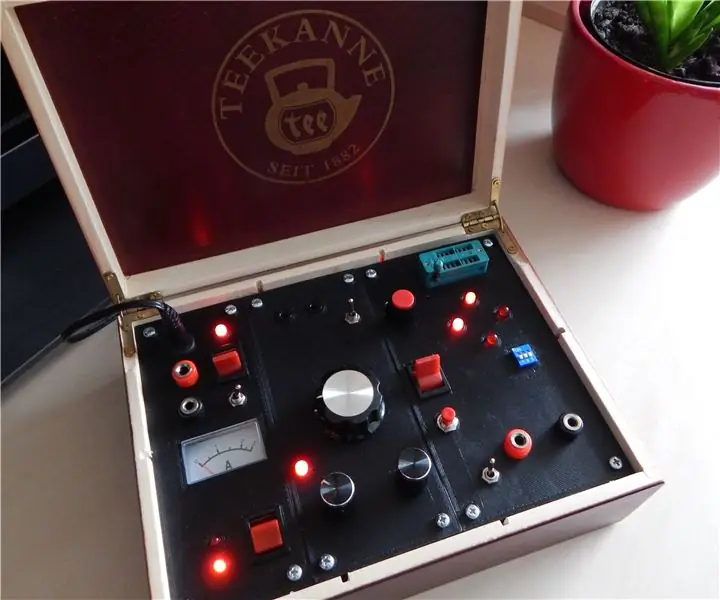
Sommario:
- Passaggio 1: teoria del controllo DC e stepper
- Passaggio 2: schema elettrico
- Passaggio 3: schemi
- Passaggio 4: componenti e strumenti necessari
- Passaggio 5: progettazione del pannello frontale
- Passaggio 6: stampa 3D e verniciatura a spruzzo
- Passaggio 7: cablaggio del pannello
- Passaggio 8: connettori pannello-scheda
- Passaggio 9: PCB
- Passaggio 10: Arduino
- Step 11: Assemblaggio e Collaudo
- Passaggio 12: conclusione
2025 Autore: John Day | [email protected]. Ultima modifica: 2025-01-23 14:49

Pochi mesi fa, un mio amico mi ha regalato un paio di stampanti a getto d'inchiostro e fotocopiatrici scartate. Ero interessato a raccogliere le loro unità di alimentazione, cavi, sensori e soprattutto motori. Ho recuperato quello che potevo e volevo testare tutte le parti per assicurarmi che fossero funzionanti. Alcuni motori erano classificati a 12V, alcuni a 5V, alcuni erano stepper e altri erano motori DC. Se solo avessi un dispositivo, dove potrei semplicemente collegare il motore, impostare la frequenza, il ciclo di lavoro e selezionare un metodo a passi per testarlo.
Ho deciso di costruirlo senza utilizzare un processore di segnale digitale o un microcontrollore. L'umile 555 o tl741 come oscillatore, contatore 4017 e molte porte logiche per le modalità del motore passo-passo. All'inizio mi sono divertito molto a progettare il circuito, oltre a progettare il pannello frontale del dispositivo. Ho trovato una scatola da tè di legno decente per mettere tutto dentro. Ho diviso il circuito in quattro parti e ho iniziato a testarlo su una breadboard. Presto apparvero i primi segni di frustrazione. È stato un disastro. Molte porte, molti circuiti integrati, cavi. Non funzionava correttamente e stavo pensando tra due opzioni: renderlo molto semplice - solo per i motori DC, o metterlo da parte e finirlo a volte più tardi … Ho scelto la seconda opzione.
Passaggio 1: teoria del controllo DC e stepper
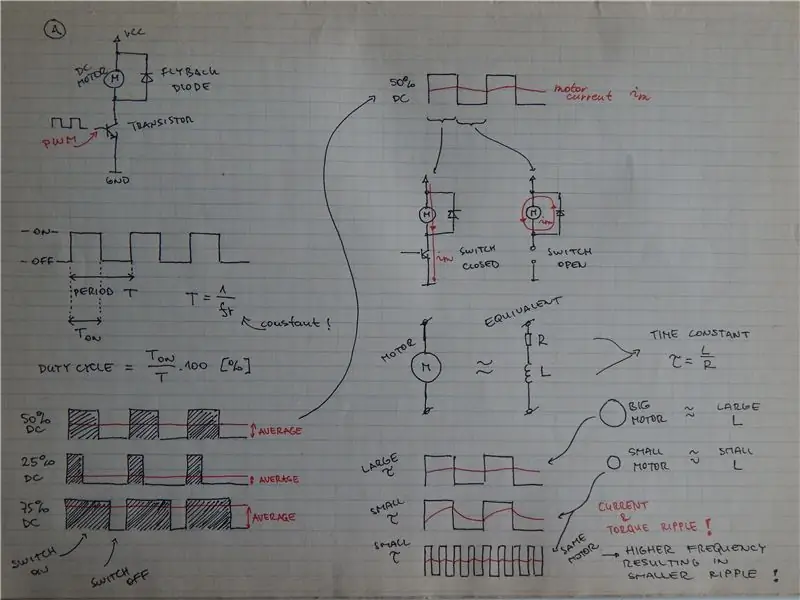
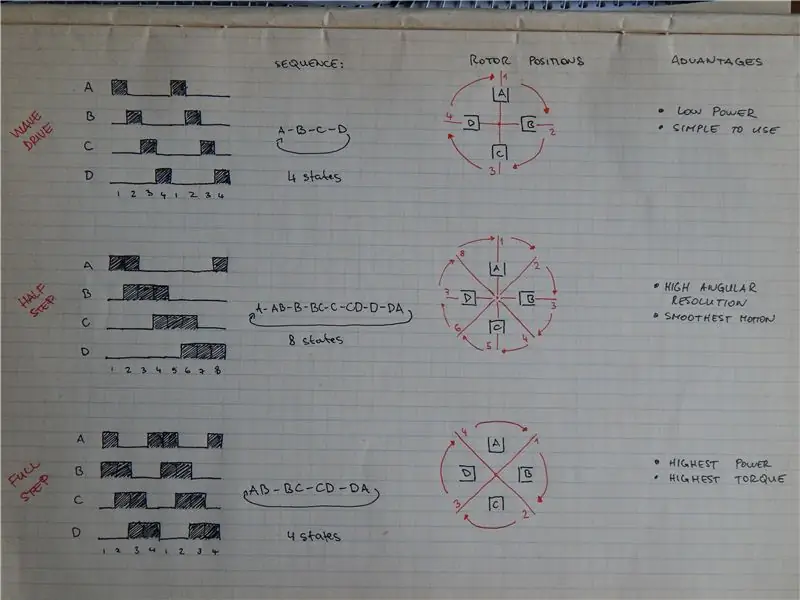
Motore a corrente continua
Il modo più comune per controllare un motore in corrente continua è attraverso la cosiddetta modulazione di larghezza di impulso (PWM). Il PWM viene applicato a un interruttore specifico e accende e spegne il motore. Nell'immagine è possibile vedere il periodo di commutazione indicato e la sua relazione con la frequenza, è indicato anche il tempo di commutazione. Il duty cycle è definito come il tempo di commutazione diviso per il periodo totale. Se manteniamo la frequenza costante, l'unico modo per modificare il ciclo di lavoro è modificare l'orario di accensione. Aumentando il duty cycle, aumenta anche il valore medio della tensione applicata al motore. A causa della tensione più elevata, una corrente maggiore scorre attraverso il motore CC e il rotore ruota più velocemente.
Ma quale frequenza scegliere? Per rispondere a questa domanda, diamo un'occhiata più da vicino a cosa è in realtà un motore a corrente continua. Equivalentemente, può essere descritto come un filtro RL (trascurando indietro l'EMF solo per un momento). Se viene applicata una tensione al motore (filtro RL), la corrente aumenta con una costante di tempo tau pari a L/R. Nel caso di controllo PWM, quando l'interruttore è chiuso, la corrente che attraversa il motore aumenta e diminuisce durante il tempo in cui l'interruttore è spento. A questo punto, la corrente ha la stessa direzione di prima e scorre attraverso il diodo flyback. I motori con potenza maggiore hanno un'induttanza maggiore e quindi una costante di tempo maggiore rispetto ai motori più piccoli. Se la frequenza è bassa quando il motore piccolo è alimentato, si ha una rapida diminuzione della corrente durante il tempo di spegnimento, seguita da un forte aumento durante il tempo di accensione. Questa ondulazione di corrente provoca anche l'ondulazione della coppia del motore. Non lo vogliamo. Pertanto, quando si alimentano motori più piccoli, la frequenza PWM dovrebbe essere maggiore. Utilizzeremo questa conoscenza nella progettazione nei passaggi successivi.
Motore passo-passo
Se vogliamo controllare un motore passo-passo unipolare, utilizzato nell'elettronica per hobby, abbiamo una scelta di 3 opzioni di controllo di base (modalità) - Wave drive (WD), Half Step (HS) e Full Step (FS). La sequenza delle singole modalità e la posizione del rotore è indicata in figura (per semplicità ho indicato un motore con due coppie di poli). In questo caso, Wave Drive e Full Step fanno ruotare il rotore di 90 gradi e possono essere ottenuti ripetendo 4 stati. In modalità Half Step, abbiamo bisogno di una sequenza di 8 stati.
La scelta della modalità dipende dai requisiti del sistema: se abbiamo bisogno di una coppia elevata, la scelta migliore è Full Step, se è sufficiente una coppia inferiore e forse alimentiamo il nostro circuito dalla batteria, è preferibile la modalità Wave Drive. Nelle applicazioni in cui vogliamo ottenere la massima risoluzione angolare e il movimento più fluido, la modalità Half Drive è la scelta ideale. La coppia in questa modalità è inferiore di circa il 30% rispetto alla modalità Full Drive.
Passaggio 2: schema elettrico
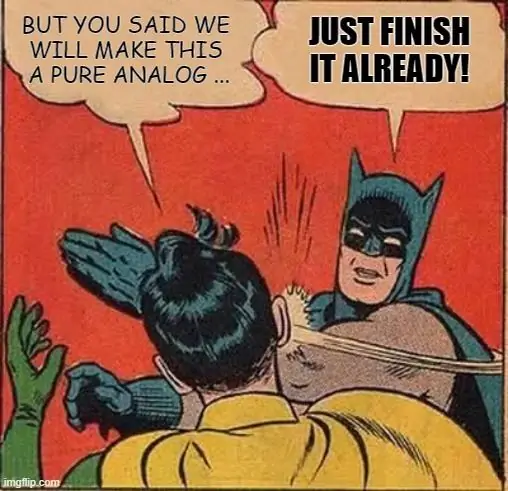
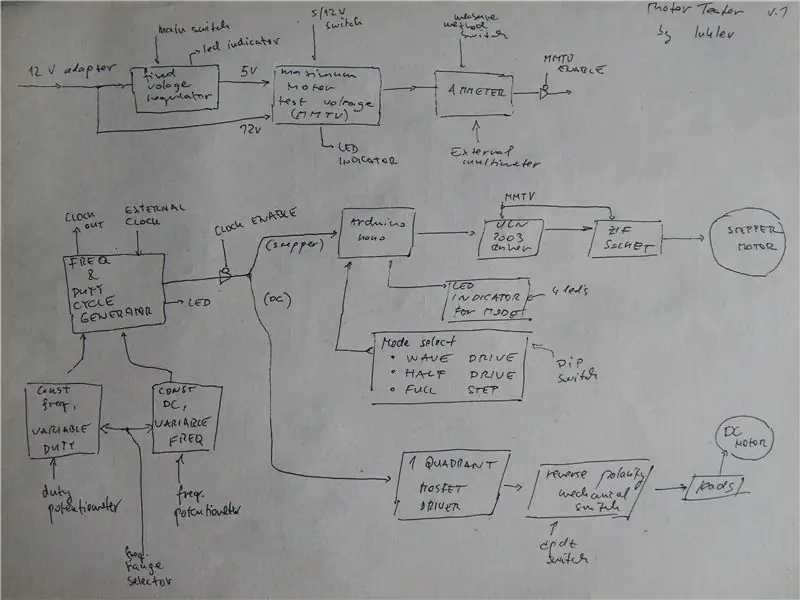
Questo semplice meme descrive in modo appropriato il mio processo di pensiero durante la progettazione.
La parte superiore del diagramma descrive l'alimentazione: un adattatore da 12 volt, che viene ridotto a 5 volt da un regolatore lineare. Volevo essere in grado di scegliere la tensione di prova massima del motore (MMTV) - 12 o 5 volt. L'amperometro integrato bypasserà i circuiti di controllo e misurerà solo la corrente del motore. Sarebbe anche conveniente poter passare dalla misurazione della corrente interna a quella esterna utilizzando un multimetro.
L'oscillatore funzionerà in due modalità: la prima è una frequenza costante e un ciclo di lavoro variabile, e la seconda è una frequenza variabile. Entrambi questi parametri potranno essere impostati utilizzando i potenziometri e un interruttore rotante cambierà modalità e gamme. Il sistema includerà anche un interruttore tra l'orologio interno ed esterno tramite un connettore jack da 3,5 mm. Anche l'orologio interno sarà collegato al pannello tramite un jack da 3,5 mm. Un interruttore e un pulsante per abilitare/disabilitare l'orologio. Il driver del motore CC sarà un driver mosfet a canale N a quadrante singolo. La direzione verrà modificata utilizzando l'interruttore dpdt meccanico. I cavi del motore saranno collegati tramite jack a banana.
La sequenza del motore passo passo sarà controllata da un arduino, che riconoscerà anche 3 modalità di controllo specificate dal dip switch. Il driver del motore passo-passo sarà uln2003. L'Arduino controllerà anche 4 LED che rappresenteranno l'animazione degli avvolgimenti del motore alimentato in queste modalità. Il motore passo passo sarà collegato al tester tramite una presa ZIF.
Passaggio 3: schemi
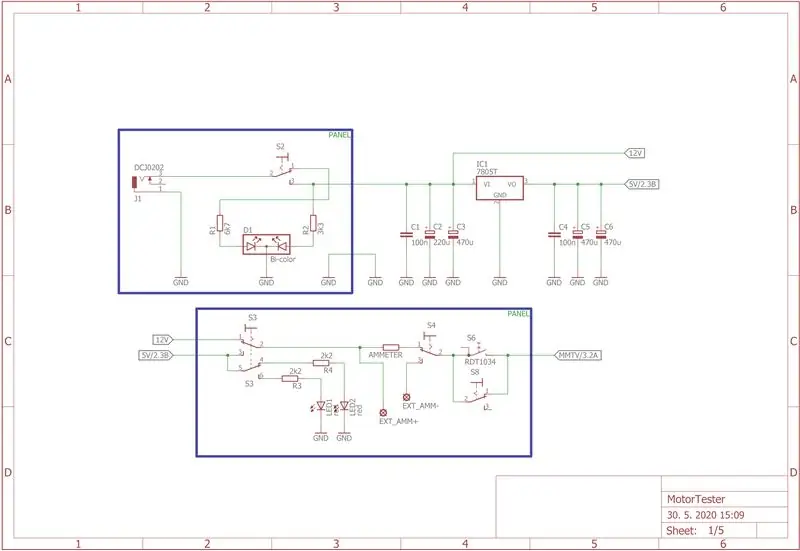
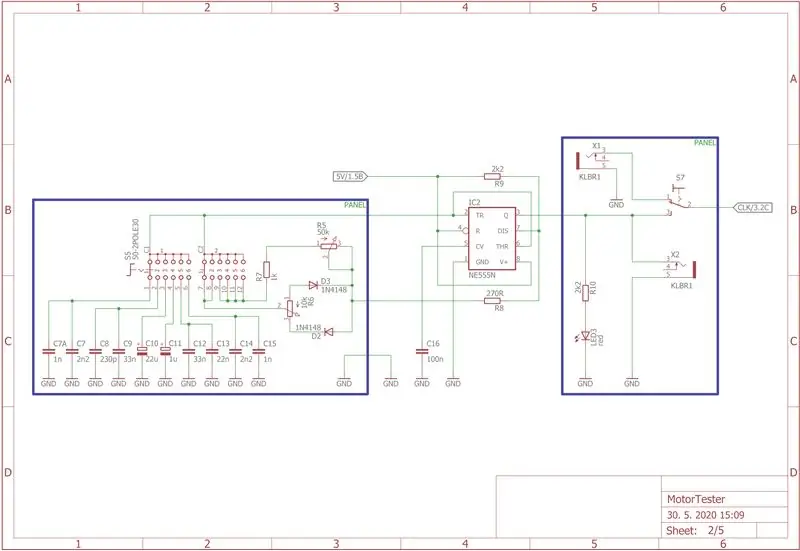
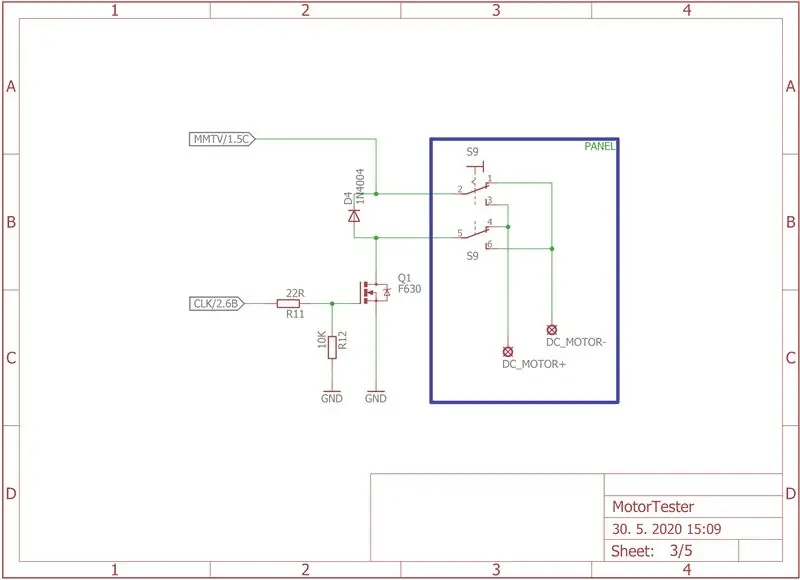
Gli schemi sono divisi in cinque parti. I circuiti racchiusi in riquadri blu rappresentano i componenti che saranno sul pannello.
- Alimentazione elettrica
- Oscillatore
- Driver CC
- Driver passo-passo Arduino
- Driver passo-passo per porte logiche
Foglio n. 5 è il motivo per cui ho lasciato questo progetto mentendo. Questi circuiti formano sequenze per le modalità di controllo precedentemente menzionate - WD, HS e FS. Questa parte è sostituita da arduino completamente nel foglio nr. 4. Sono allegati anche gli schemi completi dell'Aquila.
Passaggio 4: componenti e strumenti necessari

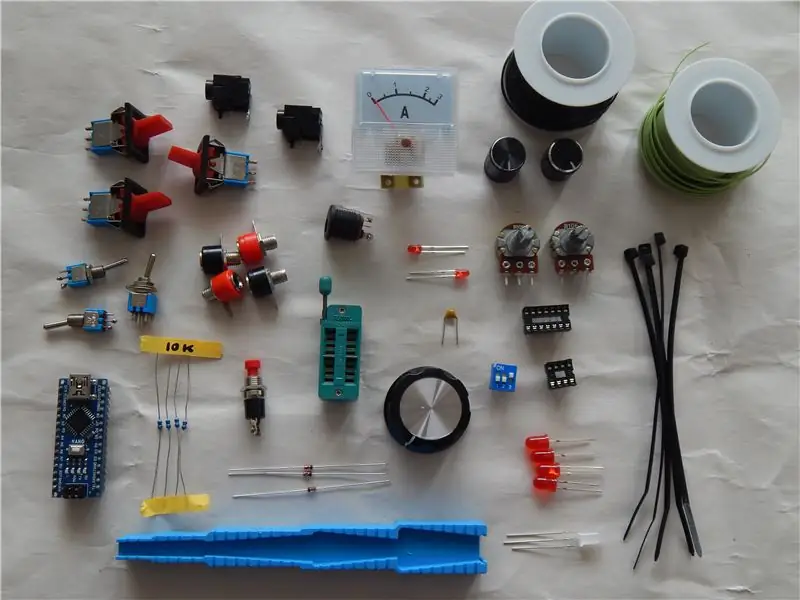
Componenti e strumenti necessari:
- Multimetro
- Calibro
- Taglierina di cartone
- marcatore
- pinzette
- Belle pinze
- Pinze da taglio
- Pinza spelafili
- Saldatore
- Saldare
- Colofonia
- Fili (24 awg)
- 4x interruttore velocità
- 2x interruttore dpdt
- 4x jack banana
- Premi il bottone
- ZIF socket
- 2x jack da 3,5 mm
- Connettore CC
- Arduino nano
- Interruttore DIP a 3 poli
- 2 LED da 3 mm
- LED 5x 5 mm
- LED bicolore
- Manopole del potenziometro
- Prese DIP
- PCB universale
- Connettori Dupont
- Fascette in plastica
e
- Potenziometri
- resistori
- Condensatori
con i valori scelti, corrispondenti alle gamme di frequenza e alla luminosità dei LED.
Passaggio 5: progettazione del pannello frontale
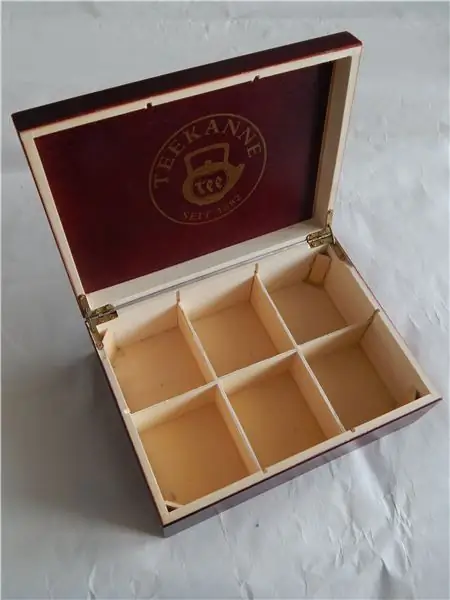
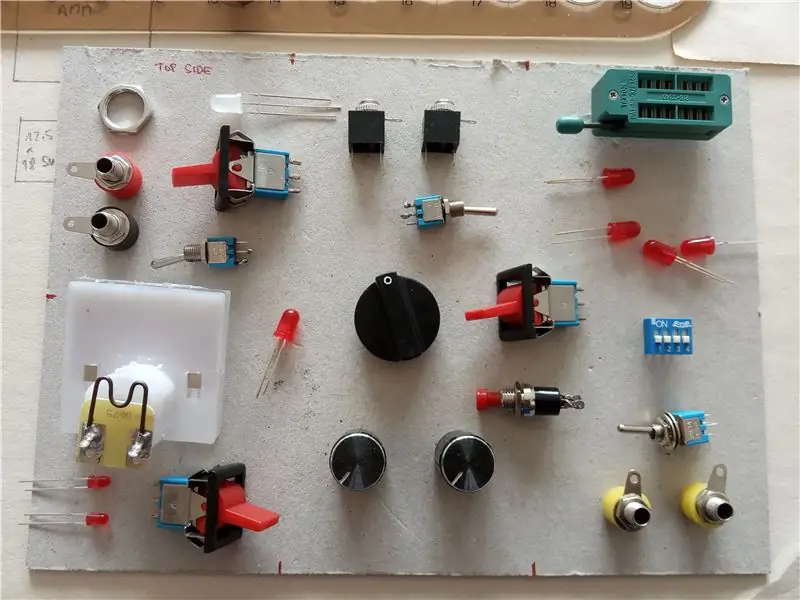
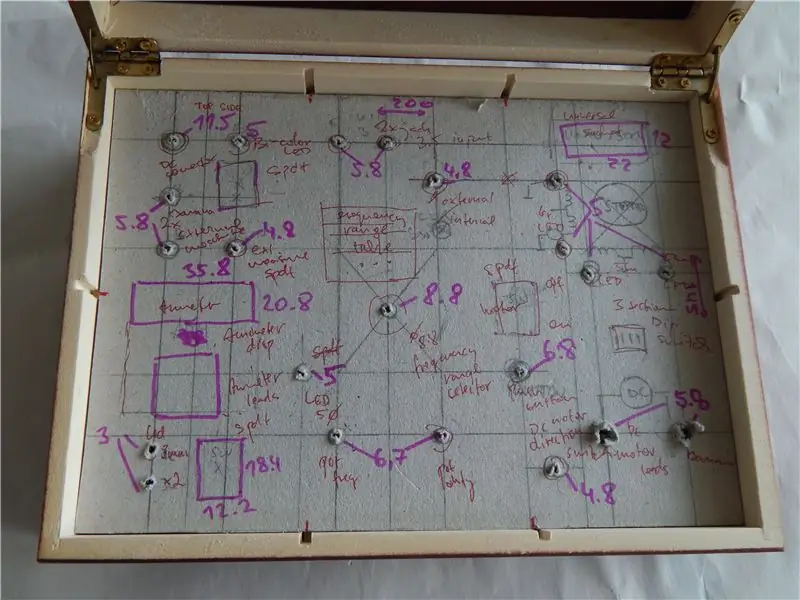
Il tester è stato collocato in una vecchia scatola da tè in legno. Prima ho misurato le dimensioni interne e poi ho ritagliato un rettangolo di cartone rigido, che serviva da sagoma per il posizionamento dei componenti. Quando ero soddisfatto del posizionamento delle parti, ho misurato nuovamente ogni posizione e ho creato un design del pannello in Fusion360. Ho diviso il pannello in 3 parti più piccole, per semplicità nella stampa 3D. Ho anche disegnato un supporto a forma di L per fissare i pannelli ai lati interni della scatola.
Passaggio 6: stampa 3D e verniciatura a spruzzo
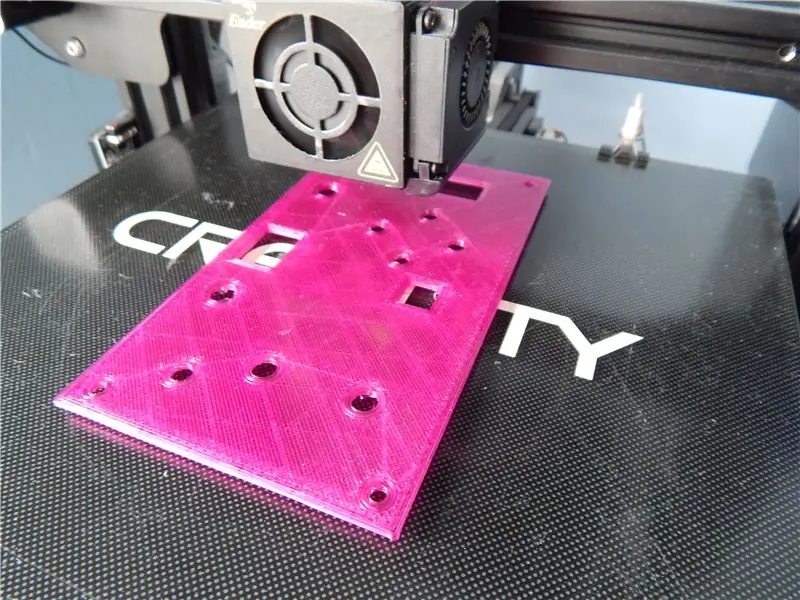
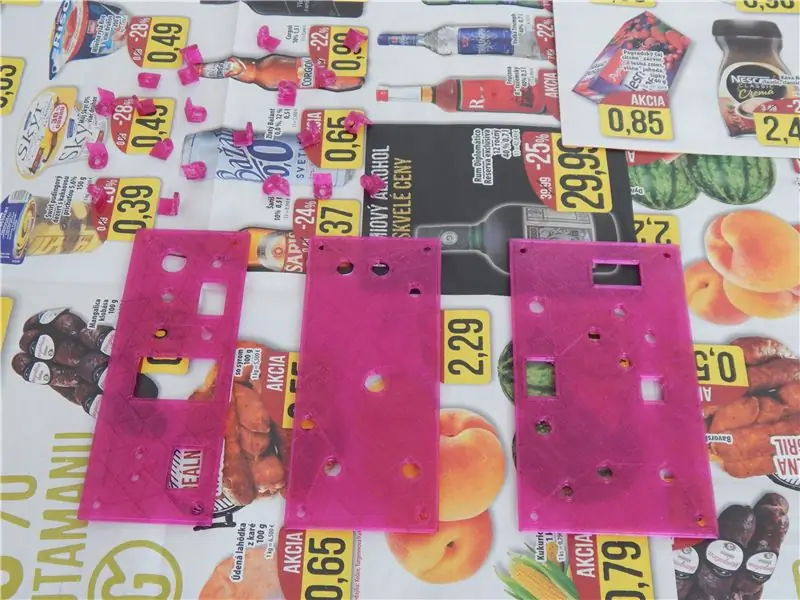
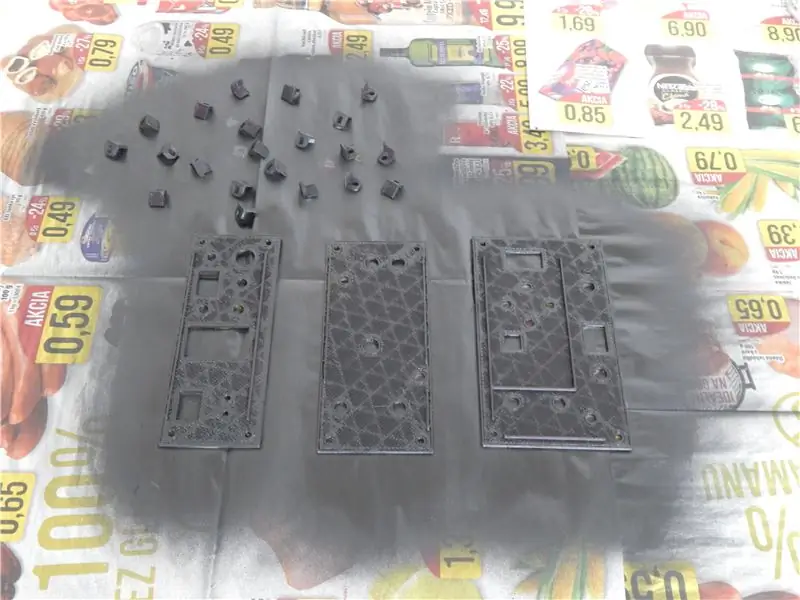
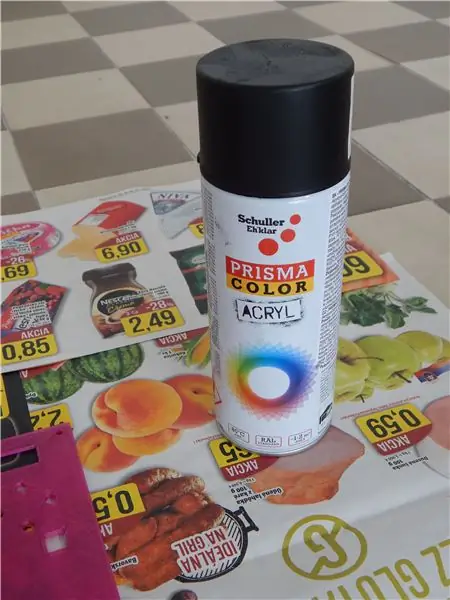
I pannelli sono stati stampati utilizzando una stampante Ender-3, dal materiale residuo che avevo in casa. Era un petg rosa trasparente. Dopo la stampa, ho spruzzato i pannelli e i supporti con vernice acrilica nera opaca. Per una copertura completa, ho applicato 3 mani, le ho stese all'esterno per qualche ora ad asciugare e ventilare per circa mezza giornata. Fai attenzione, i fumi di vernice possono essere dannosi. Usali sempre solo in una stanza ventilata.
Passaggio 7: cablaggio del pannello
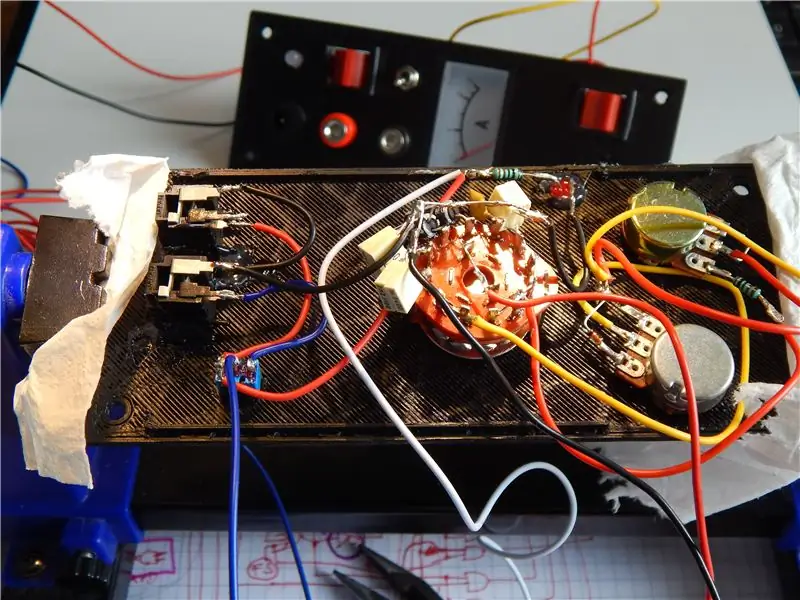
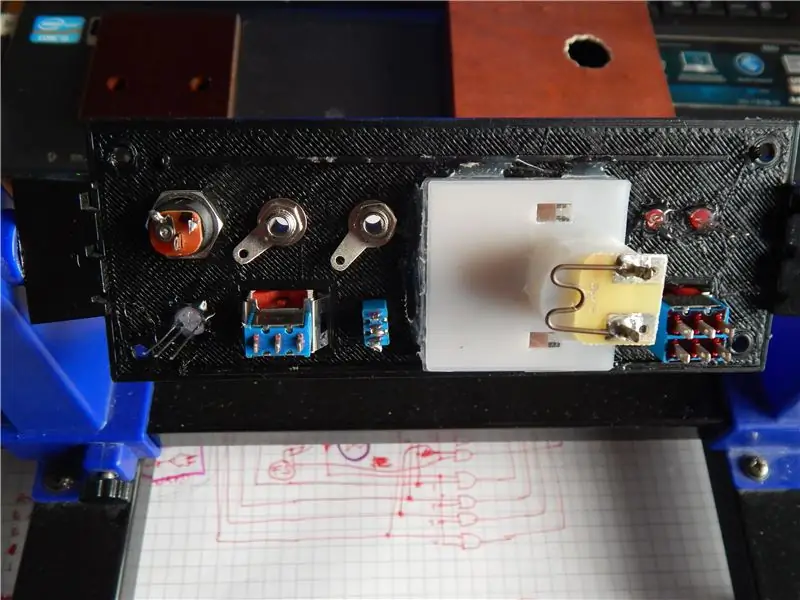
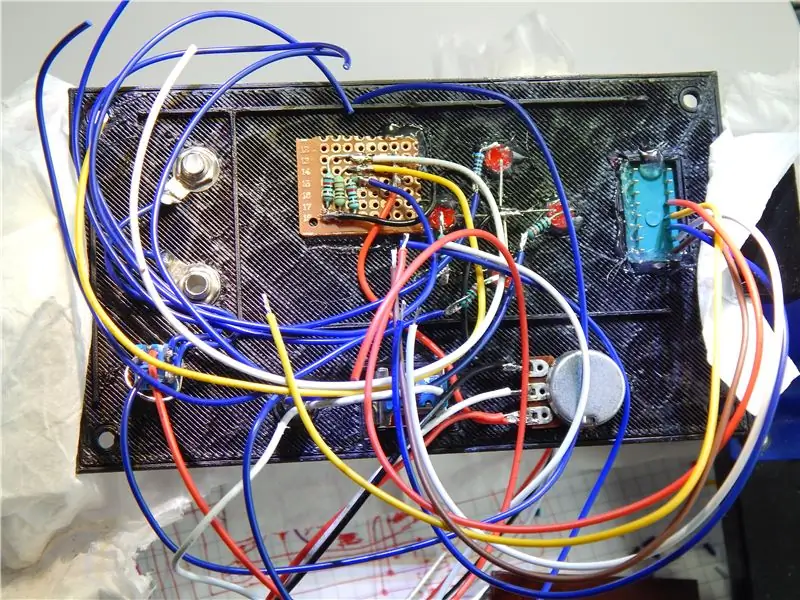
Personalmente, la parte che preferisco, ma che richiede più tempo (mi scuso in anticipo per non aver usato i tubi termoretraibili, ero in una crisi di tempo - altrimenti li userei sicuramente).
Le staffe regolabili aiutano molto durante il montaggio e la movimentazione dei pannelli. È anche possibile usare la cosiddetta terza mano, ma io preferisco il supporto. Ho coperto le sue maniglie con un panno in tessuto in modo che il pannello non si graffiasse durante il lavoro.
Ho inserito e avvitato tutti gli interruttori e potenziometri, LED e altri connettori nel pannello. Successivamente ho stimato la lunghezza dei fili che collegheranno i componenti sul pannello e anche quelli che serviranno per il collegamento al pcb. Questi tendono ad essere un po' più lunghi ed è bene estenderli un po'.
Io uso quasi sempre il flusso di saldatura liquido durante la saldatura dei connettori. Ne applico una piccola quantità sul perno e poi lo stagno e lo collego al filo. Flux rimuove qualsiasi metallo ossidato dalle superfici, rendendo molto più facile la saldatura del giunto.
Passaggio 8: connettori pannello-scheda
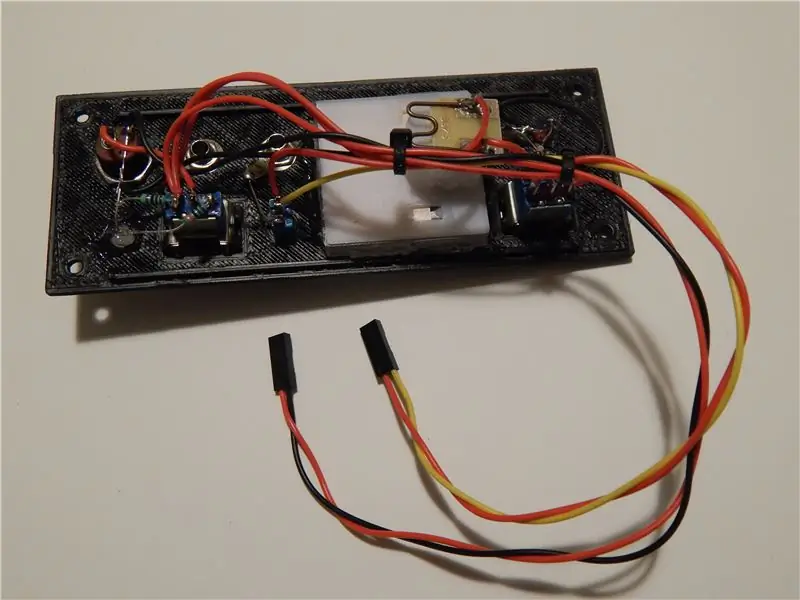
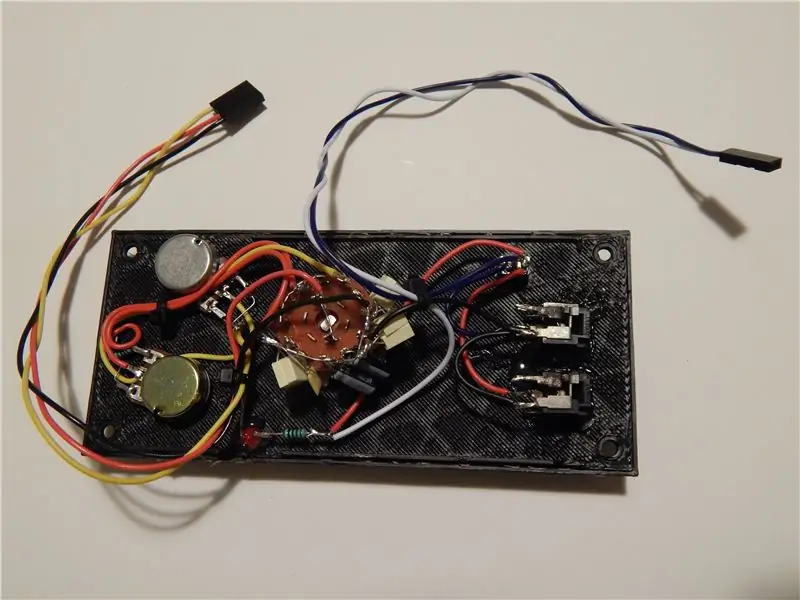
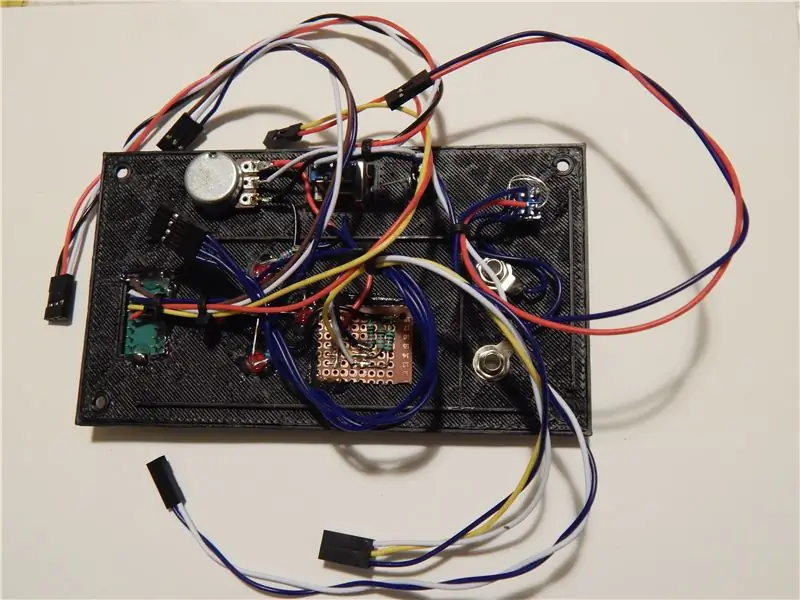
Per collegare il pannello al pcb, ho usato connettori di tipo dupont. Sono ampiamente disponibili, economici e, soprattutto, abbastanza piccoli da stare comodamente nella scatola scelta. I cavi sono disposti secondo lo schema, a coppie, triplette o quadruple. Sono codificati a colori per essere facilmente identificati e facili da collegare. Allo stesso tempo, è pratico per il futuro non perdersi in un groviglio uniforme di fili. Infine, sono fissati meccanicamente con fascette in plastica.
Passaggio 9: PCB
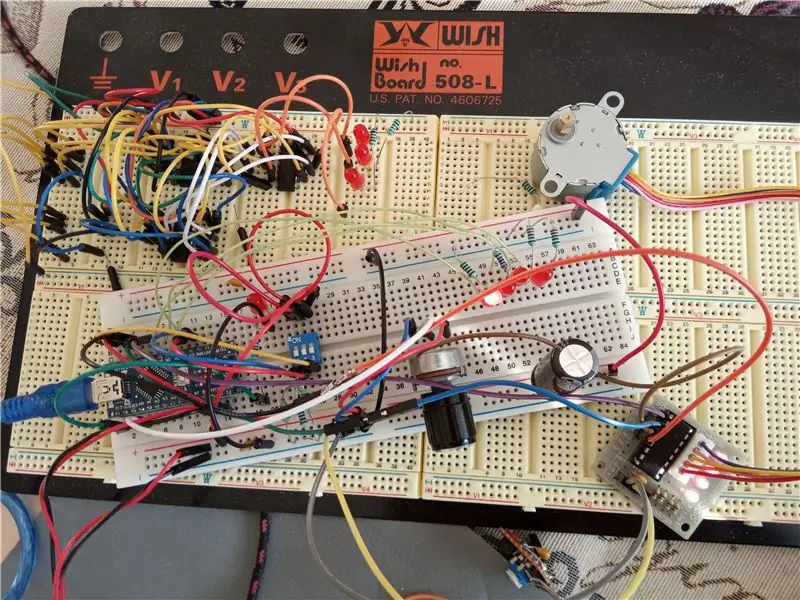
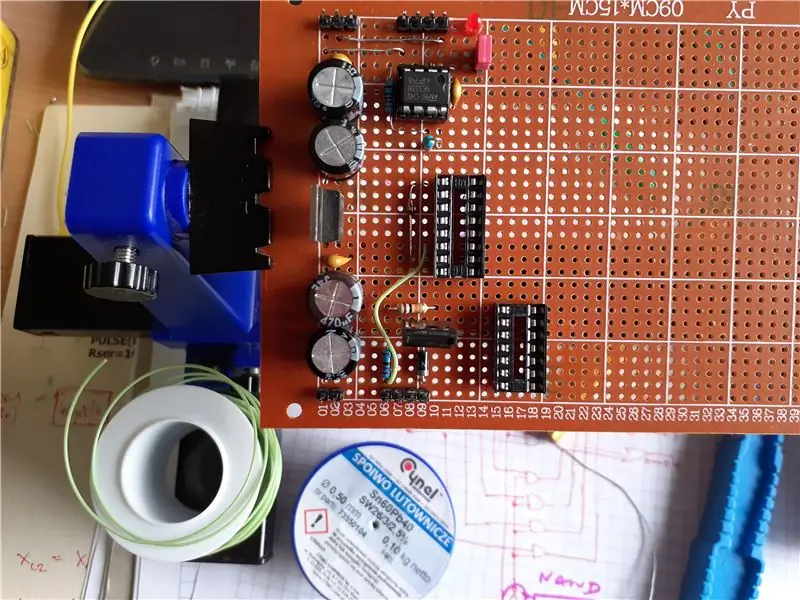
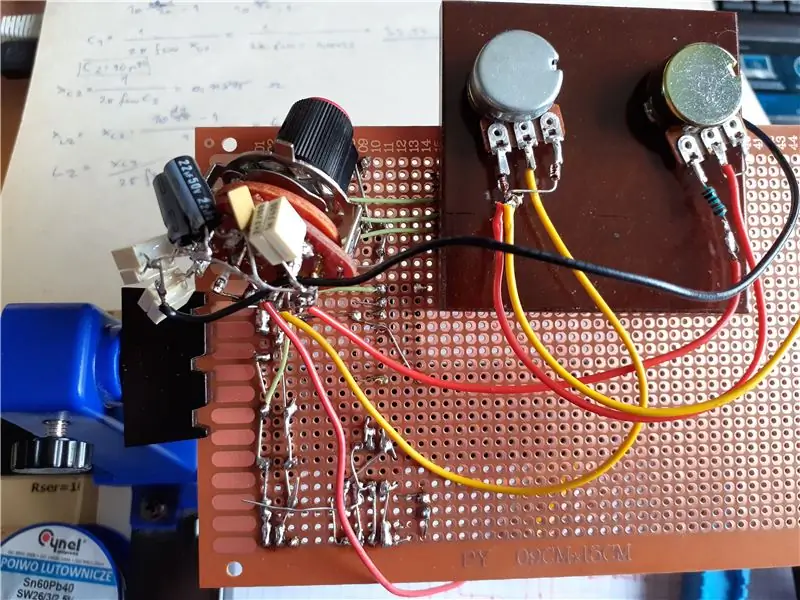
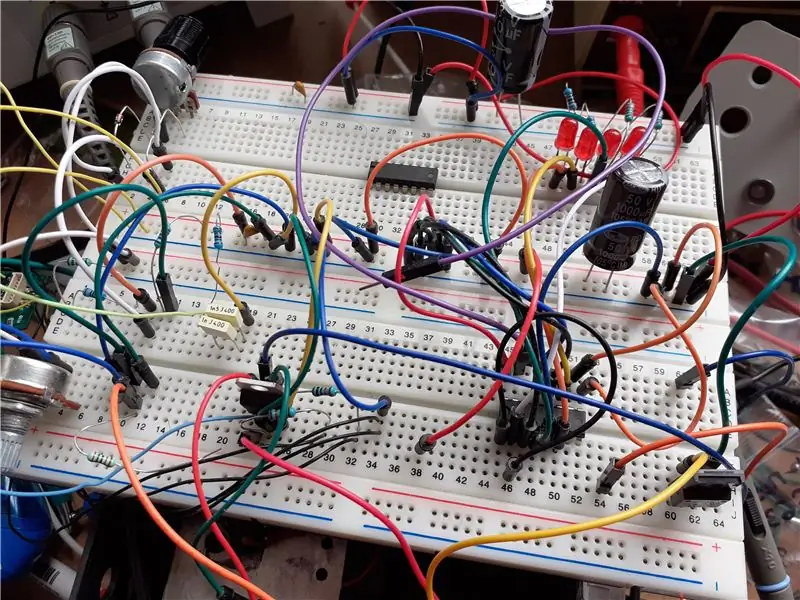
Siccome la parte dello schema che si trova all'esterno del pannello non è ampia, ho deciso di realizzare un circuito su un pcb universale. Ho usato un normale pcb 9x15 cm. Ho posizionato i condensatori di ingresso insieme al regolatore lineare e al dissipatore di calore sul lato sinistro. Successivamente, ho installato i socket per IC 555, contatore 4017 e driver ULN2003. La presa per il contatore 4017 rimarrà vuota poiché la sua funzione viene rilevata da arduino. Nella parte inferiore è presente un driver per il mosfet a canale N F630.
Passaggio 10: Arduino
Il collegamento del sistema con arduino è documentato nel foglio degli schemi nr. 4. è stata utilizzata la seguente disposizione dei perni:
- 3 ingressi digitali per DIP switch - D2, D3, D12
- 4 uscite digitali per indicatori LED - D4, D5, D6, D7
- 4 uscite digitali per driver passo-passo - D8, D9, D10, D11
- Un ingresso analogico per potenziometro - A0
Gli indicatori LED che rappresentano i singoli avvolgimenti del motore, si accendono lentamente rispetto a quando gli avvolgimenti sono effettivamente alimentati. Se la velocità di lampeggio dei led corrispondesse agli avvolgimenti del motore, la vedremmo come un'illuminazione continua di tutti loro. Volevo ottenere una rappresentazione chiara e semplice e le differenze tra le singole modalità. Pertanto, gli indicatori LED sono controllati in modo indipendente a intervalli di 400 ms.
Le funzioni per il controllo del motore passo-passo sono state create dall'autore Cornelius sul suo blog.
Step 11: Assemblaggio e Collaudo
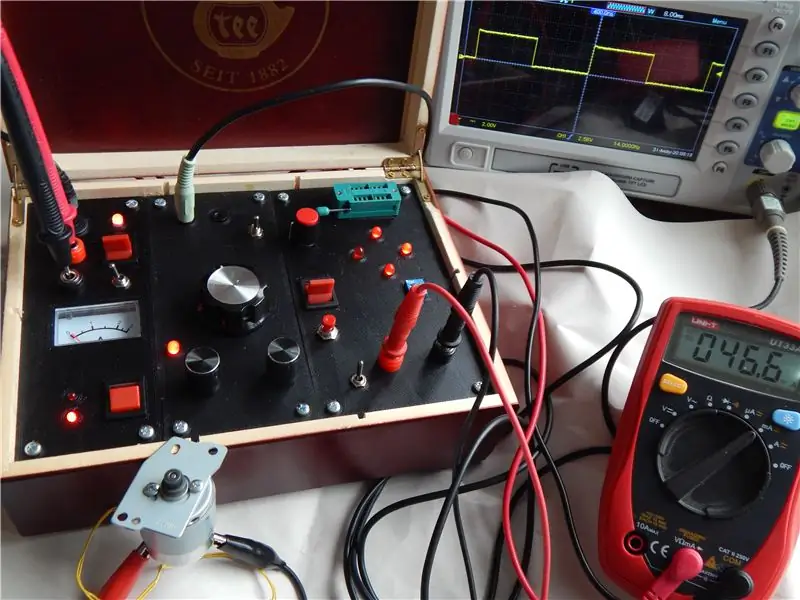
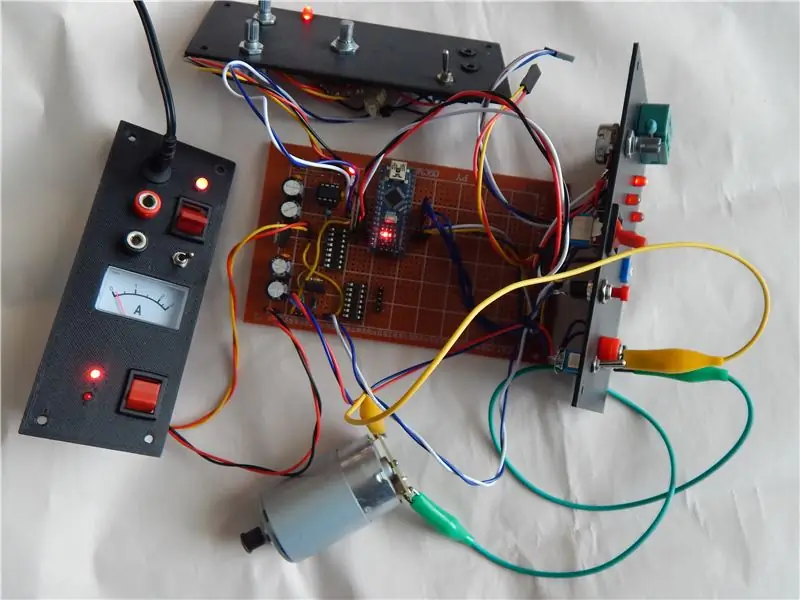
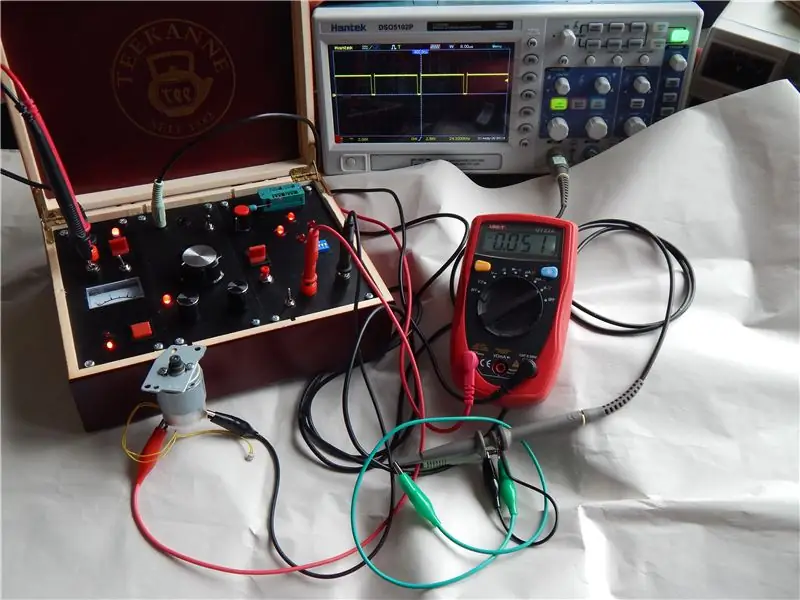
Infine, ho collegato tutti i pannelli al pcb e ho iniziato a testare il tester. Ho misurato l'oscillatore e le sue gamme con un oscilloscopio, nonché il controllo della frequenza e del ciclo di lavoro. Non ho avuto grossi problemi, l'unica modifica che ho fatto è stata aggiungere condensatori ceramici in parallelo ai condensatori elettrolitici di ingresso. Il condensatore aggiunto fornisce l'attenuazione delle interferenze ad alta frequenza introdotte nel sistema da elementi parassiti del cavo adattatore CC. Tutte le funzioni del tester funzionano come richiesto.
Passaggio 12: conclusione
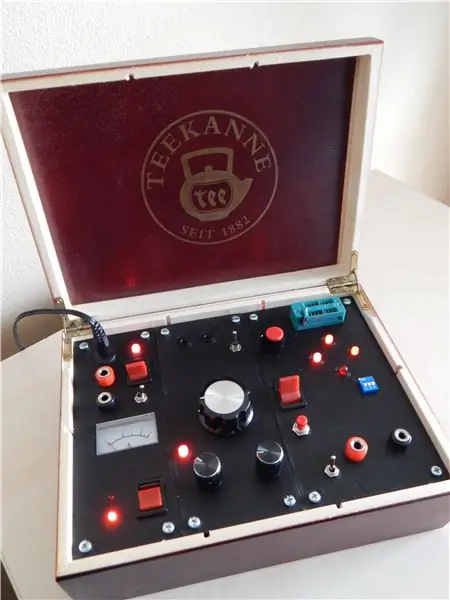
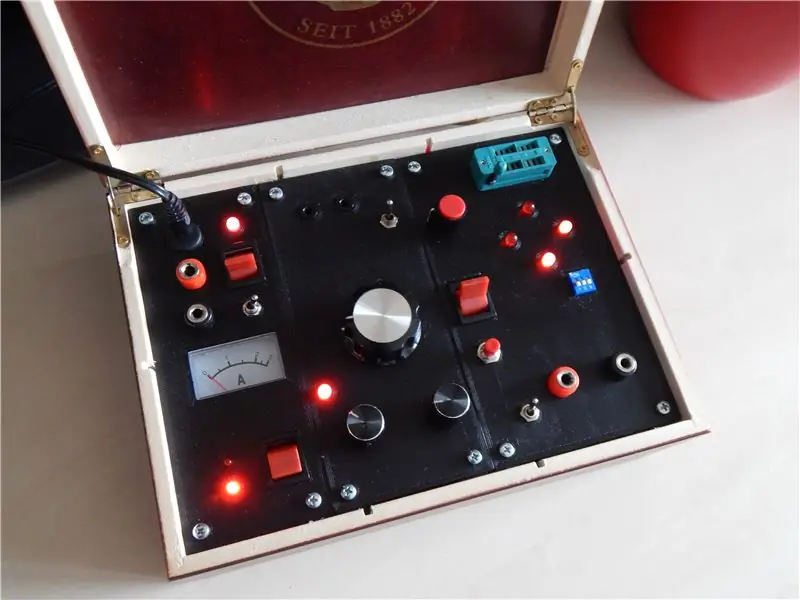
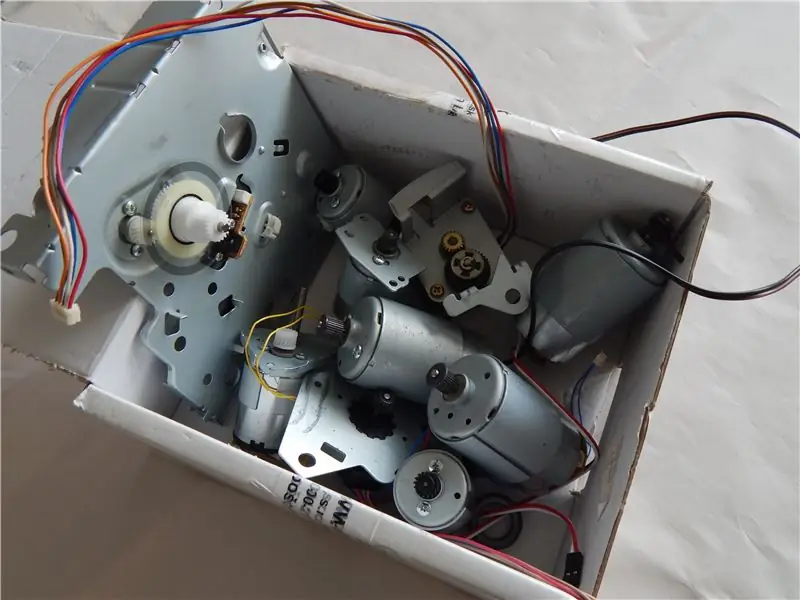
Ora posso finalmente semplicemente testare tutti i motori che sono riuscito a salvare nel corso degli anni.
Se sei interessato alla teoria, allo schema o a qualsiasi cosa sul tester, non esitare a contattarmi.
Grazie per la lettura e il tuo tempo. Rimani sano e al sicuro.
Consigliato:
Fai da te un giradischi con due motori: 10 passaggi (con immagini)
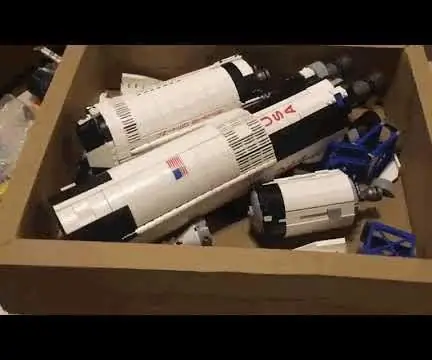
Fai da te un giradischi con due motori: all'inizio, voglio sempre avere un giradischi da tiro, e recentemente ho scoperto che c'erano due motoriduttori inattivi. Quindi, mi chiedevo se potevo fare un giradischi con loro. Senza ulteriori indugi, ci proverò! Principio: la riduzione r
Tester di compressione per motori rotativi fai-da-te TR-01: 6 passaggi (con immagini)
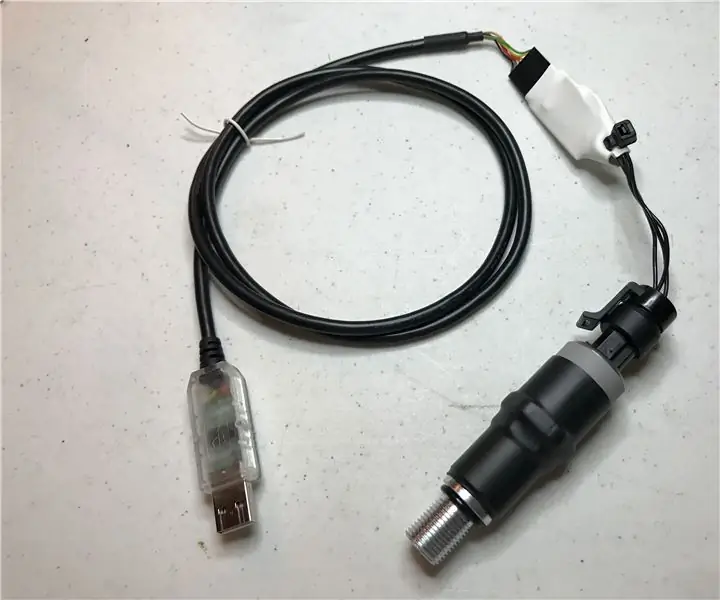
Tester di compressione per motori rotativi fai-da-te TR-01: a partire dal 2009, l'originale TR-01 v1.0, v2.0 e v2.0 Baro di TwistedRotors ha fissato lo standard per i tester di compressione per motori rotativi portatili, digitali. E ora puoi costruirne uno tuo! Per il 2017, in onore del 50° anniversario di Mazda Rotary E
Controllo di motori CC con Arduino e L293: 5 passaggi (con immagini)
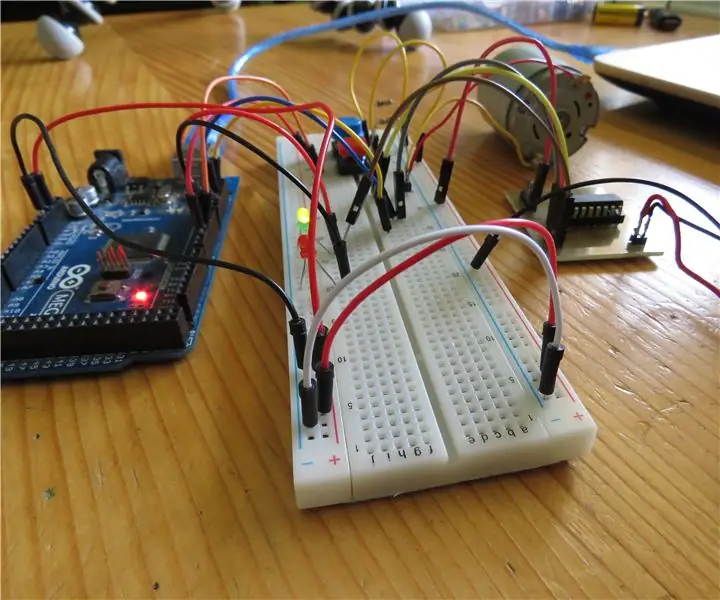
Controllo di motori CC con Arduino e L293: un modo semplice per controllare i motori CC. Tutto ciò di cui hai bisogno è conoscenza di elettronica e programmazione Se hai domande o problemi puoi contattarmi sulla mia mail: [email protected] Visita il mio canale youtube: https ://www.youtube.com/channel/UCuS39O01OyP
Nozioni di base sui motori - Concetto Super facile da capire con un esperimento: 7 passaggi (con immagini)
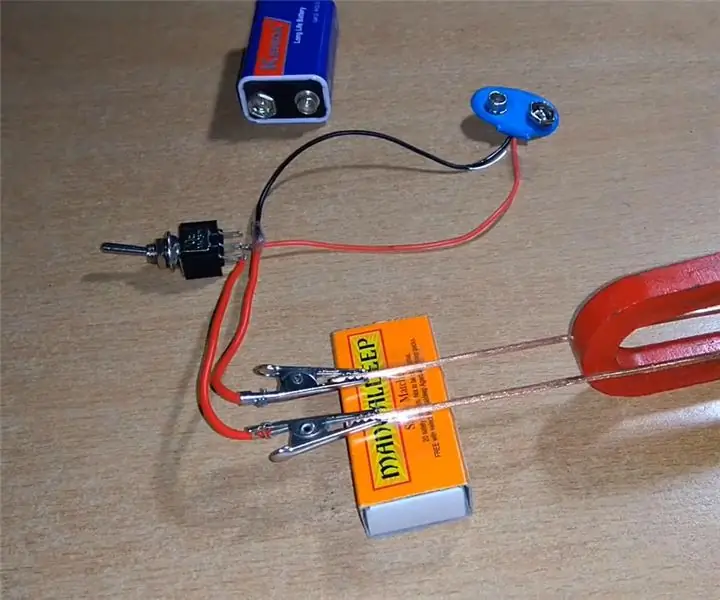
Nozioni di base sui motori | Concetto Super facile da capire con un esperimento: in questo tutorial ti insegnerò il principio fondamentale alla base dei motori. Tutti i motori intorno a noi lavorano su questo principio. Anche i generatori lavorano sulla dichiarazione reciproca di questa regola. Sto parlando del Fleming's Left-Hand Ru
Cosa fare con le collezioni di motori casuali: Progetto 2: Luci rotanti (modello UFO): 12 passaggi (con immagini)
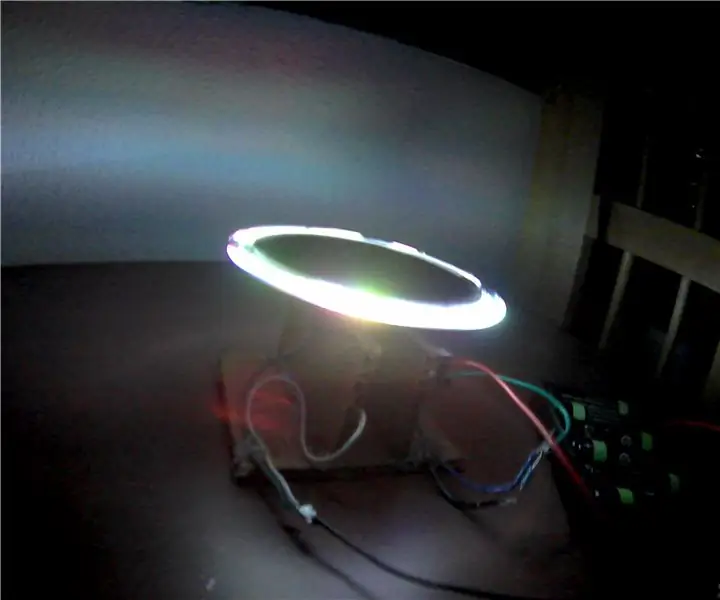
Cosa fare con le collezioni di motori casuali: Progetto 2: Luci rotanti (modello UFO): Quindi, ho ancora una collezione di motori casuali… Cosa farò? Bene, pensiamo. Che ne dici di uno spinner con luce a LED? (Non a mano, scusate gli amanti del fidget spinner.) Sembra un po' un UFO, suona come un mix tra uno spaccaerba e un frullatore