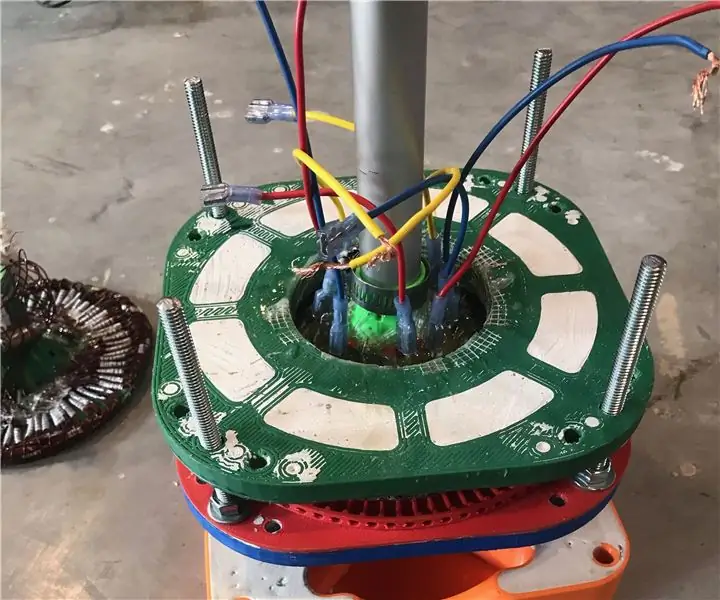
Sommario:
2025 Autore: John Day | [email protected]. Ultima modifica: 2025-01-23 14:49
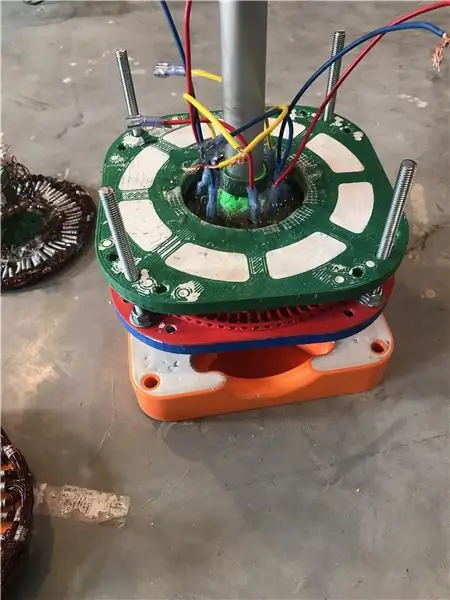
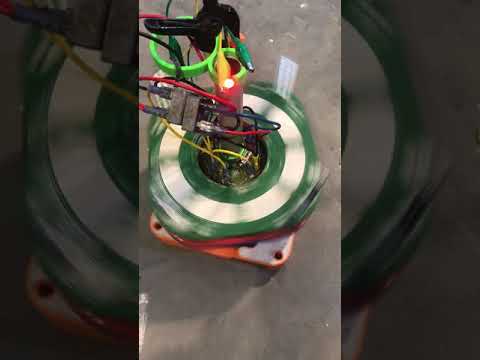
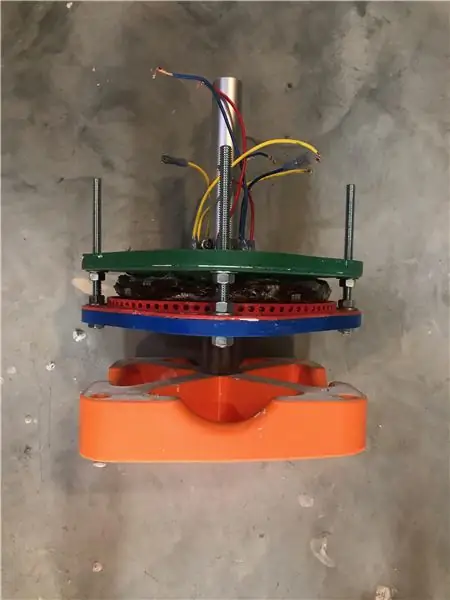
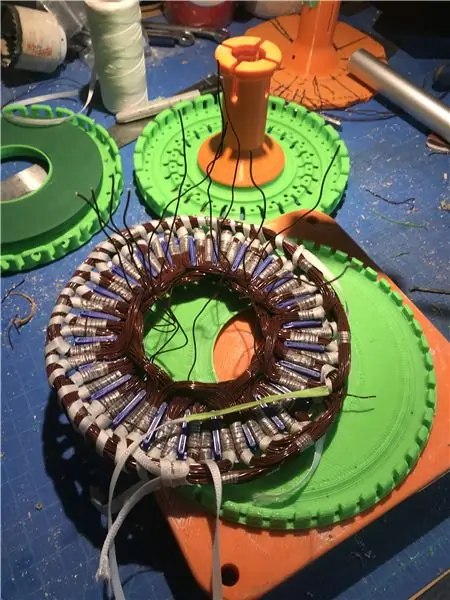
FERMARE!! LEGGI PRIMA QUESTO!!! Questa è la registrazione di un progetto ancora in fase di sviluppo, non esitare a offrire supporto.
Il mio obiettivo finale è che questo tipo di motore/alternatore possa diventare un progetto parametrizzato open source. Un utente dovrebbe essere in grado di inserire alcuni parametri, come coppia, velocità, corrente, volt/rpm, dimensioni dei magneti comuni e forse spazio disponibile, e dovrebbe essere generata una serie di file di taglio.stl e.dxf stampabili in 3D.
Quello che ho fatto è creare una piattaforma in grado di convalidare un progetto simulato, che può quindi essere evoluto in un dispositivo più ottimale dalla comunità.
In parte, questo è uno dei motivi per cui l'ho impostato con un dinamometro. Un dinamometro misura la coppia e la velocità per consentire la misurazione dei CV o Watt dell'albero. In questo caso ho costruito l'alternatore con un albero fisso passante, il che rende più semplice l'installazione di un sistema dinamometrico, e quindi può essere configurato per essere guidato come un motore da un RC ESC (spero), e la coppia misurata sull'uscita, così come la velocità, V e Ampere, consentendo di determinare l'efficienza del motore.
Per i miei scopi può essere azionato da un motore a velocità variabile (surplus dal trapano a batteria, con ingranaggio step-down) e misurata l'ingresso di coppia dell'albero, nonché V e Ampere in uscita, consentendo di generare l'efficienza reale e i carichi previsti della turbina da simulare.
In questa modalità spero di utilizzare un RC ESC in grado di frenare rigenerativo, e forse un Arduino per controllare il carico che il mio VAWT trasporta per ottenere MPPT (Multi Power Point Tracking).
L'MPPT è utilizzato nel controllo del solare e delle turbine eoliche, ma è un po' diverso per il vento. Con l'energia eolica un grosso problema è che quando la velocità del vento raddoppia da 10 km/h a 20 km/h, l'energia disponibile dal vento aumenta del cubo, quindi di 8 volte. Se 10 W erano disponibili a 10 km/h, allora 80 W sono disponibili a 20 km/h. È fantastico avere più energia, ma la potenza degli alternatori raddoppia solo quando la velocità raddoppia. Quindi, se hai l'alternatore perfetto per un vento di 20 km/h, il suo carico potrebbe essere così forte che a 10 km/h non si avvia nemmeno.
Quello che fa MPPT è utilizzare un interruttore a stato solido per impieghi gravosi, per scollegare e quindi ricollegare un alternatore molto rapidamente. Ti consente di regolare quanto carico trasporta un alternatore e il Multi, dell'MPPT, significa che puoi impostare carichi diversi per velocità diverse.
Questo è molto utile, poiché tutti i tipi di turbine raccolgono la loro massima energia quando il carico è abbinato all'energia disponibile o alla velocità del vento.
COSÌ
Questa non è una ricetta, anche se credo che possa essere copiata da quello che ho postato, e sarei felice di fornire ulteriori informazioni ma suggerisco che l'opzione migliore sarebbe suggerirmi miglioramenti, prima che finisca il concorso Circuiti e Sensori, in modo che io possa considerare, rispondere e forse migliorare questo istruibile.
Continuerò ad aggiornare, rivedere e aggiungere informazioni, quindi se è interessante ora, potresti voler controllare di nuovo tra un po', ma spero di fare un bel po' prima che il concorso Sensors termini il 29/19 luglio.
Inoltre, non sono una bestia particolarmente socievole, ma ogni tanto mi piace una pacca sulla spalla, e questo è uno dei motivi per cui sono qui:-) Dimmi se ti piace vedere il mio lavoro e vuoi vedere ancora per favore:-)
Questo progetto è nato perché volevo un carico controllabile per testare i miei progetti di turbine e volevo che fosse facilmente riproducibile, in modo che anche altri potessero usarlo. A tal fine, mi sono limitato a progettare qualcosa che potesse essere costruito solo con una stampante FDM, senza bisogno di altre macchine utensili. Non sembrano esserci molti prodotti commerciali che soddisfano la necessità di un alternatore a coppia elevata, bassa velocità e non cogging, sebbene ce ne siano alcuni dalla Cina. In generale non c'è molta richiesta perché i sistemi di trasmissione sono così economici e l'elettricità è così economica.
Quello che volevo era qualcosa che producesse circa 12V a 40-120 giri/min e circa 600-750W a 120-200 giri/min. Volevo anche che fosse compatibile con i controller PMA trifase economici del mondo RC (Electronic Speed Controller di ESC). Un requisito finale era che fosse un fuoricampo (la cassa o il guscio con i magneti ruota, mentre l'albero con lo statore è fisso), con un albero che passa completamente attraverso la cassa e uno statore che si fissa all'albero.
Questo istruibile è un lavoro in corso e lo sto pubblicando in modo che le persone possano avere una visione del processo, non tanto perché penso che dovrebbero copiarlo. Una cosa fondamentale che cambierei è che la piastra di supporto del filo che ho costruito non è abbastanza forte da incanalare correttamente i campi magnetici attorno all'anello, quindi gran parte del flusso magnetico pagato in quei magneti viene sprecato sul retro. Quando rifarò il progetto, cosa che farò a breve, probabilmente lo farei con le piastre di supporto magnetiche come piastre in acciaio tagliate a cnc. L'acciaio sarebbe abbastanza economico, molto più forte e semplificherebbe la maggior parte di questa build. È stato interessante realizzare i compositi FDM/filo/gesso come ho illustrato qui, e con il PLA caricato con ferro, anche le cose sarebbero state diverse. Ho deciso però che volevo qualcosa che sarebbe durato davvero, quindi piastre d'acciaio.
Ho fatto buoni progressi su questa versione, che userò per testare questo VAWT. Non sono ancora arrivato in termini di prestazioni a bassa tensione. Penso che il mio wattaggio/coppia sia nella giusta misura, aggiornerò man mano che le cose progrediscono, ma a questo punto quello che ho ha buone possibilità di essere il carico controllabile di cui ho bisogno. Quando è in cortocircuito sembra essere in grado di fornire un bel po' di resistenza alla coppia, più che sufficiente per testare la turbina. Ho solo bisogno di creare una banca di resistenza controllata, e ho un amico che mi sta aiutando in questo.
Una cosa di cui parlerò brevemente è che, come molte persone ora, ho avuto una stampante 3D (che utilizza PLA FDM) per alcuni anni, da cui ho goduto di 20-30 kg. Spesso lo trovo frustrante, poiché parti di qualsiasi dimensione/forza sono costose e molto lente da stampare, o economiche, veloci e fragili.
So quante migliaia di queste stampanti 3D sono là fuori, spesso senza fare nulla perché ci vuole troppo tempo o costa troppo per realizzare parti utili. Ho trovato una soluzione interessante per parti più forti e più veloci dalla stessa stampante e PLA.
La chiamo una "struttura colata", in cui l'oggetto stampato (composto da 1 o più parti stampate, e talvolta cuscinetti e alberi), sono realizzati con vuoti progettati per essere versati pieni di un riempitivo liquido indurente. Ovviamente alcune delle scelte ovvie per un riempimento colato sarebbero qualcosa come la resina epossidica caricata con fibra di vetro tagliata a filo corto, che potrebbe essere utilizzata per assemblaggi ad alta resistenza e leggeri. Sto provando anche qualche idea più economica e più ecologica. L'altro lato di questo assemblaggio di "struttura colata", è che la cavità o il vuoto che stai per riempire, può avere elementi ad alta resistenza di piccolo diametro, infilati pretensionati sullo "stampo/tassello" stampato, che rende la struttura risultante un composito nei materiali e nella struttura, in parte Stressed Skin (la guaina in PLA), ma con un nucleo ad alta resistenza alla compressione che include anche elementi ad alta resistenza alla trazione. Farò una seconda istruzione con questo, quindi ne parlerò qui, solo per coprire come riguarda questa build.
Passaggio 1: elenco e processo dei materiali
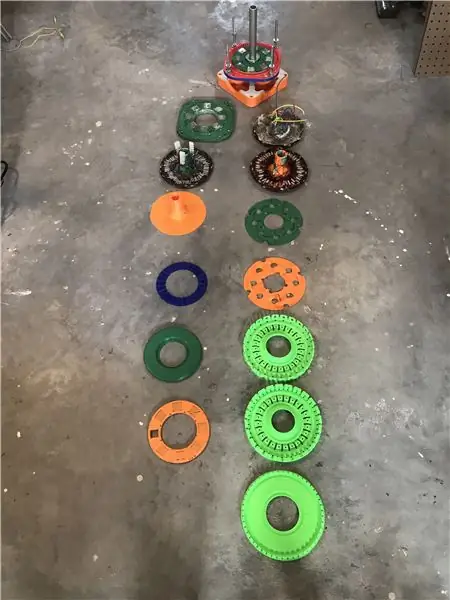
Il PMA è costituito da 3 gruppi, ciascuno dei quali contiene o utilizza una varietà di parti e materiali.
Dall'alto (lato cuscinetto) al basso (lato statore), 1. Supporto del cuscinetto e matrice di cuscinetti superiore
2. Statore
3. Serie di magneti inferiori
1. Il supporto del cuscinetto e l'array di magneti superiori
Per questo ho usato le parti stampate in 3D elencate sopra
- 150mm8poli caricatore superiore e supporto per cuscinetti CV5.stl,
- piastra interna lato cuscinetto
- piastra esterna lato cuscinetto
- Cuscinetto autoallineante da 1 "ID (come quello utilizzato nei blocchi cuscino standard + aggiungi collegamento a Internet),
- 25' di filo di acciaio zincato da 24 g
- 15' di filo di acciaio zincato da 10 g
- 2 rotoli di lana d'acciaio grossa
Facoltativamente, il filo di acciaio pesante e la lana d'acciaio potrebbero essere sostituiti con piastre di supporto in acciaio, taglio laser / getto d'acqua o potrebbe essere possibile una piastra di supporto magnetica stampata in 3D (ma un filo di acciaio pesante è ancora una buona idea in quanto resisterà alla deformazione plastica oltre tempo). Ho provato a fondere una piastra di supporto con resina epossidica caricata con polvere di ossido di ferro e ho avuto un certo successo. Migliorare l'accoppiamento del flusso tra i magneti nell'array lateralmente utilizzando una piastra di supporto più efficace dovrebbe aumentare i Volt a regimi inferiori. È anche bene tenere presente che questo è il principale componente strutturale e la piastra posteriore trasferisce le forze dai magneti ai montanti. Le forze magnetiche che tirano le piastre l'una verso l'altra possono essere centinaia di libbre e le forze aumentano esponenzialmente (cubo, alla terza potenza) man mano che le piastre si avvicinano. Questo può essere molto pericoloso e bisogna fare attenzione con gli attrezzi e qualsiasi altro oggetto che possa essere attratto dalla piastra assemblata o dalla sua parte posteriore!
Ho usato circa 300 piedi di filo magnetico rivestito da 24 g negli avvolgimenti che tratterò in dettaglio più avanti.
Passaggio 2: fabbricazione delle piastre magnetiche
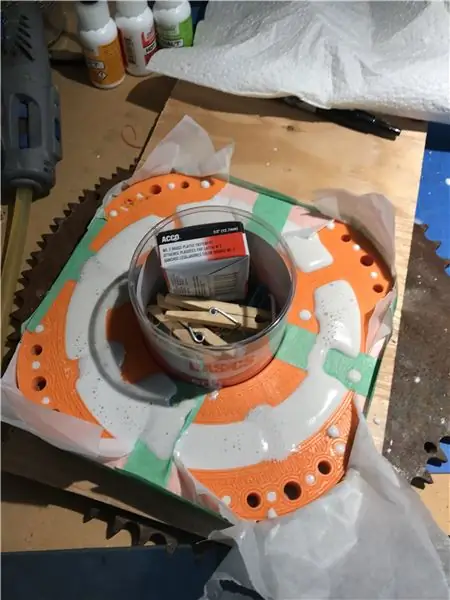
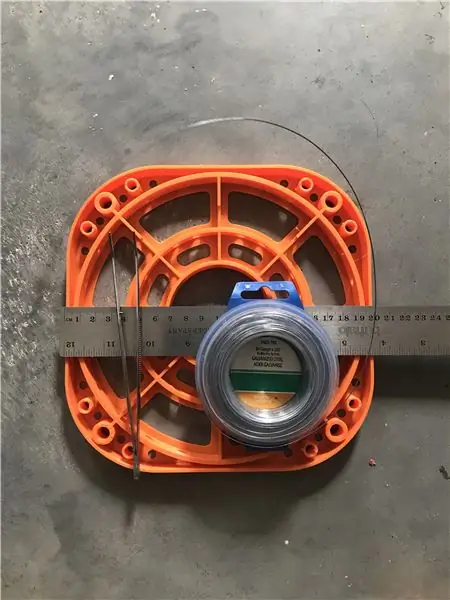
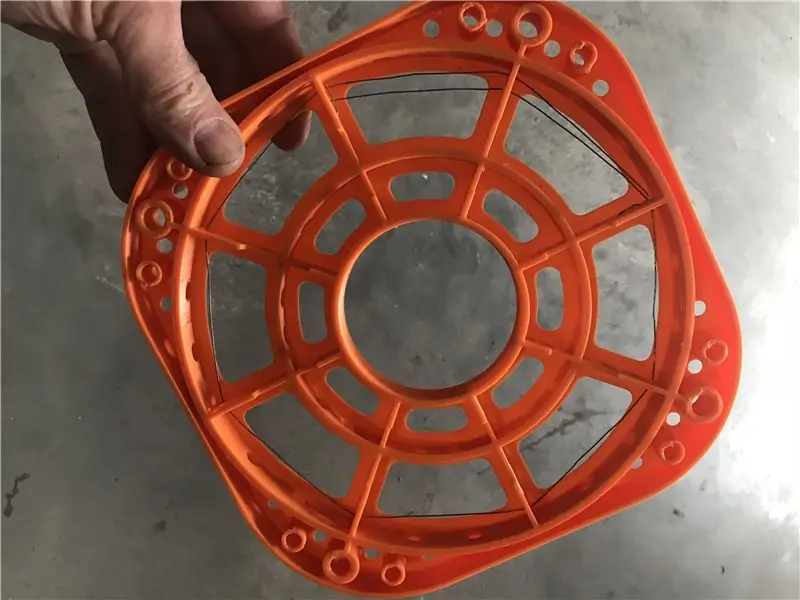
In questo alternatore a flusso assiale, per ridurre al minimo il cogging e massimizzare l'uscita, sto usando due array di magneti, uno su ciascun lato delle bobine dello statore. Ciò significa che non è necessario alcun nucleo magnetico per attirare il campo magnetico attraverso gli avvolgimenti di rame, come fanno la maggior parte delle geometrie del motore/alt. Ci sono alcuni progetti di flusso assiale che utilizzano nuclei ferris e potrei provare alcuni esperimenti in questo modo in futuro. Mi piacerebbe provare del materiale caricato con ferro stampabile in 3D.
In questo caso, ho scelto un array di magneti a 8 poli in un cerchio di circa 150 mm, utilizzando magneti in terre rare da 1"x1"x0,25". Questa dimensione era per garantire che tutte le parti si adattassero a un letto di stampa da 210 mm x 210 mm. In generale, ho dimensionato prima questo alternatore capendo che maggiore è il diametro, migliore è in termini di volt per giri/min, quindi l'ho reso grande quanto sarebbe comodamente adatto al mio letto di stampa. Cordiali saluti, c'è più di una ragione per cui più grande è meglio: più spazio per magneti, più i magneti sono lontani dal centro, più velocemente viaggiano e c'è più spazio anche per il rame! Tutte queste cose possono sommarsi velocemente! Tuttavia una conclusione a cui sono giunto è che in questa gamma di dimensioni, un convenzionale il sistema di flusso potrebbe essere una costruzione casalinga migliore. I rotori piccoli non hanno molto spazio e le cose possono diventare piuttosto strette, specialmente se stai facendo un albero passante come ho fatto in questo progetto. Anche se il tuo magnete (lunghezza radiale) è piccolo rispetto al diametro del rotore, come in questo, (da circa 6" di diametro a 1" magnete), quindi il windi ng diventa un po 'strano con l'avvolgimento dell'estremità interna che è solo circa metà della lunghezza dell'esterno.
Torna all'istruzione! Il modo in cui ho assemblato le piastre magnetiche di questo alternatore è quello di incollare prima la piastra magnetica (verde) alla flangia/piastra di supporto rossa. Ho quindi posizionato la piastra del magnete su alcuni strati sottili di compensato (spessore circa 0,75 pollici) e ho posizionato entrambi su una piastra di acciaio pesante, per consentire ai magneti di bloccare il gruppo in posizione. Quindi ho avvolto il filo di acciaio, sul retro delle piastre magnetiche. Non è andata proprio come speravo. Il forte campo magnetico ha tirato il filo verso il centro dei magneti e non sono riuscito a piegare ogni fila di filo per adattarsi perfettamente al punto successivo, senza spingere il primo avvolgimento. Speravo di poter semplicemente avvolgere il filo e il flusso magnetico lo avrebbe bloccato. Poi ho provato a tagliare anelli di filo, e questo era meglio, ma ancora lontano da quello che avevo speravo in termini di ottenere una piastra di supporto coerente dal filo. Sono possibili modi più complessi per ottenere questo risultato e potrebbero valere la pena di sperimentazioni future. Ho anche provato a utilizzare lana d'acciaio, compattata nel campo magnetico, come piastra di supporto o flusso percorso di ritorno. Sembrava funzionare, ma la densità effettiva del ferro non sembrava essere molto alta, quindi di non ho testato la sua efficacia, in parte perché credevo che la struttura del filo fosse importante per i carichi meccanici sulle piastre magnetiche. La lana d'acciaio potrebbe anche valere un'indagine futura, tuttavia le piastre d'acciaio tagliate a getto d'acqua sono probabilmente la prossima opzione che proverò.
Successivamente, ho preso la parte arancione stampata in 3D e ho intrecciato del filo attraverso e attorno ad essa, lungo quelle che mi sembravano essere le direzioni del carico massimo, bullone contro bullone e bullone per centrare alcune volte su ogni angolo. L'ho anche avvolto attorno ai fori dei bulloni in cui l'asta tutta filettata passa come pali di sollevamento per mantenere e regolare la distanza tra le piastre.
Dopo essermi accertato che la piastra magnetica e la flangia fossero abbastanza buone e che la piastra di supporto arancione fosse stata filettata in modo soddisfacente con filo di rinforzo, ho unito le due con la colla. È necessario prestare attenzione poiché questo giunto di colla dovrà essere a tenuta d'acqua o chiudere. Ho avuto perdite le prime due volte, ed è un disastro, spreca un sacco di gesso ed è più stress del necessario. Consiglierei di tenere della puntina blu o altra gomma da masticare come un adesivo non permanente in giro per riparare rapidamente le perdite. Una volta unite le parti, riempire con il materiale di rinforzo di vostra scelta. Ho usato un gesso duro, modificato con colla vinilica. L'intonaco dovrebbe raggiungere i 10.000 psi di compressione, ma non molto in tensione (quindi il filo). Mi piacerebbe provare la resina epossidica con vetro tritato e cabosil, o cemento e miscele.
Una cosa utile dell'intonaco è che una volta che prende a calci hai un bel po' di tempo in cui è duro, ma fragile e le perdite o le macchie possono essere facilmente raschiate o eliminate.
In questo design, ci sono due piastre magnetiche. Uno ha un cuscinetto, un'unità autoallineante con supporto standard da 1 . Ho premuto il mio nell'array di magneti all'inizio. Per l'applicazione per cui l'ho progettato, un secondo cuscinetto sarà posizionato nella turbina sopra l'alternatore, quindi ho usava solo un cuscinetto autoallineante. Questo è stato un po' un problema alla fine. Queste parti potrebbero anche essere assemblate con ogni piastra magnetica con un cuscinetto, se i fili di uscita dallo statore fossero condotti internamente attraverso l'albero montato. consentire il montaggio di eliche controrotanti su un albero/tubo comune e non rotante.
Passaggio 3: creazione dello statore

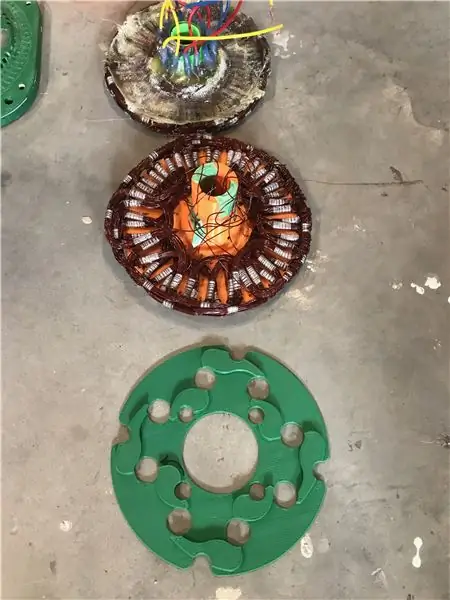
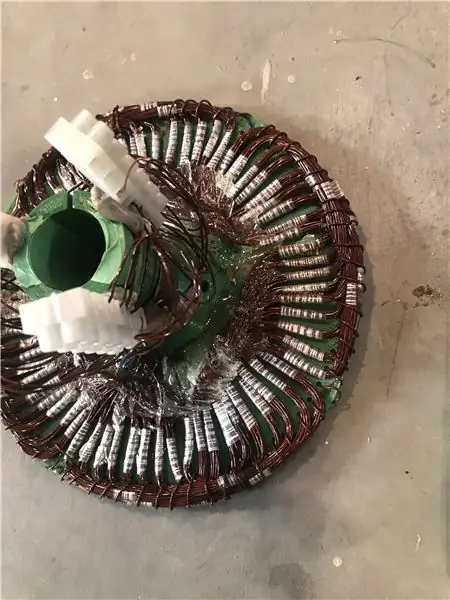
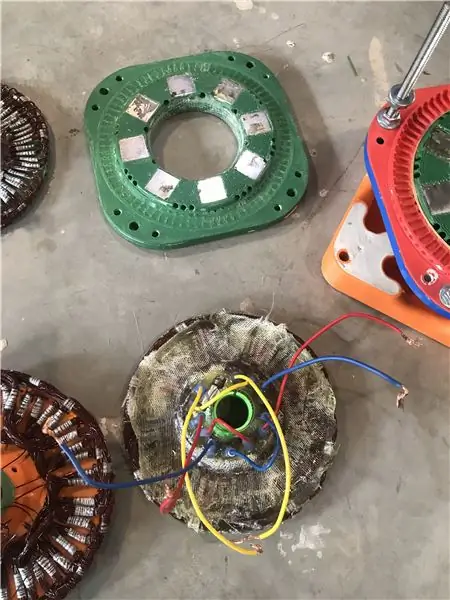
In linea con il mio tema di cercare di spiegare cosa ho fatto e perché all'epoca sembrava una buona idea, lo statore richiederà un po' più di spazio.
In un PMA, generalmente gli avvolgimenti sono stazionari, mentre i gruppi magnetici ruotano. Non è sempre così, ma quasi sempre. In un assemblaggio di flusso assiale, con la comprensione della fondamentale "regola della mano destra", si intende che qualsiasi conduttore che incontra un campo magnetico rotante, avrà corrente e tensione generate tra le estremità del filo, con la quantità di corrente utile proporzionale alla direzione del campo. Se il campo si muove parallelamente al filo (ad es. in un cerchio attorno all'asse di rotazione), non verrà generata alcuna corrente utile, ma verranno generate significative correnti parassite, che si oppongono al movimento dei magneti. Se il filo scorre perpendicolare, verrà raggiunta la tensione e la corrente più elevate.
Un'altra generalizzazione è che lo spazio all'interno dello statore, attraverso il quale passa il flusso magnetico durante la rotazione, per la massima potenza di uscita, dovrebbe essere riempito con quanto più rame, tutto disposto radialmente, il più possibile. Questo è un problema per i sistemi a flusso assiale di piccolo diametro, poiché in questo caso l'area disponibile per il rame vicino all'albero è una frazione dell'area sul bordo esterno. È possibile ottenere il 100% di rame nell'area più interna incontrata dal campo magnetico, ma all'interno di questa geometria si ottiene solo il 50% sul bordo esterno. Questa è una delle ragioni più forti per stare alla larga da progetti di flusso assiale troppo piccoli.
Come ho detto in precedenza, questo istruibile non riguarda come lo rifarei, ma piuttosto puntare in alcune direzioni che sembrano promettenti e mostrare alcune delle buche che possono essere raggiunte su questo percorso.
Nel progettare lo statore volevo renderlo il più flessibile possibile in termini di volt di uscita per giri/min, e volevo che fosse trifase. Per la massima efficienza, riducendo al minimo le correnti parassite generate, qualsiasi "gamba" (ogni lato di una bobina dovrebbe essere pensato come una "gamba") dovrebbe incontrare solo un magnete alla volta. Se i magneti sono vicini tra loro o si toccano come nel caso di molti motori rc ad alto rendimento, durante il tempo in cui la "gamba" sta attraversando l'inversione del flusso magnetico, si svilupperanno significative correnti parassite. Nelle applicazioni per motori questo non ha molta importanza, poiché la bobina viene alimentata dal controller quando si trova nelle posizioni giuste.
Ho dimensionato l'array di magneti con questi concetti in mente. Gli otto magneti nell'array sono ciascuno di 1" di diametro e lo spazio tra di loro è di 1/2". Ciò significa che un segmento magnetico è lungo 1,5" e ha spazio per 3 x 1/2" "gambe". Ogni "gamba" è una fase, quindi in qualsiasi momento, una gamba vede un flusso neutro, mentre le altre due vedono un flusso crescente e un flusso decrescente. Uscita trifase perfetta, anche se dando al punto neutro così tanto spazio (per ridurre al minimo le correnti parassite) e utilizzando magneti quadrati (o a forma di torta), il flusso raggiunge quasi il picco all'inizio, rimane alto, quindi scende rapidamente a zero. Questo tipo di output penso sia chiamato trapezoidale e può essere difficile per alcuni controller che capisco. Magneti rotondi da 1" nello stesso apparato darebbero più di una vera onda sinusoidale.
Generalmente questi alternatori autocostruiti sono stati costruiti utilizzando "bobine", fasci di filo a forma di ciambella, in cui ciascun lato della ciambella è una "gamba" e un numero di bobine può essere collegato insieme, in serie o in parallelo. Le ciambelle sono disposte in cerchio, con i loro centri allineati con il centro del percorso del magnete. Funziona, ma ci sono alcuni problemi. Un problema è che poiché i conduttori non sono radiali, gran parte del conduttore non passa a 90 gradi rispetto al campo magnetico, quindi vengono generate correnti parassite, che appaiono come calore nella bobina e resistenza alla rotazione nella matrice del magnete. Un altro problema è che poiché i conduttori non sono radiali, non si impacchettano insieme così bene. L'uscita è direttamente proporzionale alla quantità di filo che puoi inserire in questo spazio, quindi l'uscita è ridotta da "gambe" non radiali. Mentre sarebbe possibile e talvolta è fatto in progetti commerciali, avvolgere una bobina con "gambe radiali, unite in alto e in basso, richiede il doppio dell'avvolgimento finale di un avvolgimento a serpentina in cui la parte superiore di una gamba è unita alla parte superiore del prossima gamba appropriata, e poi la parte inferiore di quella gamba viene unita alla prossima gamba appropriata, e così via.
L'altro grande fattore negli alternatori a flusso assiale di questo tipo (magneti rotanti sopra e sotto lo statore), è lo spazio tra le piastre. Questa è una relazione della legge del cubo, poiché riduci la distanza tra le piastre di 1/2, la densità del flusso magnetico aumenta di 8 volte. Più sottile puoi rendere il tuo statore, meglio è!
Con questo in mente ho realizzato una maschera di avvolgimento a 4 lobi, ho impostato un sistema per misurare circa 50 piedi di trefoli di filo e ho avvolto la maschera 6 volte, creando fasci di fili di circa 6 mm di diametro. Questi li ho inseriti nell'anello distanziatore blu, legandoli attraverso i fori in modo che le estremità del filo uscissero dal retro. Non è stato facile. È stato un po' aiutato dall'avere accuratamente legato i fasci con del nastro adesivo in modo che non fossero allentati, e prendendomi il mio tempo e usando uno strumento di formatura in legno liscio per spingere i fili in posizione. Una volta che sono stati tutti legati in posizione, l'anello distanziatore blu è stato posizionato nella più grande delle vaschette di formatura verde chiaro e, con l'aiuto dello strumento per la formatura delle ciambelle verde scuro, sull'altro lato della vasca verde chiaro, accuratamente schiacciato con una morsa da banco. Questa vasca di formatura ha una scanalatura per l'inserimento delle torsioni del cavo di collegamento. Ciò richiede tempo e pazienza mentre si ruota con attenzione di circa 1/5 di giro, si preme, si ruota e si continua. Questo forma il disco piatto e sottile, consentendo allo stesso tempo agli avvolgimenti finali di impilarsi. Potresti notare che il mio avvolgimento a 4 lobi ha "gambe" dritte ma le connessioni interne ed esterne non sono rotonde. Questo avrebbe dovuto renderli più facili da impilare. Non ha funzionato così bene. Se lo facessi di nuovo, farei in modo che gli avvolgimenti interni ed esterni seguano percorsi circolari.
Dopo averlo piatto e sottile, e i bordi compressi, ho avvolto un nastro piatto attorno al bordo per compattarlo, e un altro su, giù e intorno a ciascuna gamba e poi anche a quella accanto. Fatto ciò, puoi rimuovere i fili di collegamento e passare alla vasca di pressatura più piccola, quindi tornare alla morsa e premerla il più sottile e piatta possibile. Una volta che è piatto, rimuoverlo dalla vasca della pressa. Invece del complesso processo di incerare accuratamente e rivestire stampi come questo con composti distaccanti, generalmente uso solo un paio di strati di pellicola estensibile (dalla cucina). Stendi un paio di strati sul fondo dello stampo e appoggia la fibra di vetro sulla pellicola estensibile. Quindi aggiungi il tubo di montaggio dello statore, che si adatta alla parte superiore della vasca di formatura verde chiaro, ma ha lo strato di pellicola estensibile e fibra di vetro in mezzo. Quindi rimetti in posizione l'avvolgimento dello statore per spingere verso il basso sia l'involucro estensibile che la fibra di vetro e bloccare il tubo di montaggio dello statore in posizione. Quindi tornare alla morsa e premere di nuovo in piano. Una volta che si è adattato bene alla vasca, con la pellicola estensibile e la fibra di vetro inserite a sandwich, viene aggiunto un panno in fibra di vetro (con un foro al centro per il tubo di montaggio dello statore).
Ora è pronto per versare il materiale legante, comunemente usati resina epossidica o poliestere. Prima che questo sia fatto, è importante un'attenta preparazione poiché una volta avviato questo processo non puoi davvero fermarti. Ho usato una piastra di base stampata in 3D che avevo realizzato in precedenza, con un foro da 1 "al centro e una piastra piatta attorno ad essa. Ho usato un pezzo da 16" di tubo di alluminio da 1", su cui si sarebbe adattato il tubo di montaggio dello statore tenuto perpendicolare alla piastra piana. La vasca di formatura verde, l'avvolgimento dello statore e il tubo di montaggio dello statore sono stati fatti scorrere verso il basso per sedersi sulla piastra piana. Prima di mescolare la resina epossidica, ho preparato 4 pezzi di pellicola termoretraibile e ho posizionato con cura un quinto pezzo sul formando una ciambella verde scuro, così avrebbe le rughe minime sulla faccia contro l'avvolgimento dello statore. Dopo aver mescolato la resina epossidica e versata sul panno in fibra di vetro, ho quindi steso con cura l'involucro estensibile attorno al tubo da 1 "e ho posizionato il verde formando un anello sopra di esso. Avevo anche preparato un paio di vecchi rotori dei freni, che davano un po' di peso, e si sedevano bene sulla ciambella verde. Dopo questo ho messo una pentola capovolta sopra i rotori dei freni e sopra la pentola ho impilato circa 100 libbre di roba. L'ho lasciato per 12 ore ed è venuto fuori uno spessore di circa 4-6 mm.
Passaggio 4: test e sensori
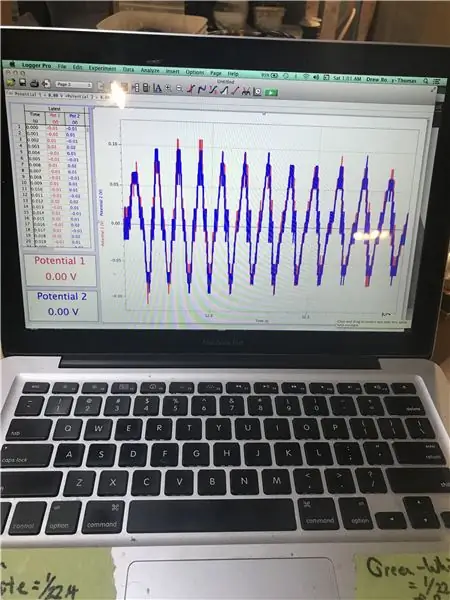
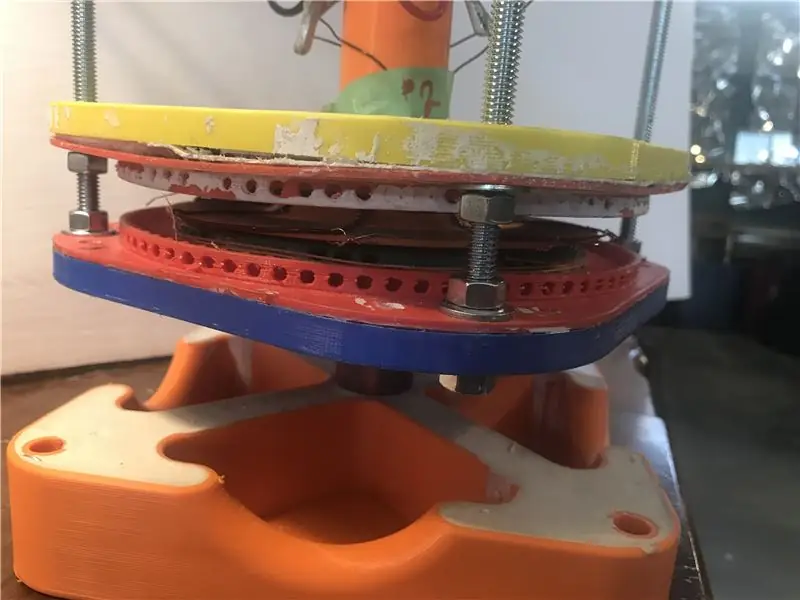
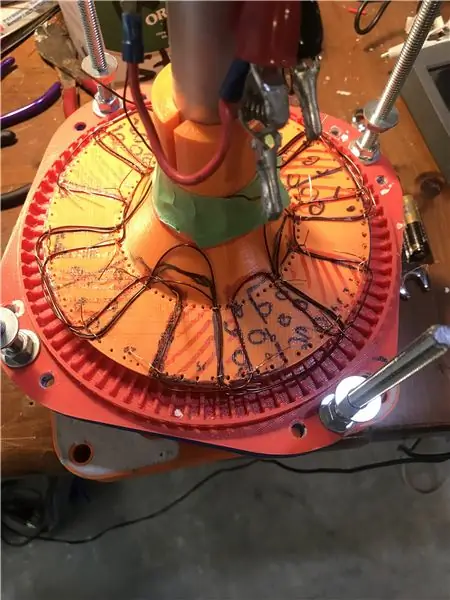
Ci sono un certo numero di ingressi e uscite misurabili dall'alternatore e misurarli tutti allo stesso tempo non è facile. Sono molto fortunato ad avere alcuni strumenti di Vernier che rendono tutto questo molto più semplice. Vernier realizza prodotti di livello educativo, non certificati per uso industriale, ma molto utili per sperimentatori come me. Uso un data logger Vernier, con una varietà di sensori plug and play. In questo progetto utilizzo sonde di corrente e tensione basate su hall, per misurare l'uscita dell'alternatore, un sensore ottico per fornire la velocità dell'alternatore e una cella di carico per misurare l'ingresso di coppia. Tutti questi strumenti vengono campionati circa 1000 volte al secondo e registrati sul mio laptop, utilizzando il logger Vernier come dispositivo passthrough AD. Sul mio laptop il software associato può eseguire calcoli in tempo reale basati sugli ingressi, combinando i dati di coppia e velocità per fornire la potenza dell'albero di ingresso in tempo reale in Watt e i dati di uscita in tempo reale in Watt elettrici. Non ho finito con questo test, e l'input di qualcuno che ha una migliore comprensione sarebbe utile.
Un problema che ho è che questo alternatore è davvero un progetto parallelo, e quindi non voglio dedicarci troppo tempo. Così com'è, penso di poterlo usare per un carico controllabile per la mia ricerca VAWT, ma alla fine mi piacerebbe lavorare con le persone per perfezionarlo, in modo che sia un abbinamento efficiente per la mia turbina.
Quando ho iniziato la ricerca VAWT circa 15 anni fa, mi sono reso conto che testare VAWT e altri motori primi è più complesso di quanto la maggior parte delle persone creda.
Un problema primario è che l'energia rappresentata in un fluido in movimento è esponenziale alla sua velocità di movimento. Ciò significa che raddoppiando la velocità di un flusso, l'energia contenuta nel flusso aumenta di 8 volte (è al cubo). Questo è un problema, poiché gli alternatori sono più lineari e in generale, se raddoppi il numero di giri di un alternatore, ottieni circa 2 volte i watt.
Questa fondamentale discrepanza tra la turbina (dispositivo di raccolta dell'energia) e l'alternatore (potenza dell'albero in energia elettrica utile) rende difficile scegliere un alternatore per una turbina eolica. Se scegli un alternatore per la tua turbina eolica che genererà la massima potenza disponibile da venti a 20 km/h, probabilmente non inizierà nemmeno a girare fino a 20-25 km/h poiché il carico sulla turbina dall'alternatore sarà troppo alto. Con quella partita dell'alternatore, una volta che il vento è superiore a 20 km, non solo la turbina catturerà solo una frazione dell'energia disponibile nel vento ad alta velocità, la turbina potrebbe superare la velocità e danneggiarsi poiché il carico fornito dall'alternatore non è elevato abbastanza.
Nell'ultimo decennio una soluzione è diventata più economica a causa del calo dei prezzi dell'elettronica di controllo. Invece di cercare di far corrispondere un intervallo di velocità, il progettista calcola la velocità massima a cui il dispositivo deve funzionare e sceglie un alternatore in base alla quantità di energia e alla velocità ideale per la turbina a quella velocità, o leggermente superiore. Questo alternatore, se collegato al suo carico, normalmente fornirebbe troppa coppia a bassa velocità e la turbina sovraccaricata non catturerebbe tutta l'energia che potrebbe avere se fosse caricata correttamente. Per creare il carico corretto, viene aggiunto un controller che disconnette momentaneamente l'alternatore dal carico elettrico, consentendo alla turbina di accelerare alla velocità corretta e l'alternatore e il carico vengono ricollegati. Questo è chiamato MPPT (Multi Power Point Tracking). Il controller è programmato in modo tale che quando la velocità della turbina cambia (o la tensione dell'alternatore aumenta), l'alternatore viene collegato o scollegato, un migliaio di volte al secondo circa, per adattarsi al carico programmato per quella velocità o tensione.
Consigliato:
Realizza circuiti stampati con laser: 4 passaggi (con immagini)
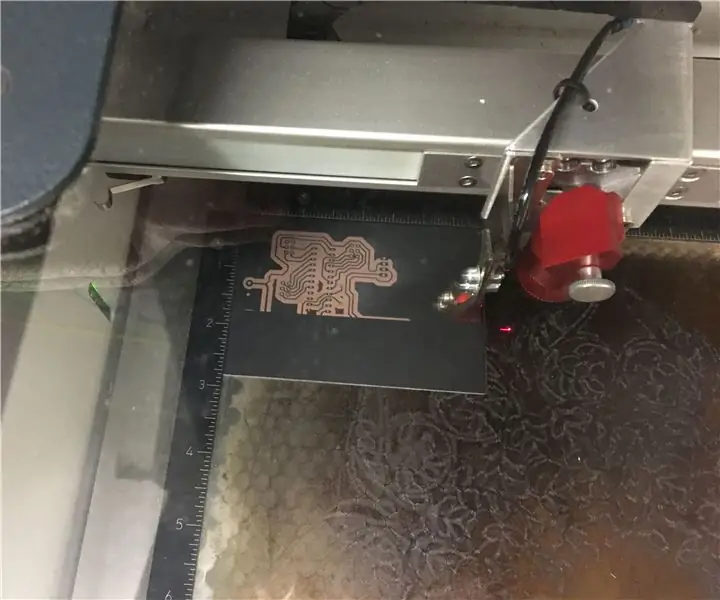
Crea circuiti stampati con i laser: un circuito stampato fatto in casa è buono quanto la maschera che ci metti sopra. Indipendentemente dal metodo che usi per eseguire l'incisione vera e propria, devi comunque incollare un'immagine del tuo circuito sulla scheda e assicurarti che lasci tracce nitide, pulite e solide dietro
Misurazione del flusso con misuratori di portata d'acqua (ultrasuoni): 5 passaggi (con immagini)
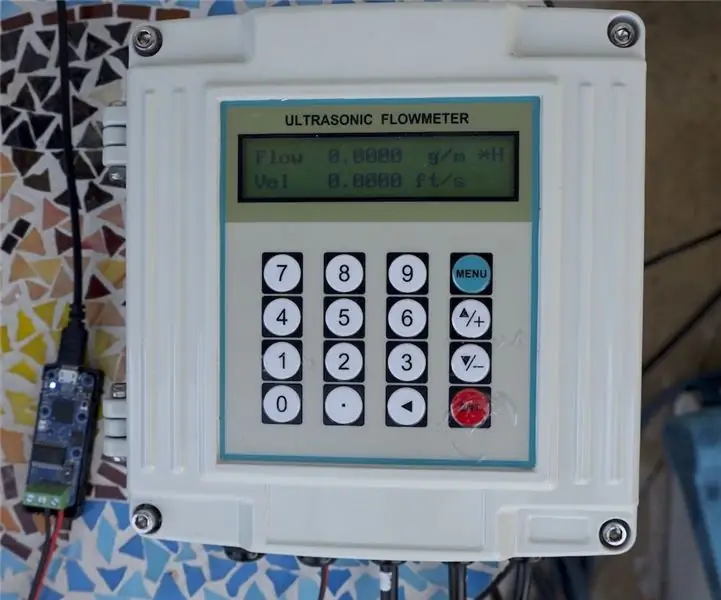
Misurazione della portata con misuratori di portata dell'acqua (ultrasuoni): l'acqua è una risorsa fondamentale per il nostro pianeta. Noi esseri umani abbiamo bisogno di acqua ogni giorno. E l'acqua è necessaria per una varietà di industrie e noi esseri umani ne abbiamo bisogno ogni giorno. Poiché l'acqua è diventata più preziosa e scarsa, la necessità di un monitoraggio efficace e l'uomo
Misurazione della velocità del flusso: 7 passaggi (con immagini)
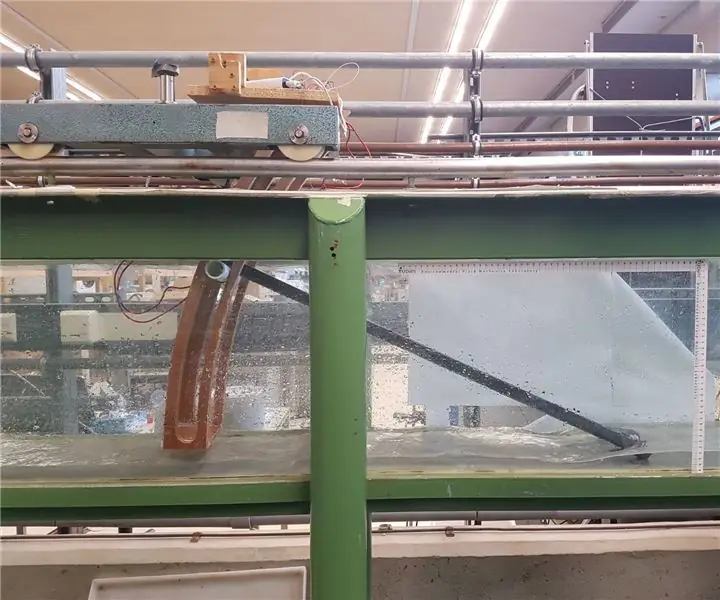
Misurazione della velocità del flusso: con questo dispositivo è possibile misurare la velocità di un flusso a flusso libero. L'unica cosa necessaria sono Arduino e alcune abilità di crafting di base e, naturalmente, un flusso libero. Non è il modo più pratico per misurare la velocità
Autoeccitare un alternatore senza generatore CC, banco di condensatori o batteria: 5 passaggi (con immagini)
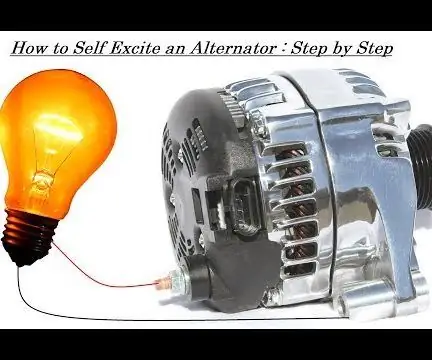
Autoeccitare un alternatore senza alcun generatore CC, banco di condensatori o batteria: Ciao! Questo istruibile è per convertire un alternatore eccitato dal campo in uno autoeccitato. Il vantaggio di questo trucco è che non dovrai alimentare il campo di questo alternatore con una batteria da 12 volt ma invece si accenderà da solo in modo che tu
Creazione di circuiti stampati con una stampante INKJET: 8 passaggi (con immagini)
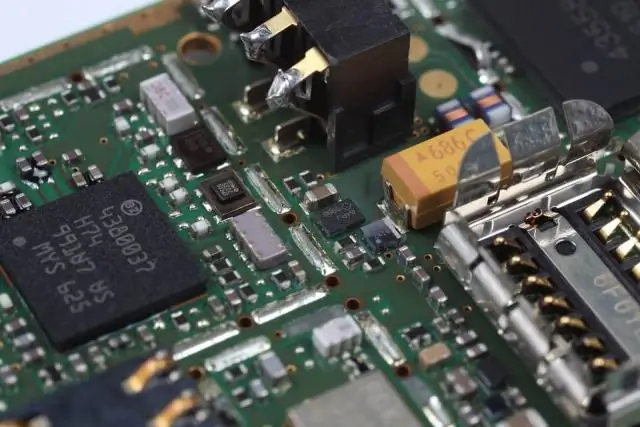
Creazione di circuiti stampati con una stampante INKJET: Quando ho iniziato a esaminare come incidere i miei circuiti stampati, ogni Instructable e tutorial che ho trovato utilizzava una stampante laser e stirava il modello in una sorta di modo. Non possiedo una stampante laser ma ho un inchiostro economico