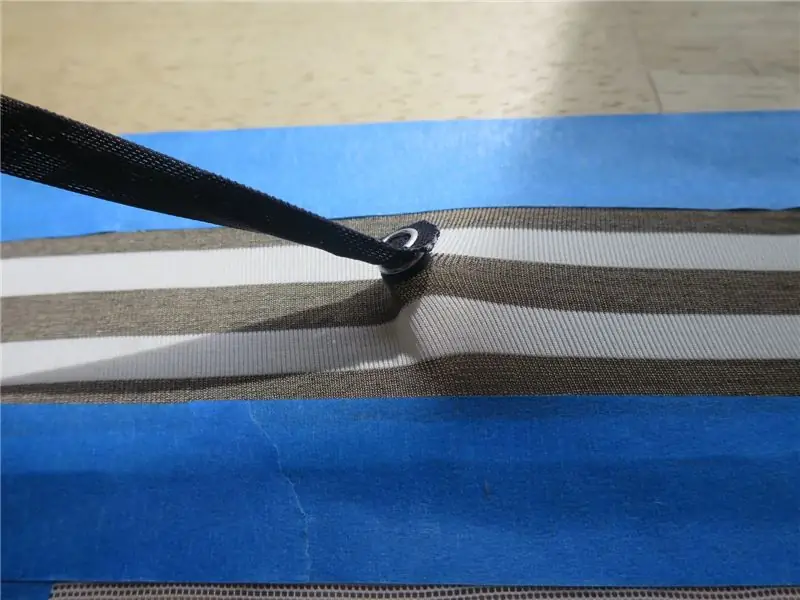
Questo tessuto brillante è un jersey elasticizzato lavorato a maglia con tracce conduttive. Credo che sia la stregoneria di Hannah Perner-Wilson e Mika Satomi di Kobakant ed è stata realizzata su misura. Me ne sono state date alcune al campo estivo di eTextiles e abbiamo deciso che sarebbe stata un'ottima cosa per testare la connessione elettrica tra tessuto e stampa.
È un tessuto jersey e sembra che le fibre siano state rivestite prima di essere tessute, piuttosto che il rivestimento conduttivo stampato dopo la produzione. È troppo spesso per stampare attraverso la superficie (come nel test precedente) poiché il filamento non si collegherebbe allo stesso modo di quanto avviene attraverso i fori nel powernet.
Impostiamo Makerbot per stampare direttamente sopra il tessuto. quella che vedete sopra è la prima stampa di prova su questo materiale.
Molte persone diverse hanno testato la stampa 3D su tessuto e sembra differire a seconda della natura della stampa, dei materiali e delle macchine utilizzate. La maggior parte dei successi sembra coinvolgere le maglie poiché la trama è allentata e il filamento può affondare attraverso il tessuto per creare un legame.
Alcune persone abbassano l'ugello della stampante. Questo rompe l'estrusore nel tessuto e forza il filamento nelle fibre, ma può trascinare il materiale. Un'altra opzione è quella di alzare il punto di partenza dell'estrusore per iniziare la stampa, il che significa che si taglia la stampa in modo tale che inizi appena sopra lo spessore del tessuto. Immagino che funzionerebbe bene se il tuo tessuto fosse spesso. Dato che i nostri sono piuttosto sottili e piatti, abbiamo stampato direttamente sul materiale con le impostazioni predefinite, semplicemente spegnendo le zattere e qualsiasi supporto.
Ha funzionato magnificamente! Ciò potrebbe essere dovuto a vari fattori:- la superficie di questo particolare tessuto era ideale per l'adesione della stampa- l'estrusore era semplicemente alla temperatura perfetta in questo momento (questo filamento può essere molto incoerente)- gli dei della stampa 3D eravamo di buon umore e siamo stati super fortunati
Chiaramente, questo ha bisogno di più test.
Passaggio 4: test di conduttività

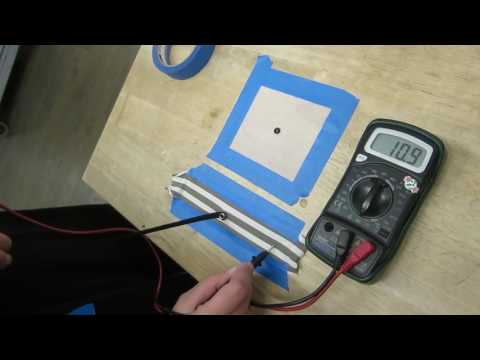
Questo test ha utilizzato un connettore eTextile elasticizzato realizzato con filo conduttivo Karl Grimm. All'interno del connettore nero c'è uno zigzag di filo conduttivo isolato da strati di tessuto su entrambi i lati. Ogni estremità ha uno snapet maschio. Tutti questi materiali hanno una resistenza piuttosto bassa.
La resistenza attraverso il connettore da 30 cm, attraverso lo scatto e attraverso circa 8 cm di tessuto conduttivo sembra essere di circa 10 ohm. Questo è stato sorprendente e sembrava rimanere abbastanza stabile anche quando allungato. Non sono sicuro che questa sia una lettura accurata e ripetibile!
Passaggio 5: stampa su superfici diverse
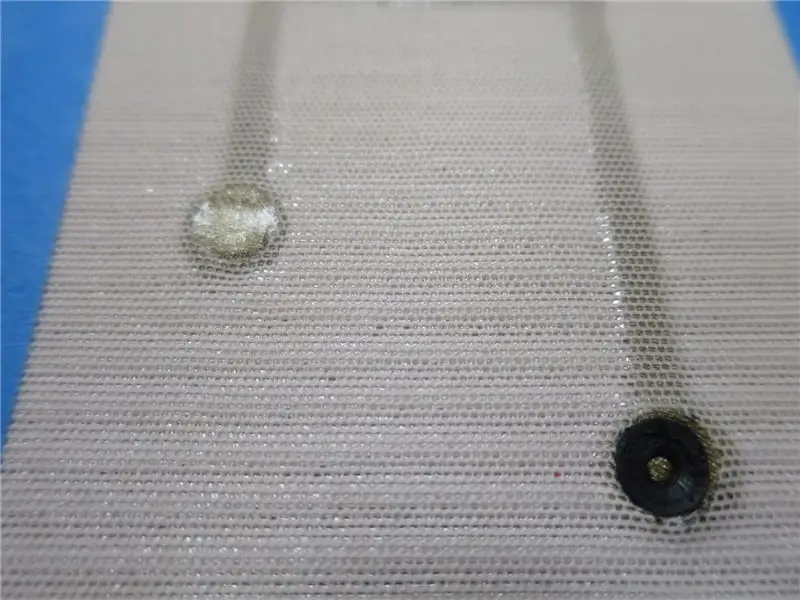
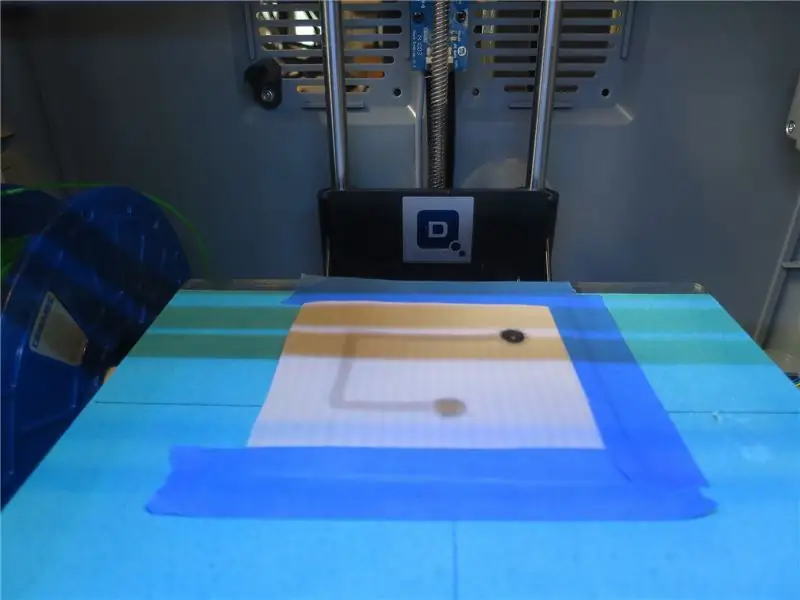
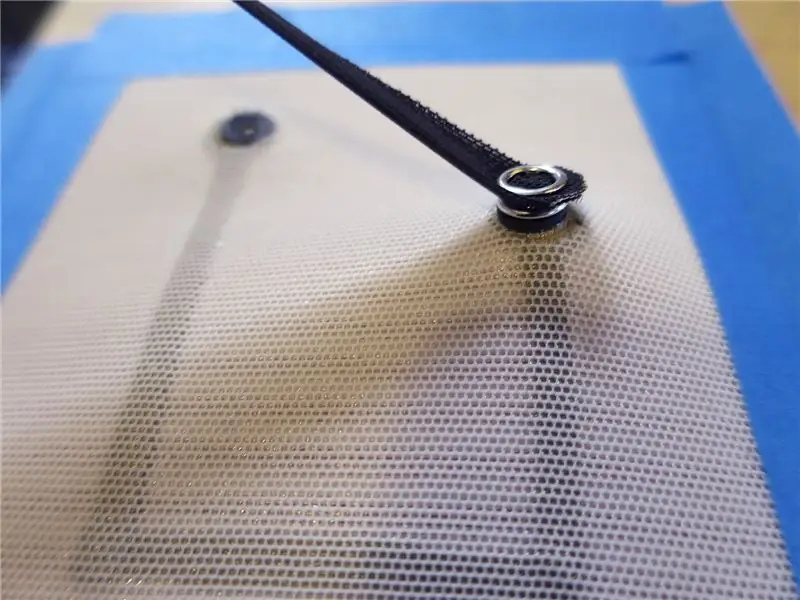
Successivamente ho deciso di provare a stampare su un Dremel. Ciò è dovuto principalmente al fatto che Makerbot stava avendo un attacco sibilante, ma la varietà è sempre buona. Anche in questo caso, la temperatura di stampa e l'estrusore sono stati impostati su 220°
Ho lavorato su tracce conduttive incollate, isolate ed elastiche per eTextiles. Questi tessuti utilizzano strati di tessuto accoppiato con fusione Bemis SewFree, una pellicola termosaldante super fine. Ciò significa che i campioni di tessuto erano più spessi rispetto ai test precedenti. Le tracce conduttive sono isolate all'interno del tessuto powernet e hanno solo le estremità esposte come cuscinetti rotondi.
Quando ho stampato per la prima volta il file con le impostazioni predefinite, si è schiantato contro la superficie del tessuto e ha distorto la stampa. Potete vedere il risultato nella prima immagine. Lo scatto questa volta non ha funzionato.
Jonathon mi ha mostrato come tagliare il file in Cura e aumentare la posizione iniziale dell'estrusore di 0,4 mm.
Per il prossimo test ho anche aggiunto uno strato di adesivo SewFree alla superficie su cui stavo per stampare. Questo era per vedere se questo faceva qualche differenza sul modo in cui la stampa aderiva.
Inizialmente ha funzionato molto bene, come puoi vedere nell'ultima immagine. Sfortunatamente dopo un paio di scatti, lo scatto si è allentato dal tessuto ed è caduto.
Passaggio 6: test di stampa multipla
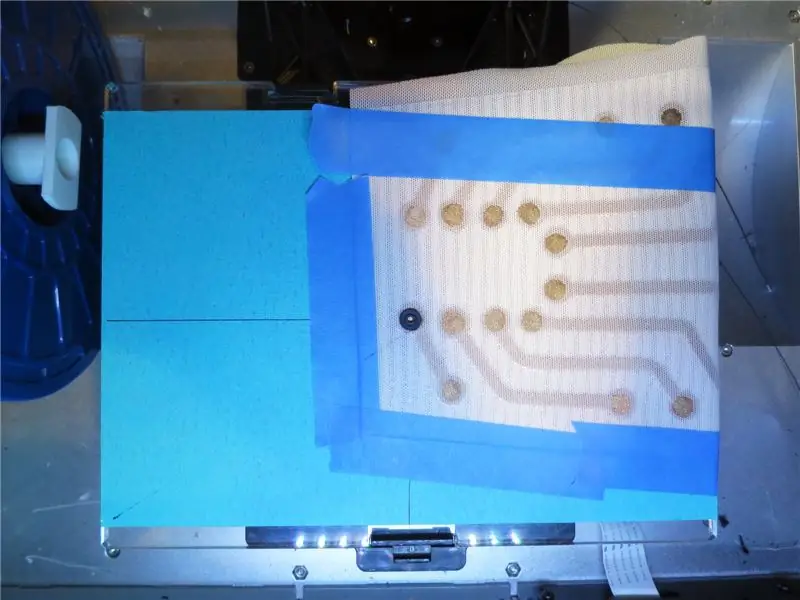
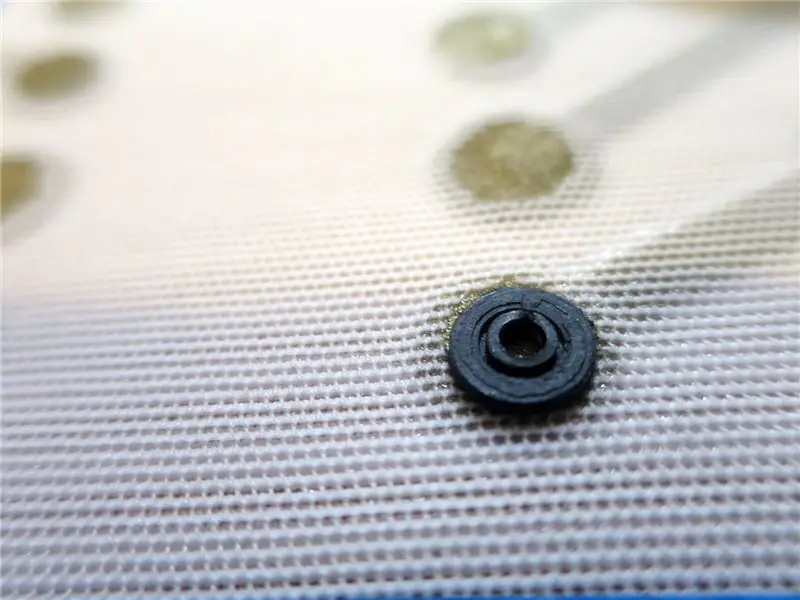
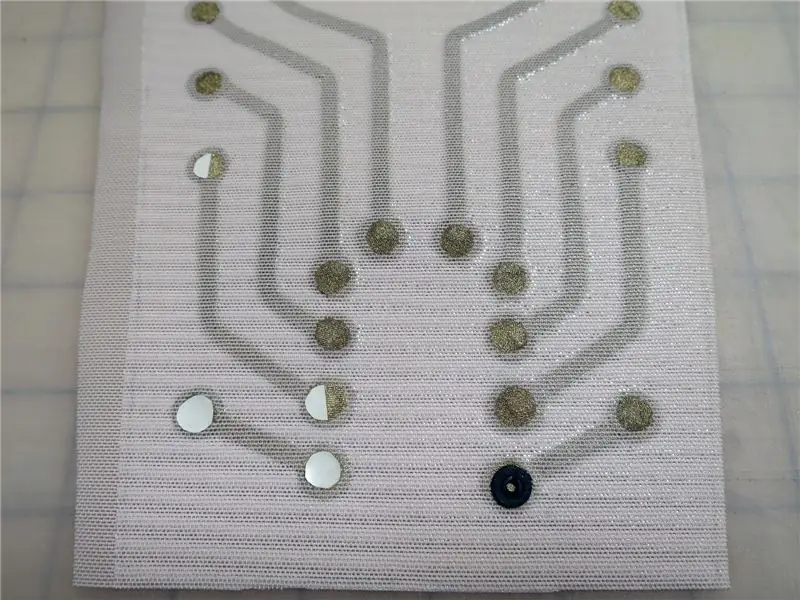
Successivamente ho provato a stampare più snap per vedere come la corrente scorreva attraverso due snap alle due estremità di una traccia conduttiva. Dato che avevo solo uno snap funzionante nel test precedente, non ho potuto verificare. Forse la stampa che Lara aveva fatto in precedenza era un colpo di fortuna. Ho fatto un pannello veloce per provare più stampe.
Poiché si trattava di un test, ho deciso di stampare ogni scatto singolarmente, piuttosto che provare a stampare più scatti su un pezzo di tessuto.
Tre motivi: 1. Non volevo investire tempo nella creazione di un file di layout poiché il circuito di tessuto su cui stavo stampando era realizzato in modo impreciso2. Le stampe spesso falliscono 3. Non volevo che il filamento canaglia si trascinasse sul tessuto
Ho allineato ogni scatto fino a un punto centralizzato e li ho stampati uno per uno. Ognuno è venuto perfettamente.
Ho aggiunto la fusione SewFree ad alcuni pad conduttivi. Puoi vederlo nelle immagini come cerchi e semicerchi bianchi. Questo è il supporto di carta che viene staccato. L'ho lasciato acceso così è più facile da vedere nelle immagini. Ho pensato che sarebbe stato bello vedere come la fusione influenzasse l'aderenza sulla stessa stampa. Sono risultati tutti abbastanza simili. La maggior parte si è bloccata e alcuni sono caduti. Non sono sicuro del perché, ma presumo sia dovuto a piccole differenze nello spessore della stratificazione del tessuto. Sono stati tutti stampati in rapida successione sulla stessa stampante con le stesse impostazioni.
la resistenza su una traccia conduttiva di 15 cm attraverso due scatti resistivi era di circa 50 ohm. Questo è stato fatto subito dopo la stampa e sembrava super conduttivo, quindi avevamo bisogno di più test..
Passaggio 7: leggere la resistenza
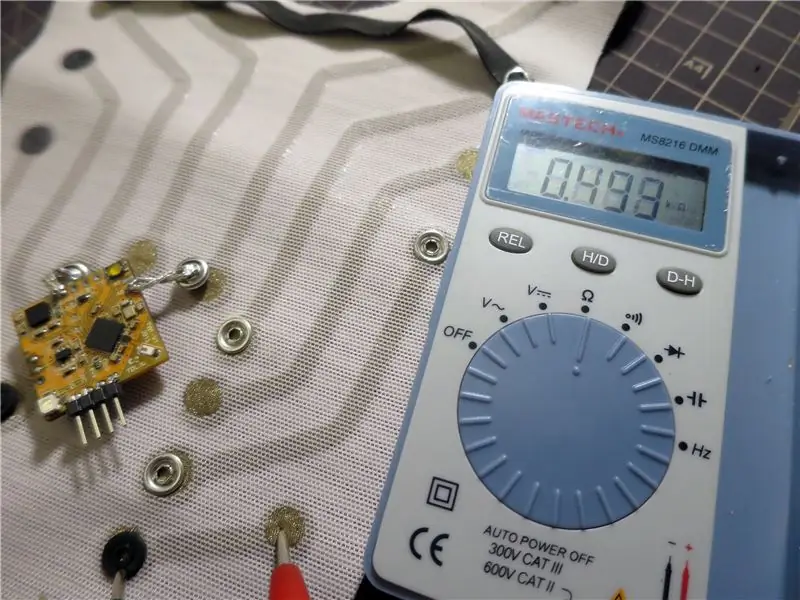
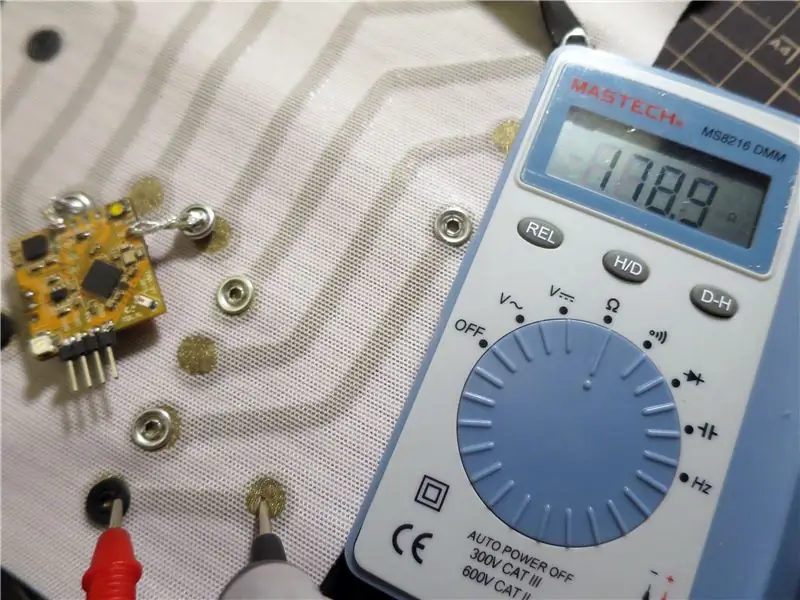
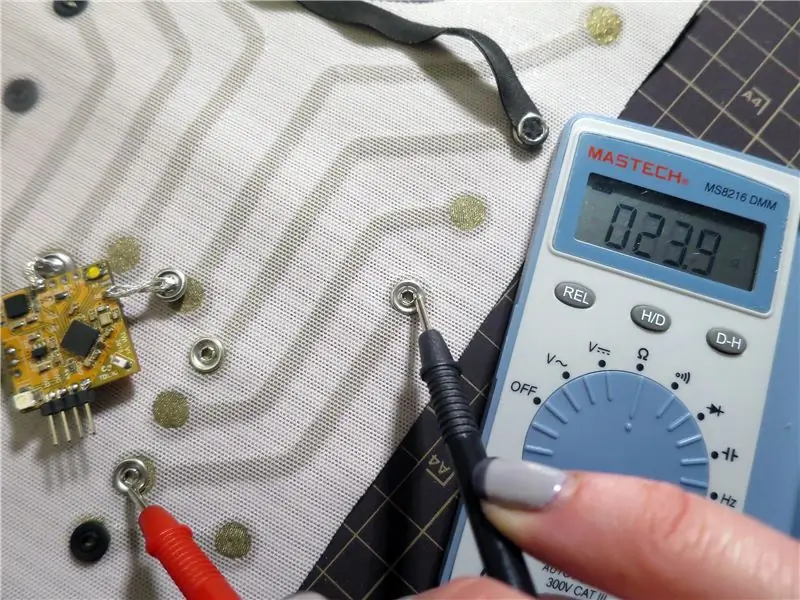
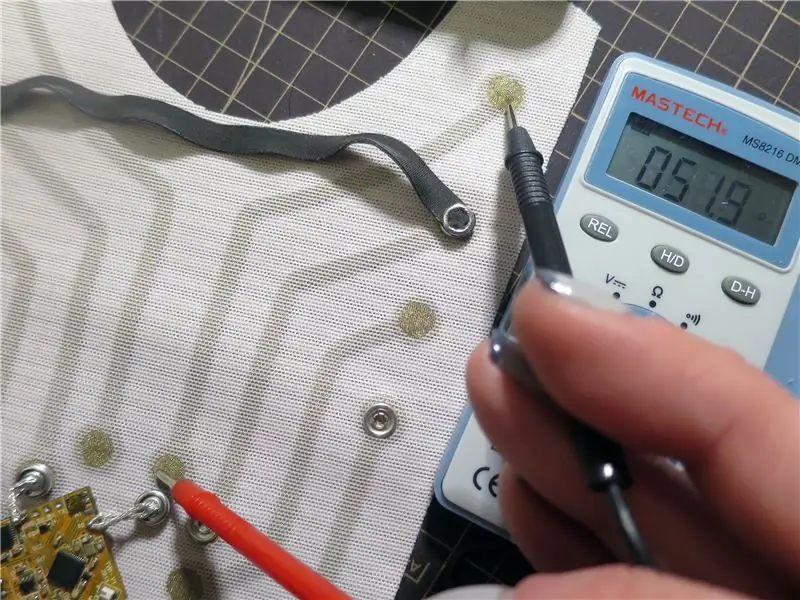
Le letture che ho preso dagli scatti sembravano differire molto. Anche questo è cambiato nel tempo.
Passaggio 8: riattaccare gli snap con resina epossidica conduttiva
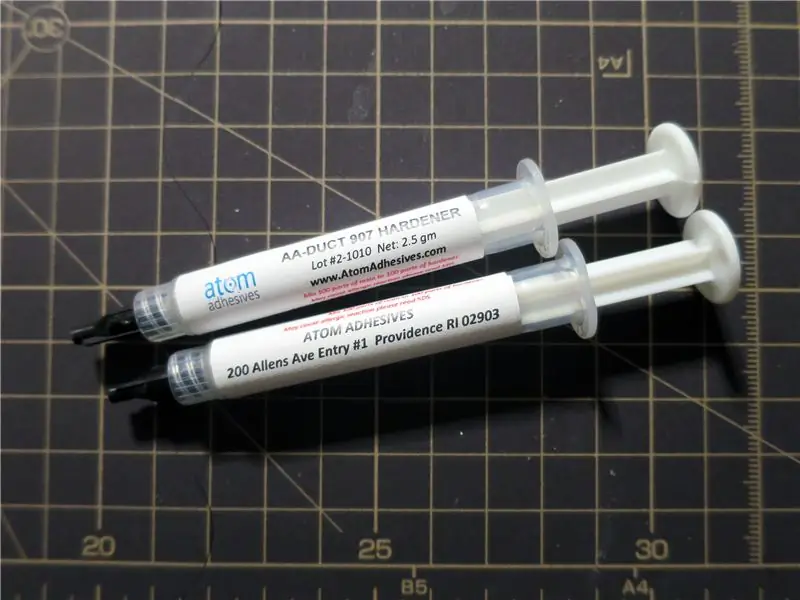
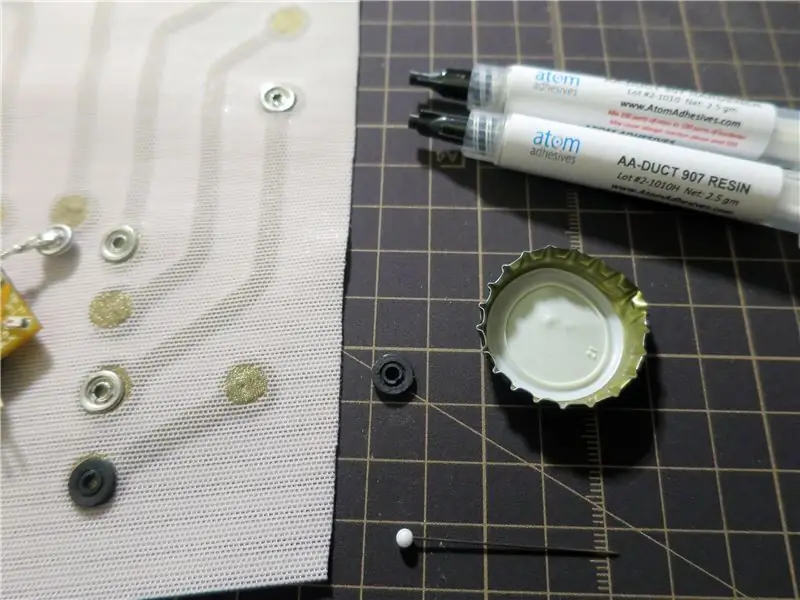
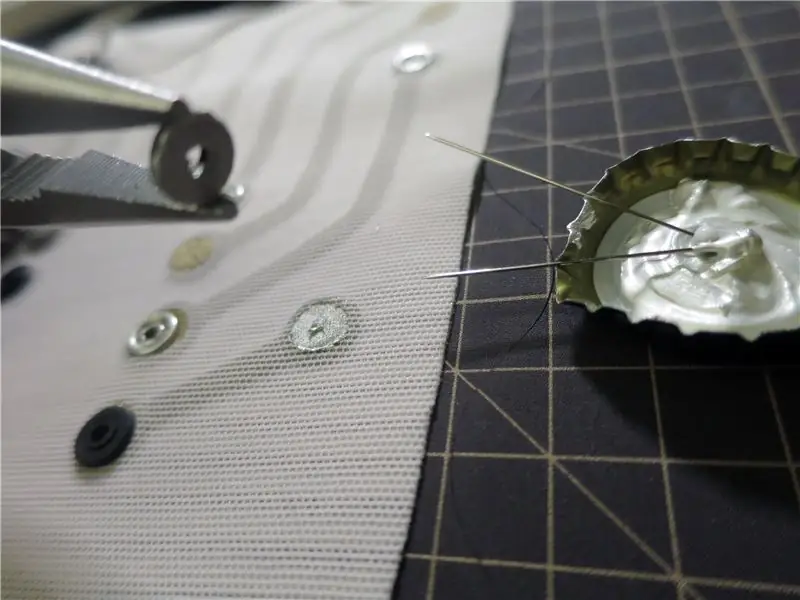
Alcuni degli scatti sono caduti dopo un po' di utilizzo. Non hanno aderito così bene al materiale incollato come nei test precedenti.
A questo punto, vale la pena indagare su un'altra opzione: gli snap possono essere stampati e poi attaccati al tessuto.
Può essere vero che gli snap possono essere stampati su determinati tessuti ma devono essere incollati su altri. Questa potrebbe essere ancora un'opzione praticabile.
Ho usato resina epossidica conduttiva e ho incollato due degli snap in posizione per vedere se la colla può fare un legame e condurre in modo affidabile.
Purtroppo questo non ha aderito per niente bene al tessuto. La resina epossidica è piuttosto gessosa e non ama il materiale sintetico denso. Sebbene la colla permettesse a una piccola quantità di corrente di fluire, i bottoni automatici si staccarono dopo uno schiocco.
Passaggio 9: conclusione e passaggi successivi
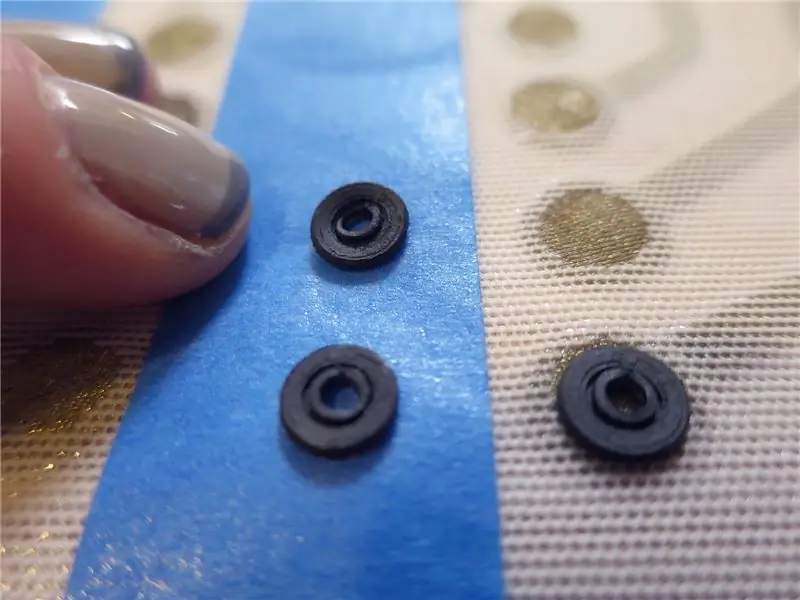
Questo design a scatto ha funzionato molto bene per un primo test. Scatta in modo sicuro, può condurre una piccola quantità di corrente ed è una buona prova di concetto.
Sfortunatamente non hanno dato una conduttività costante. Alcuni erano ok e altri non funzionavano affatto. Sembra che usare un tessuto a trama fitta sia un problema, quindi non funziona così bene per i miei tessuti accoppiati. Usare una trama più aperta come la maglia, e soprattutto il powernet, sembra l'opzione migliore. Il problema è che meno denso è un tessuto, peggiore è la conduttività per gli etextiles.
Ci sono alcuni problemi pratici con il PLA. Tende a deformarsi e restringersi. Alcuni degli scatti hanno funzionato immediatamente, alcuni hanno avuto bisogno di alcune chiusure forzate iniziali prima di essere conformi, apparentemente per allungare un po' la stampa. Alcuni sembravano troppo piccoli per spezzarsi. Era tutto un po' incoerente.
Ho anche letto che la conduttività di questi materiali può cambiare nel tempo. In questo caso direi che la pressione dello scatto stesso può influire su questo. Anche il passaggio di corrente attraverso lo snap può aumentare in modo permanente la resistenza. Questo richiederà sicuramente più test.
c'è una buona panoramica dei filamenti Black Magic 3D qui
Voglio usare questa idea a scatto in un design di guanti. Voglio trovare un modo per creare connettori rimovibili per i sensori di allungamento. L'idea sarebbe che questo file snap possa essere integrato direttamente in un sensore stampato in 3D per collegarlo a un circuito.
In revisione ho trovato questo processo interessante e informativo. Non è abbastanza stabile da produrre risultati misurabili coerenti e vorrei esplorare ulteriormente in esperimenti più controllati.
Se provi una di queste stampe, lascia un commento!
Consigliato:
Crea un EASY Infinity Mirror Cube - NESSUNA stampa 3D e NESSUNA programmazione: 15 passaggi (con immagini)
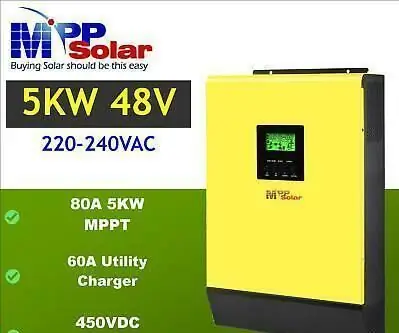
Crea un EASY Infinity Mirror Cube | NESSUNA stampa 3D e NESSUNA programmazione: a tutti piace un buon cubo infinito, ma sembra che sarebbe difficile da realizzare. Il mio obiettivo per questo Instructable è mostrarti passo dopo passo come crearne uno. Non solo, ma con le istruzioni che ti sto dando, sarai in grado di farne uno o
Stampa di assegni senza software speciale o stampante con MS Excel (stampa assegni bancari): 6 passaggi
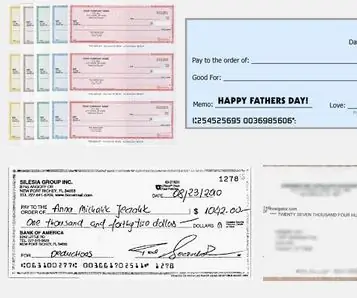
Stampa di assegni senza software speciale o stampante con MS Excel (stampa di assegni bancari): questa è una semplice cartella di lavoro Excel, che sarà molto utile per qualsiasi azienda per scrivere molti assegni bancari in secondo luogo ai loro fornitori. Non hai bisogno di stampanti o software speciali, ti serve solo un computer con MS Excel e una stampante normale. Sì, ora puoi
Servo tester a 16 canali con Arduino e stampa 3D: 3 passaggi (con immagini)
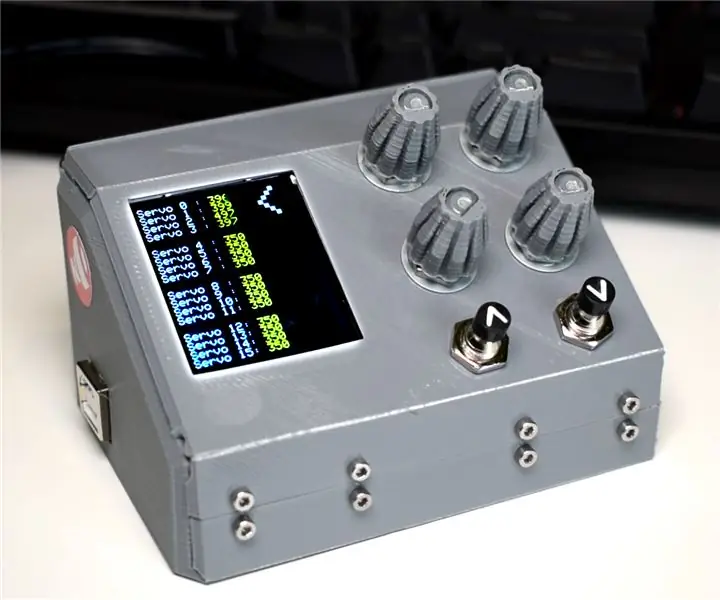
Servo tester a 16 canali con Arduino e stampa 3D: praticamente tutti i progetti che ho realizzato di recente mi hanno richiesto di testare alcuni servi e sperimentare le loro posizioni prima che entrino nell'assieme. Di solito faccio un tester servo veloce su una breadboard e uso il monitor seriale nell'ardui
SLIDER MOTORIZZATO PER TELECAMERA Con SISTEMA DI INSEGUIMENTO (stampa 3D): 7 passaggi (con immagini)
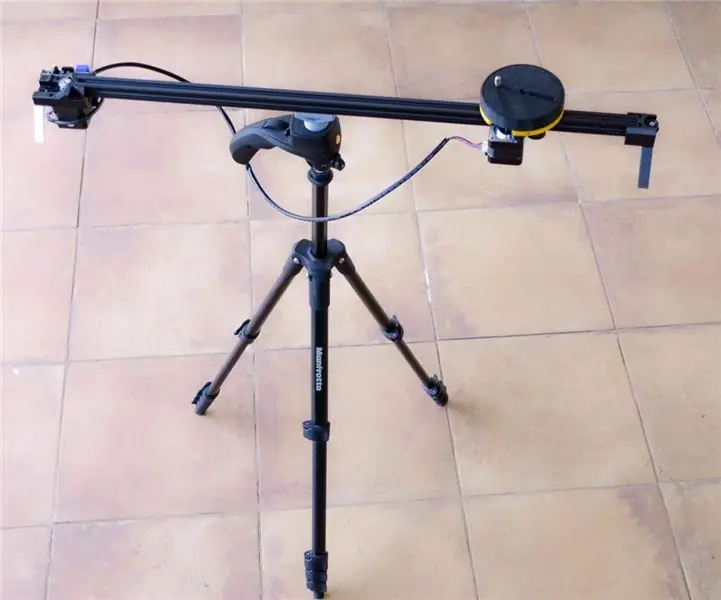
SLIDER PER FOTOCAMERA MOTORIZZATO Con SISTEMA DI TRACKING (stampa 3D): Fondamentalmente, questo robot sposterà una fotocamera/smartphone su un binario e "traccerà" un oggetto. La posizione dell'oggetto target è già nota al robot. La matematica dietro questo sistema di tracciamento è abbastanza semplice. Abbiamo creato una simulazione del processo di tracciamento
Stampa di circuiti personalizzati con una stampante 3D: 7 passaggi (con immagini)
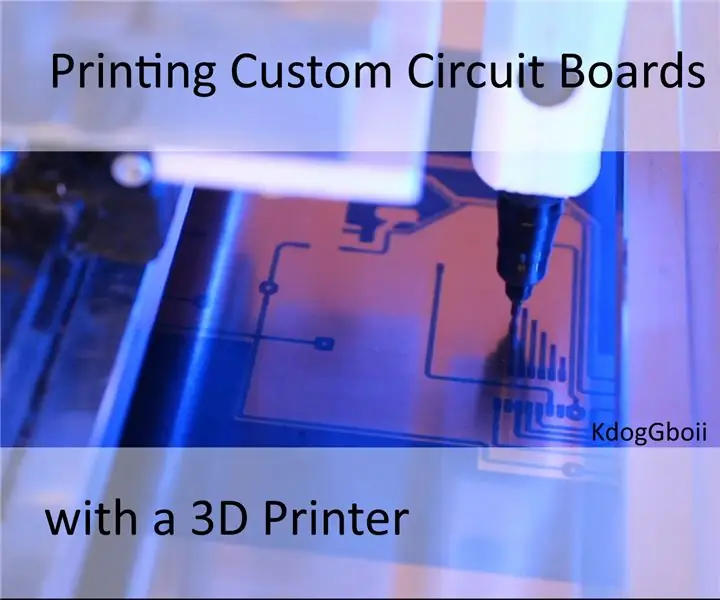
Stampa di circuiti stampati personalizzati con una stampante 3D: se questa non è la prima volta che vedi una stampante 3D, probabilmente avrai sentito qualcuno dire qualcosa del tipo: 1) Acquista una stampante 3D2) Stampa un'altra stampante 3D3) Restituisci il 3D originale stampante4) ????????5) ProfitNow chiunque w