![Driver del motore CC che utilizza i Power Mosfet [Controllo PWM, 30A Half Bridge]: 10 passaggi Driver del motore CC che utilizza i Power Mosfet [Controllo PWM, 30A Half Bridge]: 10 passaggi](https://i.howwhatproduce.com/images/003/image-6762-j.webp)
Sommario:
- Passo 1:
- Passaggio 2: Figura-1, il diagramma schematico del potente driver del motore CC
- Passaggio 3:
- Passaggio 4: Figura-2, layout PCB progettato per lo schema del driver del motore
- Passaggio 5: Figura-3, librerie di componenti selezionate per IR2104 e IRFN150N
- Passaggio 6: Figura-4, una vista 3D della scheda PCB del driver del motore
- Passaggio 7: Figura 5, il primo prototipo del design (su un PCB semi-fatto in casa), vista dall'alto
- Passaggio 8: Figura 6, una vista dal basso del prototipo della scheda PCB, le tracce scoperte
- Passaggio 9: Figura 7, un filo di rame nudo spesso
- Passaggio 10: Tabella-1, Distinta dei materiali del circuito
2025 Autore: John Day | [email protected]. Ultima modifica: 2025-01-23 14:49
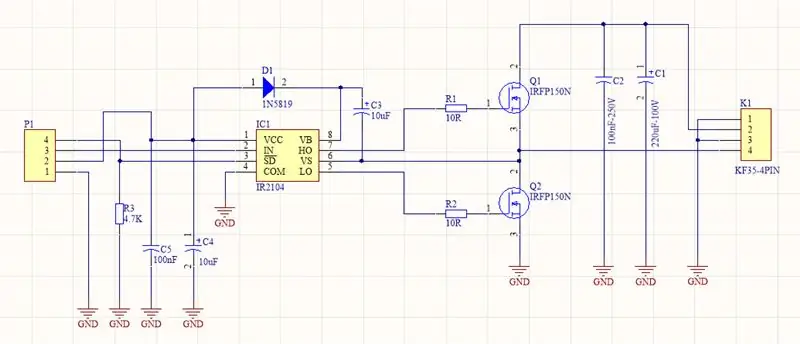
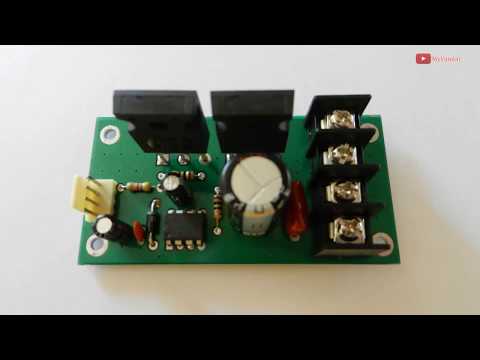
Fonte principale (Scarica Gerber/Ordina il PCB):
Passo 1:
I motori DC sono ovunque, dalle applicazioni per hobby alla robotica e alle aree industriali. Pertanto c'è un ampio utilizzo e la richiesta di driver per motori DC adatti e potenti. In questo articolo impareremo a costruirne uno. Puoi controllarlo utilizzando un microcontrollore, un Arduino, un Raspberry Pi o anche un chip generatore PWM autonomo. Utilizzando un adeguato dissipatore di calore e metodi di raffreddamento, questo circuito può gestire correnti fino a 30A.
[1]: Analisi del circuitoIl cuore del circuito è un chip driver MOSFET IR2104 [1]. È un CI driver MOSFET popolare e applicabile. Il diagramma schematico del circuito mostrato in figura-1.
Passaggio 2: Figura-1, il diagramma schematico del potente driver del motore CC
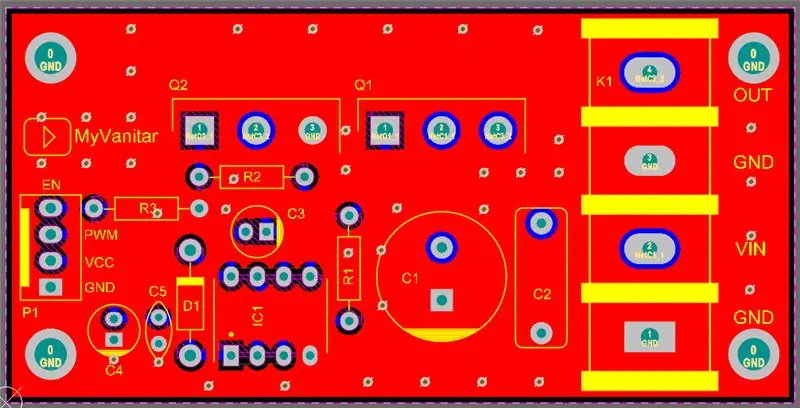
Passaggio 3:
Secondo la scheda tecnica IR2104 [1]:”Gli IR2104(S) sono MOSFET di potenza ad alta tensione e ad alta velocità e driver IGBT con canali di uscita referenziati high e low side dipendenti. Le tecnologie proprietarie HVIC e latch immuni CMOS consentono una costruzione monolitica rinforzata. L'ingresso logico è compatibile con l'uscita CMOS standard o LSTTL, fino a 3,3 V di logica. I driver di uscita sono dotati di uno stadio buffer ad alta corrente a impulsi progettato per ridurre al minimo la conduzione incrociata del driver. Il canale flottante può essere utilizzato per pilotare un MOSFET o IGBT di potenza a canale N nella configurazione high side che opera da 10 a 600 volt. L'IR2104 pilota i MOSFET [2] in una configurazione a semiponte. Non ci sono problemi con l'elevata capacità di ingresso dei MOSFET IRFP150. Questo è il motivo per cui i driver MOSFET come IR2104 sono utili. I condensatori C1 e C2 vengono utilizzati per ridurre il rumore del motore e l'EMI. La tensione massima tollerabile dei MOSFET è 100V. Quindi ho usato almeno condensatori da 100V. Se sei sicuro che la tua tensione di carico non superi una soglia (ad esempio un motore da 12 V CC), puoi diminuire le tensioni dei condensatori ad esempio a 25 V e aumentare invece i loro valori di capacità (ad esempio 1000 uF-25 V). Il pin SD è stato abbassato con un resistore da 4,7K. Quindi è necessario applicare una tensione di livello logico a stato stazionario a questo pin per attivare il chip. Devi iniettare anche il tuo impulso PWM al pin IN.
[2]: Scheda PCB
Il layout PCB dello schema mostrato in figura-2. È progettato in modo da ridurre il rumore e i transitori per aiutare la stabilità del dispositivo.
Passaggio 4: Figura-2, layout PCB progettato per lo schema del driver del motore
Non avevo l'impronta del PCB e i simboli schematici dei componenti IR2104 [1] e IRFP150 [2]. Pertanto utilizzo i simboli forniti da SamacSys [3] [4], invece di sprecare il mio tempo e progettare le librerie da zero. Puoi utilizzare il "motore di ricerca dei componenti" o un plug-in CAD. Poiché ho usato Altium Designer per disegnare lo schema e il PCB, ho usato direttamente il plugin SamacSys Altium [5] (figura-3).
Passaggio 5: Figura-3, librerie di componenti selezionate per IR2104 e IRFN150N
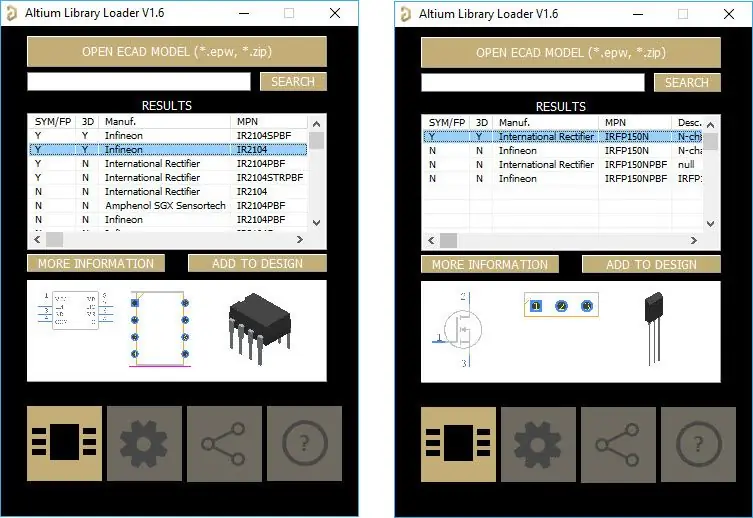
La Figura-4 mostra una vista 3D della scheda PCB. La vista 3D migliora la procedura di ispezione della scheda e il posizionamento dei componenti.
Passaggio 6: Figura-4, una vista 3D della scheda PCB del driver del motore
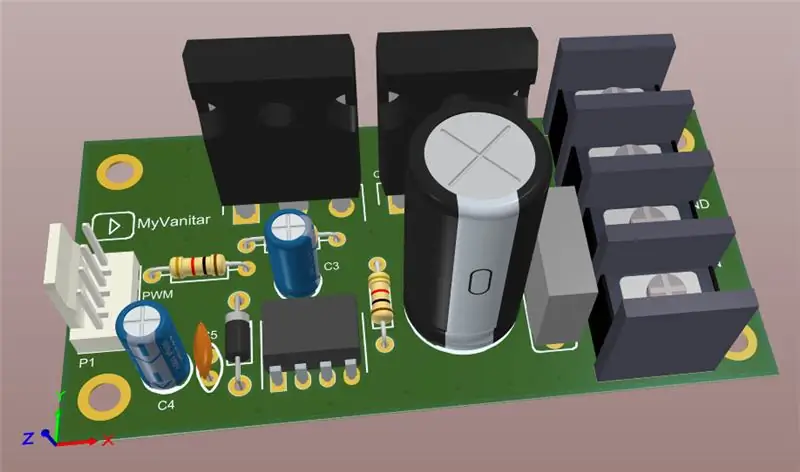
[3] AssemblaggioCosì costruiamo e costruiamo il circuito. Ho appena usato una scheda PCB semi-fatta in casa per poter assemblare rapidamente la scheda e testare il circuito (figura-5).
Passaggio 7: Figura 5, il primo prototipo del design (su un PCB semi-fatto in casa), vista dall'alto
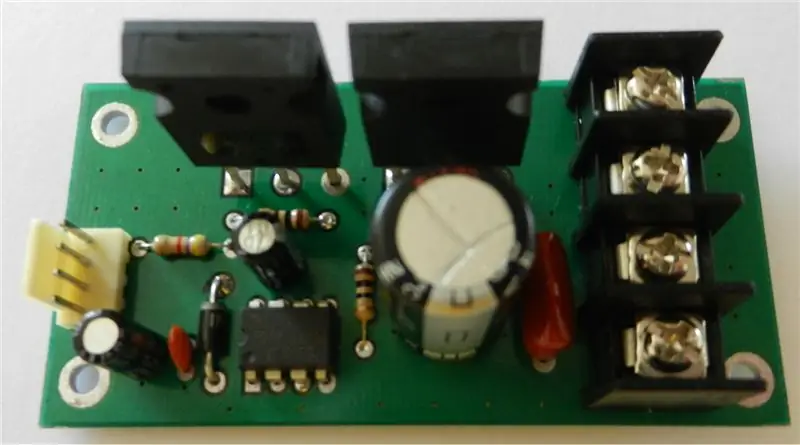
Dopo aver letto questo articolo, sei sicuro al 100% del vero funzionamento del circuito. Pertanto, ordina il PCB a un'azienda di fabbricazione di PCB professionale, come PCBWay, e divertiti con la tua scheda di saldatura e assemblata. La Figura 6 mostra una vista dal basso della scheda PCB assemblata. Come puoi vedere, alcune tracce non sono state completamente coperte con la maschera di saldatura. Il motivo è che queste tracce potrebbero trasportare una quantità significativa di corrente, quindi hanno bisogno di un supporto in rame aggiuntivo. Una normale pista PCB non può tollerare una quantità elevata di corrente e alla fine si riscalderà e brucerà. Per superare questa sfida (con un metodo economico), è necessario saldare uno spesso filo di rame nudo (figura-7) sulle aree scoperte. Questo metodo migliora la capacità di trasmissione corrente della traccia.
Passaggio 8: Figura 6, una vista dal basso del prototipo della scheda PCB, le tracce scoperte
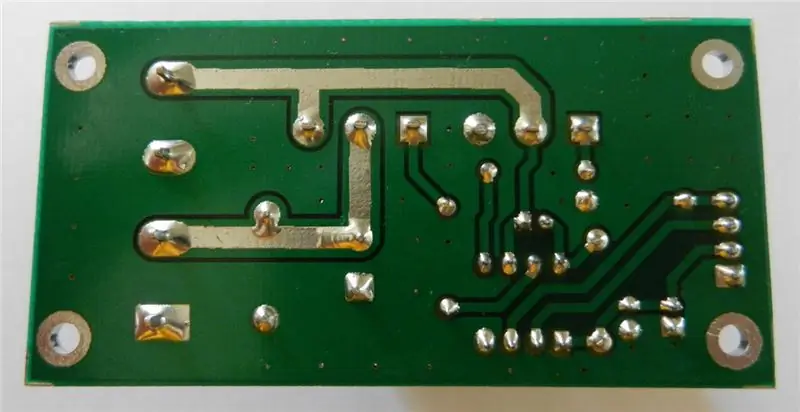
Passaggio 9: Figura 7, un filo di rame nudo spesso
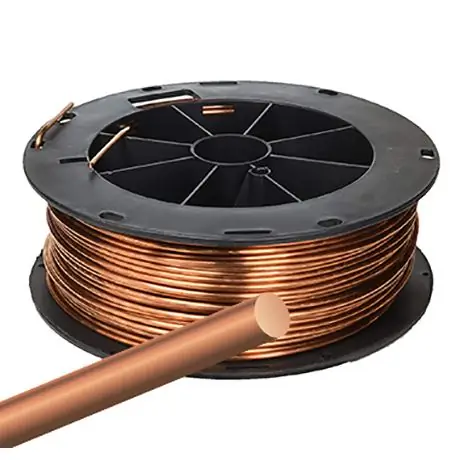
[4] Test e misurazioni Il video YouTube fornito dimostra un test effettivo della scheda con il motore CC del tergicristallo di un'auto come carico. Ho fornito l'impulso PWM con un generatore di funzioni e ho esaminato gli impulsi sui fili del motore. Inoltre, è stata dimostrata la correlazione lineare del consumo di corrente del carico con il ciclo di lavoro PWM.
[5] Distinta base
La tabella-1 mostra la distinta base.
Passaggio 10: Tabella-1, Distinta dei materiali del circuito
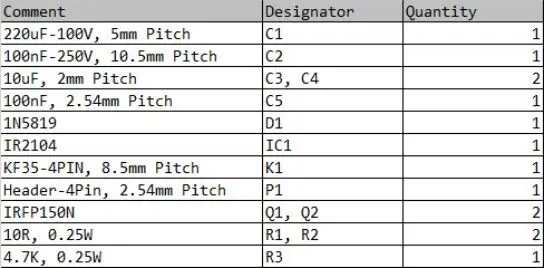
Riferimenti [1]:
[2]:
[3]:
[4]:
[5]:
[6]: Sorgente (Scaricamento Gerber/Ordine del PCB)
Consigliato:
Robot a controllo vocale che utilizza il modulo V3: 6 passaggi
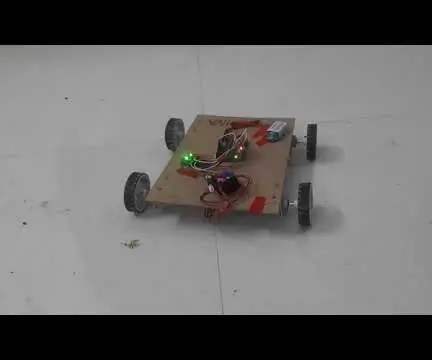
Robot a controllo vocale che utilizza il modulo V3: questo robot può essere realizzato facilmente da chiunque, basta seguire il processo come ho indicato. Questo è un robot a controllo vocale e puoi vedere la demo del mio robot puoi usarlo in due modi in un modo è da remoto e altro è a voce
Motore passo-passo controllato da motore passo-passo - Motore passo-passo come encoder rotativo: 11 passaggi (con immagini)
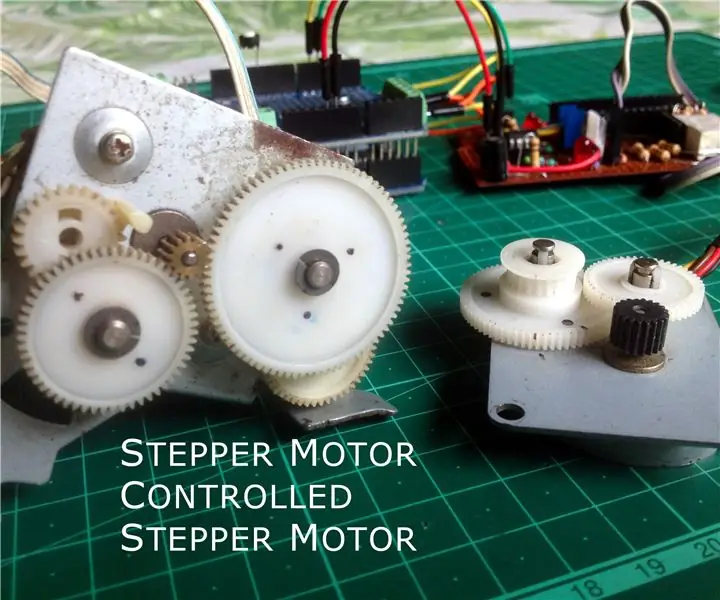
Motore passo-passo controllato da motore passo-passo | Motore passo-passo come encoder rotativo: hai un paio di motori passo-passo in giro e vuoi fare qualcosa? In questo Instructable, utilizziamo un motore passo-passo come encoder rotativo per controllare la posizione di un altro motore passo-passo utilizzando un microcontrollore Arduino. Quindi, senza ulteriori indugi, ge
Driver del motore ad alta corrente fai-da-te (h-bridge): 5 passaggi
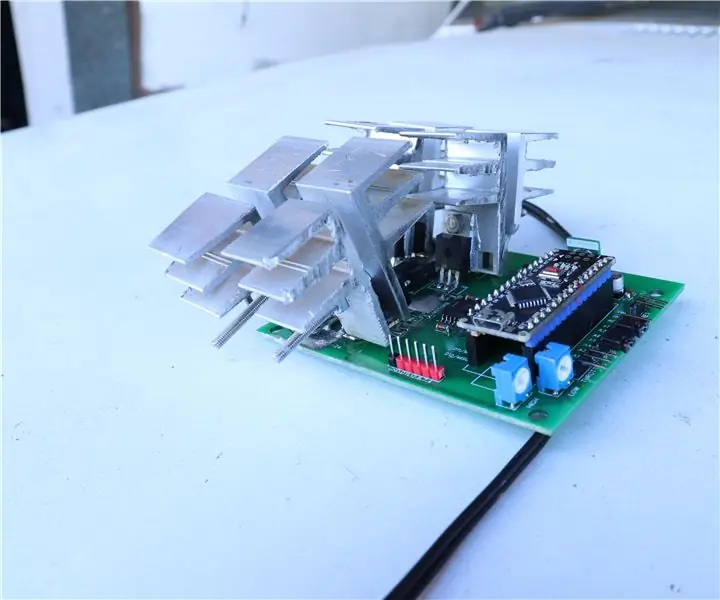
Driver del motore ad alta corrente fai-da-te (ponte h): il progetto è quello di aggiornare i motori e l'elettronica in questo quad per bambini Power Wheels. Deluso dalle prestazioni di questo mini-quad da 12 V. abbiamo programmato di passare a un sistema a 24 V con 2 nuovi motori a spazzole traxxis 775 dopo aver effettuato ricerche commerciali
Sistema di sterzo intelligente per auto robot che utilizza il motore passo-passo del vecchio lettore floppy/CD: 8 passaggi (con immagini)
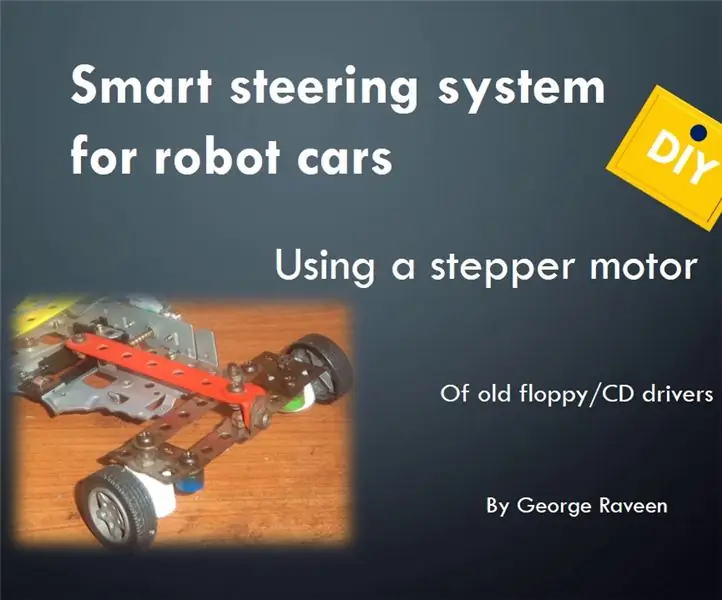
Sistema di sterzo intelligente per auto robot che utilizza il motore passo-passo del vecchio lettore floppy/CD: sistema di sterzo intelligente per auto robot Sei preoccupato di realizzare un buon sistema di sterzo per la tua auto robot? Ecco una soluzione superba usando solo le tue vecchie unità floppy/CD/DVD. guardalo e fatti un'ideaVisita georgeraveen.blogspot.com
Robot che evita gli ostacoli utilizzando il driver del motore L298n: 5 passaggi
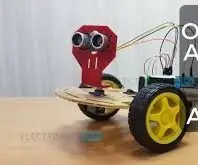
Robot che evita ostacoli usando il driver del motore L298n: ciao ragazzi oggi realizzeremo questo robot .. spero che vi piaccia