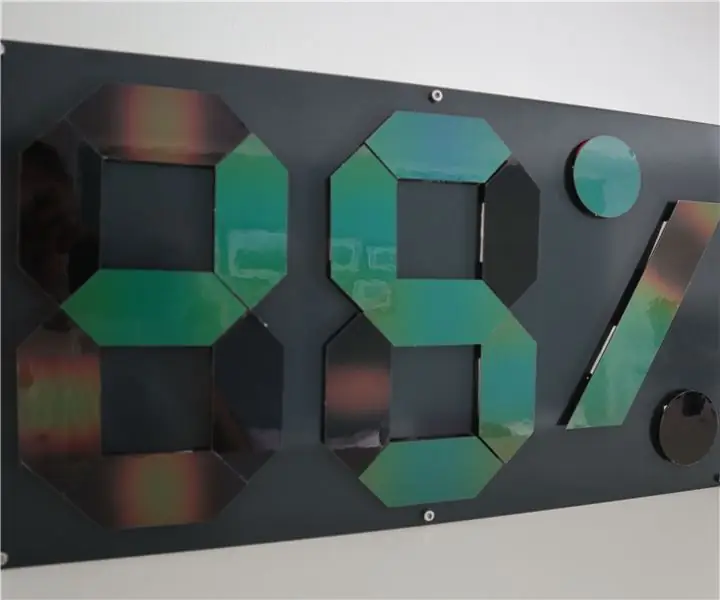
Sommario:
- Forniture
- Passaggio 1: realizzare le lastre di rame
- Passaggio 2: collegamento del foglio a cristalli liquidi
- Passaggio 3: collegamento dell'elemento TEC
- Passaggio 4: preparazione della piastra in alluminio
- Passaggio 5: collegamento dei segmenti
- Passaggio 6: collegamento di dissipatori di calore e supporti
- Passaggio 7: caricamento del codice
- Passaggio 8: follia di cablaggio
- Passaggio 9: preparazione della lastra acrilica
- Passaggio 10: progetto finito
2025 Autore: John Day | [email protected]. Ultima modifica: 2025-01-23 14:49
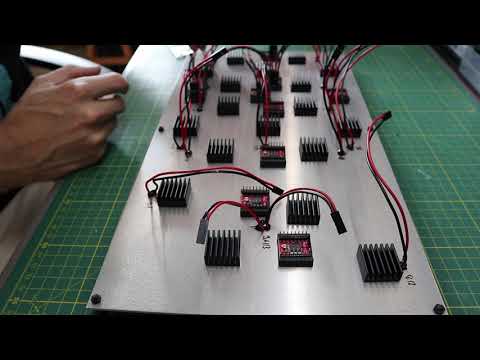
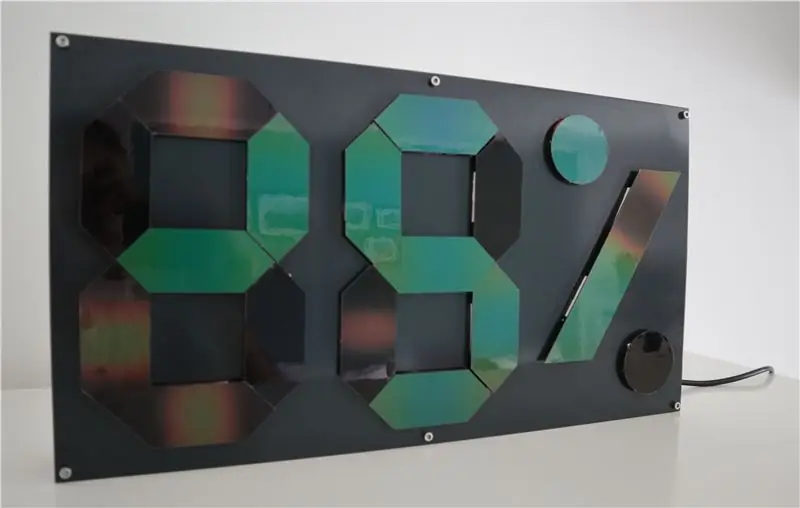

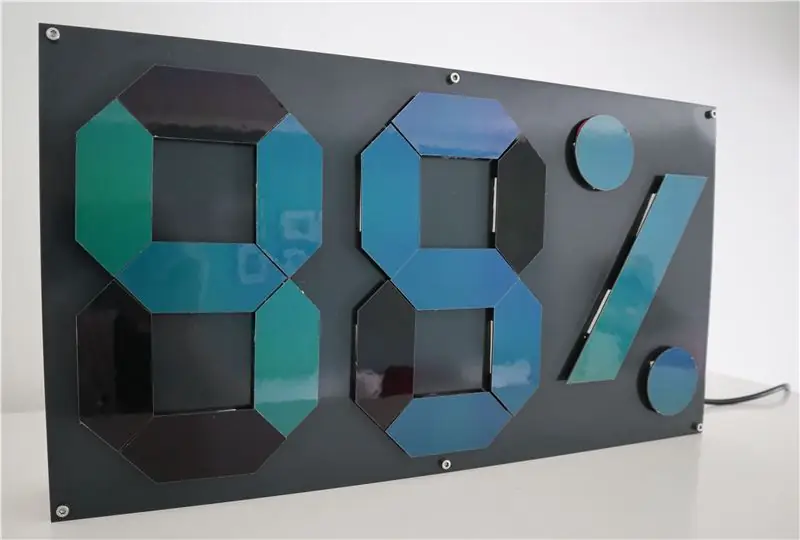
Sto lavorando a questo progetto da un po' di tempo. L'idea originale mi è venuta dopo aver costruito un dimostratore di controller TEC al lavoro per una fiera. Per mostrare le capacità di riscaldamento e raffreddamento dei TEC abbiamo utilizzato una vernice termocromica che cambia dal nero al trasparente.
In questo progetto ho portato avanti l'idea e ho costruito un display a 7 segmenti a due cifre utilizzando lastre di rame ricoperte da fogli termocromici a base di cristalli liquidi. Dietro ogni lastra di rame si trova un elemento TEC che controlla la temperatura e quindi cambia il colore del foglio di cristalli liquidi. I numeri mostreranno la temperatura e l'umidità da un sensore DHT22.
Potresti apprezzare l'ironia di avere un dispositivo che visualizza la temperatura ambiente modificando la propria temperatura;-)
Forniture
- 3 pz, lastra a cristalli liquidi 150x150 mm (29-33°C) (vedi qui).
- 17 pezzi, lastre di rame, spessore 1 mm (dimensioni vedi sotto)
- Piastra in alluminio 401 x 220 x 2 mm (anodizzata grigia/nera)
- Lastra acrilica 401 x 220 x 2 mm (bianca)
- 18 pezzi, elemento Peltier TES1-12704
- 9 pezzi, driver doppio motore TB6612FNG
- 6 pezzi, Arduino Nano
- 2 pezzi, ventola di raffreddamento 40x40x10 mm
- 18 pezzi, dissipatore di calore 25x25x10 mm
- Alimentazione 12 V, 6 A
- DHT22 (AM2302) sensore di temperatura e umidità
- 6 pezzi, distanziatori PCB lunghi 40 mm
Inoltre, ho usato questa resina epossidica termicamente conduttiva che era piuttosto economica e ha un lungo pot life. Un trapano e uno strumento dremel sono stati utilizzati per realizzare i fori necessari nelle lastre di alluminio e acrilico. Il supporto per gli arduino e i PCB del driver del motore sono stati stampati in 3D e fissati con colla a caldo. Inoltre, ho usato un sacco di cavi Dupont per fare tutti i collegamenti. Inoltre, questo PCB con terminali a vite è stato molto utile per distribuire l'alimentazione a 12 V.
Attenzione: a quanto pare, molte delle schede TB6612FNG hanno i condensatori sbagliati installati. Sebbene tutti i venditori specifichino la scheda per tensioni del motore fino a 15 V, i condensatori sono spesso classificati solo per 10 V. Dopo aver bruciato i condensatori sulle mie prime due schede, li ho dissaldati tutti e li ho sostituiti con quelli corretti.
Passaggio 1: realizzare le lastre di rame
Per le lastre di rame ho utilizzato un servizio di taglio laser online (vedi qui) dove ho potuto caricare i file dxf allegati. Tuttavia, poiché le forme non sono molto complicate, il taglio laser non è obbligatorio e probabilmente esistono tecniche di produzione più economiche (ad es. punzonatura, segatura). In totale, per il display sono necessari 14 dei segmenti, due cerchi e un trattino. Lo spessore delle lastre di rame era di 1 mm, ma potrebbe probabilmente essere ridotto a 0,7 o 0,5 mm, il che richiederebbe meno potenza di riscaldamento/raffreddamento. Ho usato il rame perché la capacità termica e la conduttività termica sono superiori all'alluminio, ma anche quest'ultimo dovrebbe funzionare abbastanza bene.
Passaggio 2: collegamento del foglio a cristalli liquidi
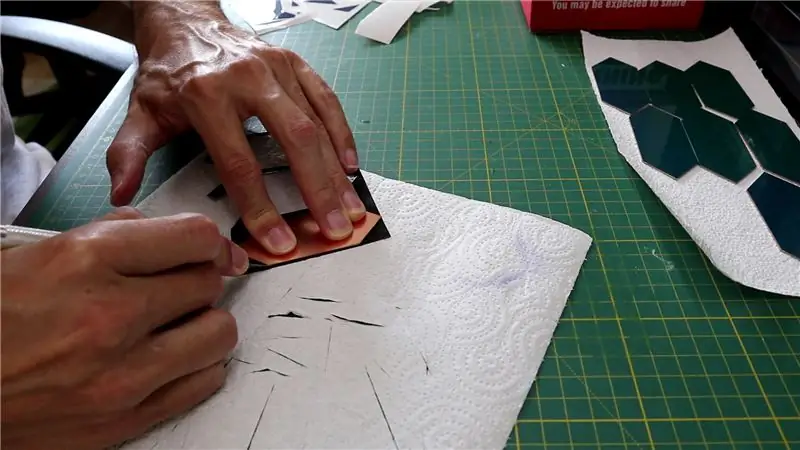
Il componente chiave di questo progetto è la lamina a cristalli liquidi termocromica che ho ottenuto da SFXC. La pellicola è disponibile in diversi intervalli di temperatura e cambia colore dal nero alle basse temperature al rosso, arancione e verde al blu alle alte temperature. Ho provato due diverse larghezze di banda 25-30°C e 29-33°C e alla fine ho scelto quest'ultima. Poiché il riscaldamento con un elemento peltier è più facile che il raffreddamento, l'intervallo di temperatura dovrebbe essere leggermente al di sopra della temperatura ambiente.
La pellicola a cristalli liquidi ha un supporto autoadesivo che aderisce molto bene alle lastre di rame. La pellicola in eccesso è stata tagliata attorno al piatto usando un coltello esatto.
Passaggio 3: collegamento dell'elemento TEC
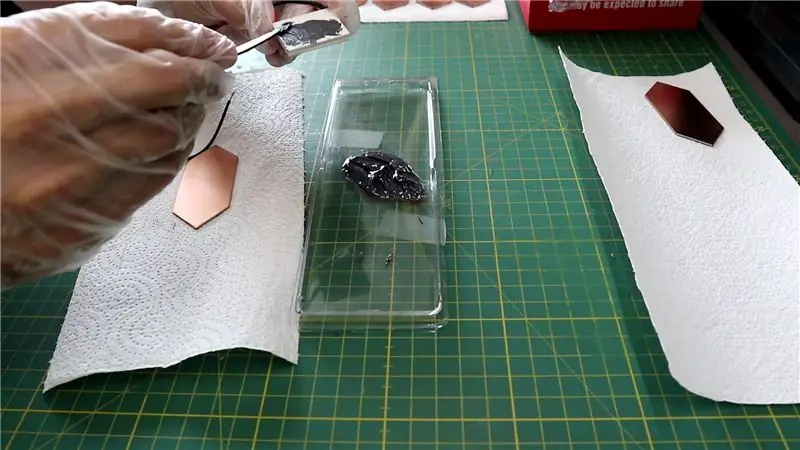
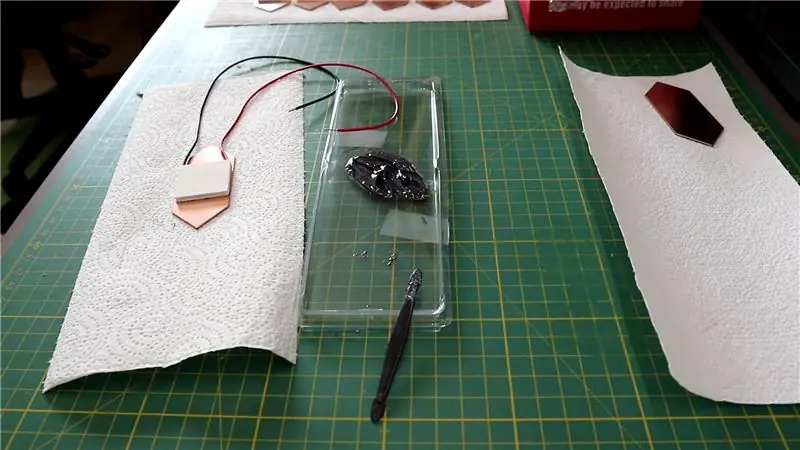
I peltier sono stati fissati al centro di ciascuna piastra di rame utilizzando resina epossidica termicamente conduttiva. I piatti sono un po' più grandi dei peltier in modo che rimangano completamente nascosti dietro. Per il piatto più lungo che costituisce il trattino del simbolo di percentuale ho usato due peltier.
Passaggio 4: preparazione della piastra in alluminio
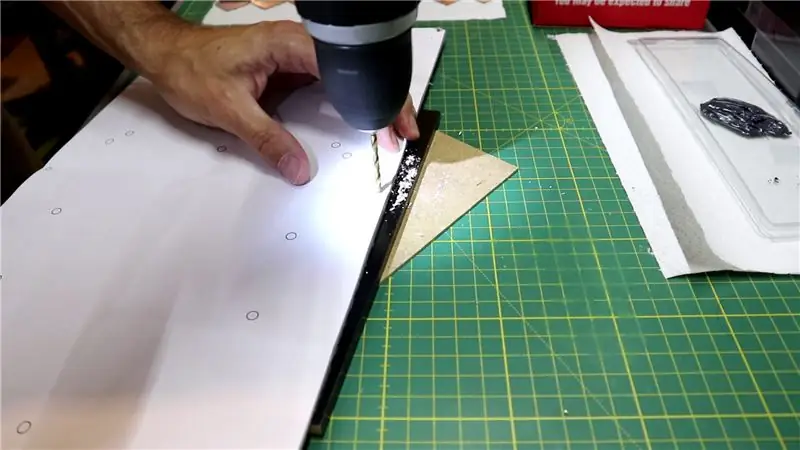
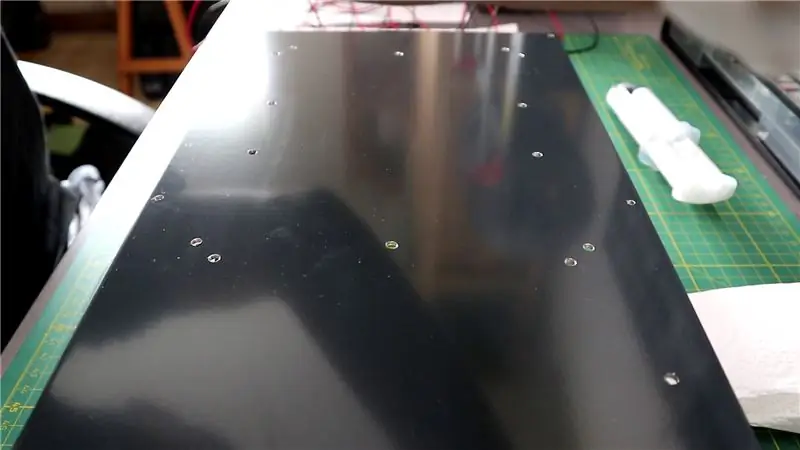
Per risparmiare un po' di soldi ho praticato io stesso tutti i fori nella piastra di alluminio. Ho appena stampato il pdf allegato su carta A3 e l'ho usato come dima di foratura. C'è un foro per ogni segmento in cui passano i cavi TEC e 6 fori sui bordi per il fissaggio successivo della piastra acrilica.
Passaggio 5: collegamento dei segmenti
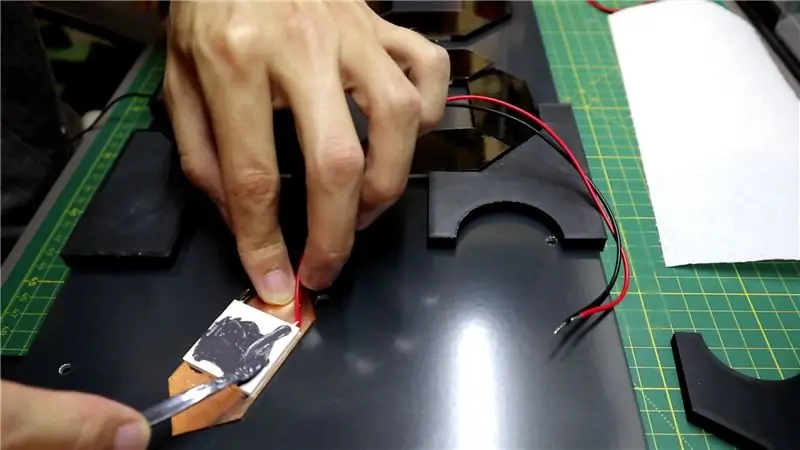
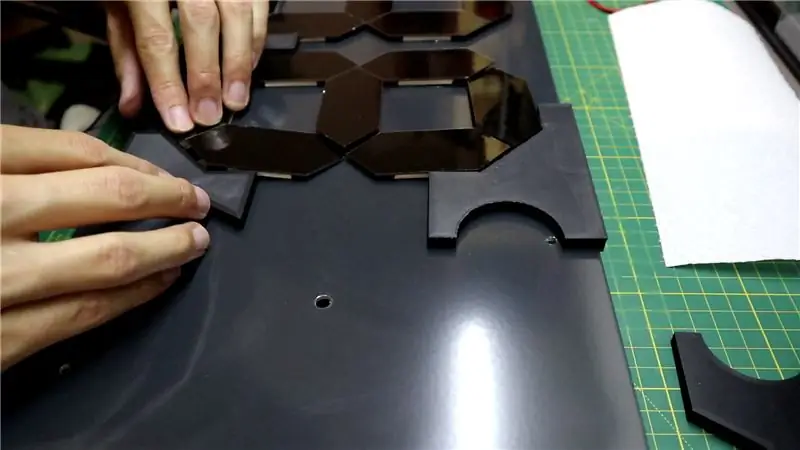
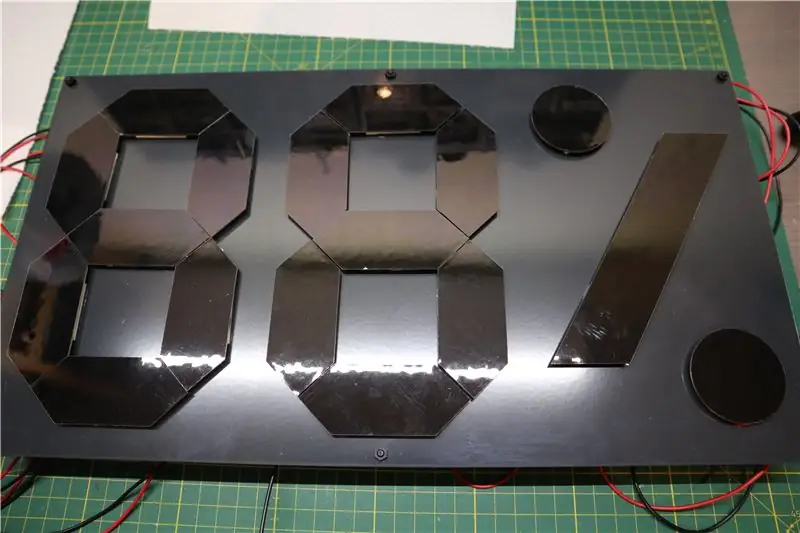
Una delle parti più difficili in questo progetto è stata quella di attaccare correttamente i segmenti alla piastra posteriore. Ho stampato in 3D diverse maschere che mi avrebbero aiutato con l'allineamento dei segmenti, ma questo ha funzionato solo in parte perché i segmenti scivolavano costantemente via. Inoltre, i cavi spingono sul peltier in modo che si allenti dalla piastra. In qualche modo sono riuscito a incollare tutti i segmenti nel posto giusto, ma uno dei peltier nel segmento del cruscotto ha un pessimo accoppiamento termico. Potrebbe essere meglio usare pad termici autoadesivi invece di resina epossidica, anche se sospetto che possa allentarsi nel tempo.
Passaggio 6: collegamento di dissipatori di calore e supporti
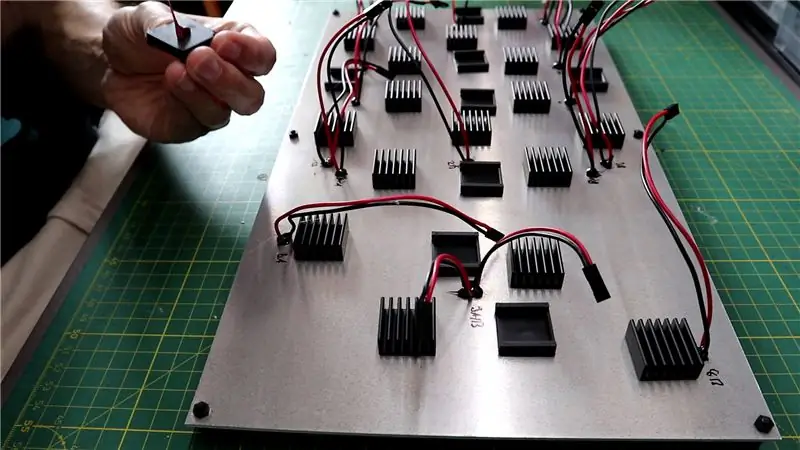
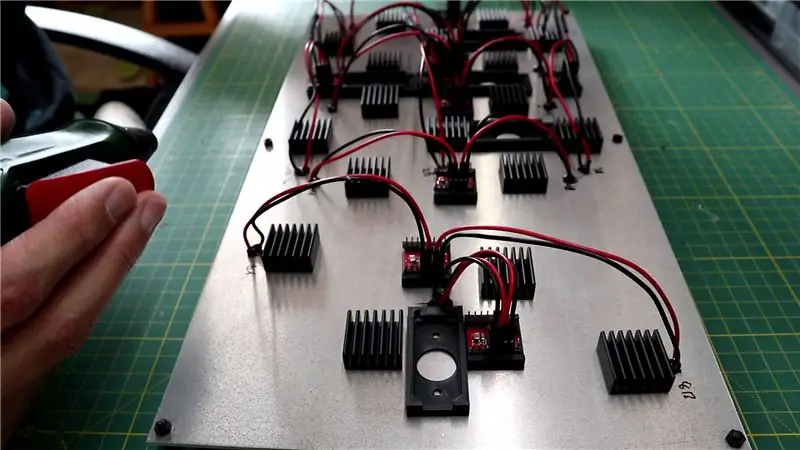
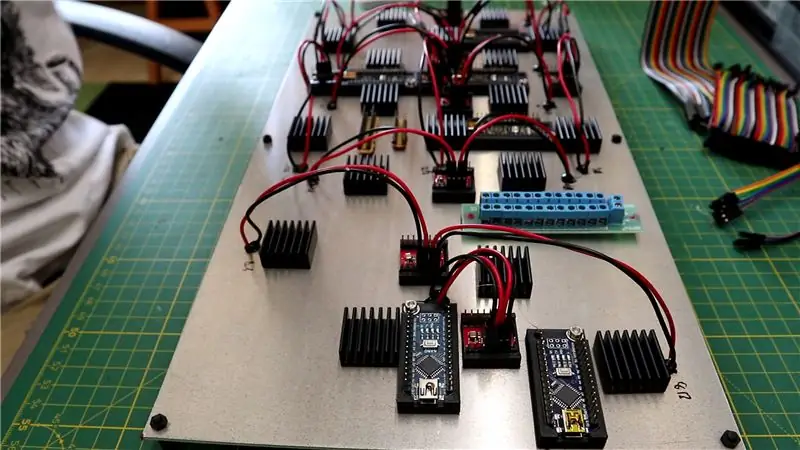
La mia idea originale era di usare solo la piastra in alluminio come dissipatore di calore per i peltier anche senza ventola. Ho pensato che la temperatura totale della piastra aumenterà solo leggermente poiché alcuni segmenti vengono raffreddati mentre altri vengono riscaldati. Tuttavia, si è scoperto che senza ulteriori dissipatori di calore e senza ventola di raffreddamento, la temperatura continuerà a salire fino a un punto in cui le piastre di rame non possono più essere raffreddate. Ciò è particolarmente problematico poiché non utilizzo termistori per controllare la potenza di riscaldamento/raffreddamento, ma utilizzo sempre un valore fisso. Pertanto, ho acquistato piccoli dissipatori di calore con un pad autoadesivo che sono stati attaccati alla parte posteriore della piastra di alluminio dietro ogni peltier.
Successivamente, i supporti stampati in 3D per i driver del motore e gli arduino sono stati fissati anche sul retro della piastra utilizzando la colla a caldo.
Passaggio 7: caricamento del codice
Ogni arduino può controllare solo fino a due driver del motore poiché hanno bisogno di due pin PWM e 5 IO digitali. Esistono anche driver per motori controllabili tramite I2C (vedi qui) ma non sono compatibili con la logica a 5 V degli arduino. Nel mio circuito c'è un arduino "master" che comunica con 5 arduino "slave" tramite I2C che a loro volta controllano i driver del motore. Il codice per arduino può essere trovato qui sul mio account GitHub. Nel codice per gli arduino "slave" l'indirizzo I2C deve essere cambiato per ogni arduino nell'intestazione. Sono inoltre presenti alcune variabili che consentono di modificare la potenza di riscaldamento/raffreddamento e le relative costanti di tempo.
Passaggio 8: follia di cablaggio
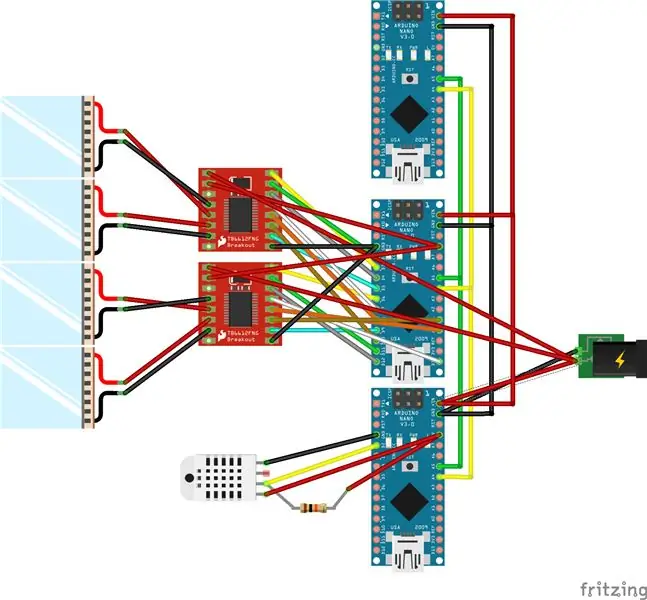
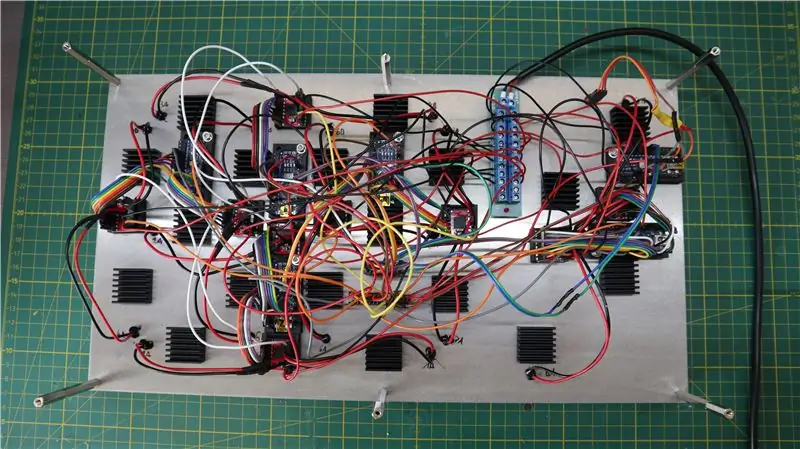
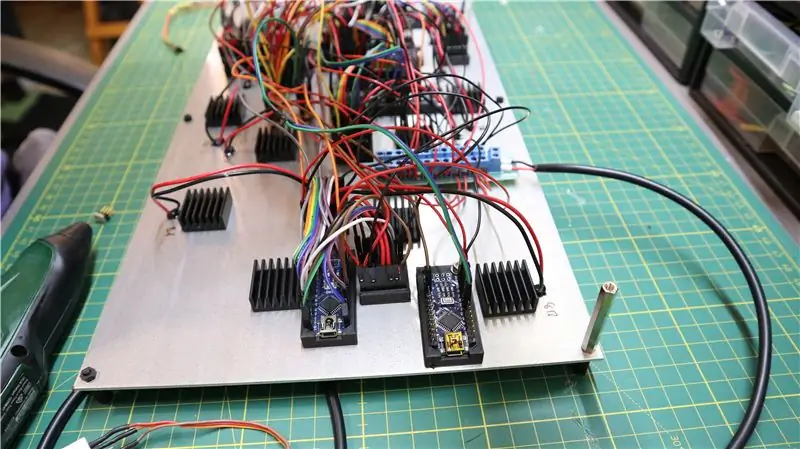
Il cablaggio di questo progetto è stato un incubo totale. Ho allegato un diagramma fritzing che mostra le connessioni per il master arduino e un singolo arduino slave come esempio. Inoltre, c'è un pdf che documenta quale TEC è collegato a quale driver del motore e arduino. Come puoi vedere dalle immagini a causa della grande quantità di connessioni, il cablaggio diventa molto disordinato. Ho usato connettori dupont ovunque fosse possibile. L'alimentazione a 12 V è stata distribuita tramite PCB con morsetti a vite. All'ingresso di alimentazione ho collegato un cavo CC con conduttori volanti. Per distribuire le connessioni 5 V, GND e I2C ho dotato alcuni prototipi di PCB con connettori maschio.
Passaggio 9: preparazione della lastra acrilica
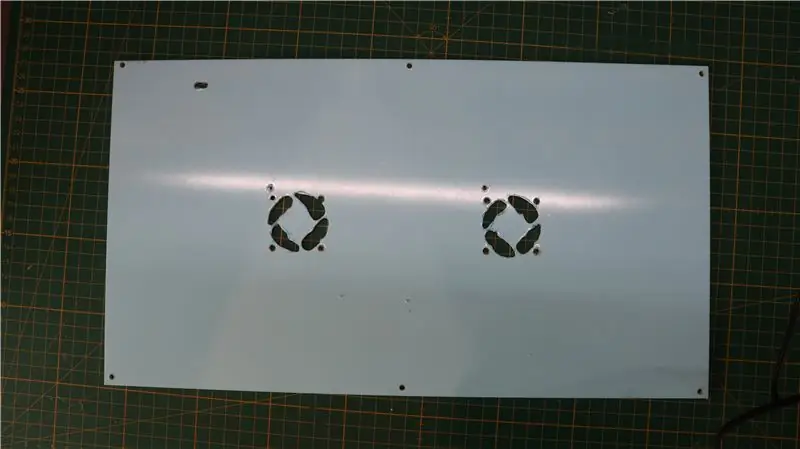
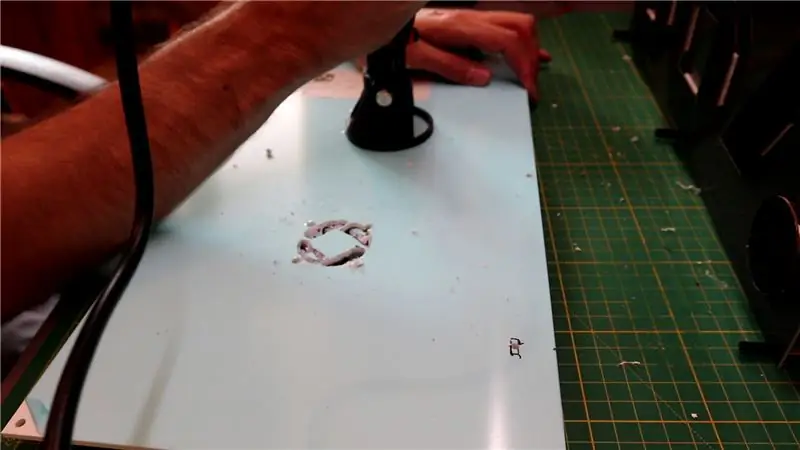
Successivamente, ho praticato alcuni fori nella lastra acrilica in modo che possa essere fissata alla lastra di alluminio tramite i distanziatori del PCB. Inoltre, ho realizzato alcuni ritagli per le ventole e una fessura per il cavo del sensore DHT22 utilizzando il mio strumento Dremel. Dopodiché le ventole sono state attaccate alla parte posteriore della lastra acrilica e i cavi sono stati fatti passare attraverso alcuni fori che ho praticato. La prossima volta probabilmente realizzerò la lastra con il taglio laser.
Passaggio 10: progetto finito
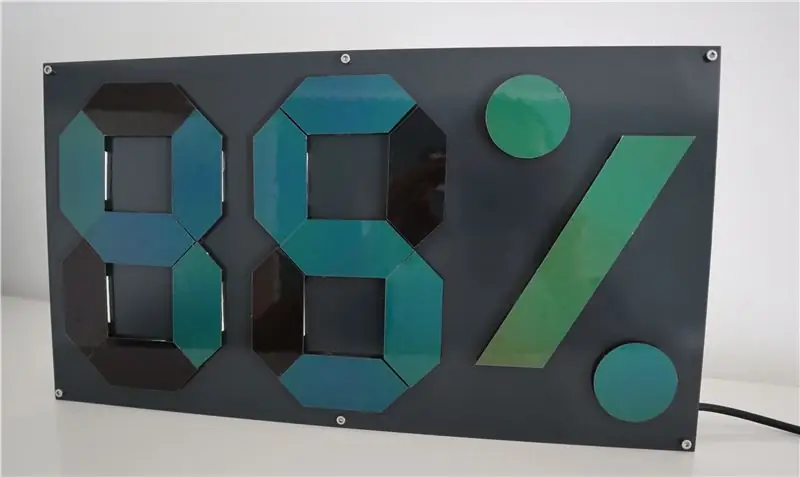
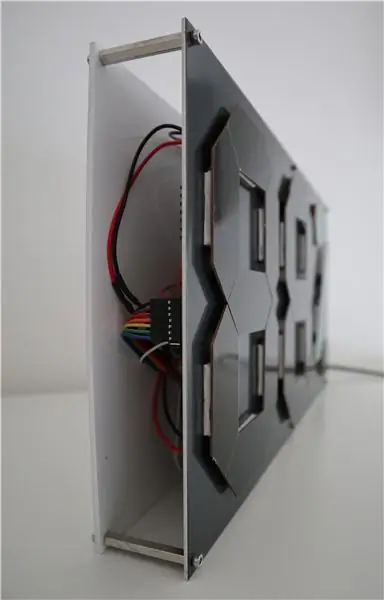
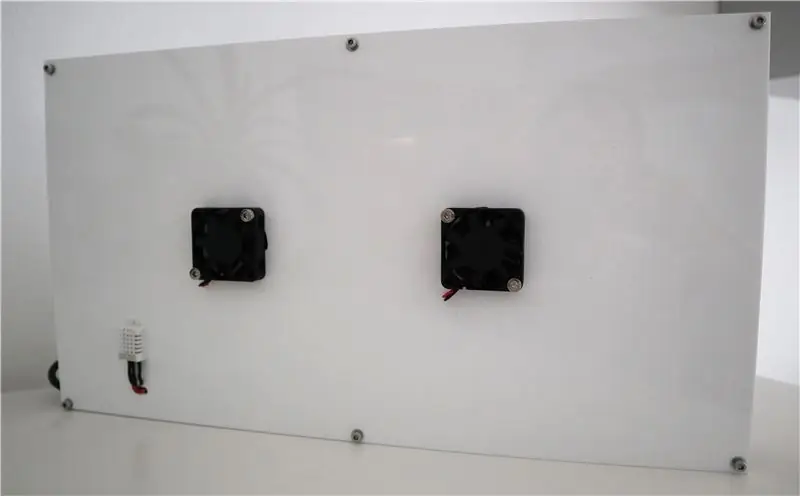
Infine, la piastra in acrilico e la piastra in alluminio sono state fissate l'una all'altra utilizzando distanziatori PCB lunghi 40 mm. Dopo di che il progetto è finito.
Una volta collegati all'alimentazione, i segmenti mostreranno la temperatura e l'umidità, alternativamente. Per la temperatura, solo il punto superiore cambierà colore mentre anche il trattino e il punto inferiore vengono evidenziati quando viene mostrata l'umidità.
Nel codice ogni segmento attivo viene riscaldato per 25 secondi raffreddando contemporaneamente i segmenti non attivi. Dopodiché i peltier vengono spenti per 35 secondi in modo che la temperatura possa stabilizzarsi nuovamente. Tuttavia, la temperatura delle lastre di rame aumenterà nel tempo e ci vorrà del tempo prima che i segmenti cambino completamente colore. L'assorbimento di corrente per una singola cifra (7 segmenti) è stato misurato in circa 2 A, quindi l'assorbimento di corrente totale per tutti i segmenti è probabilmente vicino al massimo di 6 A che l'alimentatore può fornire.
Si potrebbe certamente ridurre il consumo di energia aggiungendo termistori come feedback per regolare la potenza di riscaldamento/raffreddamento. Un ulteriore passo avanti sarebbe quello di utilizzare un controller TEC dedicato con loop PID. Questo dovrebbe probabilmente consentire un funzionamento costante senza molto consumo di energia. Attualmente sto pensando di costruire un sistema del genere utilizzando i driver Thorlabs MTD415T TEC.
Un altro svantaggio con la configurazione attuale è che si può sentire l'uscita PWM a 1 kHz dei driver del motore. Sarebbe anche bello se ci si sbarazzasse dei fan perché sono anche piuttosto rumorosi.
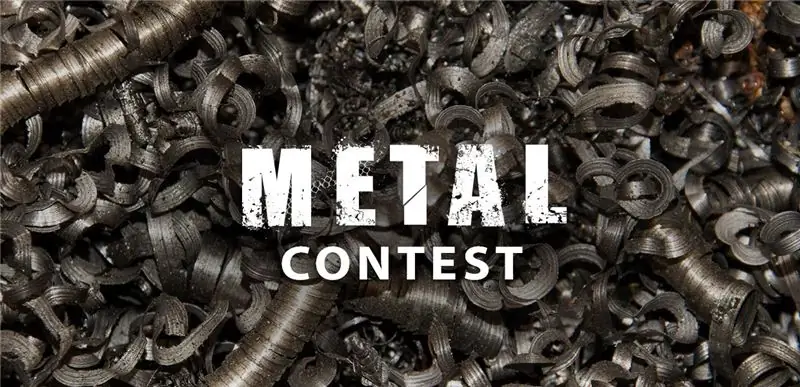
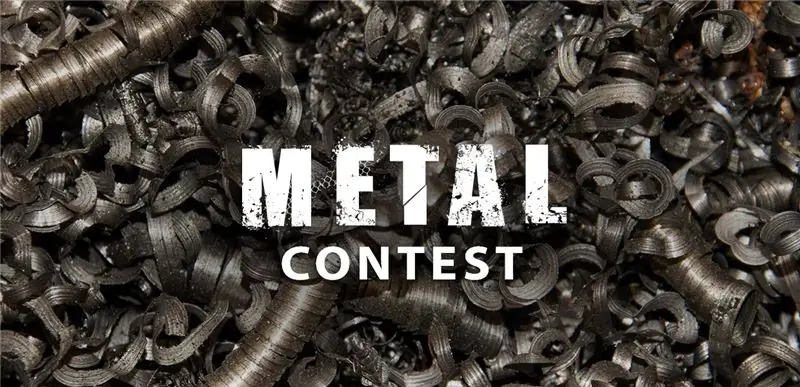
Primo Premio al Metal Contest
Consigliato:
Monitoraggio della temperatura e dell'umidità della stanza con ESP32 e AskSensors Cloud: 6 passaggi
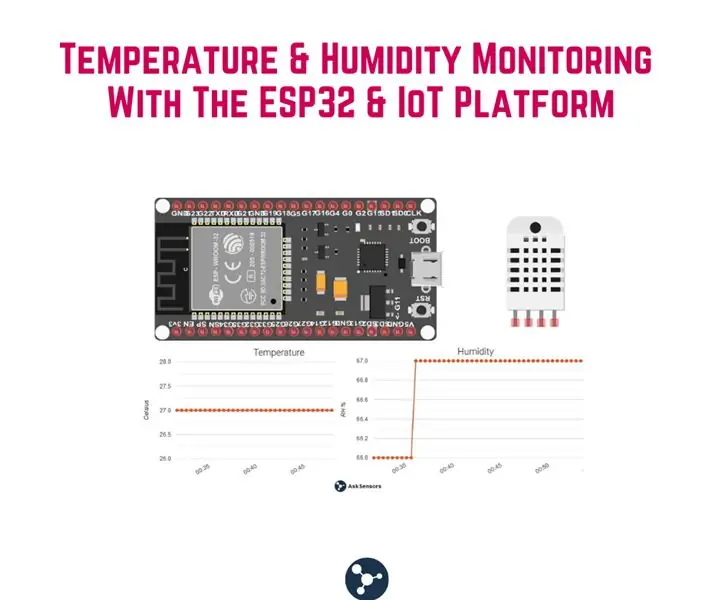
Monitoraggio della temperatura e dell'umidità della stanza con ESP32 e AskSensors Cloud: In questo tutorial imparerai come monitorare la temperatura e l'umidità della tua stanza o scrivania utilizzando il DHT11 e l'ESP32 collegati al cloud. I nostri aggiornamenti dei tutorial possono essere trovati qui.DHT11 Specifiche: il sensore DHT11 è in grado di misurare la temperatura
Display termocromico di temperatura e umidità - Versione PCB: 6 passaggi (con immagini)
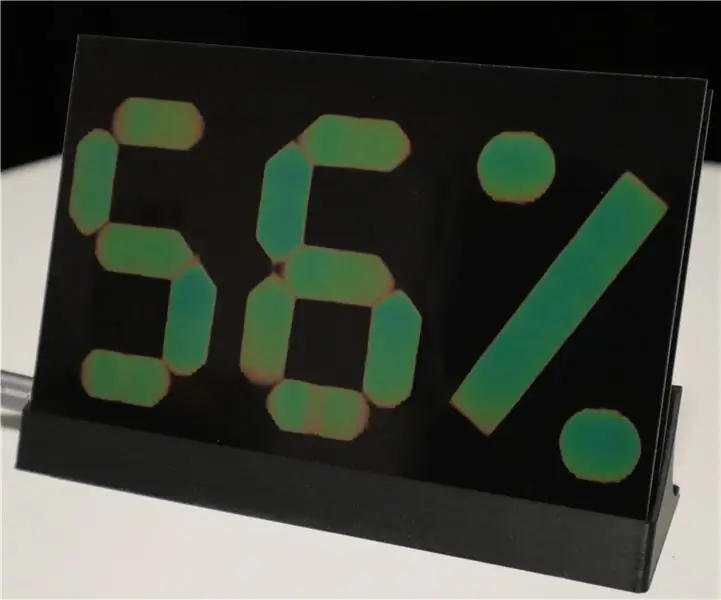
Display termocromico per temperatura e umidità - Versione PCB: qualche tempo fa ho realizzato un progetto chiamato Termocromico per temperatura e umidità; Display dell'umidità in cui ho costruito un display a 7 segmenti con piastre di rame riscaldate/raffreddate da elementi peltier. Le lastre di rame erano ricoperte da una lamina termocromica che
Monitoraggio della temperatura e dell'umidità con Raspberry Pi: 6 passaggi (con immagini)
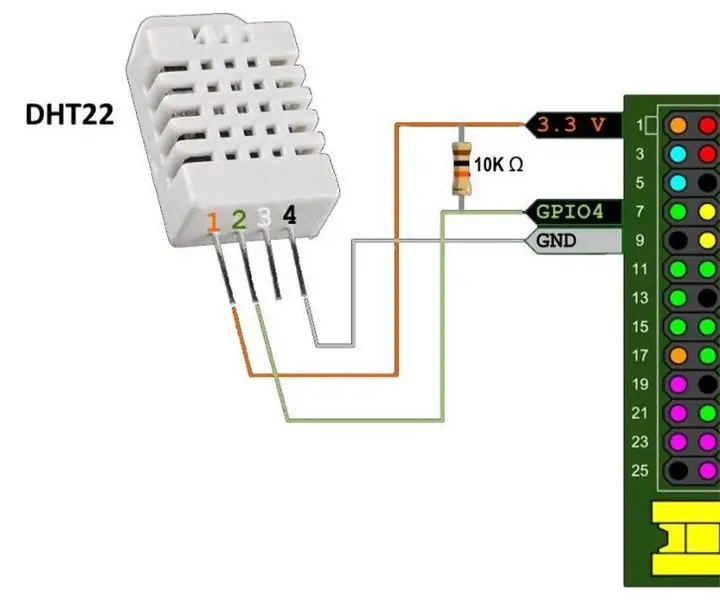
Monitoraggio della temperatura e dell'umidità tramite Raspberry Pi: l'estate sta arrivando e chi non ha un condizionatore d'aria dovrebbe essere pronto a controllare manualmente l'atmosfera all'interno. In questo post descrivo il modo moderno di misurare i parametri più importanti per il comfort umano: temperatura e umidità. T
Display dell'umidità della temperatura 24 ore su Arduino: 3 passaggi (con immagini)
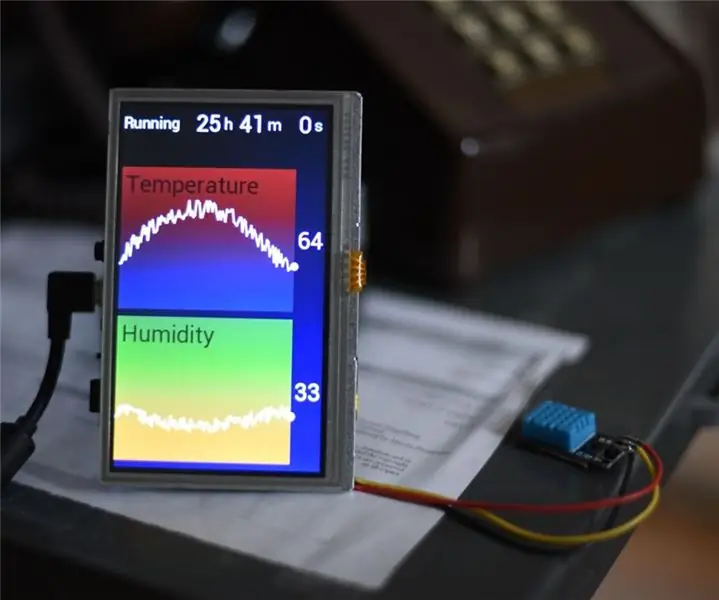
Display dell'umidità della temperatura 24 ore su Arduino: il DHT11 è un ottimo sensore con cui iniziare. È economico e facile da collegare a un Arduino. Riporta la temperatura e l'umidità con una precisione di circa il 2% e questo istruibile utilizza un Gameduino 3 come display grafico, mostrando 24 ore di cronologia
Controlla i tuoi elettrodomestici con il telecomando della tua TV (telecomando ir) con display della temperatura e dell'umidità: 9 passaggi
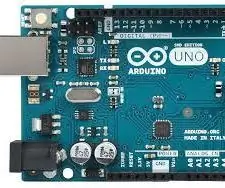
Controlla i tuoi elettrodomestici con il telecomando della tua TV (telecomando a infrarossi) con display di temperatura e umidità: ciao sono Abhay ed è il mio primo blog su Instructables e oggi ti mostrerò come controllare i tuoi elettrodomestici con il telecomando della tua TV costruendo questo progetto semplice. grazie al laboratorio atl per il supporto e la fornitura del materiale