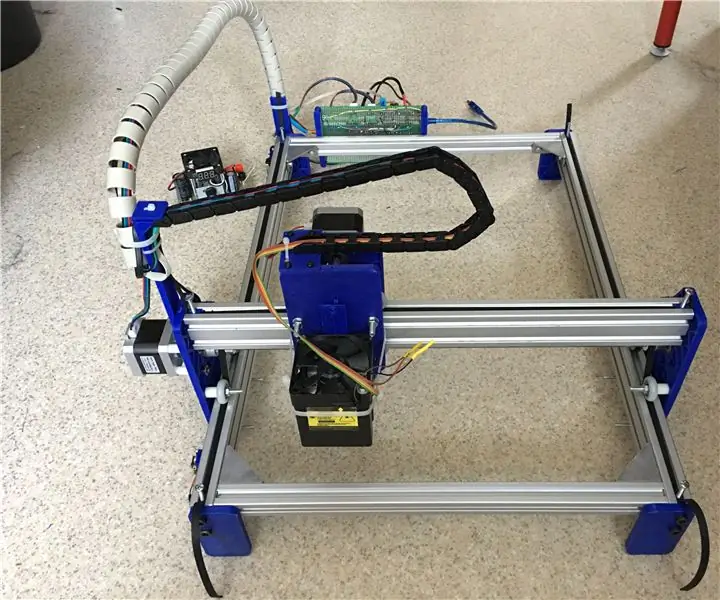
Sommario:
- Passaggio 1: Distinta base
- Passaggio 2: file di stampa STL
- Passaggio 3: parti stampate in 3D
- Passaggio 4: strumenti necessari
- Passaggio 5: preparativi
- Passaggio 6: il telaio principale
- Passaggio 7: assicurati che le dimensioni di stampa siano corrette e metti insieme il carrello
- Passaggio 8: asse e motore
- Passaggio 9: il supporto laser/motore e le cinture
- Passaggio 10: i finecorsa + i supporti
- Passaggio 11: l'elettronica
- Passaggio 12: software
- Passaggio 13: calibrazione
- Passaggio 14: pronto
- Passaggio 15: ultimo passaggio
2025 Autore: John Day | [email protected]. Ultima modifica: 2025-01-23 14:49
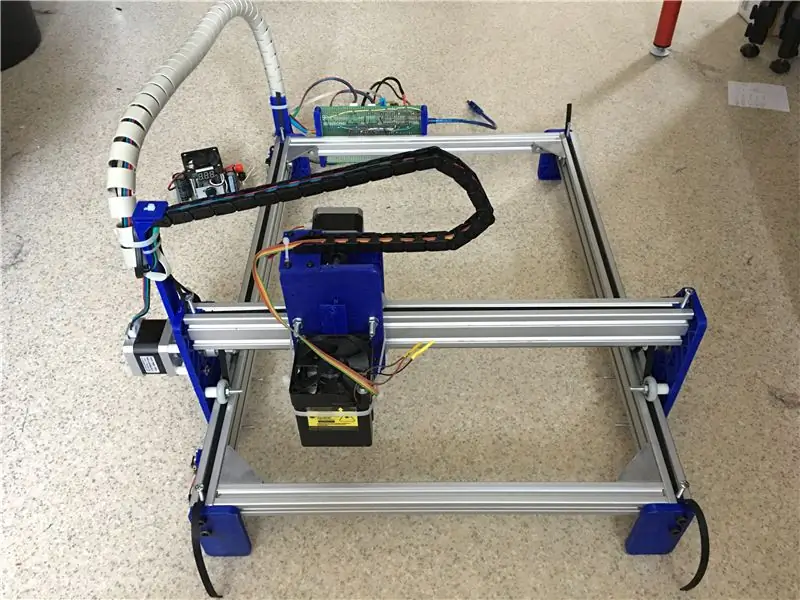
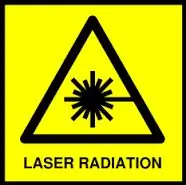
Una parola in anticipo: questo progetto fa uso di un laser con una grande quantità di potenza irradiata. Questo può essere molto dannoso per diversi materiali, la tua pelle e specialmente i tuoi occhi. Quindi fai attenzione quando usi questa macchina e cerca di bloccare ogni radiazione laser diretta e riflessa per evitare di colpire qualcosa al di fuori della macchina
Utilizzare occhiali di protezione adeguati alla frequenza del laser utilizzato
Tempo fa ho realizzato un mini incisore laser, basato su due unità cd. Dopodiché ne ho fatto uno più grande basato sulle cose che avevo in giro nel mio laboratorio (vedi il mio istruibile "Incisatore laser veloce, sporco ed economico"). Il piccolo funziona bene ma è piccolo. Quello più grande è più grande ma a causa del gioco nelle parti non è così preciso.
Ma ora che possiedo una stampante 3D ho deciso di crearne una da zero con parti che comprerò e parti che disegnerò e stamperò da solo. Così ho fatto.
Ho pagato circa 190 euro per le parti senza il laser che già possedevo.
Sì è vero, questo è di nuovo un istruibile per un incisore laser. Ma penso che tutte le istruzioni che puoi leggere su un argomento, aggiungere molte informazioni e un altro angolo di prospettiva che possa aiutarti a decidere cosa fare.
E ancora è vero, puoi acquistare un incisore laser completo per quella somma di denaro (probabilmente uno più piccolo) ma il divertimento di costruirlo da solo, per me, non ha prezzo così come sapere esattamente come tutto è messo insieme. E oltre a questo mi sono divertita molto a capire quale dovrebbe essere la dimensione per i disegni (lo ammetto: per ispirazione ho guardato un po' su internet gli incisori che puoi comprare come kit) delle cose da stampare per realizzarlo opera. Ti fa capire meglio tutta la faccenda.
In questo tutorial ti mostrerò cosa ho acquistato, cosa ho stampato e come è stato assemblato per realizzare un incisore laser di 38x29 cm (dimensioni di incisione/taglio).
Ho stampato tutte le parti stampabili con la mia stampante Davinci pro 3-in-1: le parti blu con PLA e le cose bianche (i bus a distanza) con ABS.
Impostazioni stampante PLA:
- 210 gradi C
- nessun letto riscaldato
- strati di 0,25 mm
- spessore del guscio (superficie normale, superiore e inferiore) 4 strati
- 80% di riempimento (tranne le "piastre portacinture" stampa quelle con il 100% di riempimento)
- tutte le velocità a 30 mm/s (eccetto la non stampa e la velocità di ritrazione a 60 mm/s e lo strato inferiore a 20 mm/s)
- falda 5 mm
- nessun supporto
- rapporto di estrusione 100%
Impostazioni stampante ABS:
impostazioni ABS normali con riempimento al 100%
Tieni presente che l'inglese non è la mia lingua madre e mi scuso in anticipo per eventuali errori grammaticali e di ortografia.
Passaggio 1: Distinta base

Questa è la lista delle cose che ho acquistato:
- 1x profilo in alluminio 2020 estrusi, lunghezza 1 m
- 2x profili in alluminio 2040 estrusi, lunghezza 1 m
- 1x axel 8 mm di diametro, lunghezza circa 44 cm
- 4x giunti angolari in alluminio con relativi dadi e bulloni
- 1x lotto di dadi scorrevoli (dove lo compro il lotto è di 20 pezzi. Non li usi tutti)
- 12x ruote in nylon 23 mm (dimensione interna 5 mm) appositamente per i profili utilizzati
- 1 cuscinetto a sfere, 22 mm esterno, 8 mm interno
- 2x puleggia GT2, foro 8mm, per cinghia larga 6 mm (20 denti)
- 1x puleggia GT2, foro 5 mm, per cinghia larga 6 mm (20 denti)
- 1x accoppiatore per asse flessibile 5 mm - 8 mm
- 2 metri di cinghia dentata GT2 6mm
- 2x motori passo-passo NEMA17 (1,8 gradi/passo, 4,0 kg/cm) 42BYGHW609L20P1X2, o simili
- 2x cavi per motore passo-passo, 1 m (se usi le guide per cavi hai bisogno di cavi più lunghi)
- 4x finecorsa, distanza tra i fori 10 mm (la piastra di montaggio stampata è per quella distanza)
- 1x Aduino Nano
- 2x StepStick DRV8825 stepper driver con dissipatore di calore
- 12 bulloni m6 x 30 mm
- Bulloni, dadi e rondelle 8x m5 x 30 mm
- 4x m5 x 55 mm bulloni, dadi e rondelle
- 4x m3 x n mm (dove n è il valore che dipende dalla profondità dei fori m3 nei motori e dallo spessore della lamiera di 7 mm + la lunghezza dei bus a lunga percorrenza)
- 4x m3 x n mm (dove n è il valore che dipende dalla profondità dei fori m3 nei motori e dallo spessore della lamiera di 7 mm)
- alcuni bulloni m4 per i reggicintura e la piastra di montaggio del finecorsa
necessario anche:
- 1x condensatore 100uF
- 1x resistenza 220 Ohm
- 1x led
- 1x pulsante (interruttore di rilascio del motore)
- 1x tagliere adatto
- 1x alimentatore da 12 V o un adattatore, che fornisce abbastanza Ampere.
- 1x laser con capacità TTL, preferibilmente uguale o superiore a 500 mW. Wattaggi più alti riducono abbastanza bene il tempo di incisione! Uso un laser da 2 W e va bene.
E quando hai finito il breadboard:
- 1x scheda di prototipazione / PCB in fibra di vetro (34x52 fori / 9x15 cm) (o creare un PCB inciso)
- 1x presa jack 2,1 x 5,5 mm ingresso (la parte che sarà saldata sul PCB e la spina dell'adattatore va in)
Cose da stampare:
- LE3 piedi
- Ruote di supporto interasse LE3 Test Calibre LE3
- LE3 Cuscinetto a sfere calibro 21,5 22 22,5 mm
- LE3 Autobus a distanza
- Motore LE3 e lato opposto
- LE3 laser_supporto motore
- Portacinture LE3 telaio 20x40
- LE3 Finecorsa piastra montaggio telaio 20x40
- Fermacavo LE3 cornice 20x40
- *********************aggiunto l'11 maggio 2021************************* ******
- **** Motore LE3 e lato opposto con interasse regolabile****
- ****
- **** Dopo aver regolato la distanza è possibile fissare in posizione il supporto del bullone exentric con
- **** due viti parker. Ci sono due fori per lato per farlo.
- ****
- **** questi possono sostituire "motore LE3 e lato opposto" che non ha interasse regolabile!
- ****
- ***************************************************************************
e, se necessario:
Supporti per cavi LE3 e montaggio su PCB
Passaggio 2: file di stampa STL
Passaggio 3: parti stampate in 3D
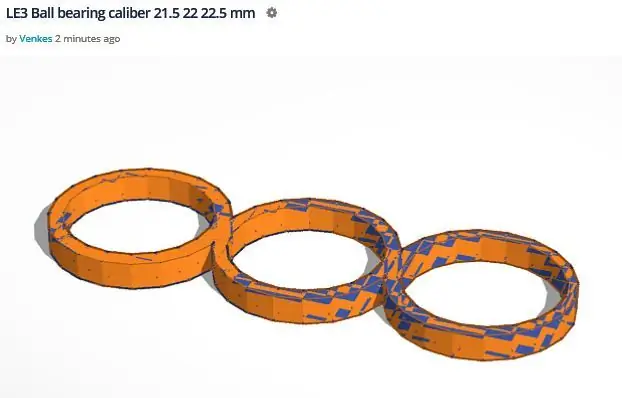
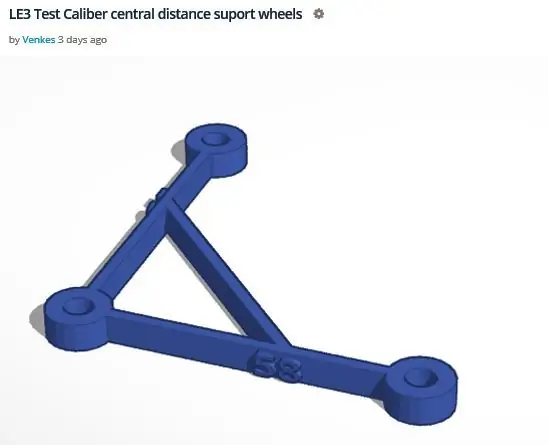
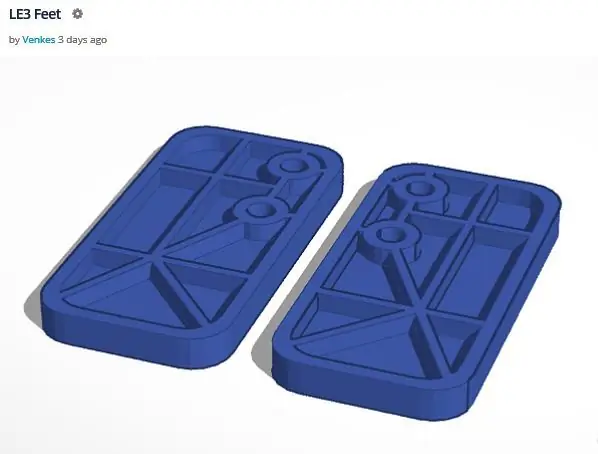
Queste sono tutte le parti stampate
Passaggio 4: strumenti necessari
La maggior parte dell'hardware di cui hai bisogno probabilmente hai in giro nella tua officina, come ad esempio:
- Plyers
- Cacciaviti
- Saldatore
- Tieraps
- Un set tocca e muori
- un calibro
Non molto di più in realtà. Ma la cosa più importante è possedere o avere accesso a una stampante 3D.
Passaggio 5: preparativi
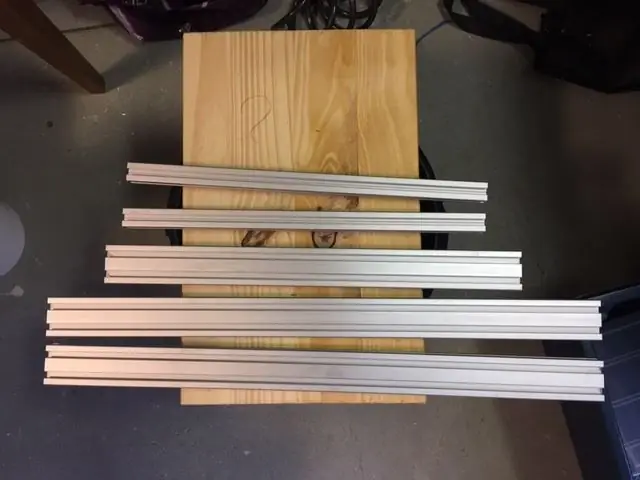
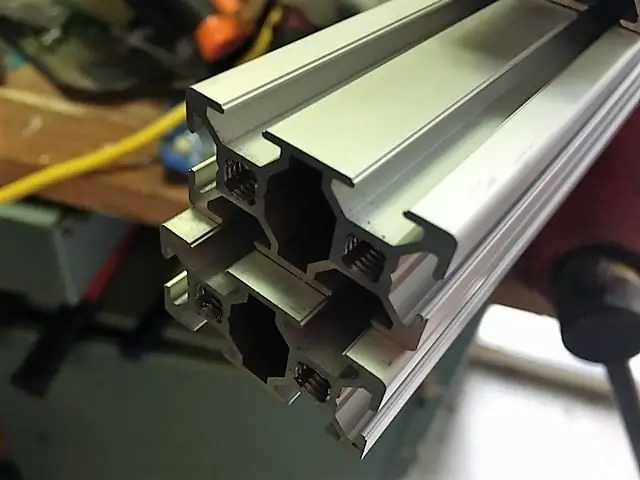
Tagliare i profili nelle seguenti lunghezze:
- il profilo 2020: 2 pezzi da 37 cm ciascuno
- il profilo 2040: 2 pezzi da 55 cm ciascuno e un pezzo da 42 cm.
Puoi segare i profili con un seghetto, ma se hai accesso a un seghetto industriale (come ho fatto io) devi usare quello. I risultati sono molto migliori.
Ora hai 5 pezzi di cornice. Vedi foto. 1
La prossima cosa da fare è toccare il filo M6 in tutti i profili 2040. Vedi foto. 2
Queste sono in realtà le uniche preparazioni che devi fare.
Passaggio 6: il telaio principale
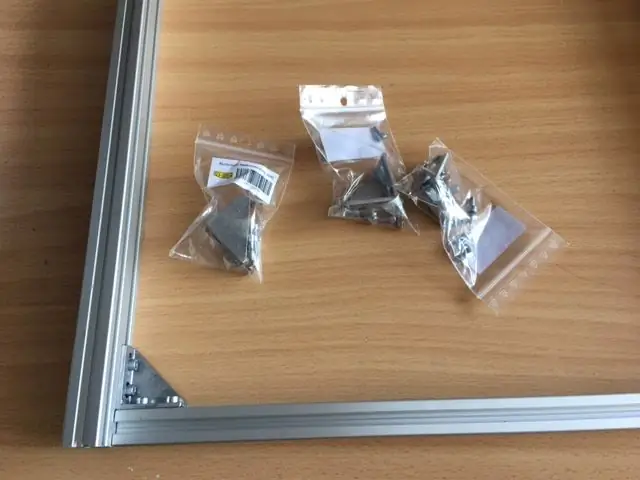
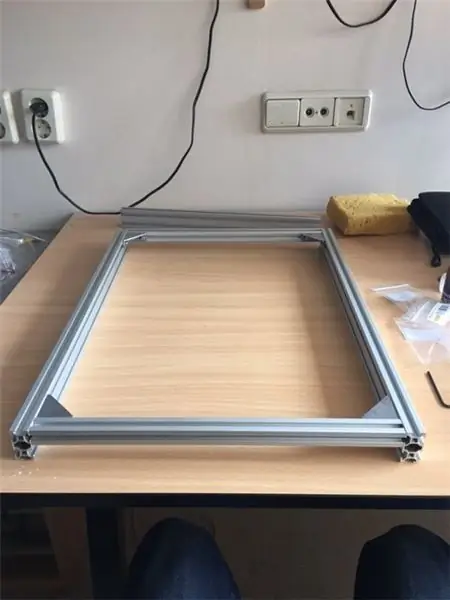
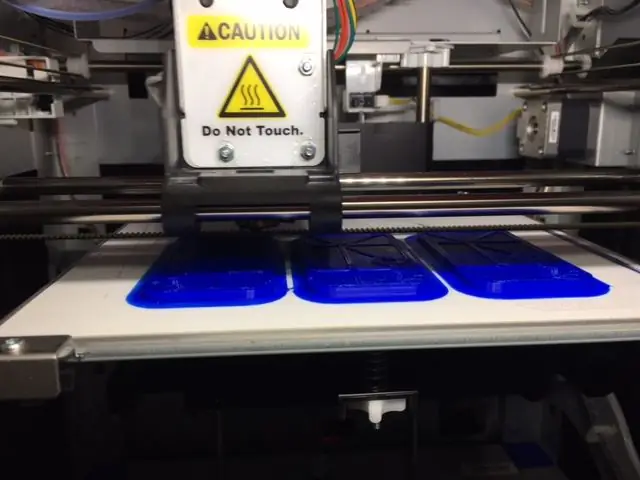
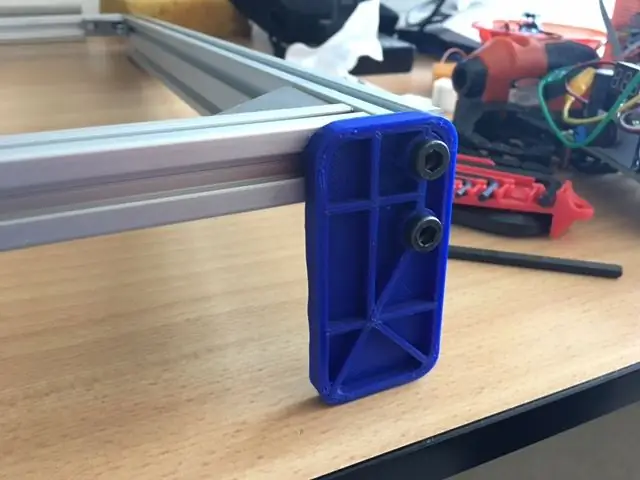
Mettere insieme il telaio principale è facile e diretto (fig. 1 e 2). Quando hai finito ti fai una buona idea delle dimensioni.
Quindi stampare i piedi, "LE3 Feet" (fig. 3), praticare i fori da 6 mm e fissarli con bulloni da 8 m6 al telaio.
Come puoi vedere non ho stampato le parti completamente massicce ma vuote su un lato. Ciò consente di risparmiare molto filamento e tempo di stampa ed è molto resistente! Il lato liscio dentro o fuori (fig. 4) non fa differenza sulla robustezza, è una scelta estetica.
Passaggio 7: assicurati che le dimensioni di stampa siano corrette e metti insieme il carrello
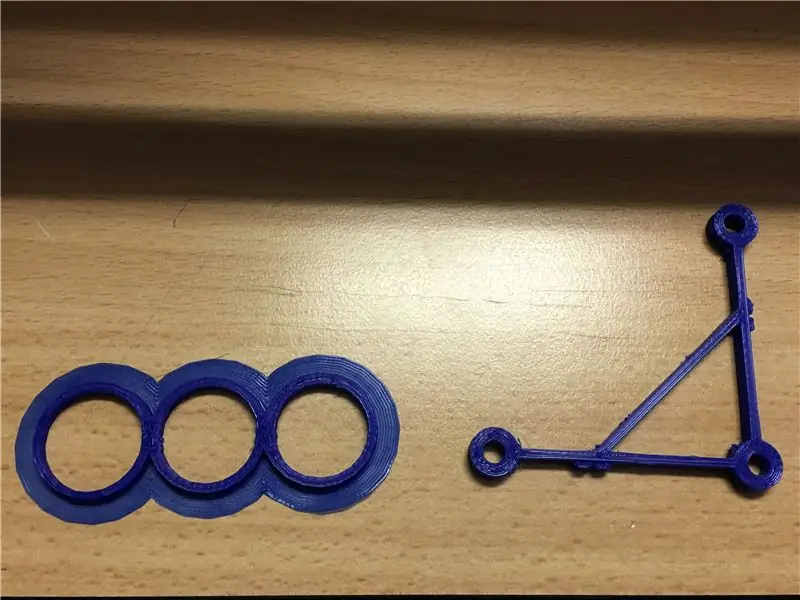
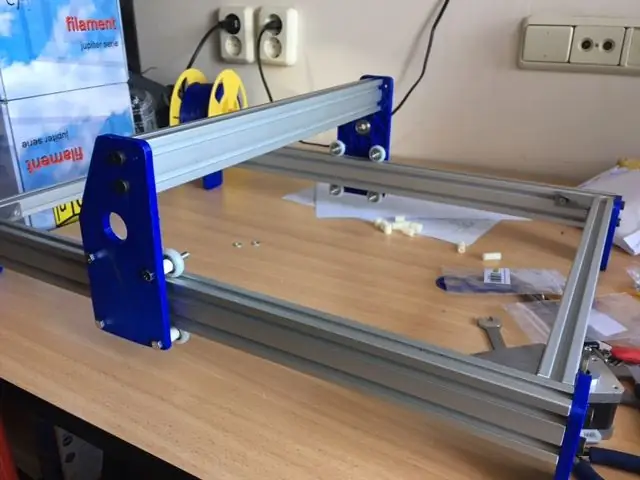
È importante capire quanto sia accurata la stampa della stampante. A tale scopo ho realizzato alcuni calibri di prova:
quindi che si fa:
- stampa i "Bus di distanza LE3" (bianco su fig. 2)
- stampa le "ruote di supporto interasse LE3 Test Calibre" e il "calibro LE3 con cuscinetti a sfera"
- praticare i fori per gli assi delle ruote (bulloni da 5 mm) con un trapano da 5 mm
- a sinistra nella foto. 1 è il calibro di prova per determinare quanto grande deve essere stampato il foro per il cuscinetto a sfere per farlo aderire perfettamente. Sono disponibili tre diverse dimensioni: 21,5, 22 e 22,5 mm. Questi sono i valori che danno nel design della stampa. Il foro in cui il cuscinetto si adatta meglio (devi esercitare un po' di forza per inserirlo) è quello che ti serve.
- A destra si vede il calibro per testare la distanza tra le ruote di guida. È importante che non ci sia gioco tra il telaio 2040 e le ruote. Puoi capirlo con questo calibro. Basta avvitare tre ruote con bulloni da 5 mm e i distanziali e provare a quale distanza (58 o 59 mm) il telaio si muove con una certa resistenza attraverso le ruote.
Nota:
nei disegni di stampa ho usato 22,5 mm per il foro del cuscinetto a sfere e 58 mm di distanza tra le ruote. Questo funziona perfettamente per me. Se questi valori non funzionano per te, devi armeggiare il design.
Dopo aver individuato le giuste dimensioni, e stampato il "Motore LE3 e lato opposto", eseguire prima i fori su entrambe le piastre.
Montare il carrello (fig. 2).
Hai bisogno del telaio 2040, lungo 42 cm e del motore e delle piastre dei cuscinetti, 4 bulloni da m6, bulloni e dadi da 8 m5.
- eseguire i fori: 3mm per i fori motore, 5mm per i fori perno ruota, 6mm per i fori per il fissaggio della piastra al profilo
- avvitare le due ruote superiori su una delle piastre (usare rondelle da 5 mm tra i bus e le ruote, le ruote devono girare liberamente!)
- quando si appoggiano queste ruote sul telaio, montare anche le due ruote inferiori
- fare lo stesso con l'altro lato (nella foto 2 la piastra del motore è davanti e la piastra del cuscinetto nella parte posteriore)
- bullone con 4 bulloni m6 il telaio 2040 tra le piastre
Ora puoi spostare il carrello. Va bene se senti una certa resistenza, ti dice che non c'è gioco. I motori sono abbastanza forti per gestirlo.
Questo assemblaggio è in effetti un modo generale di come mettere insieme il resto di questa macchina. D'ora in poi mi dilungherò quindi meno e indicherò solo cose importanti. Anche le immagini dicono molto.
Passaggio 8: asse e motore
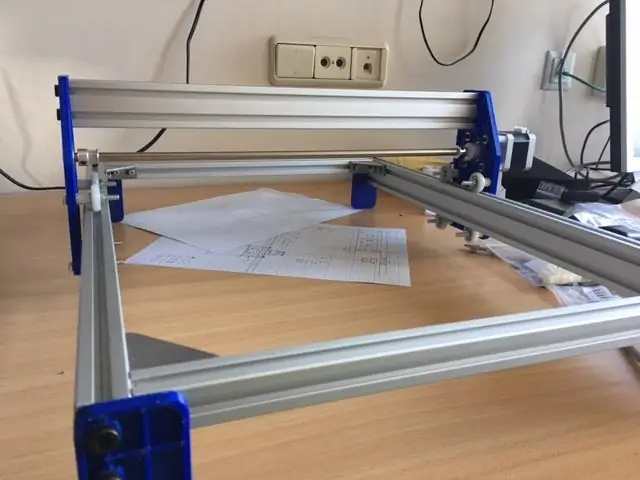
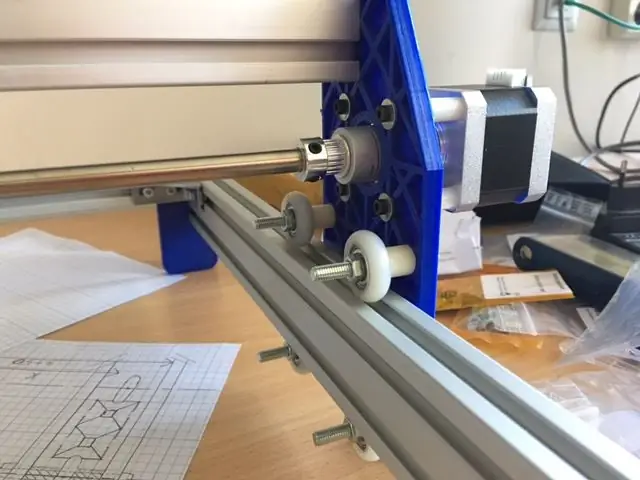
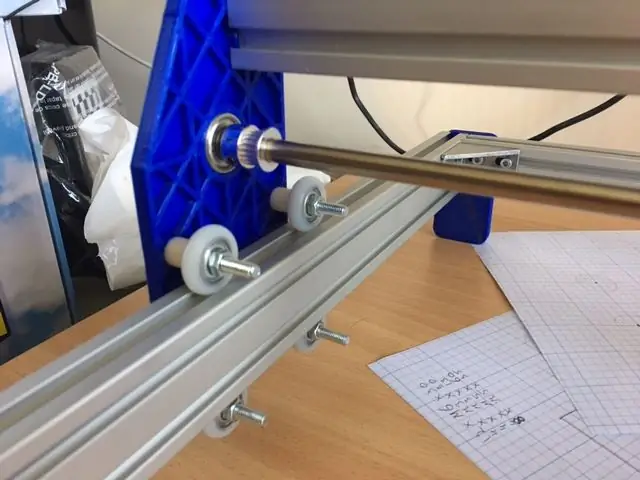
- Usa i 4 bus a lunga percorrenza per avvitare il motore sulla piastra (devi capire la giusta lunghezza per i bulloni, dipende da quanto sono profondi i fori nel motore)
- mettere il cuscinetto in posizione
- spingere l'asse da 8 mm attraverso il cuscinetto e contemporaneamente mettere le pulegge da 8 mm e l'accoppiatore dell'asse flessibile da 5 mm-8 mm sull'asse
- fissare tutto in posizione in modo che i denti della puleggia siano esattamente sopra la fessura del telaio
Passaggio 9: il supporto laser/motore e le cinture
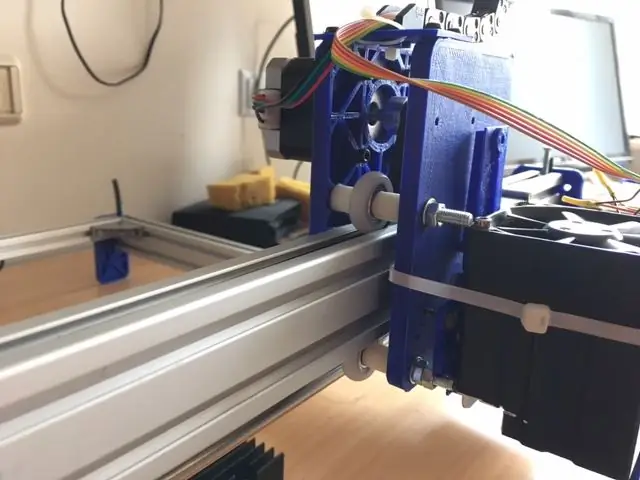
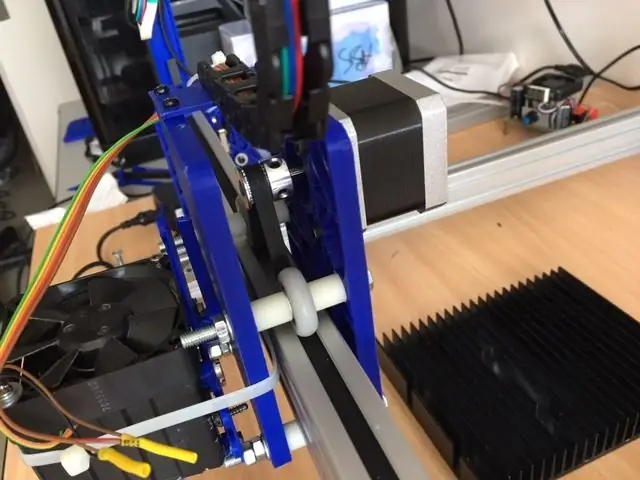
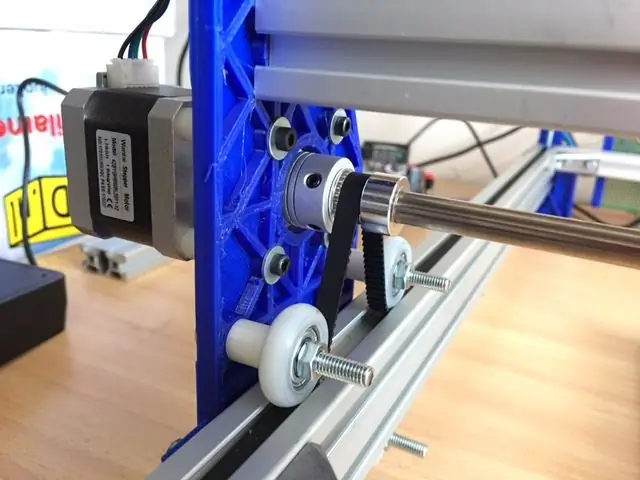
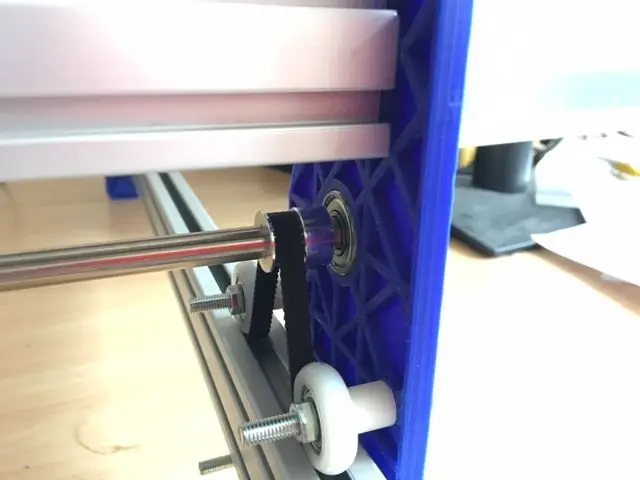
Il supporto laser/motore:
- Stampa " Supporto motore_laser LE3"
- Stampa " Portacinture LE3 telaio 20x40"
- Forare i supporti per cintura a 3,2 mm e filettare da 4 mm nei fori
- praticare i fori del supporto laser/motore ai diametri appropriati. I fori extra sul lato laser servono per montare una piastra di montaggio laser universale che non ho ancora progettato.
- assemblare il supporto laser/motore completo
- togliere provvisoriamente il profilo 2040 della carrozza
- far scorrere il profilo attraverso le ruote. Va bene se devi spingere abbastanza forte per mettere il profilo attraverso. Quando tengo il telaio perpendicolare al suolo, anche con il motore assemblato, la gravità non sposterà il supporto laser/motore.
- mettere su entrambi i lati un supporto per cintura
- rimontare il profilo con il supporto laser/motore.
Sulla foto. 1 potete vedere come è assemblato (la foto è stata scattata in una fase successiva. Mi ero dimenticato di farne una prima). Non dimenticare le rondelle tra gli autobus e le ruote! Per favore, non preoccuparti del laser, questo è solo un assemblaggio di prova.
Le cinture. Prima quello nel supporto laser:
- portare la cinghia sotto le ruote e sopra la puleggia come nella foto. 2
- portare la cintura su entrambi i lati sotto i supporti per cintura (assicurarsi di avere una lunghezza della cintura sufficiente in modo da poter afferrare un pezzo di cintura su entrambi i lati)
- da un lato spingere il più possibile di lato il reggicintura e serrare il bullone (non è necessario fissarlo molto stretto)
- ora fai lo stesso dall'altro lato e contemporaneamente tira la cinghia in modo che ci sia una tensione ragionevole tra la puleggia e le ruote
Per le due cinghie del carrello (fig. 3 e 4) fate lo stesso, ma con la differenza che dovete solo allontanare un piede (togliere il bullone superiore e allentare quello inferiore) e inserire due reggicintura su uno lato. Ora puoi far scorrere l'altro sotto il carrello dall'altra parte. Assicurarsi inoltre che, dopo aver teso le due cinghie, il carrello sia completamente ad angolo retto!
ps
se si stampano i reggicintura in una fase precedente è possibile inserirli nel telaio prima del montaggio
Passaggio 10: i finecorsa + i supporti

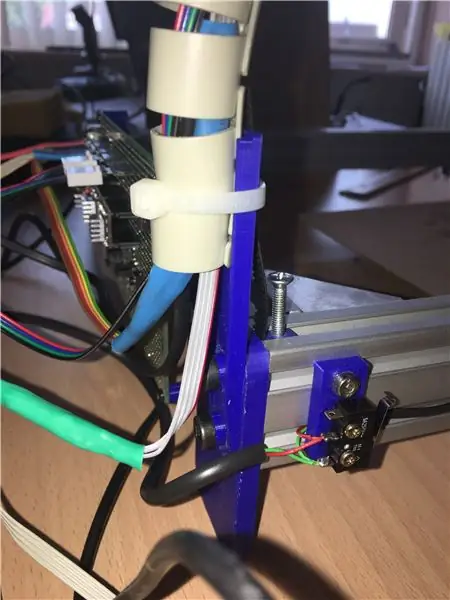
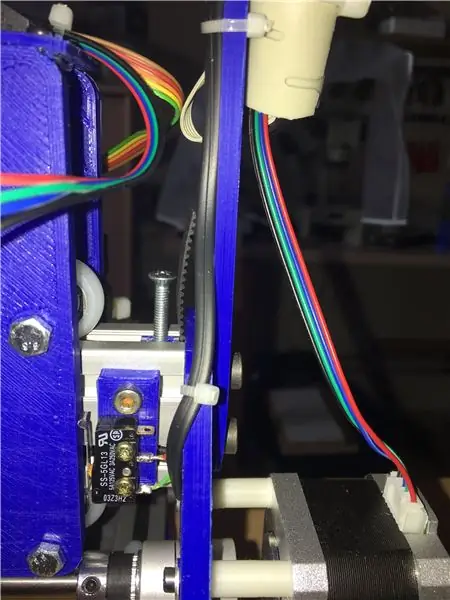
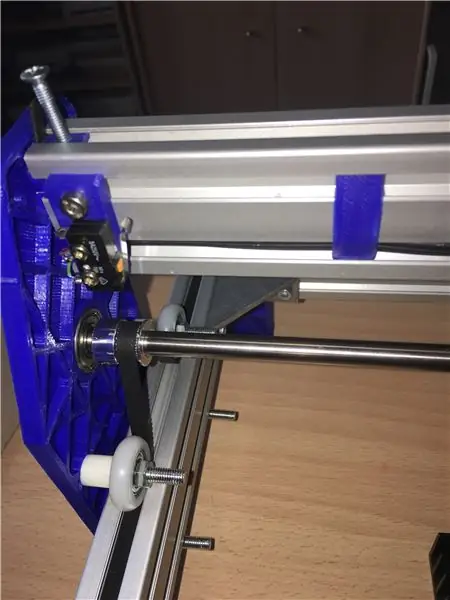
Prima stampa:
- LE3 Finecorsa piastra montaggio telaio 20x40
- Fermacavo LE3 cornice 20x40
Sulla foto. 1 e 2 si vedono i finecorsa assemblati sul telaio principale. La distanza tra loro è di ca. 45 cm (distanza di incisione 38 cm + larghezza piatto 7 cm)
Sulla foto. 3 e 4 i finecorsa sulla traversa, distanza: 36 cm (29 + 7). Dopo il montaggio verificare che gli interruttori siano posizionati correttamente (nessuna collisione meccanica).
Tutto il lavoro meccanico è praticamente fatto ora.
È già possibile cablare gli interruttori e utilizzare i fermacavi per fissare i cavi nelle fessure laterali del telaio.
Passaggio 11: l'elettronica

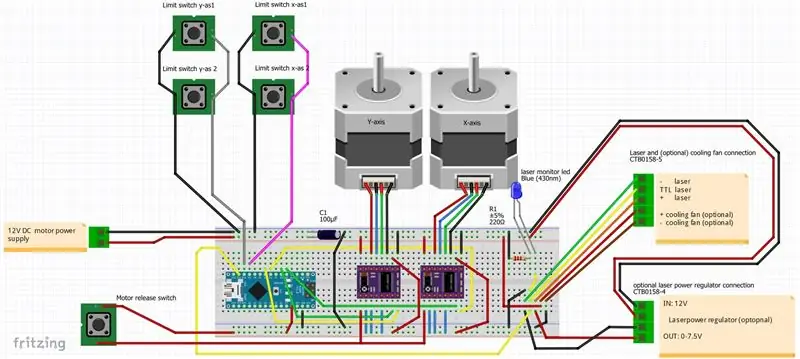
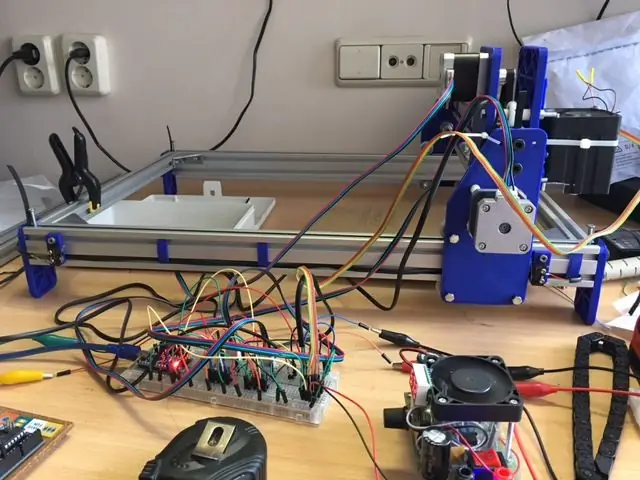
- foto. 1 mostra schematicamente le connessioni tra le parti
- foto. 2 come dovrebbero essere le connessioni della breadboard.
- foto. 3 e 6 la breadboard dal vivo
- foto. 4 il lato filo della scheda di prototipazione che ho realizzato
- foto. 5 il lato della parte. Notare tutte le connessioni dell'intestazione femmina per Arduino, le schede driver e tutte le connessioni dei cavi. Queste connessioni rendono più semplice la commutazione delle schede (quando necessario).
Ho progettato staffe di montaggio per la scheda di prototipazione 9x15 cm in modo da poter imbullonare la scheda al profilo 2020. Queste staffe fanno parte del file di stampa "Montaggi su cavo LE3 e montaggio su PCB" (fig.7 e 8).
Ci sono 3 connessioni su ogni scheda driver per controllare la risoluzione del passo: M0, M1 e M2. Con queste connessioni è possibile determinare la risoluzione del passo a seconda di come collegarle a +5V. Per questo ho realizzato sulla scheda di prototipazione delle linee jumper per ognuna delle 3 linee sui due subacquei. Sono nei cerchi gialli sulla foto. 5.
Con questi jumper puoi impostare facilmente la risoluzione del passo:
M0 M1 M2 Risoluzione
- basso basso basso Pieno
- alto basso basso Metà
- basso alto basso 1/4
- alto alto basso 1/8 (questa è l'impostazione che uso e sono disegnate nelle foto)
- basso basso alto 1/16
- alto alto alto 1/32
Dove alto significa: collegato a +5V (linea jumper chiusa).
Non troverai questi ponticelli sulla breadboard o sullo schema, ma hai l'idea e puoi implementarli tu stesso se necessario.
È possibile omettere questi ponticelli e impostare la risoluzione del passo in modo permanente sulla risoluzione del passo desiderata. Fino ad ora non ho modificato le impostazioni dei jumper: la risoluzione 1/8 funziona bene!
Inoltre non trovi l'interruttore sulla foto. 5 (angolo in alto a destra). Questo interruttore che ho implementato alterna tra D12 e D11 sulla scheda Arduino per guidare il laser, risp. M03 e M04 (codice G). Ma scopro che con i programmi giusti non devi più usare M03 quindi l'ho lasciato fuori dai piani. La linea TTL è invece collegata direttamente a D11 (M04).
ps.
si prega di notare che, sullo schema, i due connettori (5 fili e 4 fili) erano necessari per me perché avevo costruito il mio sistema laser da solo con una ventola di raffreddamento separata. Ma se hai un modulo laser e non vuoi regolare la potenza del laser. Hai solo bisogno delle 3 linee superiori del connettore a 5 linee e l'alimentazione dovrebbe provenire dall'alimentatore fornito con il tuo laser.
Passaggio 12: software


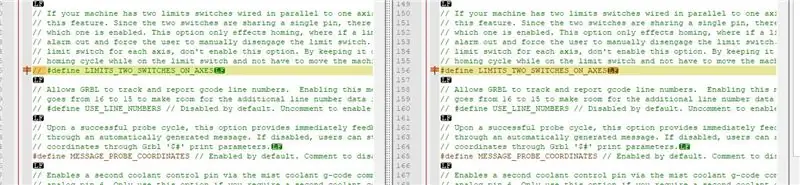
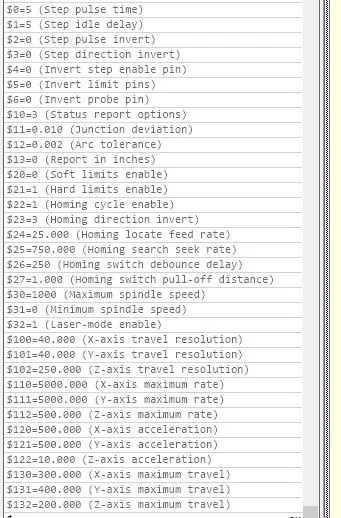
Programmi utilizzati ai fini di questo istruibile:
- GRBL, versione 1.1 (libreria arduino)
- LaserGRBL.exe, programma per inviare immagini affettate o grafica vettoriale al tuo incisore/taglierino
- Inkscape, programma di disegno vettoriale
- JTP Laser Tool V1.8, plugin necessario per Inkscape per creare un file Gcode per LaserGRBL
- Blocco note++
In Internet si possono trovare molte informazioni su come installare, scaricare e utilizzare questi programmi.
La prima cosa che devi fare è modificare il file config.h della libreria GRBL:
- dopo aver scaricato GRBL v1.1 apri config.h con Notepad++ (puoi trovare config.h nella directory GRBL)
- trova le linee che vedi nella foto. 1, 2 e 3 e modificarli in base alla parte destra dell'immagine (a sinistra sulle foto si vedono le linee originali ea destra quelle alterate)
- salva il file
Ora carica la libreria GRBL nel tuo controller Arduino nano:
- collega il tuo Arduino al tuo pc
- avvia il tuo programma Arduino
- scegli Schizzo
- scegli Importa libreria
- scegli aggiungi libreria
- vai alla tua directory in cui si trova GRBL e fai clic (non apri) sulla directory GRBL (la directory in cui hai modificato il file config.h)
- clicca su apri
- Ignora il messaggio bla bla bla non catalogato e chiudi il programma Arduino
- Vai alla directory …GRBL/examples/grblUpload e avvia grblUpload.ino
- ora parte il programma Arduino e inizia la compilazione. Al termine, ignora il messaggio di spazio di memoria insufficiente e chiudi il programma Arduino.
In questa fase la scheda Arduino viene caricata con GRBL e le impostazioni per Homing e i finecorsa sono corrette.
Ora devi far sapere a GRBL sulla scheda Arduino quali velocità, dimensioni ecc. sono necessarie per far funzionare il tuo incisore.
- collega il tuo Arduino al tuo pc
- Avvia laserGRBL.exe
- fare clic sul pulsante di connessione (a destra accanto al campo della velocità di trasmissione)
- digita $$ nel campo del comando di invio (sotto il campo di avanzamento) e premi [Invio]
- Modificare i valori secondo l'elenco in fig. 4. Basta digitare le righe che devono essere modificate nel campo del comando di invio (sotto il campo di avanzamento). Ad esempio: digita $100=40 [Invio]
- Ripeti questo per cambiare tutta la linea.
- dopodiché puoi digitare di nuovo $$ per vedere o tutte le possibilità sono corrette
Mentre esegui il test, vedi sotto, devi anche regolare la quantità di Ampere che va ai motori. Puoi girare il piccolo trimmer su entrambe le schede stepstick per farlo, ma scollega la scheda dall'alimentazione prima di farlo. Scarica e leggi la scheda tecnica dello stepstick! Regolare i trimmer passo dopo passo fino a quando i motori non funzionano senza intoppi e non perdono mai un passo. I trimmer sulle mie tavole sono girati a destra di circa 3/4.
Ora puoi testare l'incisore per vedere se tutti i movimenti funzionano bene e, cosa molto importante!, se i finecorsa funzionano. Se viene attivato un finecorsa, la macchina va in stato di errore. In laserGRBL puoi leggere come risolvere quel software, $x o qualcosa del genere, e ora l'interruttore di sblocco del motore torna utile: nello stato di errore probabilmente uno degli interruttori è ancora attivato, ora premi l'interruttore di sblocco del motore e allontanare leggermente il carrello desiderato dall'interruttore per rilasciarlo. Ora puoi "reset" e "homing" la macchina.
Fondamentalmente ora sei pronto per la tua prima corsa di calibrazione.
Passaggio 13: calibrazione
La seguente procedura è un estratto di una parte del mio "incisore laser rapido, sporco ed economico" che può essere utile se si riscontrano deviazioni nelle misurazioni della produzione di incisione
Per la calibrazione di $100 (x, step/mm) e $101 (y, step/mm) ho fatto quanto segue:
- Ho inserito il valore 80 circa sia per $ 100 che per $ 101
- quindi disegno un quadrato di una determinata dimensione, diciamo 25mm in Inkscape e inizio a incidere **
- Il primo risultato non deve essere un quadrato della giusta dimensione, 25x25mm.
- Inizia con l'asse x:
- diciamo che A è il valore che vuoi per $ 100 e B è il valore di $ 100 (80) e C è il valore in Inkscape (25), e D è il valore che misuri sul quadrato inciso (40 o giù di lì)
- allora A = Bx(C/D)
In questo esempio il nuovo valore per $100 (A) è 80x(25/40)=80x0, 625=50
Lo stesso puoi fare con l'asse y ($ 101).
Il risultato è abbastanza preciso. Se usi esattamente gli stessi motori, cinghie e pulegge per gli assi x e y, i valori di $ 100 e $ 101 saranno gli stessi."
** Se crei un quadrato di calibrazione in Inkscape, usa il plugin JTP Laser Tool V1.8 per creare un file Gcode (vettoriale) che puoi caricare in laserGRBL. Assicurati di compilare M04 per accendere e M05 per spegnere il laser nel plugin JTP Laser Tool V1.8!
Passaggio 14: pronto
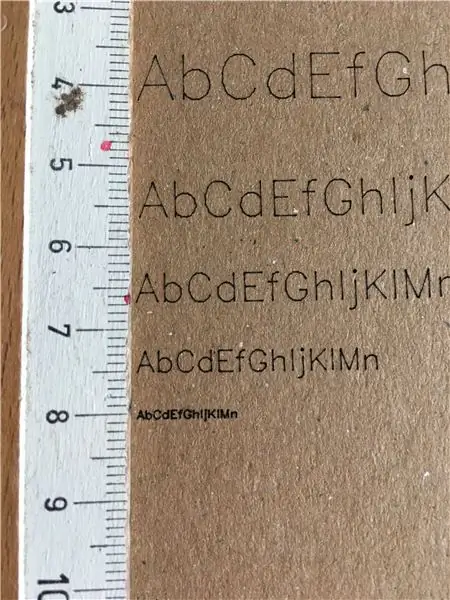

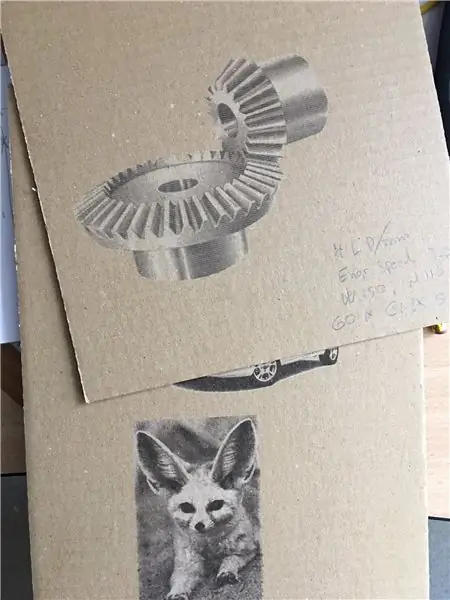
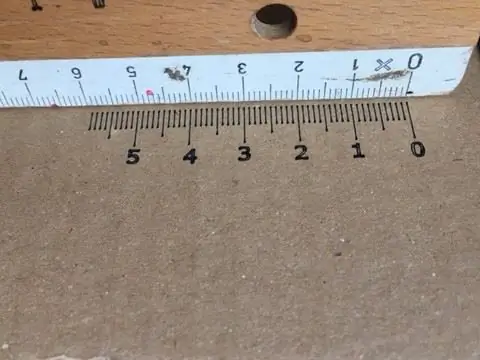
Se tutto stava andando bene, ora hai inciso un quadrato con una dimensione di esattamente 25 mm.
Ora puoi incidere/tagliare qualsiasi cosa ti piaccia: immagini in scala di grigi, disegni vettoriali, modelli da tagliare ecc. E questo con grande precisione!
fig.1, i caratteri in basso sono molto piccoli (la distanza tra due linee sul righello è di 1 mm)
fig.2, alcuni primi risultati in scala di grigi.
foto. 3, abbastanza preciso!
Il video mostra l'incisore al lavoro.
Passaggio 15: ultimo passaggio
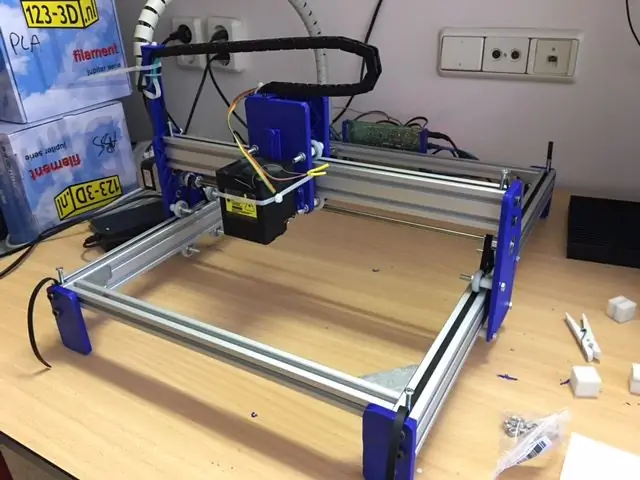
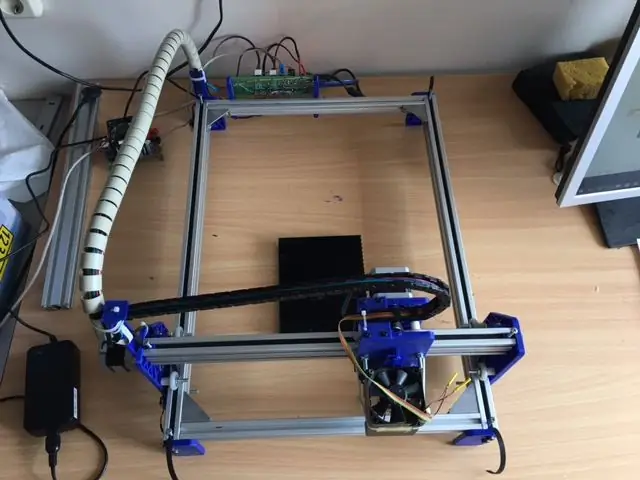
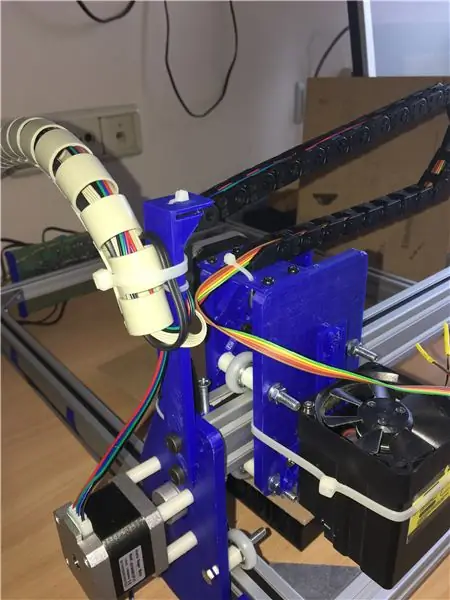
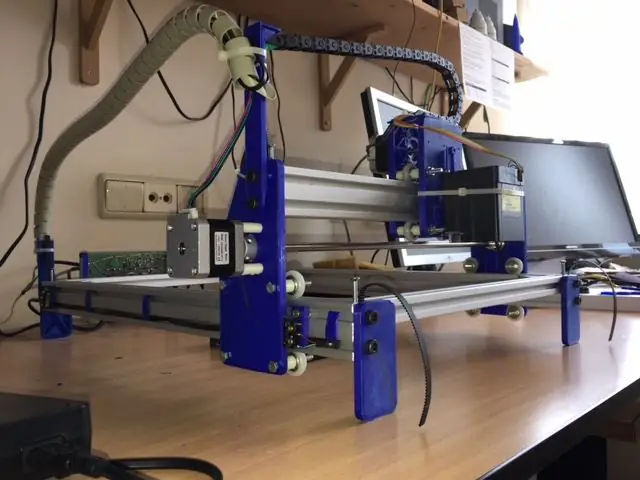
Ora tutto funziona bene, puoi iniziare con la messa a punto dell'aggeggio con le guide dei cavi e un bel PCB. Ho creato alcuni supporti per guida cavi che puoi stampare e utilizzare per collegare le guide per cavi (file di stampa "Supporti per cavi LE3 e montaggio su PCB").
Se utilizzi le guide per cavi, i cavi del motore lunghi 1 metro non sono abbastanza lunghi e devi acquistare cavi più lunghi o fare prolunghe per cavi (è quello che ho fatto). Nelle foto vedete come ho utilizzato i passacavi (e i supporti). E ad essere onesti, la guida del cavo lo rende molto più facile da incidere perché non devi aver paura di cavi bruciati o cavi bloccati tra le parti ecc.
Spero che questo tutorial sia di ispirazione per te e sia anche una fonte di informazioni per realizzare un incisore laser. Mi sono divertito molto a progettarlo e costruirlo e so che dovresti farlo quando lo costruisci.
Costruzione felice!
Consigliato:
Come realizzare un PCB personalizzato utilizzando un incisore laser a bassa potenza: 8 passaggi (con immagini)
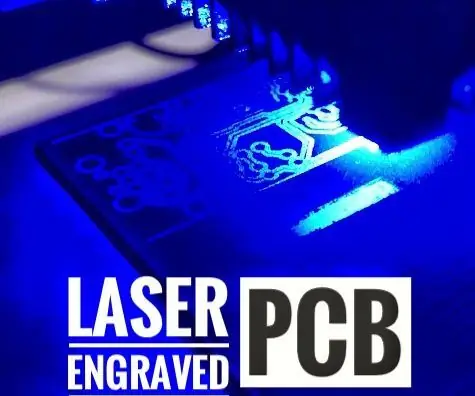
Come realizzare un PCB personalizzato utilizzando un incisore laser a bassa potenza: Quando si tratta di realizzare un PCB fatto in casa, è possibile trovare diversi metodi online: dal più rudimentale, utilizzando solo una penna, al più sofisticato utilizzando stampanti 3D e altre attrezzature. E questo tutorial cade su quest'ultimo caso! In questo progetto ho sh
Mini incisore laser CNC fai da te.: 19 passaggi (con immagini)
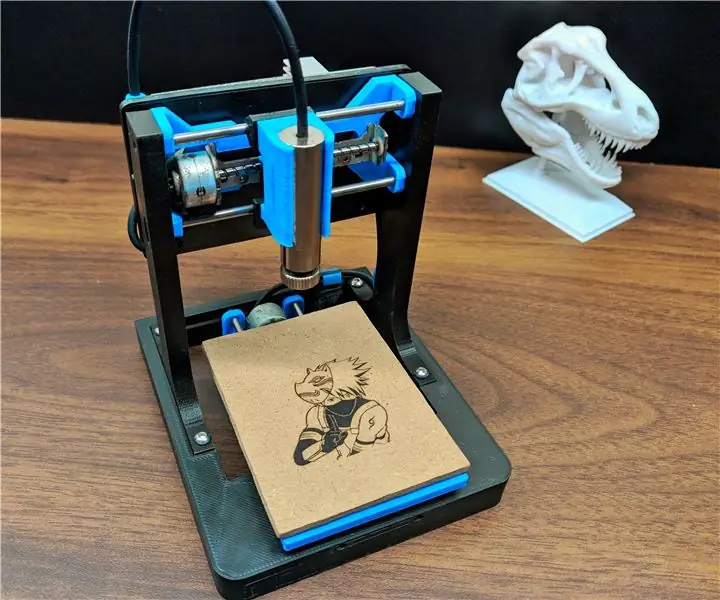
Mini incisore laser CNC fai-da-te.: Questo è un Instructables su come ho remixato il mio vecchio incisore laser CNC e realizzato una versione stabile di un incisore CNC laser basato su Arduino e una taglierina sottile utilizzando vecchie unità DVD e utilizzando un laser da 250 mW. Vecchia versione del mio CNC: https://www.instructables
Incisore laser economico e robusto fai-da-te: 15 passaggi (con immagini)
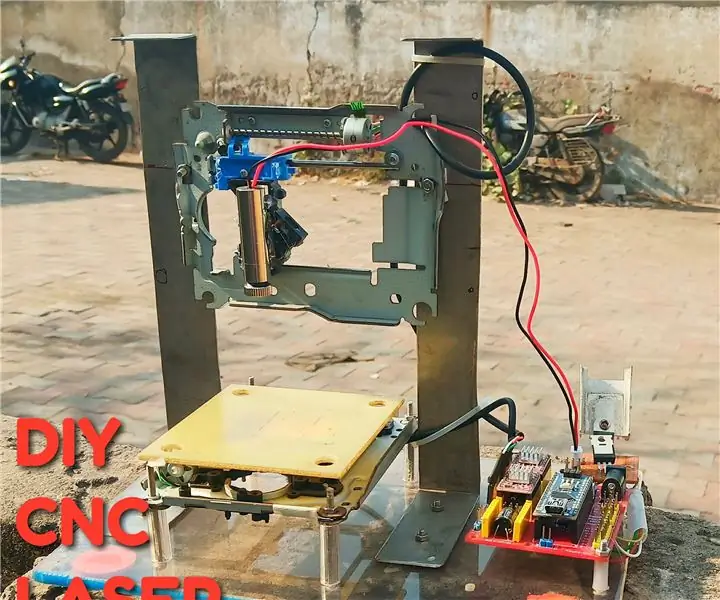
Incisore laser fai-da-te economico e robusto: in questo tutorial ti mostrerò come ho realizzato il mio incisore laser fai-da-te a un prezzo molto conveniente. Inoltre, la maggior parte delle parti sono recuperate da cose vecchie o sono molto economiche. Questo è un progetto molto interessante per qualsiasi appassionato di elettronica. Questo incisore c
Mini incisore laser per legno CNC e tagliacarte laser.: 18 passaggi (con immagini)
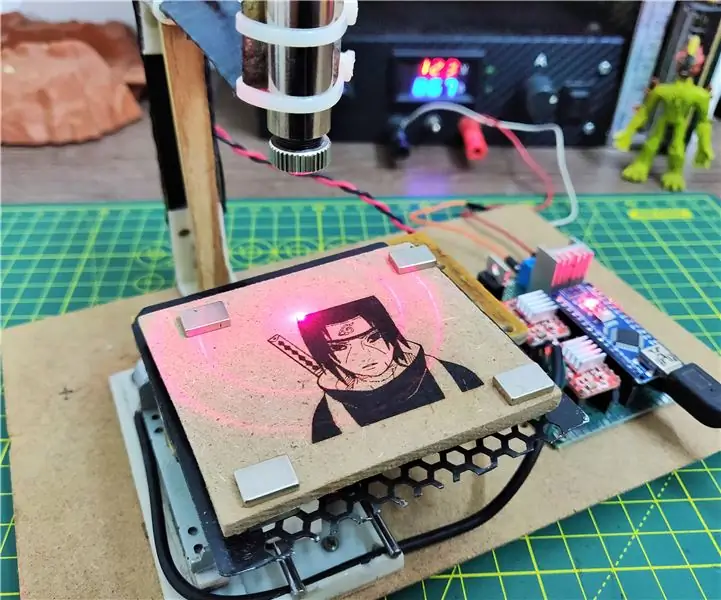
Mini incisore laser per legno CNC e taglierina laser per carta.: Questo è un Instructables su come ho realizzato un incisore per legno CNC laser basato su Arduino e una taglierina per carta sottile utilizzando vecchie unità DVD, laser da 250 mW. L'area di gioco è di 40 mm x 40 mm max. Non è divertente creare una macchina con le cose vecchie?
Cover per cellulare in sughero con incisione laser: 6 passaggi (con immagini)
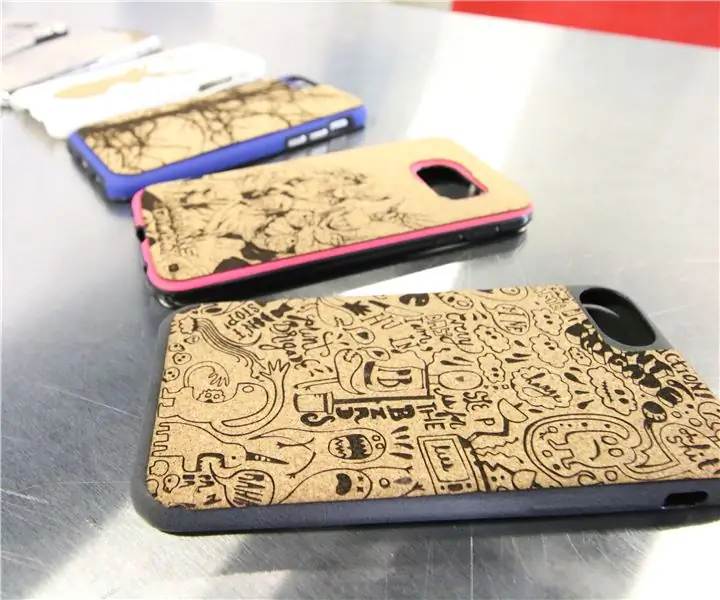
Cover per cellulari in sughero con incisione laser: questa settimana incideremo al laser il sughero utilizzando la nostra macchina per incisione laser Speedy 400. Oggi realizziamo custodie per telefoni con incisione laser utilizzando il nostro materiale di sughero. Ti mostreremo diverse tecniche per creare cover per telefono uniche utilizzando la nostra bacheca di sughero. W