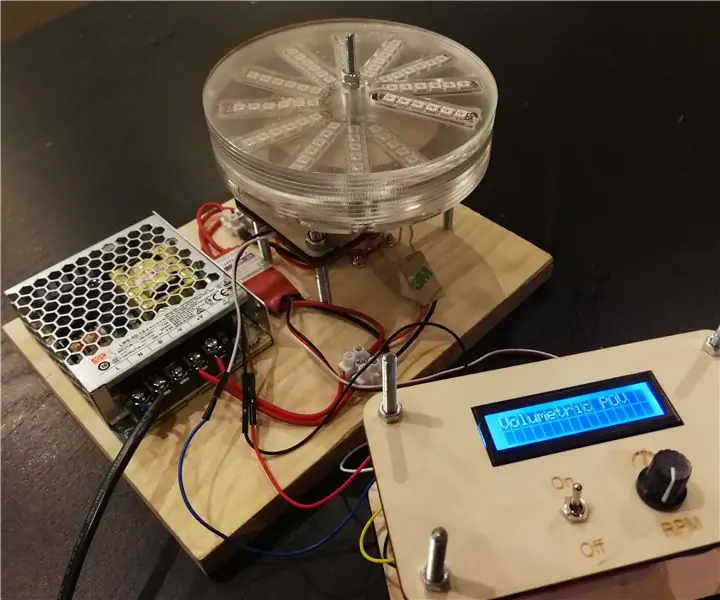
Sommario:
- Passaggio 1: materiale e strumenti utilizzati
- Passaggio 2: unità di controllo del motore per regolare la velocità di rotazione
- Passaggio 3: creazione della piattaforma per la trasmissione di potenza wireless
- Passaggio 4: involucro rotante
- Passaggio 5: cilindro rotante con strisce LED
- Passaggio 6: lezioni apprese
- Passaggio 7: potenziali miglioramenti
- Passaggio 8: gridare
2025 Autore: John Day | [email protected]. Ultima modifica: 2025-01-23 14:49
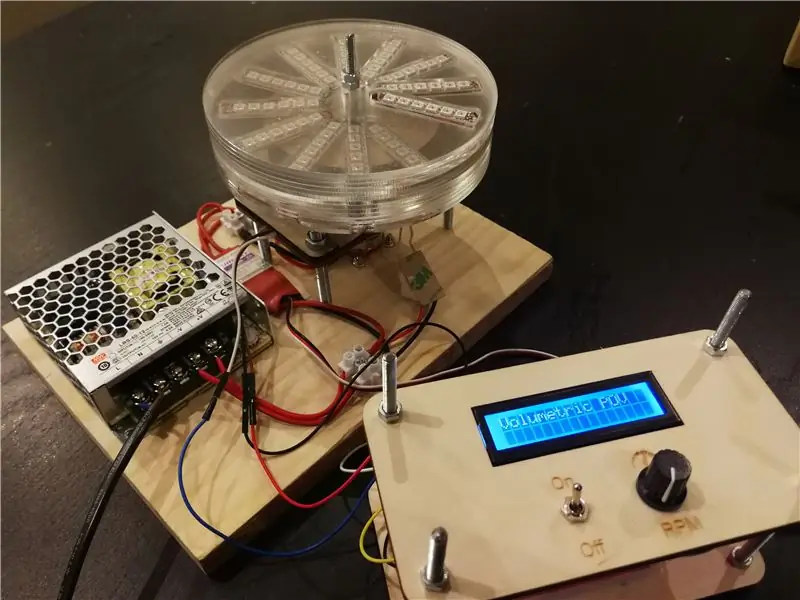
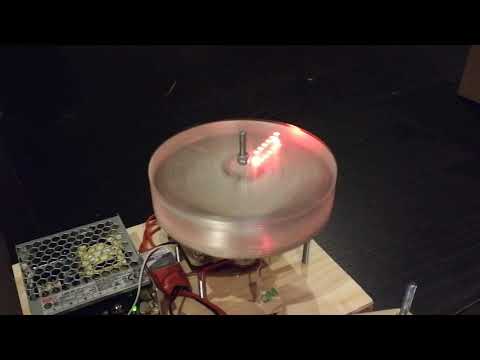

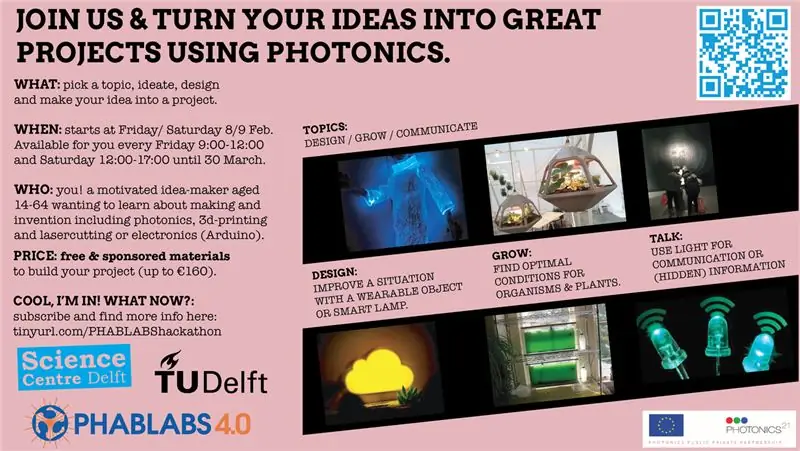
Qualche settimana fa ho ricevuto un invito dell'ultimo minuto a partecipare a un PhabLabs Hackathon presso il Science Centre Delft nei Paesi Bassi. Per un hobbista entusiasta come me, che normalmente può dedicare solo una quantità limitata di tempo ad armeggiare, ho visto questa come una grande opportunità per programmare del tempo dedicato per trasformare una delle mie tante idee, nell'ambito dell'Hackathon: Photonics, in un progetto vero e proprio. E con le ottime strutture del Makerspace al Science Center Delft era semplicemente impossibile rifiutare questo invito.
Una delle idee che avevo già da tempo riguardo alla fotonica era che volevo fare qualcosa con Persistence of Vision (POV). Ci sono già tonnellate di esempi disponibili online su come costruire un display POV di base utilizzando alcuni componenti di base: microcontrollore, vecchia ventola/hard disk/motore e una stringa di led collegati perpendicolarmente all'asse del dispositivo rotante. Con una configurazione relativamente semplice puoi già creare un'impressionante immagine bidimensionale, ad esempio:
Un'altra variante dei display POV collega una stringa di led parallela all'asse del dispositivo rotante. Ciò si tradurrà in un display POV cilindrico tridimensionale, ad esempio:
Invece di collegare la stringa di led parallelamente all'asse del dispositivo rotante si può anche inarcare la stringa di led. Ciò si tradurrà in un display POV sferico (globale), ad esempio: https://www.instructables.com/id/POV-Globe-24bit-… Il livello successivo è quello di costruire diversi strati di stringhe di led per creare un display 3D volumetrico. Ecco alcuni esempi di tali display POV 3D volumetrici che ho usato come ispirazione per questo progetto specifico:
- https://www.instructables.com/id/PropHelix-3D-POV-…
- https://github.com/mbjd/3DPOV
- https://hackaday.io/project/159306-volumetric-pov-…
- https://hackaday.com/2014/04/21/volumen-the-most-a…
Poiché i creatori degli esempi precedenti hanno fornito informazioni molto utili, aveva molto senso remixare parti dei loro progetti. Ma poiché un Hackathon dovrebbe essere impegnativo, ho anche deciso di costruire un diverso tipo di display POV 3D volumetrico. Alcuni di loro usavano rotori e molta colla a caldo per impedire ai componenti di volare in giro. Altri hanno creato PCB personalizzati per il loro progetto. Dopo aver esaminato alcuni degli altri progetti POV 3D, ho visto spazio per alcune "innovazioni" o introdurre alcune sfide per me stesso:
- Senza alcuna esperienza precedente nella creazione di PCB personalizzati e a causa dei limiti di tempo dell'Hackathon, ho scelto di seguire un approccio prototipale più semplice. Ma invece di creare veri rotori ero curioso di sapere come sarebbe stato un display POV 3D volumetrico quando si utilizzava un cilindro costituito da strati di plastica acrilica.
- Nessun uso o minimo uso di colla a caldo per rendere il dispositivo meno pericoloso
Passaggio 1: materiale e strumenti utilizzati
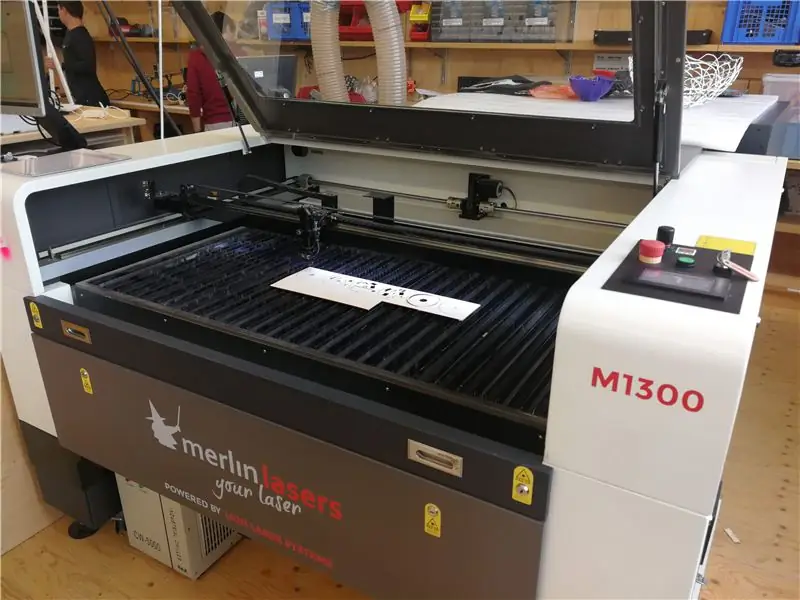
Per il controller del motore
- Arduino Pro Micro 5V/16Mhz
- Tagliere piccolo
- Sensore interruttore ad effetto Hall 3144
- Magnete con diametro: 1 cm, altezza: 3 mm
- Interruttore a levetta - MTS-102
- Potenziometro 10K
- Cavi per ponticelli Dupont
- 16 dadi M5
- Modulo display LCD con retroilluminazione blu (HD44780 16×2 caratteri)
- Resistore 10K - Resistenza Pull Up per il sensore ad effetto Hall
- Resistenza da 220 Ohm - Per controllare il contrasto dello schermo LCD
- Diametro dell'asta filettata: 5 mm
- Compensato, spessore: 3 mm
Per la base della piattaforma
- Pezzo di legno di scarto (250 x 180 x 18 mm)
- Mean Well - 12V 4.2A - Alimentatore Switching LRS-50-12
- Cavo di alimentazione 220V
- Convertitore wireless DC-DC - 5V 2A (trasmettitore)
- Motore Outrunner senza spazzole Turnigy D2836/8 1100KV
- Turnigy peluche 30amp regolatore di velocità con BEC
- Connettori per morsettiere
- 12 x M6 Dadi per fissare la piattaforma utilizzando le barre filettate con un diametro di 6 mm.
- 3 bulloni M2 (lunghezza 18 mm) per il fissaggio dell'adattatore imbullonato al motore brushless
- 4 x M3 dadi e bulloni per fissare il motore brushless al pezzo di legno di scarto
- Diametro barra filettata: 6 mm (4 x lunghezza 70 mm)
- Diametro barra filettata: 4 mm (1 x lunghezza 80 mm)
- Compensato, spessore: 3 mm
Per l'involucro rotante
- Convertitore wireless DC-DC - 5V 2A (ricevitore)
- Adattatore Bolt On stampato in 3D (filamento PLA, bianco)
- Adolescente 3.6
- Convertitore/Shifter di livello logico quad IC 74AHCT125 (da 3V a 5V)
- Resistore 10K - Resistenza Pull Up per il sensore ad effetto Hall
- Condensatore da 1000uF 16V
- Diametro barra filettata 4mm
- Magnete con diametro: 1 cm, altezza: 3 mm
- Compensato, spessore: 3 mm
- Compensato, Spessore: 2 mm
- Foglio acrilico, spessore: 2 mm
- Diametro dell'asta d'acciaio: 2 mm
- Dadi e bulloni
- Striscia led 0,5 metri APA102C 144 led / metro
Strumenti utilizzati
- Merlin Laser Cutter M1300 - Taglio laser compensato e lastre acriliche
- Ultimaker 2+ per la stampa 3D dell'adattatore Bolt On
- Stazione di saldatura e saldatura
- Trapano da tavolo
- cacciaviti
- Plyers
- Martello
- Calibro
- seghetto
- chiavi
- Guaina termorestringente
Software utilizzato
- Fusione 360
- Ultimaker Cura
- Arduino IDE e Teensyduino (contenente Teensy Loader)
Passaggio 2: unità di controllo del motore per regolare la velocità di rotazione
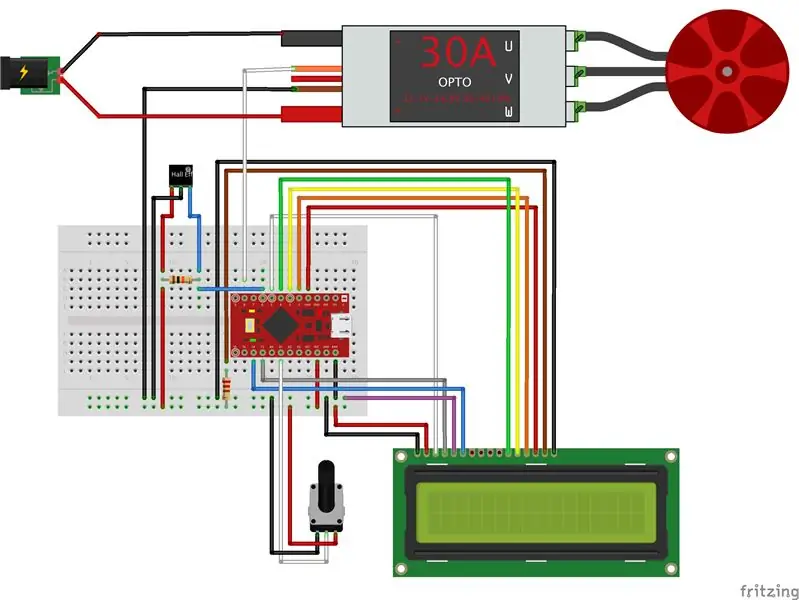
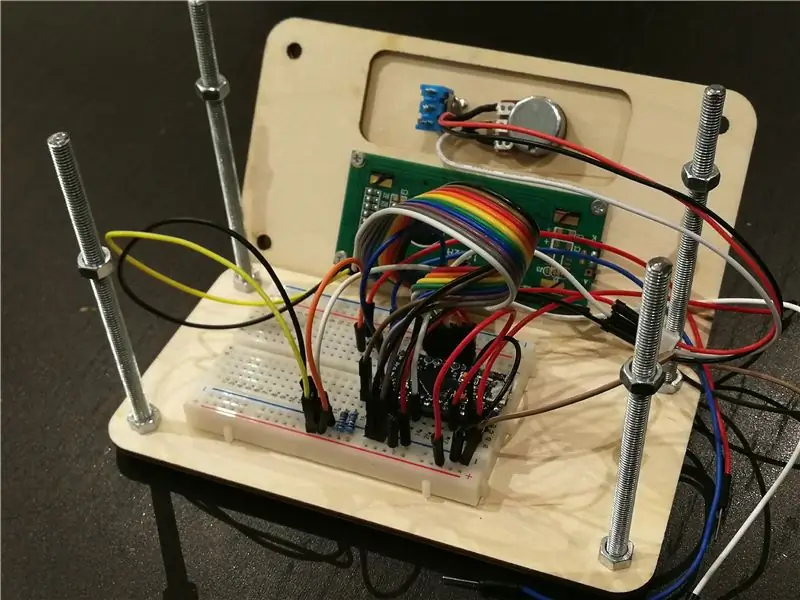
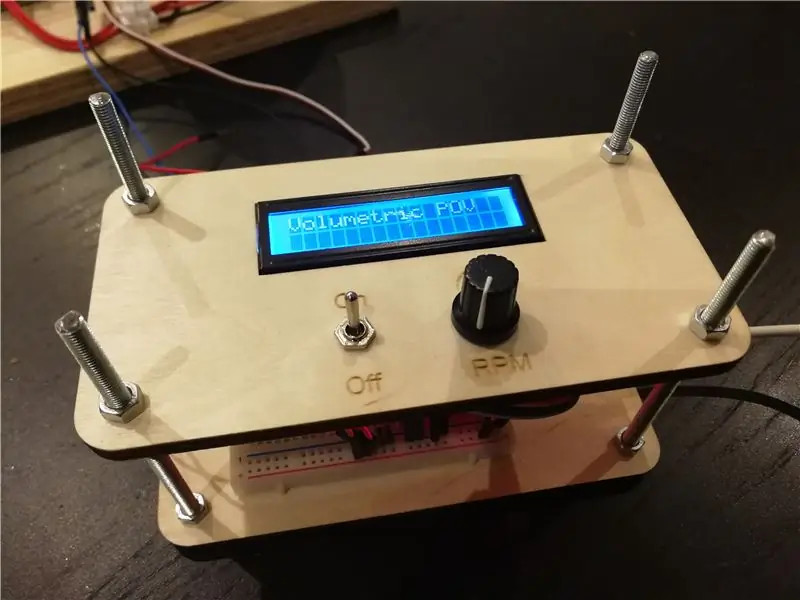
L'unità controller motore invia un segnale al controller elettronico di velocità Turnigy (ESC) che controllerà il numero di rotazioni fornite dal motore brushless.
Inoltre volevo anche essere in grado di visualizzare le rotazioni effettive al minuto del cilindro POV. Ecco perché ho deciso di includere un sensore ad effetto hall e un display LCD 16x2 nell'unità di controllo motore.
Nel file zip allegato (MotorControl_Board.zip) troverai tre file dxf che ti permetteranno di tagliare al laser una piastra di base e due piastre superiori per l'unità di controllo motore. Si prega di utilizzare compensato con uno spessore di 3 mm. Le due piastre superiori possono essere posizionate una sopra l'altra che ti permetteranno di avvitare il display LCD 16x2.
I due fori nella piastra superiore sono pensati per un interruttore a levetta on/off e un potenziometro per controllare la velocità del motore brushless (non ho ancora cablato personalmente l'interruttore a levetta on/off). Per costruire l'unità di controllo motore è necessario segare la barra filettata con un diametro di 5 mm in 4 pezzi dell'altezza desiderata. Usando gli 8 dadi M5 puoi prima fissare la base. Quindi ho attaccato la piccola breadboard alla piastra di base utilizzando l'adesivo biadesivo fornito con la breadboard. Lo schema allegato mostra come collegare i componenti in modo che possano funzionare con il codice sorgente (MotorControl.ino) allegato a questo passaggio. Ho usato una resistenza di pull-up da 10K per il sensore di hall. Un resistore da 220 Ohm ha funzionato abbastanza bene da rendere visibile il testo sullo schermo LCD.
Assicurati di isolare i pin del sensore ad effetto hall utilizzando tubi termorestringenti, proprio come mostrato nelle immagini. Il corretto funzionamento del sensore di hall si baserà su un magnete che verrà posizionato nella cassa rotante al punto 3.
Una volta completato il cablaggio è possibile fissare le 2 piastre superiori con il display LCD, l'interruttore e il potenziometro utilizzando nuovamente 8 dadi M5 come mostrato nelle immagini.
In attesa del modello del motore utilizzato, potrebbe essere necessario modificare la seguente riga di codice nel file MotorControl.ino:
acceleratore = map(averagePotValue, 0, 1020, 710, 900);
Questa riga di codice (riga 176) associa la posizione del potenziometro 10K al segnale per l'ESC. L'ESC accetta un valore compreso tra 700 e 2000. E poiché il motore che ho usato per questo progetto ha iniziato a girare intorno a 823, ho limitato gli RPM del motore limitando il valore massimo a 900.
Passaggio 3: creazione della piattaforma per la trasmissione di potenza wireless
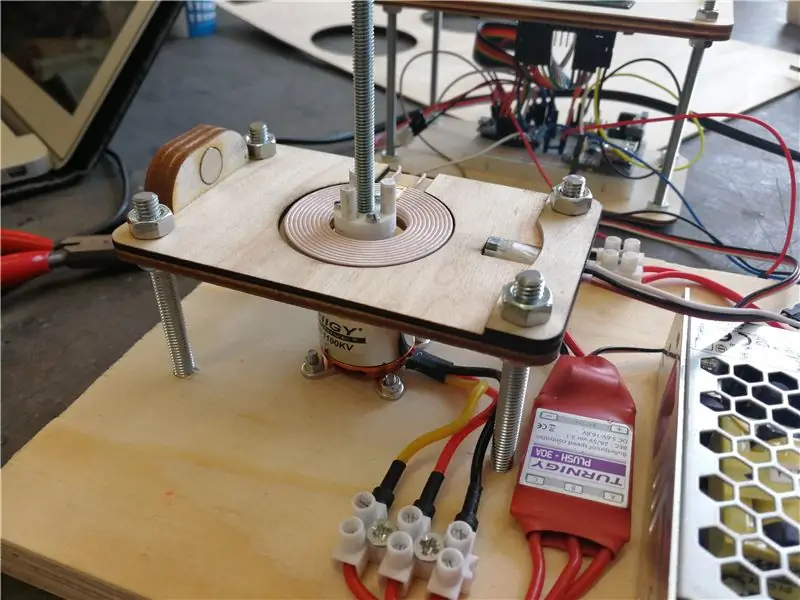
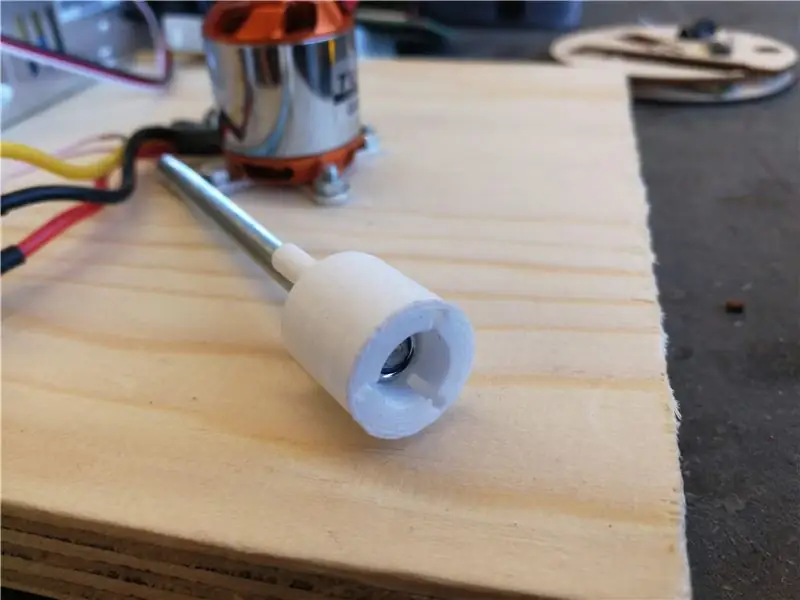
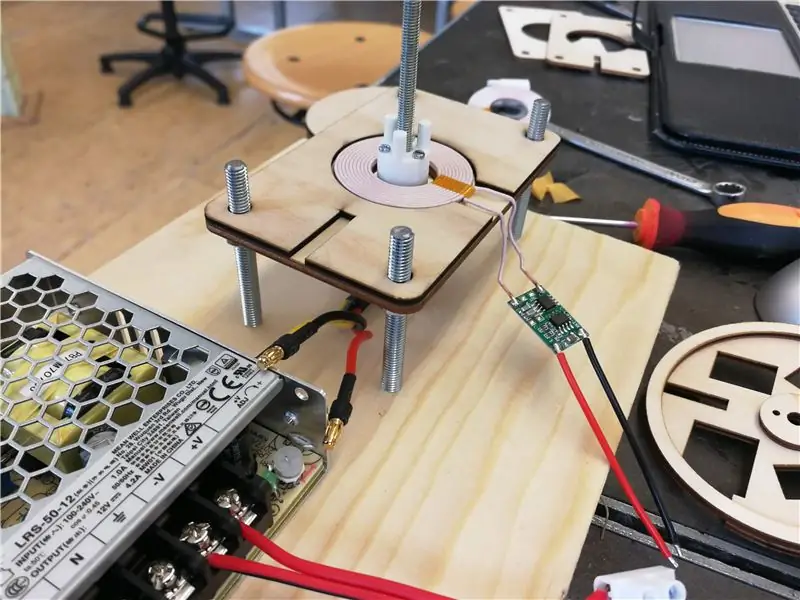
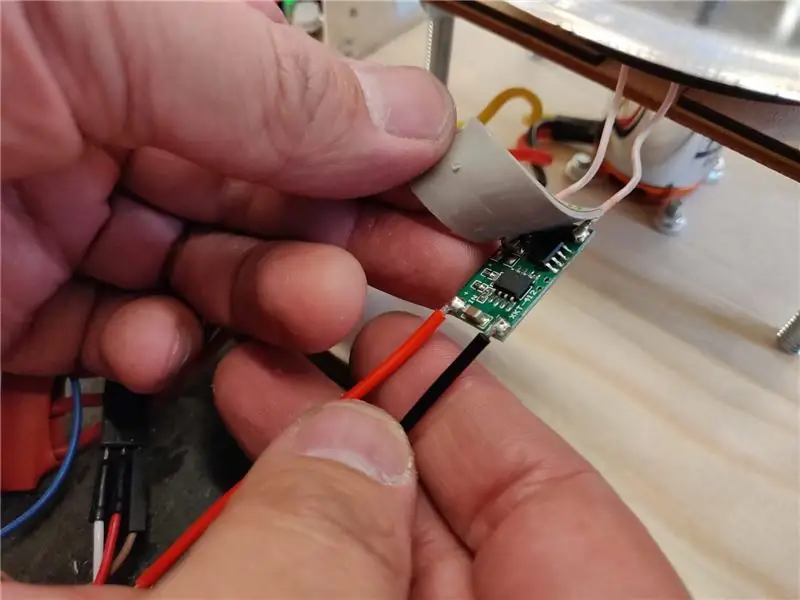
Al giorno d'oggi ci sono fondamentalmente due modi per alimentare i dispositivi che devono ruotare: anelli collettori o trasmissione di potenza in modalità wireless tramite bobine di induzione. Poiché gli anelli collettori di alta qualità che possono supportare alti RPM tendono ad essere molto costosi e più soggetti a usura, ho optato per l'opzione wireless utilizzando un convertitore DC-DC wireless da 5 V. Secondo le specifiche dovrebbe essere possibile trasferire fino a 2 Ampere utilizzando un tale convertitore.
Il convertitore DC-DC wireless è costituito da due componenti, un trasmettitore e un ricevitore. Tenere presente che il PCB collegato alla bobina di induzione trasmittente è più piccolo di quello ricevente.
La piattaforma stessa è costruita utilizzando un pezzo di legno di scarto (250 x 180 x 18 mm).
Sulla piattaforma ho avvitato l'alimentatore Mean Well 12V. L'uscita 12V è collegata all'ESC (vedere gli schemi al punto 1) e al PCB della parte trasmittente del convertitore DC-DC wireless.
Nell'allegato Platform_Files.zip trovi i file dxf per tagliare al laser la piattaforma in compensato con uno spessore di 3 mm:
- Platform_001.dxf e Platform_002.dxf: è necessario posizionarli l'uno sull'altro. Questo creerà un'area incassata per la bobina di induzione trasmittente.
- Magnet_Holder.dxf: Taglia al laser questo disegno tre volte. Una delle tre volte, includi il cerchio. Negli altri due tagli laser: rimuovere il cerchio dal taglio. Dopo aver tagliato, incollare i tre pezzi insieme per creare un supporto per un magnete (diametro 10 mm, spessore: 3 mm). Ho usato la supercolla per incollare il magnete nel supporto del magnete. Assicurati di incollare il lato corretto del magnete al supporto poiché il sensore di hall funzionerà solo con un lato del magnete.
- Platform_Sensor_Cover.dxf: questo pezzo ti aiuterà a mantenere in posizione il sensore hall collegato all'unità di controllo motore come mostrato nella prima immagine.
- Platform_Drill_Template.dxf: ho usato questo pezzo come modello per praticare i fori nel pezzo di legno di scarto. I quattro fori più grandi da 6 mm sono per le barre filettate di supporto con un diametro di 6 mm per supportare la piattaforma. I 4 fori più piccoli servono per fissare il motore brushless al pezzo di legno di scarto. Il foro più grande al centro era necessario per l'asse che sporgeva dal motore brushless. Poiché i bulloni per il motore e le barre filettate per la piattaforma devono essere fissati sul fondo della piattaforma, è necessario allargare quei fori per alcuni mm di profondità per consentire l'inserimento dei dadi.
Sfortunatamente l'albero del motore brushless sporgeva dal lato "sbagliato" per questo progetto. Ma sono stato in grado di invertire l'albero con l'aiuto delle seguenti istruzioni che ho trovato su Youtube:
Una volta fissati il motore e le aste di supporto, la piattaforma può essere costruita utilizzando i pezzi della piattaforma tagliati al laser. La piattaforma stessa può essere fissata utilizzando 8 dadi M6. Il Magnet holder può essere incollato alla piattaforma in corrispondenza del bordo come mostrato nella prima foto.
Il file allegato "Bolt-On Adapter.stl" può essere stampato utilizzando una stampante 3D. Questo adattatore è necessario per collegare un'asta filettata con un diametro di 4 mm al motore Brushless utilizzando 3 bulloni M2 con una lunghezza di 18 mm.
Passaggio 4: involucro rotante
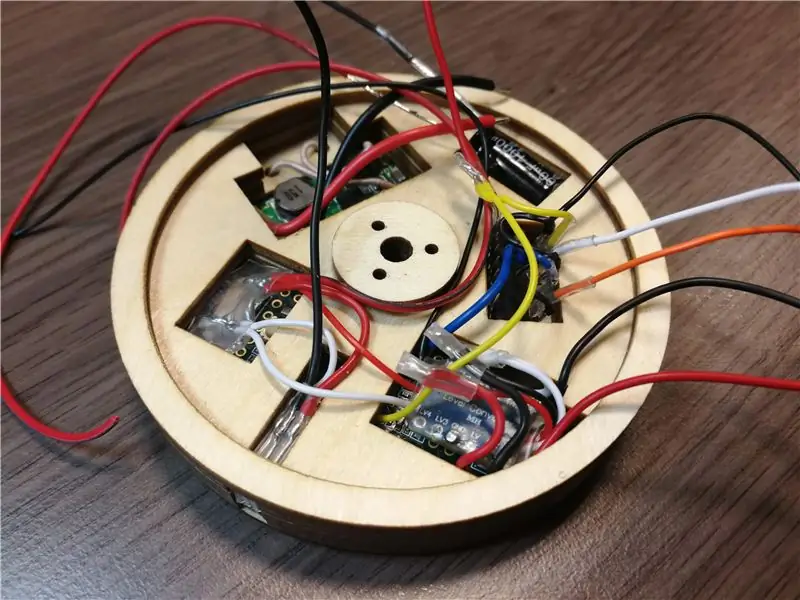
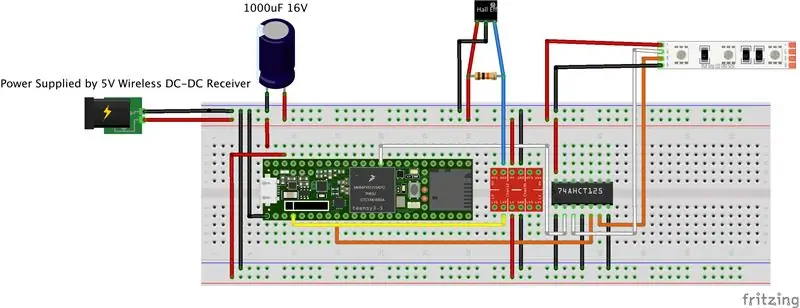
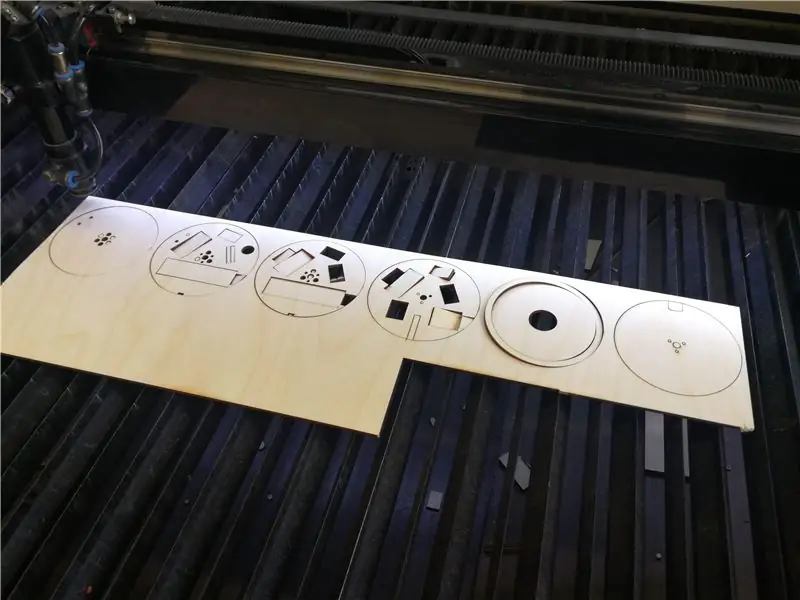
Il Base_Case_Files.zip allegato contiene i file dxf per tagliare al laser i 6 strati per costruire il case per i componenti che controllano la striscia led APA102C.
Gli strati 1-3 del design Case sono pensati per essere incollati insieme. Ma assicurati che un magnete (diametro 10 mm, altezza: 3 mm) sia inserito nel ritaglio circolare nello strato 2 prima di incollare i tre strati insieme. Assicurati inoltre che il magnete sia incollato con il polo corretto al fondo, poiché il sensore ad effetto hall posizionato sulla piattaforma costruita nel passaggio 3 risponderà solo a un lato del magnete.
Il design della custodia contiene scomparti per i componenti elencati negli schemi di cablaggio allegati. L'IC 74AHCT125 è necessario per convertire il segnale da 3,3 V dal Teensy al segnale da 5 V richiesto per la striscia led APA102. Gli strati 4 e 5 possono anche essere incollati insieme. Lo strato superiore 6 può essere impilato sugli altri strati. Tutti gli strati rimarranno nella posizione corretta con l'aiuto di 3 tondini di acciaio con un diametro di 2 mm. Ci sono tre piccoli fori per le aste in acciaio da 2 mm che circondano il foro più grande per l'asta filettata rotante da 4 mm attaccata al motore brushless. Una volta che tutti i componenti sono stati saldati secondo lo schema, la custodia completa può essere posizionata sull'adattatore imbullonato stampato nel passaggio 3. Assicurarsi che tutti i fili aperti siano adeguatamente isolati utilizzando tubi termorestringenti. Si prega di notare che il corretto funzionamento del sensore di hall di questi passaggi dipende dal magnete posizionato nel supporto del magnete descritto al passaggio 3.
Il codice proof of concept allegato 3D_POV_POC.ino illuminerà alcuni led di colore rosso. Lo schizzo risulta in un quadrato che viene visualizzato una volta che il cilindro inizia a ruotare. Ma prima che la rotazione inizi, i led necessari per simulare un quadrato sono accesi di default. Questo è utile per testare il corretto funzionamento dei led nel passaggio successivo.
Passaggio 5: cilindro rotante con strisce LED
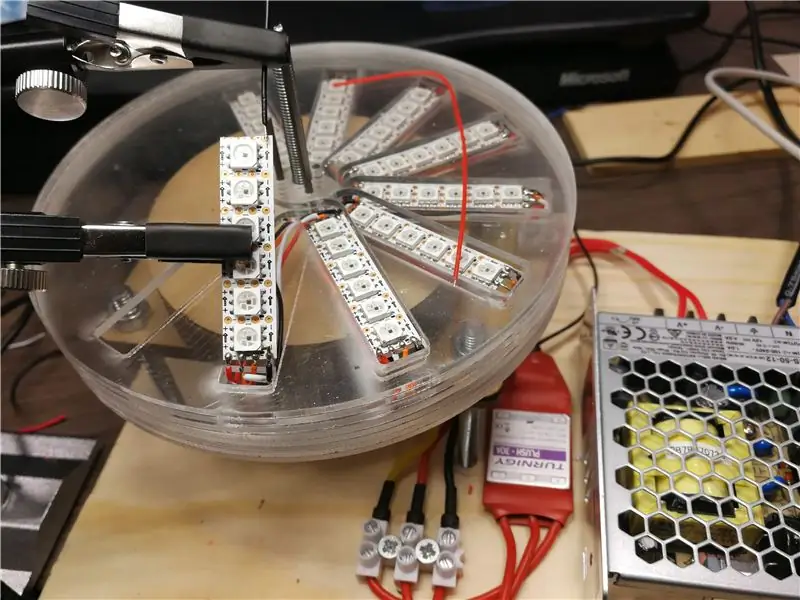
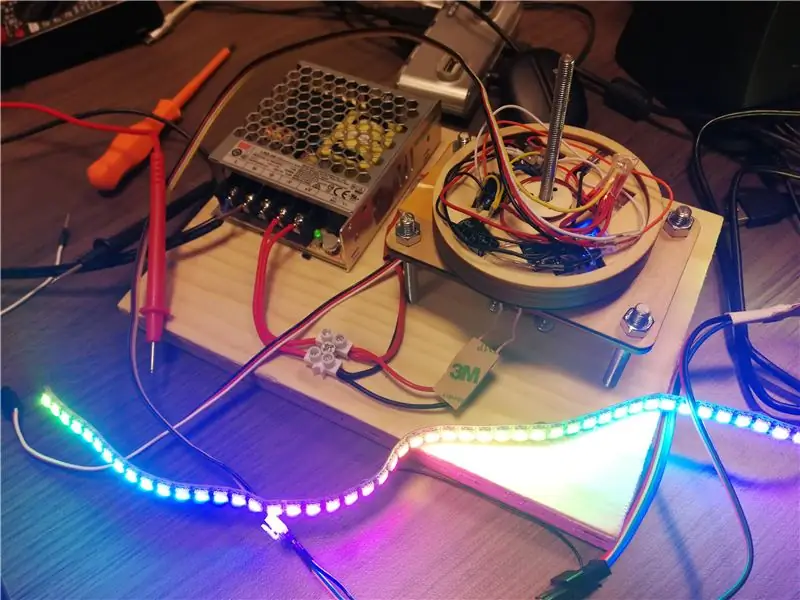
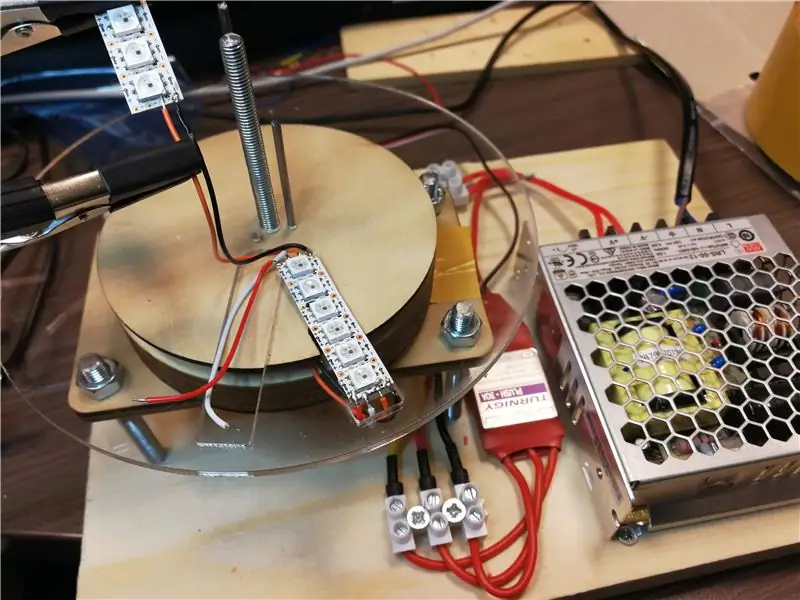
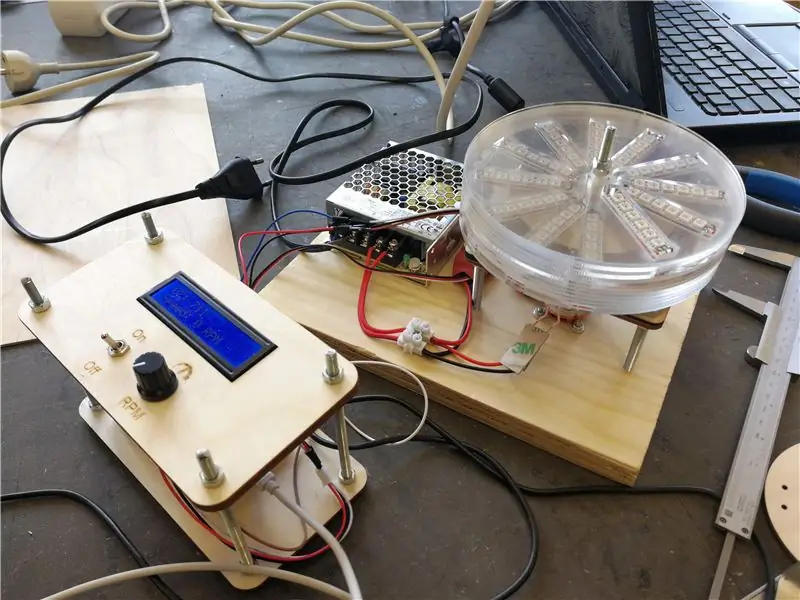
Il Rotor_Cylinder_Files.zip allegato contiene i file dxf per il taglio di un foglio acrilico di 2 mm di spessore. I 14 dischi risultanti sono necessari per costruire il cilindro trasparente per questo progetto POV. I dischi devono essere impilati l'uno sull'altro. Il design dei dischi cilindrici consente di saldare insieme 12 strisce led come una lunga striscia led. Partendo dal disco uno, una piccola striscia led contenente 6 led deve essere attaccata a un disco utilizzando gli adesivi adesivi sulla striscia led. Saldare i fili alla striscia led prima di attaccare le strisce led al disco utilizzando gli adesivi adesivi. Altrimenti corri il rischio che la pistola per saldatura sciolga il disco acrilico.
Una volta che il disco #13 è stato accatastato sul cilindro trasparente, l'asta di acciaio da 2 mm utilizzata per mantenere tutti gli strati nelle posizioni corrette ora può anche essere tagliata alla giusta lunghezza, allineata alla parte superiore del disco #13 del cilindro. Il disco n. 14 può quindi essere utilizzato per mantenere in posizione le aste di acciaio da 2 mm con l'aiuto di due dadi M4.
A causa della quantità di tempo necessaria per costruire l'intero dispositivo, non sono ancora stato in grado di programmare display 3D visivamente interessanti più stabili entro il periodo di tempo dell'hackathon. Questo è anche il motivo per cui il codice fornito per il controllo dei led è ancora molto semplice per dimostrare il concetto, mostrando solo un quadrato rosso 3 dimensionalmente per il momento.
Passaggio 6: lezioni apprese
Adolescente 3.6
- Ho ordinato un Teensy 3.5 per questo progetto, ma il fornitore mi ha inviato per errore un Teensy 3.6. Poiché non vedevo l'ora di finire il progetto entro i tempi dell'hackathon, ho deciso di andare avanti con il Teensy 3.6. Il motivo per cui volevo usare il Teensy 3.5 era a causa delle porte, sono tolleranti a 5V. Questo non è il caso di Teensy 3.6. Questo è anche il motivo per cui ho dovuto introdurre un convertitore logico bidirezionale nella configurazione. Con un Teensy 3.5 questo non sarebbe stato necessario.
- Problema di aumento della potenza: quando si accende il dispositivo, si verifica un aumento della potenza tramite il modulo di ricarica wireless dc-dc per alimentare Teensy 3.6. Sfortunatamente l'accelerazione è troppo lenta perché Teensy 3.6 si avvii correttamente. Come soluzione alternativa, attualmente devo accendere il Teensy 3.6 tramite la connessione micro USB e quindi collegare l'alimentatore da 12 V che alimenta il trasmettitore wireless dc-dc. Una volta che il ricevitore wireless dc-dc fornisce alimentazione anche a Teensy, posso scollegare il cavo USB. Le persone hanno condiviso il loro hack con un MIC803 per il problema dell'aumento lento della potenza qui:
Modulo schermo LCD
Comportamento irregolare con alimentazione esterna. Lo schermo funziona correttamente se alimentato tramite USB. Ma quando accendo lo schermo LCD tramite la breadboard utilizzando i 5V forniti dal BEC o un alimentatore indipendente, il testo inizia a essere criptato dopo pochi secondi dopo che il testo dovrebbe cambiare. Devo ancora indagare su cosa sta causando questo problema
Meccanico
Per testare la mia unità di controllo del motore per misurare gli RPM effettivi, ho lasciato che il motore girasse con il bullone sull'adattatore, il bullone e la custodia di base attaccati al motore. Durante una delle prime corse di prova le viti che collegano il portamotore al motore si svitano a causa delle vibrazioni. Fortunatamente ho notato questo problema in tempo, quindi è stato evitato un potenziale disastro. Ho risolto questo problema avvitando un po' più strettamente le viti al motore e utilizzando anche alcune gocce di Loctite per fissare ancora di più le viti
Software
Quando esporti gli schizzi di Fusion 360 come file dxf per il laser cutter, le linee di supporto vengono esportate come linee regolari
Passaggio 7: potenziali miglioramenti
Cosa avrei fatto diversamente in base all'esperienza che ho acquisito con questo progetto:
- Utilizzando una striscia led contenente almeno 7 led invece di 6 led per strato per alcune visualizzazioni testuali più belle
- Acquista un motore brushless diverso in cui l'albero sporge già dal lato corretto (inferiore) del motore. (es: https://hobbyking.com/de_de/ntm-prop-drive-28-36-1000kv-400w.html) Questo ti farà risparmiare la fatica di tagliare l'albero o di spingere l'albero dal lato corretto come ho fatto io doveva fare adesso.
- Dedicare più tempo al bilanciamento del dispositivo per ridurre al minimo le vibrazioni, meccaniche o modellarlo in Fusion 360.
Ho anche pensato ad alcuni potenziali miglioramenti, che potrei esaminare se il tempo lo consente:
- Utilizzo effettivo della funzionalità della scheda SD su Teensy per creare animazioni più lunghe
- Aumentare la densità dell'imaging utilizzando led più piccoli (APA102(C) 2020). Quando ho iniziato questo progetto qualche settimana fa, le strisce led contenenti questi piccoli led (2x2 mm) non erano facilmente reperibili sul mercato. È possibile acquistarli come componenti SMD separati, ma prenderei in considerazione questa opzione solo se si desidera saldare questi componenti su un PCB personalizzato.
- Trasferisci le immagini 3D in modalità wireless al dispositivo (Wifi o Bluetooth). Ciò dovrebbe anche consentire di programmare il dispositivo per visualizzare suoni/musica.
- Converti le animazioni di Blender in un formato di file che può essere utilizzato con il dispositivo
- Metti tutte le strisce led sulla piastra di base e focalizza la luce sugli strati di acrilico. Su ogni diverso strato possono essere incise piccole aree per riflettere la luce quando omessa dai led. La luce dovrebbe essere focalizzata sulle aree incise. Ciò dovrebbe essere possibile creando un tunnel che guidi la luce o utilizzando lenti sui led per focalizzare la luce.
- Miglioramento della stabilità del display volumetrico 3D e regolazione della velocità di rotazione separando la base rotante dal motore brushless tramite ingranaggi e cinghia dentata.
Passaggio 8: gridare
Desidero ringraziare in modo particolare le seguenti persone:
- La mia fantastica moglie e le mie figlie, per il loro supporto e comprensione.
- Teun Verkerk, per avermi invitato all'Hackathon
- Nabi Kambiz, Nuriddin Kadouri e Aidan Wyber, per il vostro supporto, assistenza e guida durante l'Hackaton
- Luuk Meints, un artista e un altro partecipante di questo Hackaton, è stato così gentile da offrirmi un corso di introduzione personale di 1 ora a Fusion 360 che mi ha permesso di modellare tutte le parti di cui avevo bisogno per questo progetto.
Consigliato:
Pannello laterale trasparente fai-da-te da un monitor riciclato!: 8 passaggi (con immagini)
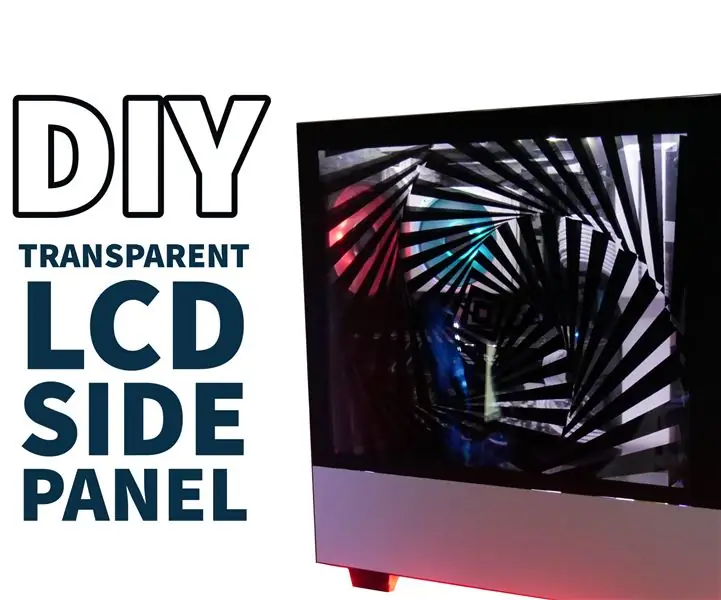
Pannello laterale trasparente fai-da-te da un monitor riciclato!: Ho visto un video davvero interessante di un case per PC chiamato "Snowblind", che aveva uno schermo LCD trasparente come pannello laterale. Sono rimasto stupito da quanto fosse bello. L'unico problema era che era davvero costoso. Pertanto, ho provato a crearne uno mio! In questo io
Smartphone trasparente: 4 passaggi (con immagini)
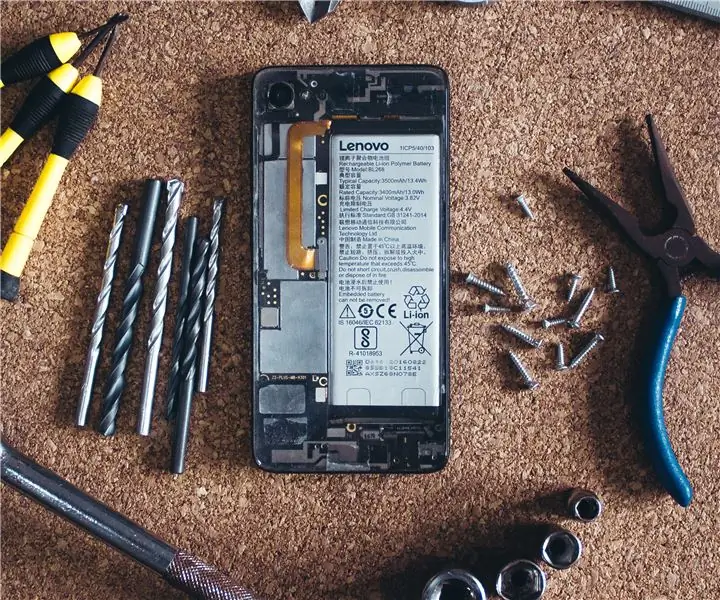
Smartphone trasparente: iscriviti al mio corso "Elettronica in poche parole" qui: https://www.udemy.com/electronics-in-a-nutshell/?… Dai un'occhiata anche al mio canale YouTube qui per altri progetti e tutorial sull'elettronica : https://www.youtube.com/channel/UCelOORs7UioZ4TZF…A
Lastre olografiche - Photonics Challenger Hackathon PhabLabs: 6 passaggi
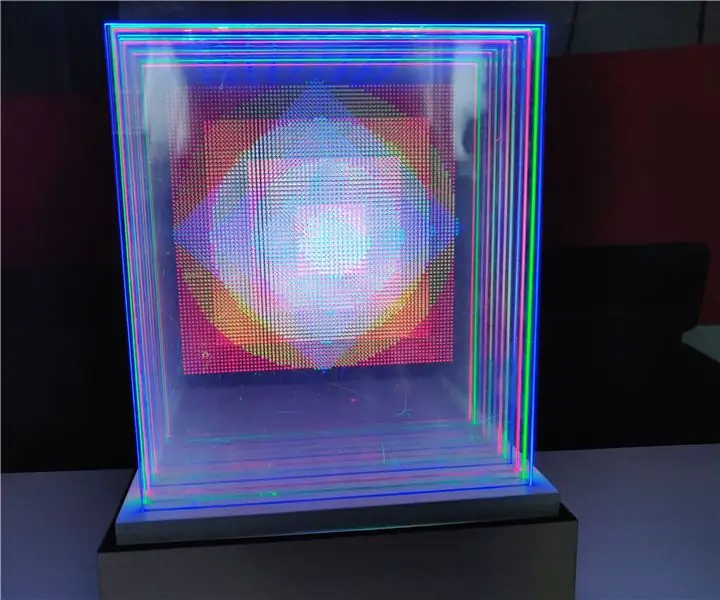
Lastre olografiche - Photonics Challenger Hackathon PhabLabs: All'inizio di quest'anno mi è stato chiesto di partecipare al PhabLabs Photonics Hackathon presso il Science Centre Delft nei Paesi Bassi. Qui hanno un grande spazio di lavoro con molte macchine che potrebbero essere utilizzate per creare qualcosa che io normale
Matrice LED trasparente flessibile enorme a meno di $ 150. Facile da realizzare: 8 passaggi (con immagini)
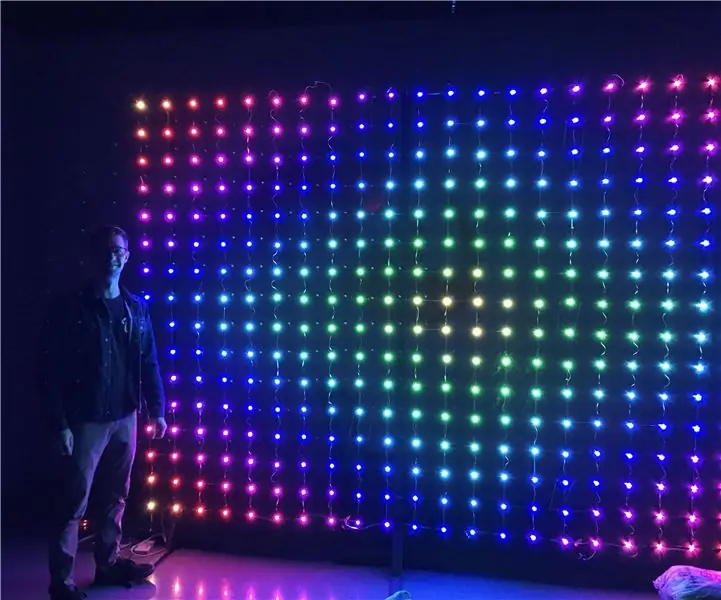
Matrice LED trasparente flessibile enorme a meno di $ 150. Facile da realizzare.: Voglio iniziare dicendo che non sono un professionista, non ho una laurea in elettronica. Mi piace semplicemente lavorare con le mie mani e capire le cose. Lo dico per incoraggiare tutti voi non professionisti come me. Hai la capacità di
Rendi trasparente il MOTORE CC: 4 passaggi (con immagini)
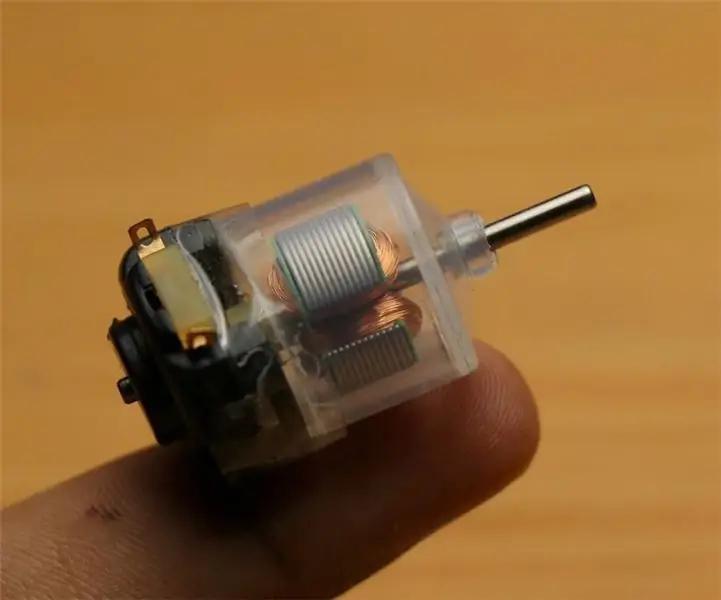
Rendi il motore CC trasparente: ciao amici in questo tutorial ti mostrerò come modificare il motore CC giocattolo in motore CC trasparente in passaggi molto semplici e una cosa speciale qui sono i materiali necessari per renderlo disponibile a casa tua:) È un progetto ideale per la fiera della scienza t