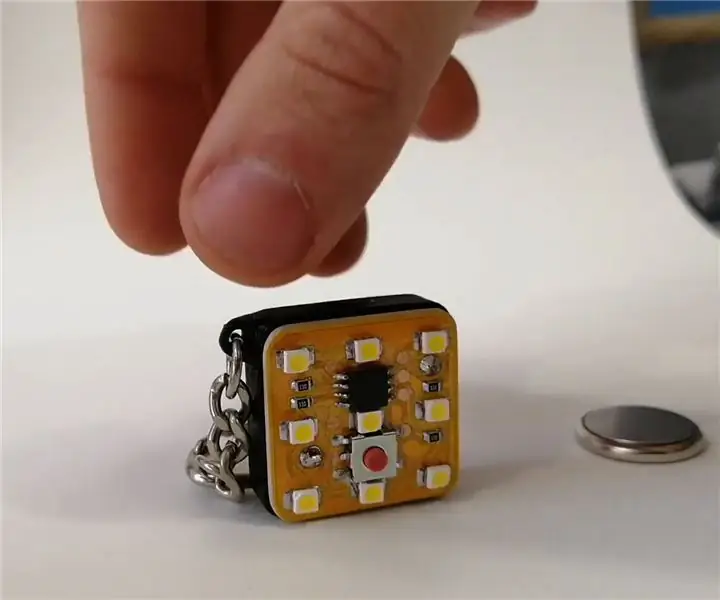
Sommario:
- Passaggio 1: materiali, forniture e strumenti
- Passaggio 2: prepara tutti gli adesivi
- Passaggio 3: incidere il rivestimento di rame
- Passaggio 4: tagliare e carteggiare i dadi
- Passaggio 5: applicazione degli adesivi Kapton Soldermask
- Passaggio 6: assemblare i dadi: applicare la pasta saldante
- Step 7: Popolazione e saldatura a riflusso
- Passaggio 8: stampa 3D delle custodie per portachiavi
- Passaggio 9: crea una maschera di programmazione
- Passaggio 10: programmazione dei dadi
2025 Autore: John Day | [email protected]. Ultima modifica: 2025-01-23 14:49
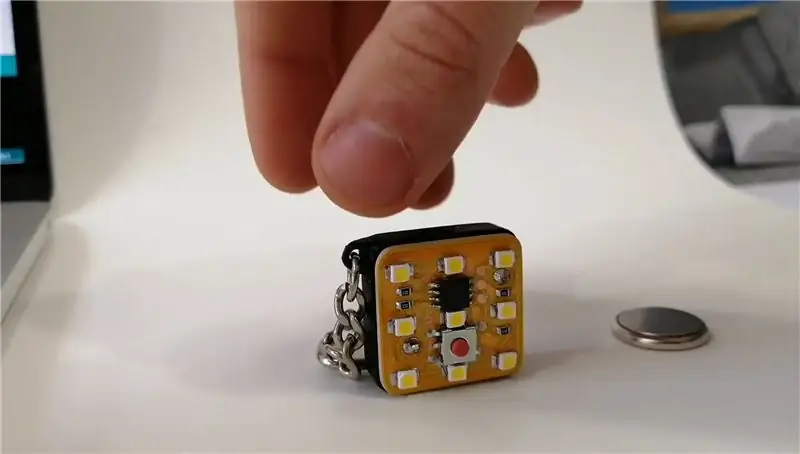
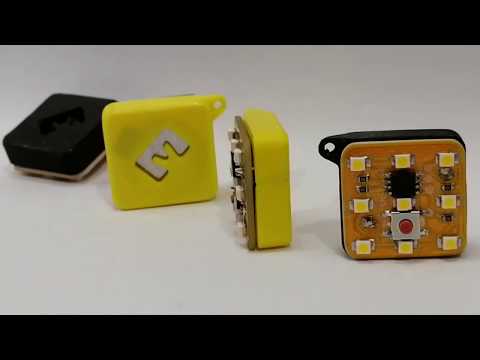
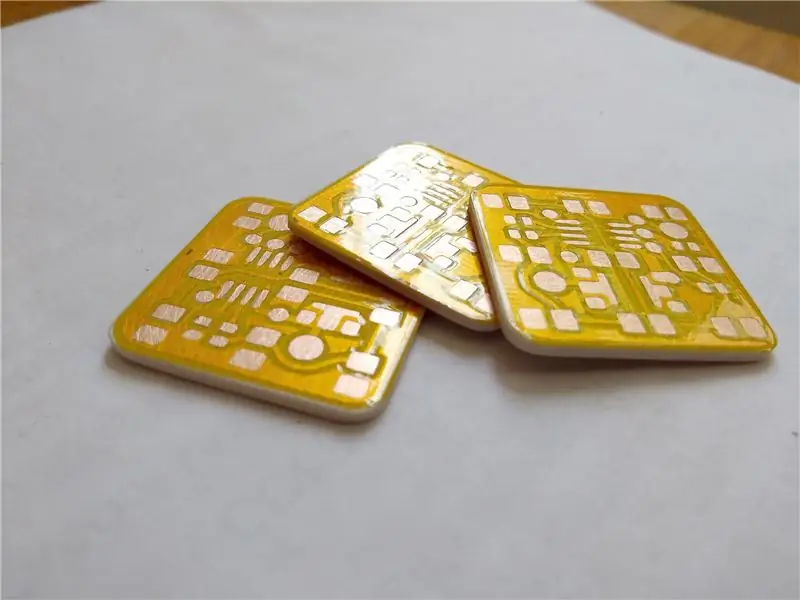
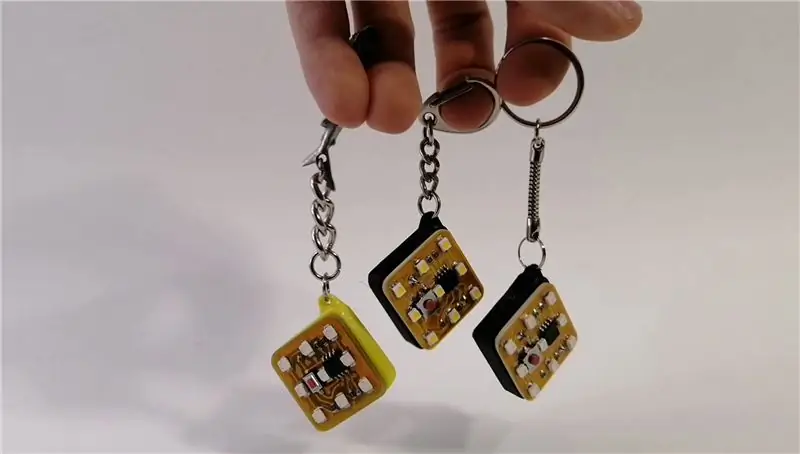
Questo tutorial consiste in una guida passo passo che documenta un metodo per produrre PCB di qualità professionale a casa attraverso l'uso di un cutter per vinile, in modo affidabile, semplice ed efficiente. Questo metodo consente la produzione di PCB coerenti e di alta qualità a casa con pochi materiali comuni e in un lasso di tempo molto breve. Con tutti i file pronti, l'intero processo può essere completato in poche ore.
Oggetto della guida, tinyDice:
Ai fini di questa guida verrà illustrato il processo con la produzione di un batch di 3 tinyDice, un die elettronico basato sul microcontrollore atTiny85 con software charlieplexing, che consente il controllo di 9 LED con soli 4 pin e 4 resistori. È una versione migliorata del mio tinyDice originale (2014) e tutti i file sorgente richiesti per questo Instructable sono disponibili per il download come pacchetto compresso nella fase dei materiali di consumo.
Origine del metodo:
Come appassionato di elettronica, ho avuto la mia giusta dose di esperienza con la realizzazione di PCB in passato, ma la maggior parte dei metodi domestici sono eccessivamente inaffidabili, come il metodo di trasferimento del toner, o eccessivamente complessi e laboriosi, come il metodo del router CNC o l'UV photoresist (che ho trattato in passato sull'originale tinyDice). Inoltre, la qualità finale dei prodotti tende ad essere piuttosto scarsa, soprattutto se si tenta di implementare maschere di saldatura UV.
Da queste esperienze insoddisfacenti, ho deciso di esplorare metodi alternativi per creare PCB a casa. Dato che di recente ho iniziato a sperimentare con una taglierina per vinile desktop, mi è venuto in mente che un timbro in vinile potrebbe creare una maschera eccellente e affidabile per l'incisione del PCB. Durante la ricerca online iniziale, non ho trovato alcun riferimento a persone che utilizzano timbri in vinile per realizzare PCB, il che mi ha sorpreso in quanto sembra molto plausibile. Questo mi ha motivato a sperimentare il processo e scoprire se poteva funzionare in modo affidabile ed efficiente per trasferire tracce PCB dal computer al rame.
Sviluppo dei processi:
Fare tracce di rame pulite e coerenti in un PCB domestico è di per sé un risultato, ma affinché i PCB funzionino correttamente e durino a lungo, richiedono una sorta di soldermask, che prevenga ponti di saldatura indesiderati e protegga le tracce di rame dalla corrosione. Tradizionalmente, la maschera di saldatura utilizzata è sotto forma di una resina polimerizzabile ai raggi UV, che in pratica è piuttosto difficile da lavorare.
Inizialmente, intendevo usare indirettamente i malati di vinile come maschera per la polimerizzazione del soldermask UV. Tuttavia, in diversi tentativi, non sono riuscito a far polimerizzare in modo affidabile il soldermask UV solo nei punti previsti e non sono mai stato in grado di creare uno strato sufficientemente sottile e uniforme, che alla fine ha provocato un mucchio di schede rovinate. Così ho scartato quell'idea e mi è venuto in mente che forse una sorta di timbro potrebbe anche essere usato direttamente come soldermask, anche se certamente non potrebbe essere vinile, in quanto non resisterebbe al calore della saldatura a riflusso.
Con questo in mente ho guardato al nastro Kapton, che è autoadesivo, sottile e promette di resistere a temperature abbastanza elevate per la saldatura. Il nastro Kapton viene venduto in rotoli, ma mi è venuto in mente che se fosse applicato sul supporto del vinile convenzionale, potrebbe essere tagliato direttamente sulla taglierina e utilizzato direttamente come timbro. Fin dalla prima prova di questo, era evidente che il nastro Kapton si comportava in modo abbastanza promettente sul plotter da taglio, anche se tutti i tagli che passavano su minuscole bolle erano frastagliati o incompleti, quindi la chiave per perfetti timbri in kapton stava applicando perfettamente il nastro sul supporto in vinile senza che l'aria rimanga intrappolata al di sotto. Questo inizialmente si è rivelato piuttosto complicato, poiché Kapton è eccessivamente sottile e appiccicoso, ma dopo aver provato a stenderlo usando una normale carta di plastica mi sono reso conto che poteva essere fatto perfettamente e facilmente in questo modo.
Attraverso queste prove iterative ho anche osservato alcuni dei limiti pratici del processo, che hanno spesso a che fare con il fatto che la maschera di rame è originariamente un timbro. Queste limitazioni si sono evolute in una serie di linee guida di progettazione per rendere affidabile questo processo.
Passaggio 1: materiali, forniture e strumenti
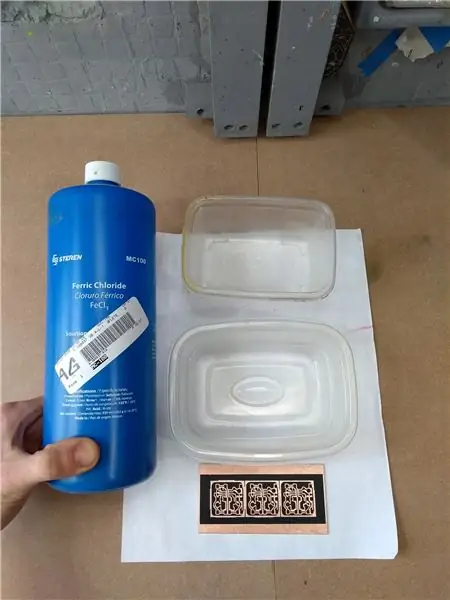
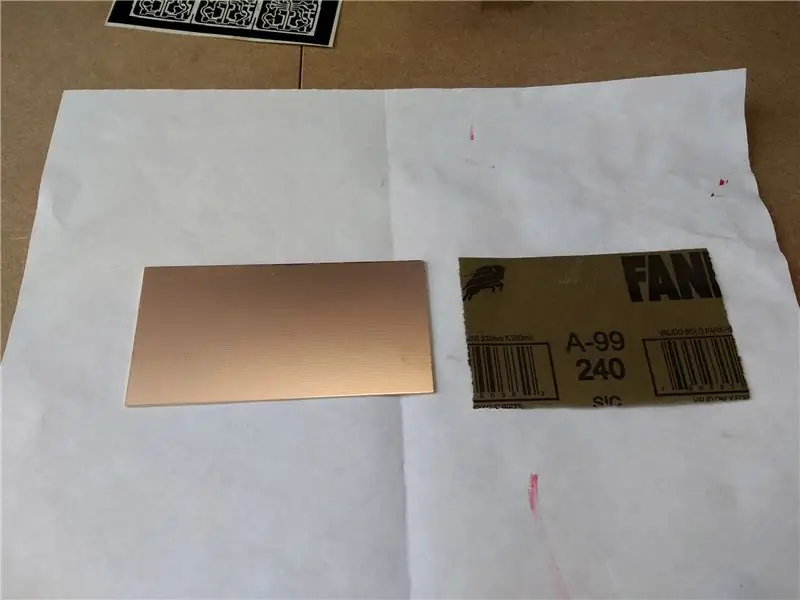
Materiali:
- PCB vuoto da 5 x 10 cm
- Vinile autoadesivo 10 x 15 cm
- Nastro Kapton largo 50 mm
- Pellicola di trasferimento in vinile 10 x 15 cm
Forniture:
- Mordenzante cloruro ferrico
- Alcool isopropilico
- Pasta per saldature
- Filamento PETG (per la custodia del portachiavi)
Utensili:
- taglierina per vinile desktop (uso Silhouette Cameo 3, ma qualsiasi macchina di base funzionerà)
- Stazione di rilavorazione ad aria calda (non indispensabile ma utile)
- saldatore
- carta di plastica (vecchio documento d'identità o di qualsiasi tipo)
- USBtinyISP o Arduino come ISP
- taglierina acrilica manuale (può essere fatta in casa da una sezione della vecchia lama del seghetto)
- Carta vetrata grana 220 e 400
- Stampante 3D (opzionale, solo per realizzare la custodia del portachiavi)
Software:
- Silhouette Studio (o equivalente per altre marche di taglia vinile)
- EAGLE CAD (non richiesto se non si intende modificare il disegno)
- Photoshop o qualsiasi editor di immagini (non richiesto se non si intende modificare il design)
- Arduino IDE + atTinyCore
- AVRDUDESS
- Slic3r o qualsiasi altro software di stampa 3D.
-
pacchetto di risorse tinyDice, (disponibile per il download in questo passaggio come file RAR)
Componenti:
per ogni tinyDice85:
- 9x 3528 LED SMD (qualsiasi colore, consigliato lo stesso)
- 1x attiny85 (SOIC)
- 4x 33 ohm 0805 resistori (il valore esatto non è critico, usa un valore simile ma lo stesso!)
- 1x pulsante SMD
- 1x clip per batteria CR20XX
- 1x batteria CR2032
Per la maschera di programmazione:
- 6x perni pogo
- 1x intestazione maschio 2x3 (per ISP)
- 1x header maschio 2x1 (per sorgente VCC esterna)
- 1x regolatore LDO AMS1117 3.3v (SOT-23)
Passaggio 2: prepara tutti gli adesivi
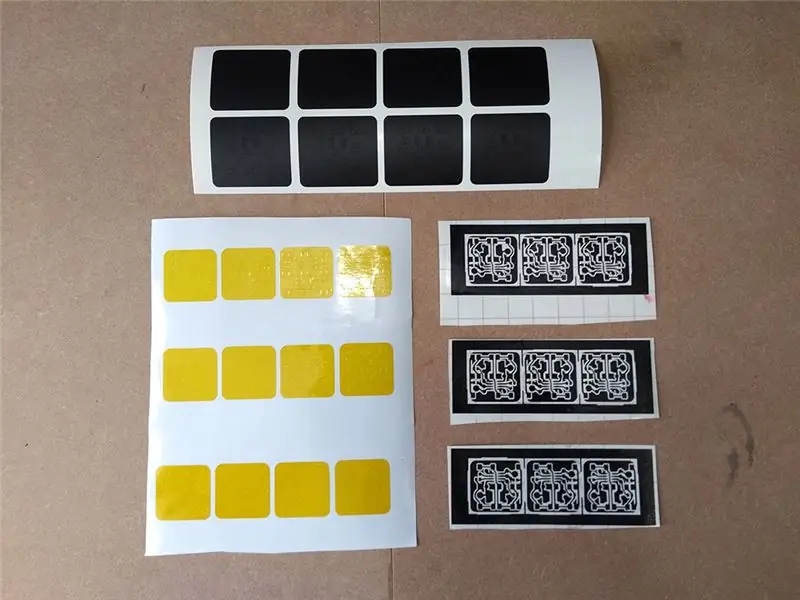
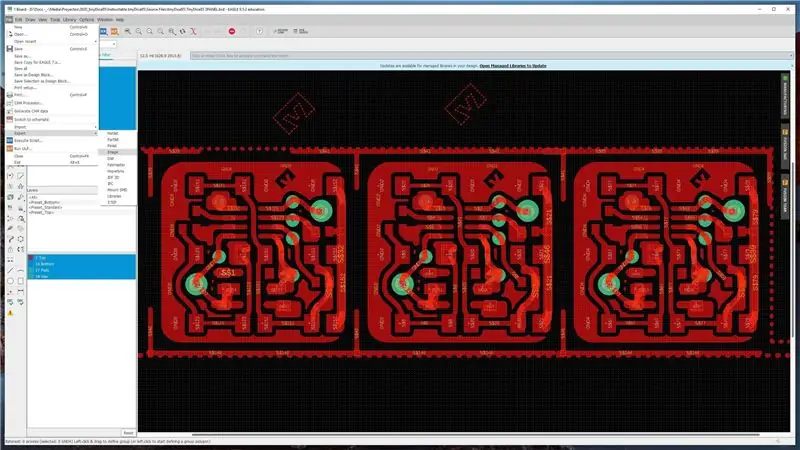
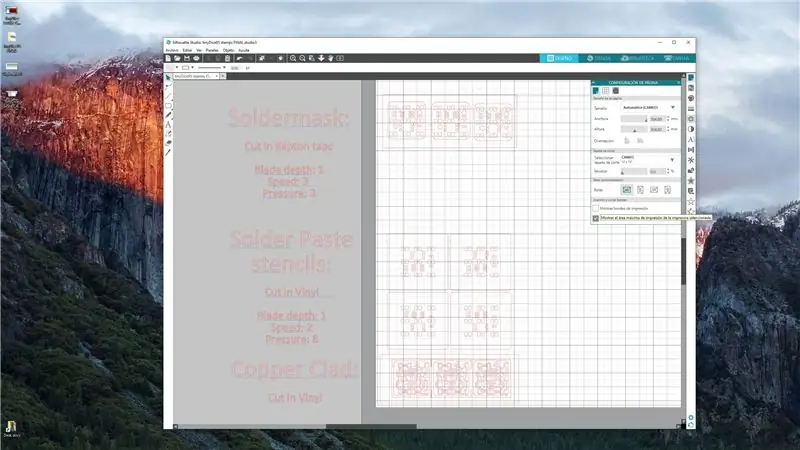
Per questo processo di creazione di PCB a casa, gli adesivi sono coinvolti in tre fasi; Come maschera per incidere il rivestimento in rame, come maschera per saldatura per proteggere le tracce e vincolare la saldatura e come stencil per applicare pasta saldante sui pad. Al fine di ottimizzare il più possibile il processo, tutti gli adesivi possono essere preparati in un'unica seduta.
Preparazione dei file per il taglio:
Se non hai intenzione di modificare il design, puoi utilizzare direttamente le immagini preparate o il file Silhouette Studio con tutti gli adesivi. Se utilizzi un altro disegno, procedi come segue per preparare il file per il taglio:
Poiché la maggior parte dei software gratuiti per la taglierina del vinile funziona con le immagini, dobbiamo esportare il design da EAGLE come immagine ad alta risoluzione. Per questo, prima nascondi tutto il livello tranne TOP e VIAS, quindi esporta il pannello come immagine in MONOCHROME e almeno 1500 dpi. Quindi, ripeti il processo ma solo con il livello Tstop, in modo da ottenere solo i pad.
Una volta esportate le immagini, è consigliabile fare un po' di pulizia in Photoshop per aumentare l'affidabilità del processo. Per l'immagine rivestita di rame, questo consiste nel cancellare eventuali piccole aree di rame isolate o collegarle ad aree più grandi, cancellare il centro di tutti i fori passanti e aumentare lo spazio intorno alle termiche. Per l'immagine dei cuscinetti, è necessario inserirli su una forma nera che trabocchi un po' dall'intero rivestimento di rame.
Quindi, importa le immagini nel software della taglierina per vinile, tracciale e ridimensionale a una dimensione di 100 x 100 mm. Un vantaggio della pannellizzazione dei PCB è che si dispone di un riferimento coerente per ridimensionarli correttamente indipendentemente dalla risoluzione.
Preparazione del nastro Kapton per il taglio:
Il nastro Kapton è un ottimo materiale, tuttavia per poterlo utilizzare come adesivo dobbiamo prima posizionarlo su un supporto piatto. Per questo utilizzeremo il supporto del nastro di trasferimento in vinile, quindi stacca il patè e mettilo temporaneamente da parte, avendo cura di tenerlo pulito. Quindi, srotolare un segmento di nastro e applicarlo con cura sul supporto di carta cerata usando una carta di plastica come spatola per assicurarsi che non rimangano bolle intrappolate sotto. Ti consiglio di preparare più di quello che ti aspetti di utilizzare, poiché alcuni adesivi potrebbero non uscire perfettamente.
Taglio degli adesivi:
Una volta che tutti gli adesivi sono stati tracciati e ridimensionati nel software della taglierina per vinile, procedere al posizionamento del materiale vinilico autoadesivo su un angolo del tappetino da taglio e posizionare il nastro Kapton su un altro angolo.
Quindi, sul software, posiziona solo i disegni dello stencil con rivestimento in rame e pasta saldante sull'area corrispondente al vinile e imposta i parametri di taglio su: Velocità 3, Profondità lama 1, Pressione 8. Invia il lavoro per il taglio e lascia che la macchina faccia è cosa.
Infine, sposta da parte i disegni utilizzati in precedenza e posiziona solo il disegno della maschera di saldatura sull'area corrispondente al nastro Kapton. Impostare i parametri di taglio su: Velocità 1, Profondità lama 1, Pressione 3. Procedere all'invio del lavoro alla macchina e una volta terminato rimuovere con cura sia il vinile autoadesivo che i materiali Kapton dal tappetino di taglio. Fare attenzione a non formare pieghe nette quando si staccano.
Eliminare gli adesivi:
Per trasferire gli adesivi in vinile sul PCB, dobbiamo utilizzare la pellicola di trasferimento in vinile per garantire che tutte le regioni vengano trasferite sul posto. Per poter trasferire solo i segmenti di timbro previsti, dobbiamo rimuovere tutte le aree indesiderate prima di applicare la pellicola di trasferimento. Per questo utilizzare un cutter e sollevare con cautela un angolo dell'area indesiderata. Spingi la taglierina sotto e premi il vinile sulla lama per farlo aderire. Quindi, tira via la taglierina e l'eccesso dovrebbe iniziare a staccarsi. A seconda del design, tutte le aree indesiderate possono risultare come un unico pezzo. Una volta diserbato, posiziona la pellicola di trasferimento SOLO sugli adesivi rivestiti in rame e scarta tutto l'eccesso. A questo punto gli adesivi in vinile sono pronti per l'uso. Gli adesivi in nastro Kapton sono un pezzo unico quindi possono essere trasferiti direttamente senza la pellicola di trasferimento.
Passaggio 3: incidere il rivestimento di rame
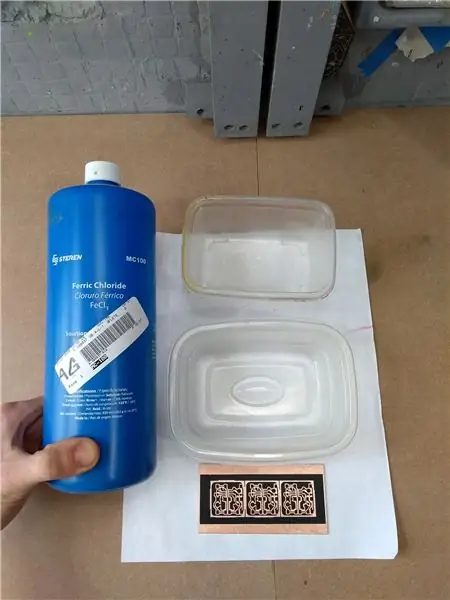
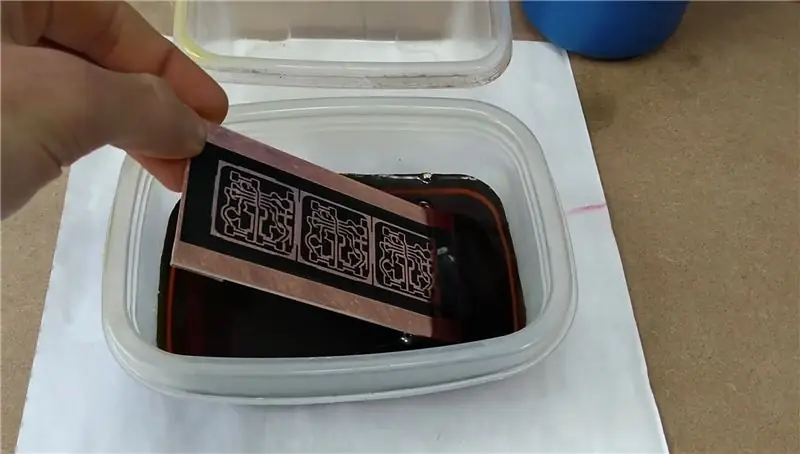
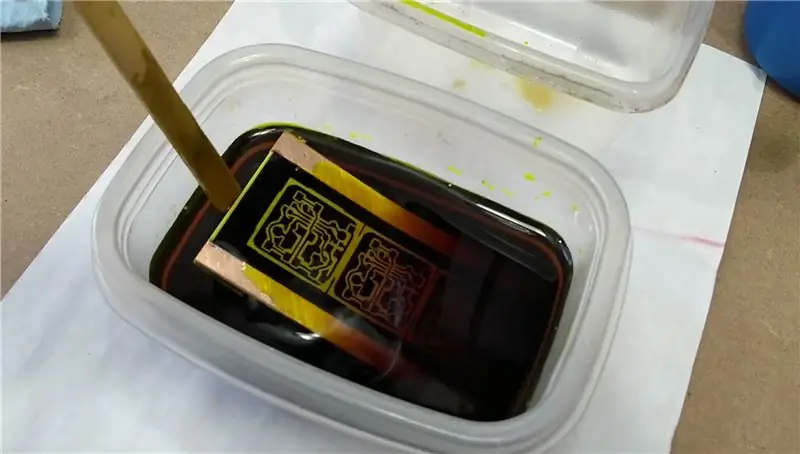
Questa è la fase più importante del processo, poiché la qualità delle tracce di rame determinerà il tasso di successo dei prodotti finali. Se fatto con attenzione può essere al 100%.
Trasferimento dell'adesivo CLAD sul rame:
Per garantire risultati puliti e affidabili, è necessario prima sgrassare il PCB vuoto con alcol isopropilico. Se il grezzo è vecchio, si consiglia di carteggiare a fondo la superficie con carta vetrata a grana 320-400 facendo piccoli cerchi su tutta la tavola.
Una volta completamente pulito, è il momento di trasferire l'adesivo sul rame. Per questo, prima stacca un angolo della pellicola di trasferimento e poi posiziona l'adesivo capovolto su un tavolo pulito. Quindi, procedi a staccare lentamente la carta dal trasferimento facendo una piega netta e tirando lungo il tavolo. In questo modo anche i piccoli tamponi dovrebbero aderire al transfer e non rimanere sulla carta. Non preoccuparti però se uno o due pad rimangono indietro, puoi posizionarli manualmente in un secondo momento.
Quindi, tieni il transfer in vinile con l'adesivo con la punta delle dita (incollali leggermente fino al bordo) e allinea lentamente l'adesivo sulla lavagna prima di appoggiarlo. Una volta allineato, appoggialo sul rame e premi leggermente con le dita DAL CENTRO FUORI, per evitare bolle intrappolate. Quindi, usa una carta di plastica per strofinare l'intera superficie per garantire che il vinile aderisca saldamente al rame. Procedi a staccare la pellicola di trasferimento in vinile dal rivestimento in rame nello stesso modo in cui hai staccato il supporto di carta e posiziona manualmente tutti i cuscinetti che sono rimasti indietro. Se l'adesivo non copre l'intero spazio vuoto, puoi coprire eventuali aree rimanenti con nastro adesivo trasparente per evitare di incidere il rame in eccesso e utilizzare eccessivamente i materiali di consumo.
Incisione del rame rivestito:
Per il processo di incisione avrai bisogno di 2 contenitori rettangolari in stile Tupperware, un bastoncino di legno e l'incisione al cloruro ferrico.
La tavola preparata con il timbro CLAD è quasi pronta per l'incisione, ma è molto importante pulirla ancora una volta con alcol isopropilico per rimuovere eventuali residui dal film di trasferimento e garantire un'incisione uniforme e completa, senza residui di rame indesiderati.
Per preparare il cloruro ferrico per l'incisione, versarlo in uno dei contenitori fino a circa metà pieno e aggiungere circa il 30% in più di acqua. A questo punto la soluzione è pronta per l'incisione, tuttavia è possibile riscaldarla facoltativamente nel forno a microonde per 15 secondi PRIMA dell'inserimento nel PCB per velocizzare il processo di incisione.
Infine, metti la tavola nel cloruro ferrico e lascia che affondi. Il processo può richiedere un po' di tempo, ma è importante tornare ogni 10-15 minuti per mescolare la soluzione e controllare i progressi. Per questo basta usare un piccolo pezzo di legno per raggiungere la tavola e inclinarla dentro e fuori dalla soluzione un paio di volte. Questo sposterà la soluzione per assicurarti che reagisca in modo uniforme e ti permetterà di vedere quanto del rame è stato rimosso. Continua a farlo finché non vedi più rame esposto, ma non lasciarlo più a lungo poiché l'agente corrosivo potrebbe iniziare a rompersi sotto l'adesivo e danneggiare le tracce. Nel frattempo, lascia il bastoncino sull'altro contenitore per evitare di macchiare qualcosa con la soluzione mordenzante, poiché è molto incline alle macchie e ha anche un odore ferroso molto forte.
Una volta fatto, rimuovere la tavola dall'acquaforte e risciacquarla abbondantemente con abbondante acqua e sapone. Dopo questo, prendi un imbuto o creane uno usando un foglio di plastica e fissalo su una bottiglia di PP vuota per recuperare e conservare l'acquaforte. NON scartare MAI il cloruro ferrico esausto attraverso lo scarico, riutilizzarlo il più possibile e gettarlo lasciandolo asciugare, quindi smaltirlo come un solido.
L'incisione è la fase che richiede più tempo del processo. Se fatto con cloruro ferrico fresco, può essere completato in meno di un'ora, tuttavia, con forniture riutilizzate possono essere necessarie fino a 4 ore per il completamento, quindi sii paziente e controlla periodicamente.
Passaggio 4: tagliare e carteggiare i dadi
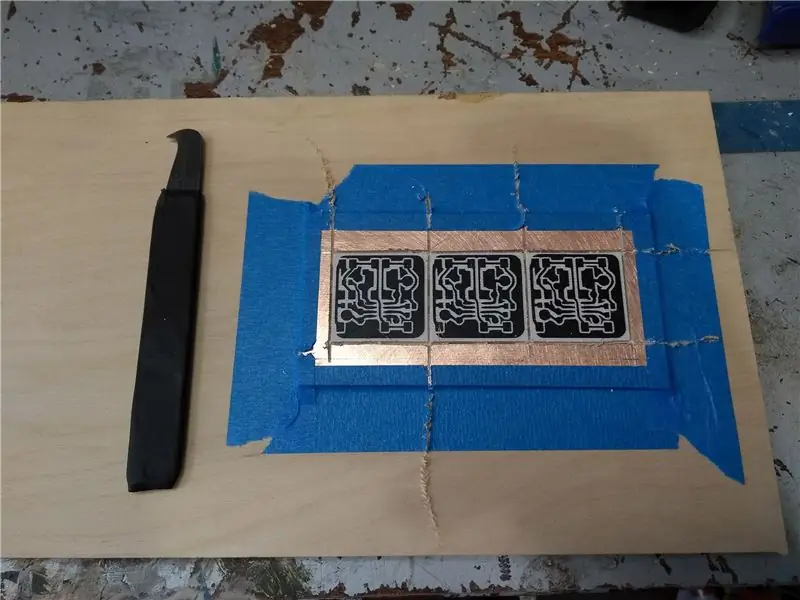
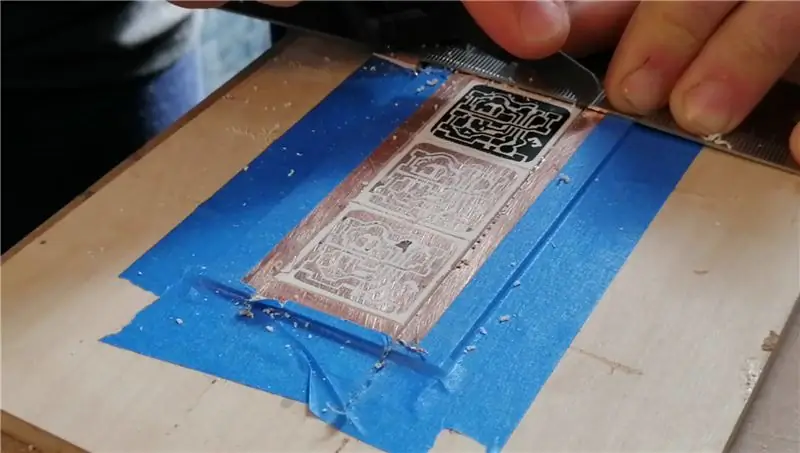
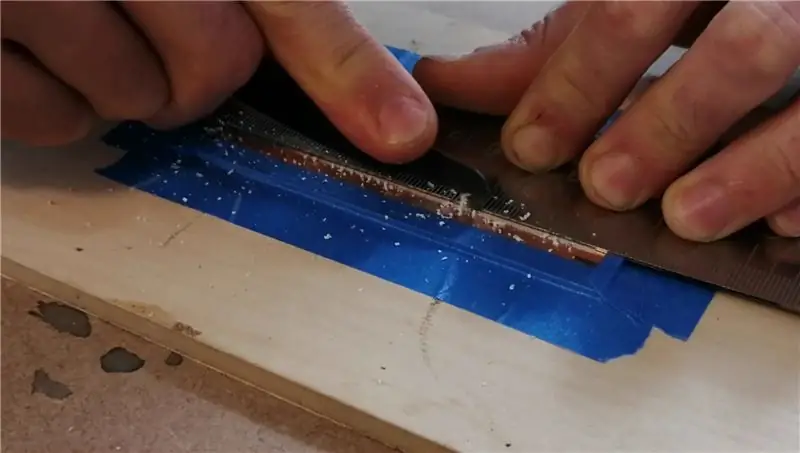
Un vantaggio della pannellatura dei PCB è che puoi utilizzare il pannello come guida per il taglio, inoltre è più facile maneggiare una scheda più grande. Per separare le tavole e dare loro una finitura adeguata, dobbiamo prima tagliarle a pezzi e carteggiare i bordi e gli angoli.
Il taglio del PCB non può essere eseguito con un normale cutter, forbici o seghe, poiché questi processi quasi sicuramente fallirebbero o danneggerebbero le schede. Per il taglio, utilizzeremo un semplice strumento ad artiglio che raschia gradualmente gli strati ad ogni passaggio, intagliando un solco fino in fondo. Queste lame sono vendute commercialmente come frese acriliche, ma possono anche essere fatte in casa da alcune lame di seghetto rotte. si consiglia di riaffilare la lama durante il processo poiché i pannelli in fibra di vetro consumano rapidamente il bordo. Non è necessario tagliare fino in fondo, solo per la maggior parte e, successivamente, staccare semplicemente ogni pezzo.
Dopo il taglio, i bordi sono piuttosto ruvidi e irregolari, quindi dobbiamo carteggiarli accuratamente prima con carta vetrata a grana 240 e poi con una grana 400 per una maggiore levigatezza. Assicurati di arrotondare anche gli angoli seguendo la forma del rivestimento in rame.
Infine, usa un cutter per staccare con cura gli adesivi dalle tavole. Questo può essere fatto prima del taglio, ma gli adesivi aiutano a proteggere il rame durante il processo di taglio.
Passaggio 5: applicazione degli adesivi Kapton Soldermask
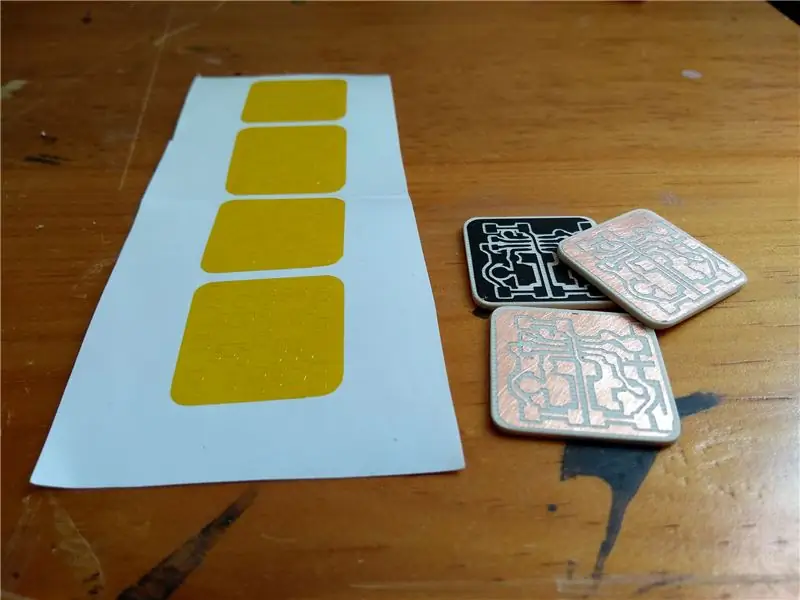
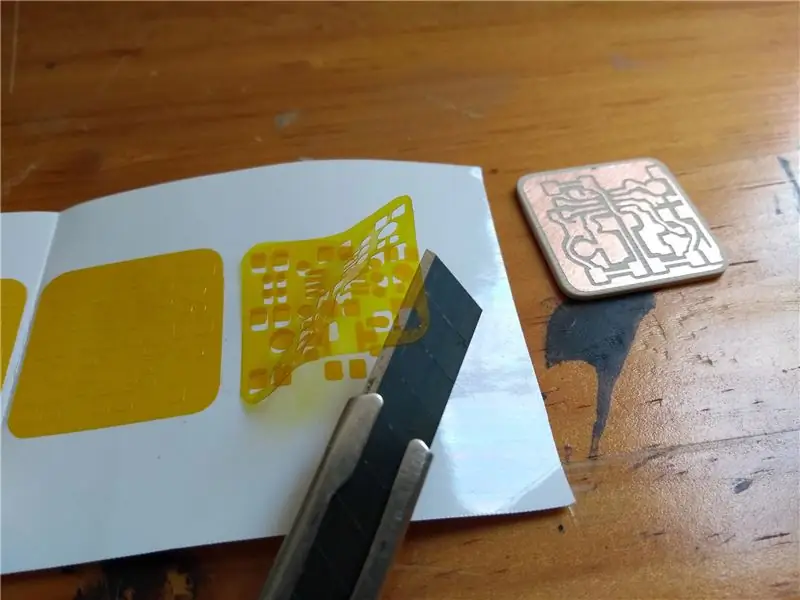
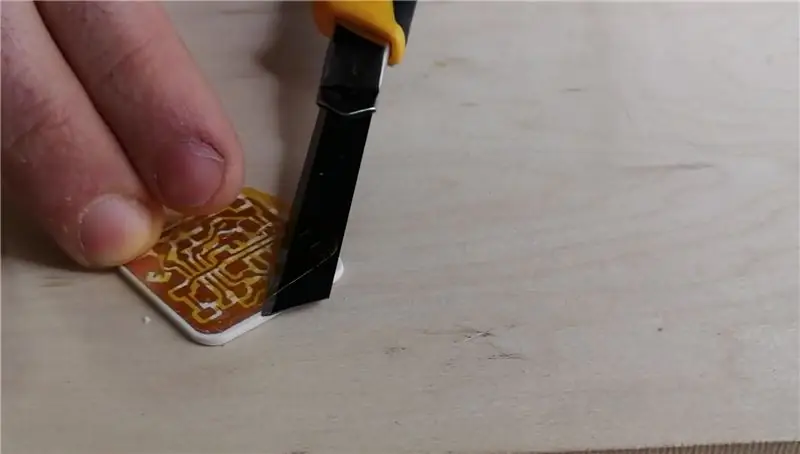
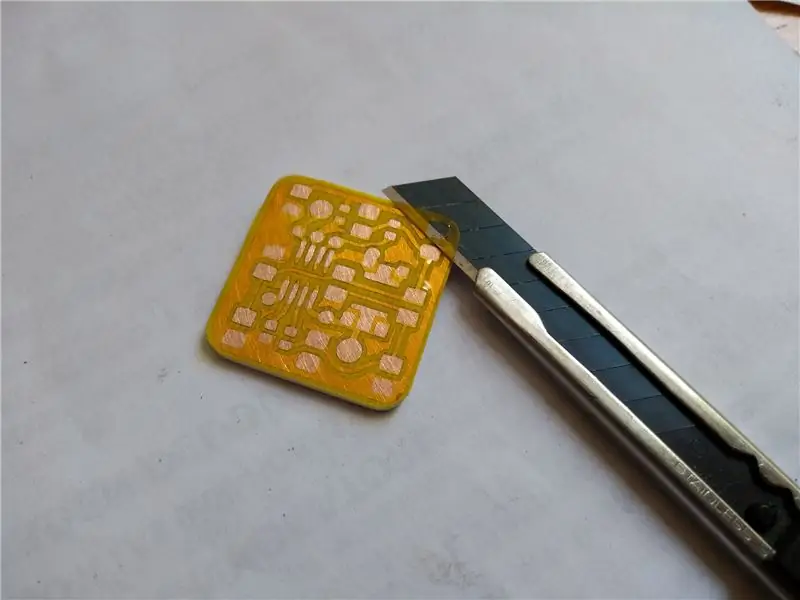
Ora con le schede tagliate, siamo quasi pronti per assemblare il circuito, tuttavia, per garantire che le tracce di rame siano protette a lungo termine e la saldatura rimanga solo dove dovrebbe, abbiamo bisogno di un soldermask, che è realizzato convenzionalmente utilizzando resine UV.. Il processo tradizionale è piuttosto tossico, disordinato e inaffidabile, quindi è necessaria un'alternativa più pratica per la produzione domestica.
In questo caso, sfruttiamo il nastro Kapton come soldermask grazie alla sua resistenza alle alte temperature e alle proprietà autoadesive. Per trasferire gli adesivi sui PCB utilizzeremo nuovamente la taglierina come supporto. Prima di trasferire gli adesivi, pulire accuratamente i PCB con alcol denaturato per rimuovere grasso o residui dal vinile. Quindi, procedi a sollevare con attenzione l'adesivo Kapton dalla carta di supporto con la taglierina (vedi immagine 2). Per questo, prima solleva un piccolo angolo dell'adesivo con il taglierino e premilo contro la lama per farlo aderire, quindi allontana lentamente il taglierino dalla carta senza fare una piega sul bordo tagliente fino a quando l'intero adesivo non si stacca dalla carta e rimane attaccato alla lama.
Infine, è importante assicurarsi che l'adesivo sia correttamente allineato con i cuscinetti prima di fissarlo in posizione, quindi portalo delicatamente sul PCB con la taglierina e strofinalo leggermente sulla scheda alcune volte, questo lo caricherà di elettricità statica e renderà una sorta di galleggiamento sulla superficie, che ti consentirà di regolare il posizionamento prima di premerlo in posizione. Se il timbro si attacca prematuramente, staccalo con attenzione dal cartone mentre lo staccavi dalla carta e ripeti l'allineamento. Una volta allineato correttamente, premilo saldamente sul PCB con le dita e stacca con cura la taglierina dall'adesivo per completare l'impostazione. Quindi, pulisci nuovamente le schede con alcool e ora i PCB sono ufficialmente finiti. Possono essere utilizzati subito o stoccati per dopo.
Passaggio 6: assemblare i dadi: applicare la pasta saldante
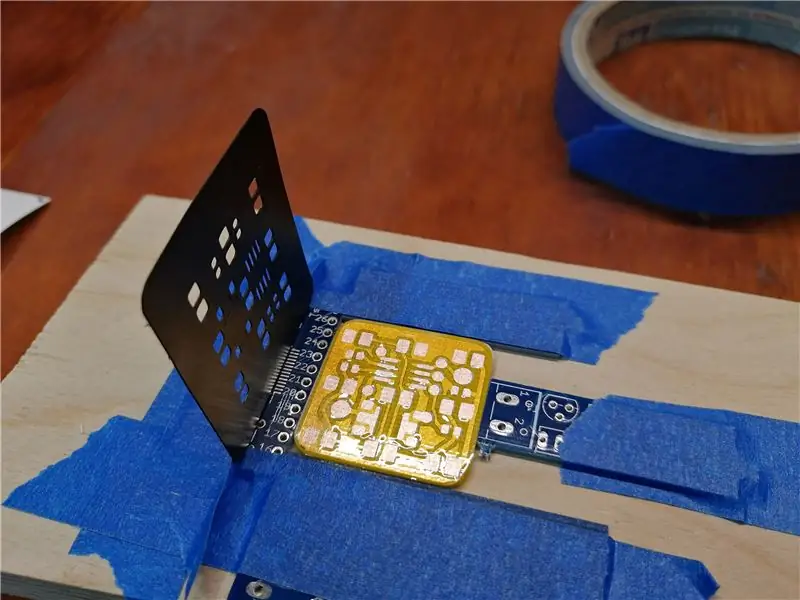
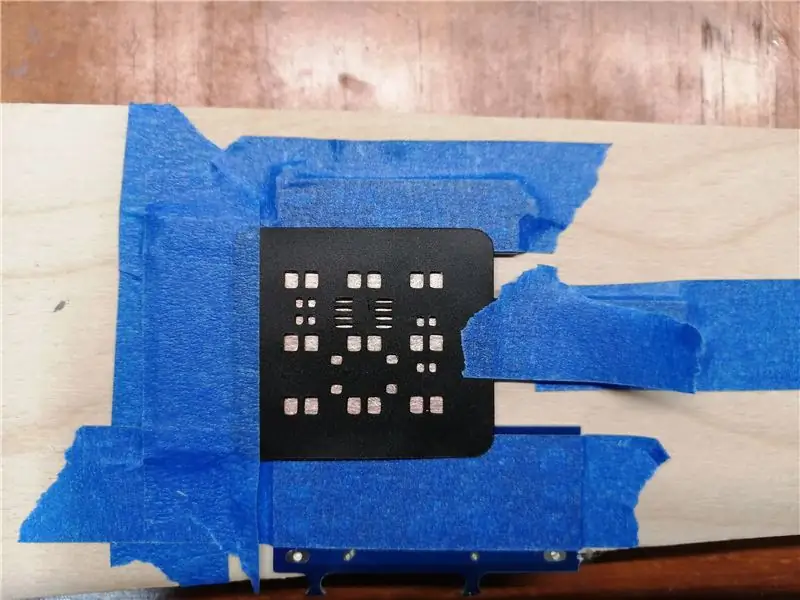
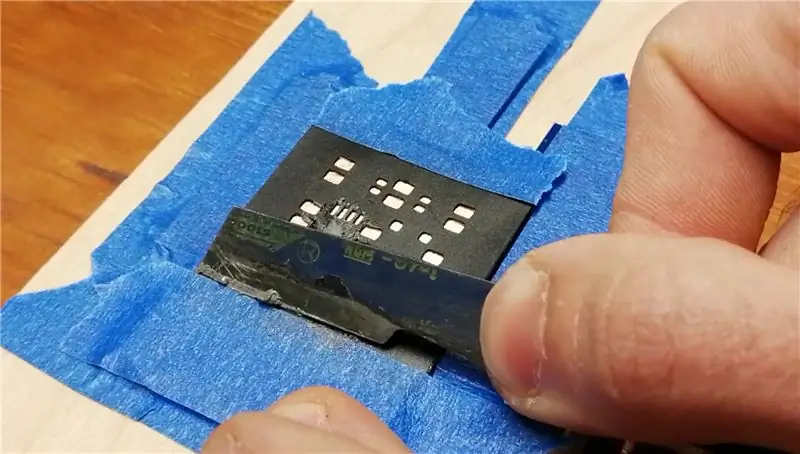
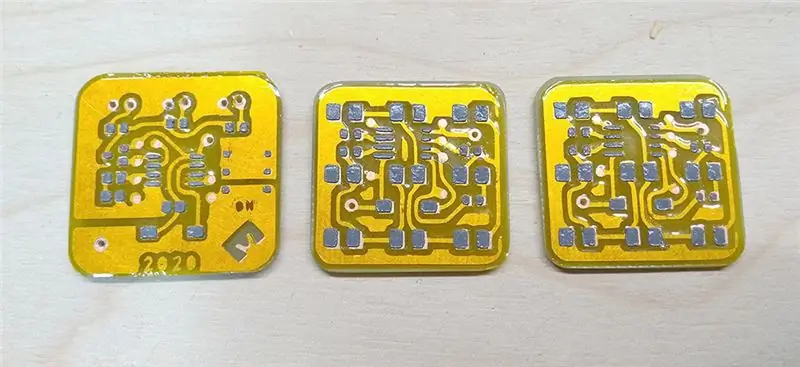
Un vantaggio dei circuiti SMD è che possono essere saldati con pasta in modo molto affidabile e veloce utilizzando un semplice stencil per applicarlo solo sulle piazzole, che possono essere riutilizzate per un numero qualsiasi di unità. Gli stencil SMD convenzionali sono realizzati in acciaio, quindi sono piuttosto costosi e poco pratici per la prototipazione, tuttavia, lo stencil può anche essere realizzato con adesivi in vinile. Per questo, utilizziamo sia la versione originale che quella specchiata dell'adesivo per creare uno stencil di plastica che non sia autoadesivo.
La pasta saldante contiene molto flusso, quindi si riduce significativamente durante il riflusso. Pertanto, è necessario applicare uno strato sufficientemente spesso per garantire che i giunti si riempiano correttamente con la saldatura. Per realizzare lo stencil dello spessore corretto, dobbiamo sovrapporre 4 adesivi in vinile. Fallo con attenzione per assicurarti che i fori siano perfettamente allineati fino in fondo.
Quindi, costruisci un piccolo bordo attorno a una scheda con PCB di scarto o qualsiasi altro materiale dello stesso spessore e fissa lo stencil in posizione da un singolo lato per fungere da cerniera, assicurando il corretto allineamento dello stencil sui pad (vedi immagine 2).
Infine, usando un qualsiasi tipo di strumento per la riga, prendi un po' di pasta saldante e inizia a spalmarlo sullo stencil fino a riempire tutti i fori, quindi raschia il resto nella bottiglia con lo stesso strumento. Non toccare direttamente la pasta saldante, poiché contiene piombo, che è meglio evitare. Non preoccuparti se lo tocchi, basta pulirlo accuratamente.
Solleva lo stencil e rimuovi la tavola dalla maschera. Ripeti il processo per tutte le schede che intendi assemblare. Ora le schede sono pronte per il popolamento e la saldatura.
Step 7: Popolazione e saldatura a riflusso
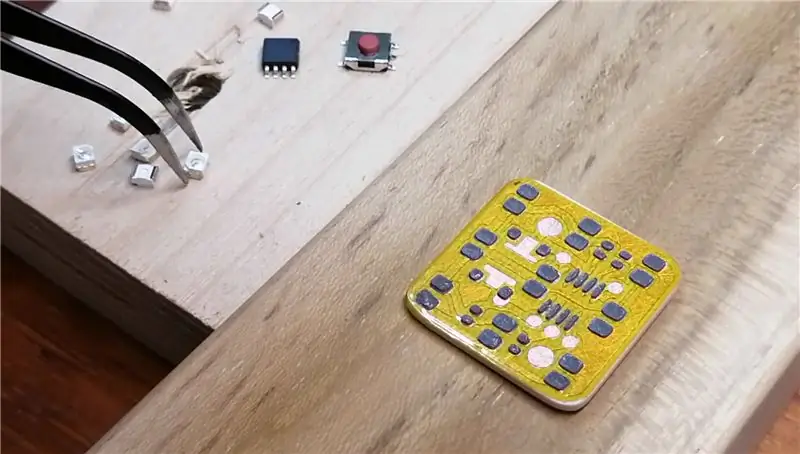
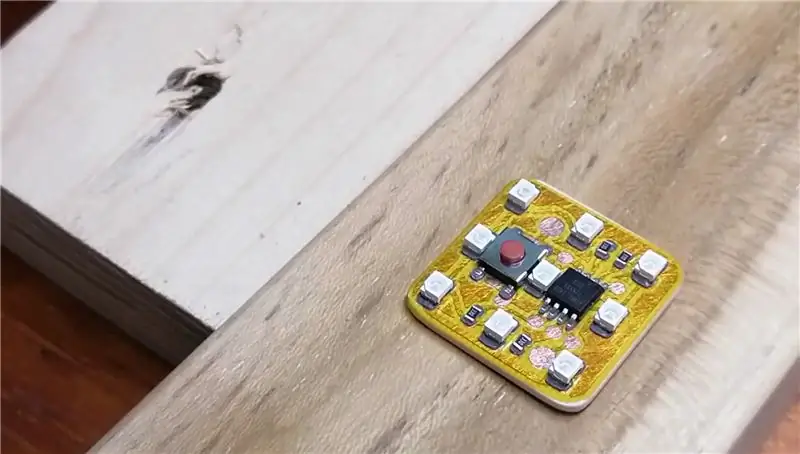
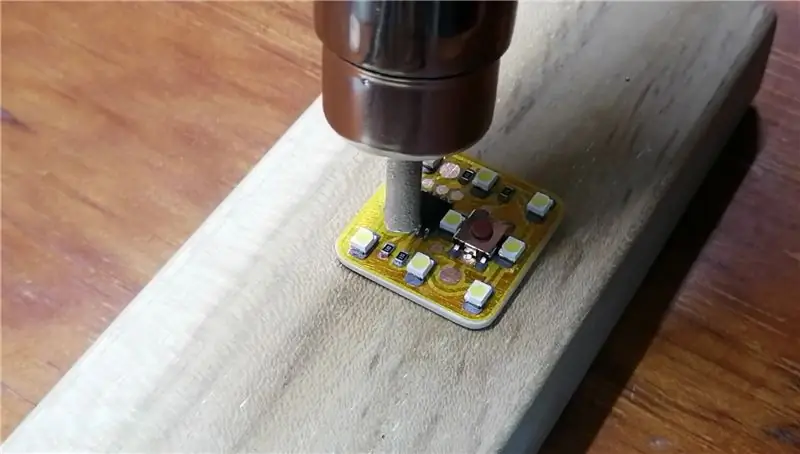
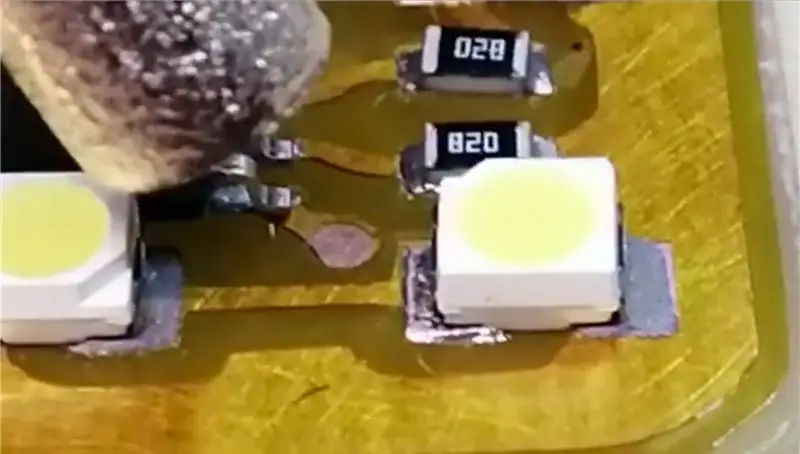
Con la pasta saldante sulle schede, è il momento di popolare tutti i componenti. Per questo, usa delle pinzette a punta fine e posiziona con cura ogni componente sui suoi pad, assicurando il corretto orientamento e allineamento (vedi immagine 2). Prenditi il tuo tempo per farlo e correggere eventuali errori di posizionamento. Una volta posizionati tutti i componenti, accendi lo strumento di riflusso dell'aria e inizia gradualmente a preriscaldare l'intera scheda passandoci sopra con il mouse (vedi immagine 3). Quindi, procedi a dirigere l'aria calda direttamente su ciascun pad finché non rifluiscono completamente (immagine 4). Quando hai finito di ridisporre, è il momento di aggiungere la clip della batteria. Per questo, forare i centri dei 2 cuscinetti rotondi più grandi e posizionare la clip della batteria sul lato inferiore della scheda. Si consiglia di incollare anche la clip della batteria alla scheda con resina epossidica per alleviare lo stress dei pin di alimentazione poiché la clip terrà la scheda sulla custodia. A questo punto il PCB è completamente assemblato e pronto per la programmazione.
Passaggio 8: stampa 3D delle custodie per portachiavi
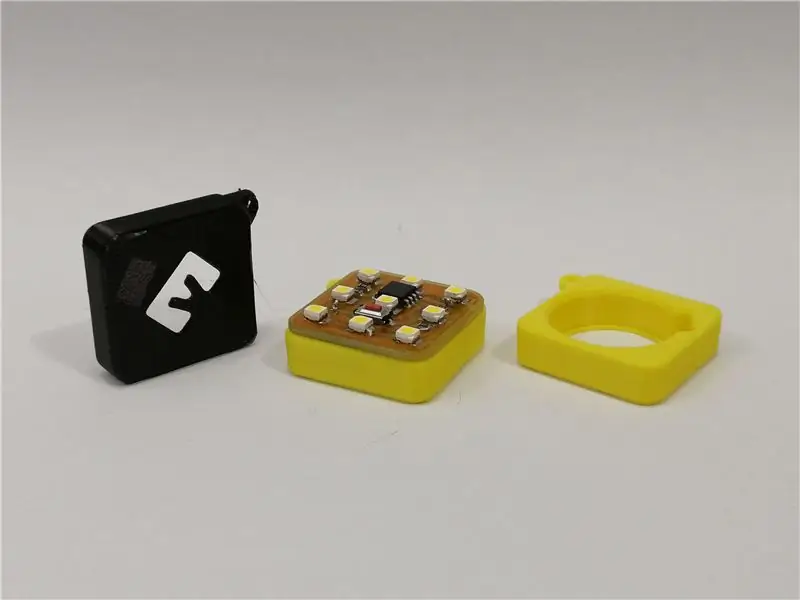

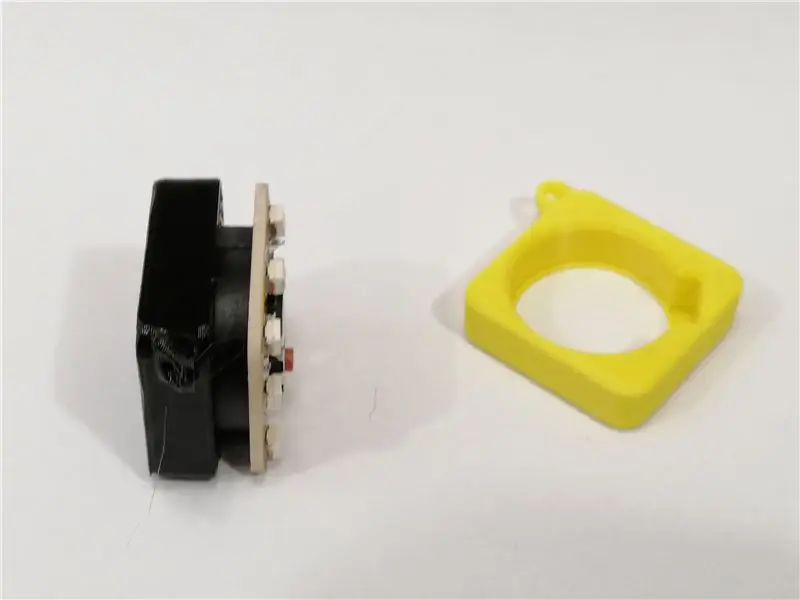
Le custodie stampate in 3D sono opzionali ma altamente consigliate, in quanto aggiungono molto carattere all'oggetto trasformandolo in un portachiavi, proteggendo anche il dado. È obbligatorio stamparli in PETG per garantire un'elevata durata, poiché molto probabilmente il PLA si romperà molto rapidamente. Ho realizzato due versioni della custodia, una con un supporto cavo per rimuovere la batteria e un'altra con il mio logo sul retro, che mantiene la batteria sicura e nascosta. Poiché il circuito consuma pochissima energia, la batteria può rimanere intrappolata all'interno della custodia senza alcun problema.
Per assemblare la custodia, basta premere la clip della batteria sulla stampa 3D finché la scheda non è a filo con il bordo. A seconda dell'esatto clip della batteria, potrebbe essere necessario carteggiarlo leggermente o aumentare l'altezza della custodia per assicurarsi che si adatti completamente, quindi assicurati di controllare prima del montaggio. Se necessario, tuttavia, la custodia può essere aperta estraendo lentamente la scheda lungo tutto il bordo.
Passaggio 9: crea una maschera di programmazione
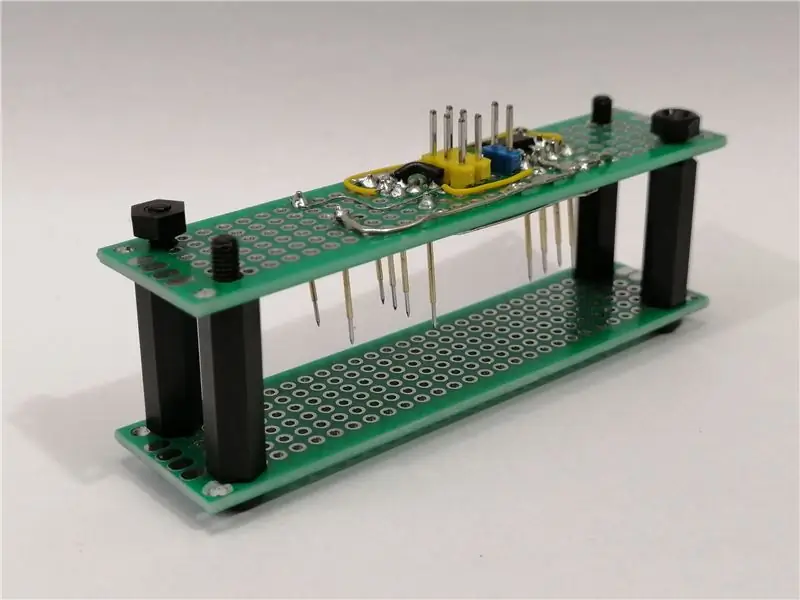
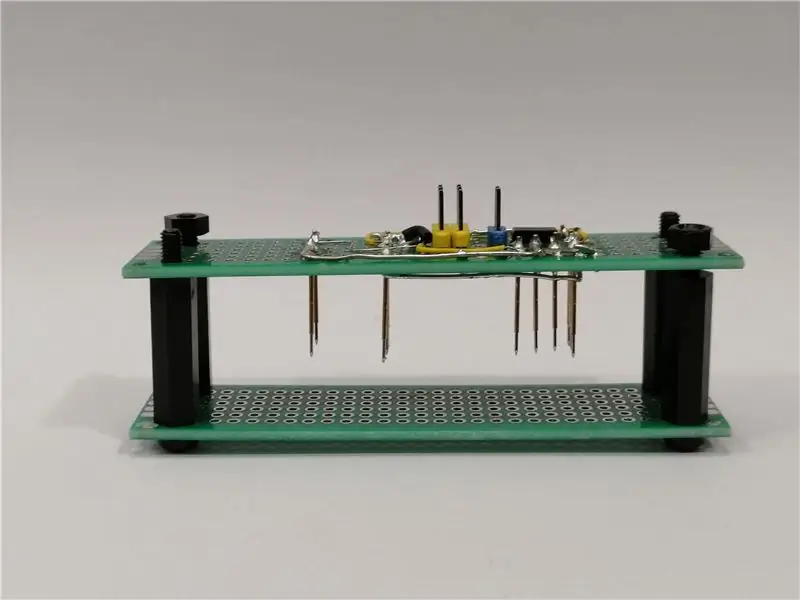
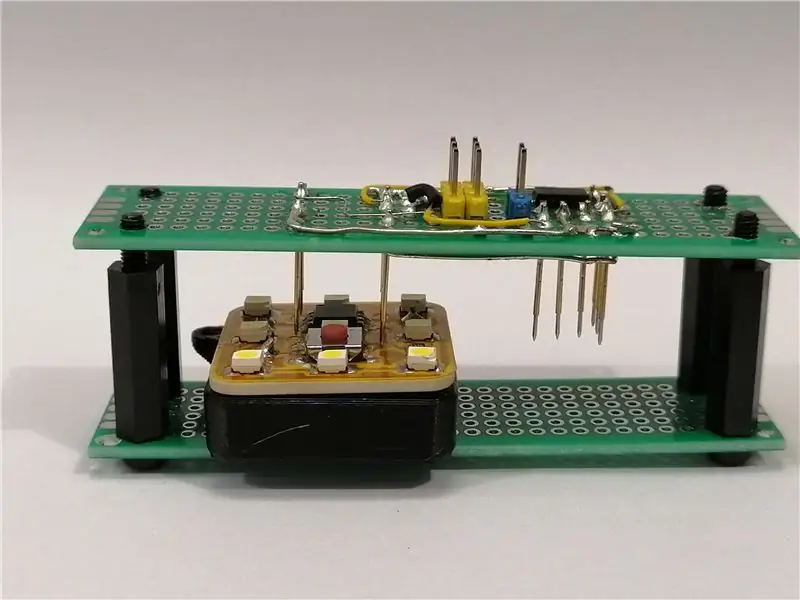
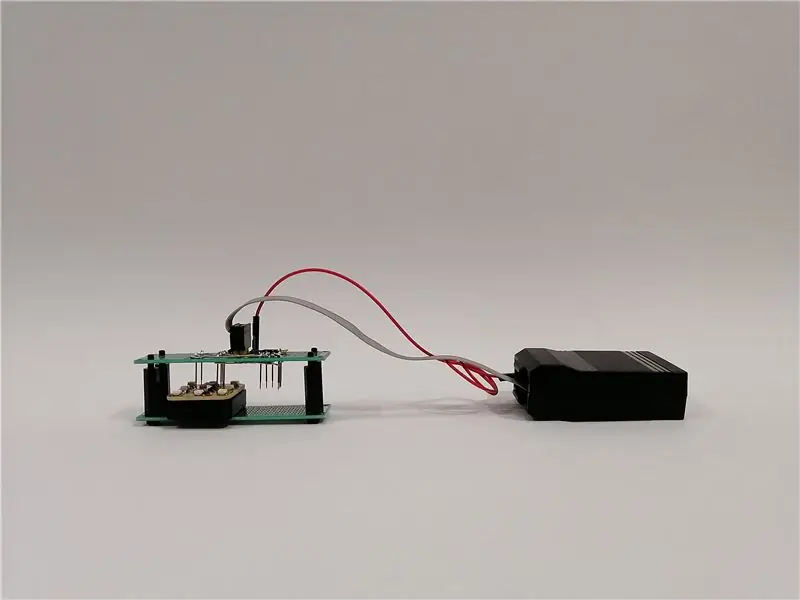
Ora i tinyDice sono completamente assemblati, tuttavia dobbiamo programmarli per farli funzionare come dovrebbero. Per questo, utilizziamo un jig pogo pin che contatta tutti i pad di programmazione sulla scheda e si collega a un programmatore ISP, che può essere un USBtinyISP o qualsiasi Arduino come ISP. il tinyDice dispone di tutti i perni di programmazione disponibili su tamponi con passo standard di 100 mill (2,54 mm), in modo da consentire il montaggio della maschera su un pannello forato standard. Segui lo schema di connessione per collegare ciascun pin pogo all'intestazione dell'ISP. Per scopi di sviluppo, ho realizzato un doppio jig che serve anche per un'altra scheda su cui sto lavorando e ho incorporato un regolatore LDO per evitare di scaricare le batterie durante i test, ma per una volta programmata possiamo utilizzare la potenza direttamente dalla batteria
tinyDice sono progettati per funzionare a 3 volt, quindi programmarli a 5 volt comporta il rischio di danneggiare i pin IO del microcontrollore, i LED o persino il programmatore poiché troppa corrente verrebbe assorbita dai resistori di limitazione della corrente del LED. Quindi, per programmare il chip senza danneggiare nulla, dobbiamo utilizzare la sua tensione nativa dalla batteria. Se usi un USBtinyISP, rimuovi semplicemente il suo ponticello di alimentazione, che alimenterà il Logic Lever Shifter interno dalla batteria del tinyDice, e se usi un Arduino, lascia semplicemente l'alimentazione scollegata per alimentare solo i dadi con la batteria e aggiungi un resistore serie 5k a ciascuna linea dati.
Passaggio 10: programmazione dei dadi
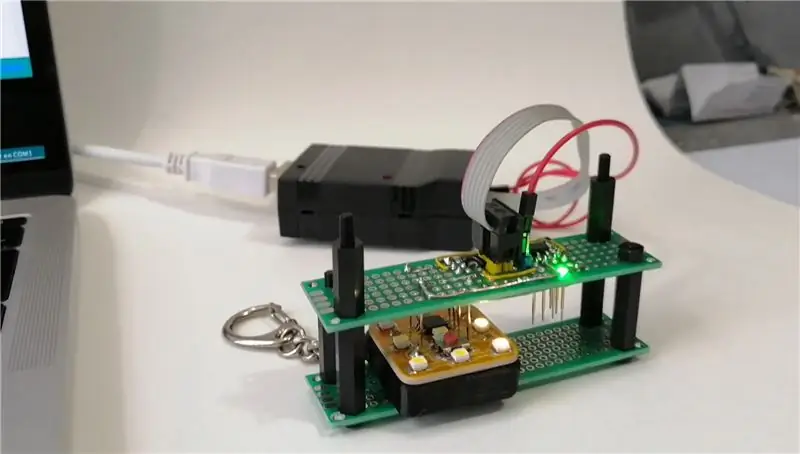
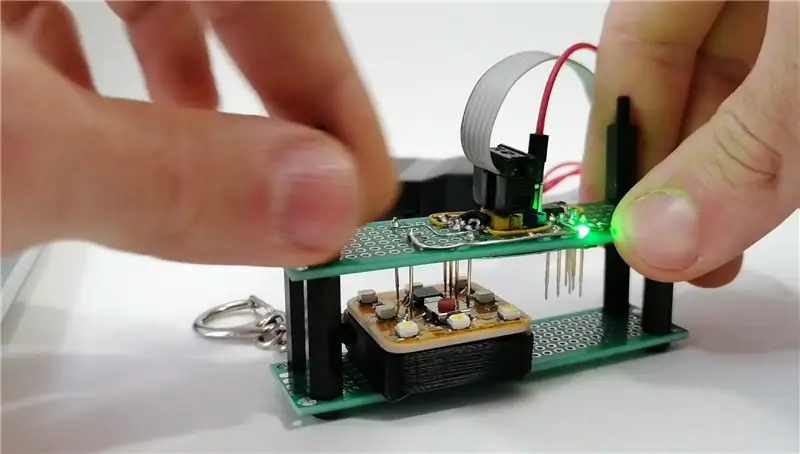
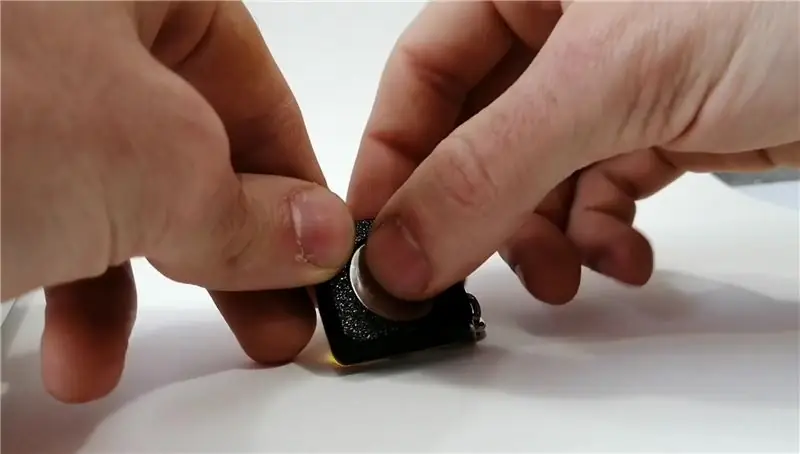
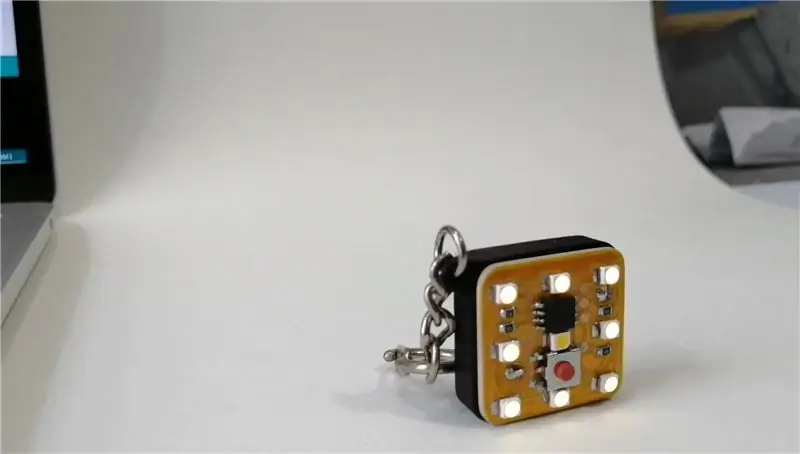
Per il processo di programmazione, assemblare con cura la maschera sui dadi utilizzando i distanziatori e assicurarsi che tutti i perni pogo premano correttamente sui pad corrispondenti. Fare attenzione e non far scivolare la fustella sotto i perni poiché è molto facile romperli. Quindi, collega USBtinyISP alla maschera e al computer.
Apri l'IDE Arduino, carica lo sketch tinyDice e seleziona il chip atTiny85 con USBtinyISP come programmatore. Premi il pulsante di caricamento e controlla i dadi, 2 LED dovrebbero iniziare a lampeggiare per un po'. Se tutto è andato a buon fine, ora tinyDice è programmato, finito e pronto per l'uso. Ripetere il processo di programmazione per tutte le unità realizzate e successivamente conservare la dima completamente assemblata per proteggere i pogo pin.
Il codice:
Il programma del tinyDice è tale da visualizzare prima un'animazione "pensante", quindi genera un numero casuale compreso tra 0 e 9 che viene visualizzato per alcuni secondi. Tutte le transizioni vengono eseguite con PWM per ciascun LED per consentire le dissolvenze. Dopo aver visualizzato il numero e la dissolvenza, il processore entra in modalità di sospensione che sostanzialmente interrompe il consumo della batteria, quindi la batteria dovrebbe teoricamente durare circa 6.000 "tiri" dei dadi.
L'intero codice è strutturato attorno a un timer di interrupt a 8 Khz che gestisce il charlieplexing e il PWM a 10 step per ogni LED, nonché l'avanzamento delle animazioni. Spiegazioni più dettagliate di ogni funzione sono commentate sullo sketch Arduino.
Conclusioni:
I risultati di questo metodo per la produzione domestica di PCB hanno superato di gran lunga le mie aspettative iniziali, poiché ho scoperto che può essere estremamente affidabile e produrre risultati di altissima qualità per la prototipazione facile e veloce di circuiti SMD e a foro passante. Per questo motivo incoraggio i fai-da-te a provare questo metodo per i propri progetti e a condividere i risultati e le scoperte con la community.
Questa nuova versione di tinyDice è di per sé un oggetto molto carino e divertente da avere e condividere con gli amici, poiché le animazioni e il portachiavi lo rendono piuttosto unico e interessante. Spero che questo tutorial ti sia piaciuto e per favore condividi i tuoi commenti ed esperienze sull'argomento in modo che il metodo continui ad evolversi. Inoltre, sentiti libero di sperimentare con il codice e condividere eventuali varianti interessanti per far provare ad altri.
Questa guida fa parte del concorso di progettazione PCB, quindi votala se la ritieni degna e condividila con i tuoi amici e appassionati di elettronica.
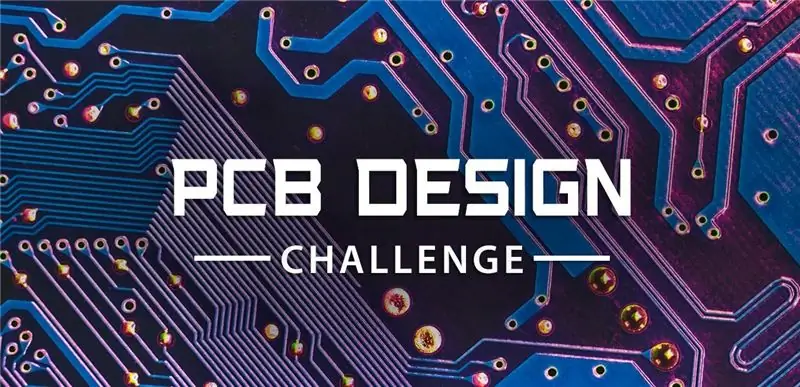
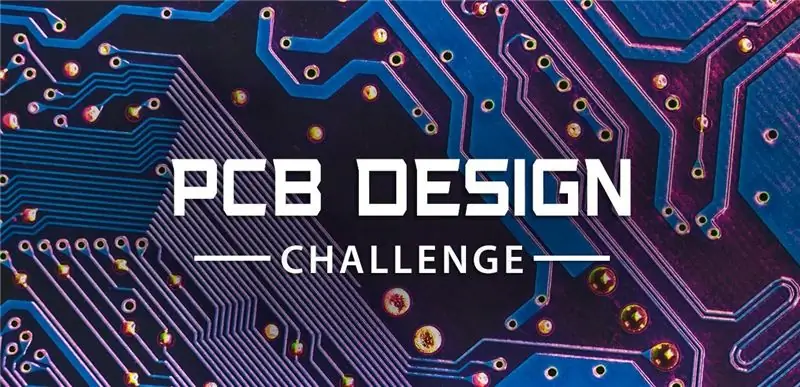
Secondo premio nella PCB Design Challenge
Consigliato:
Istruzioni su come utilizzare un cutter per vinile MH871-MK2: 11 passaggi
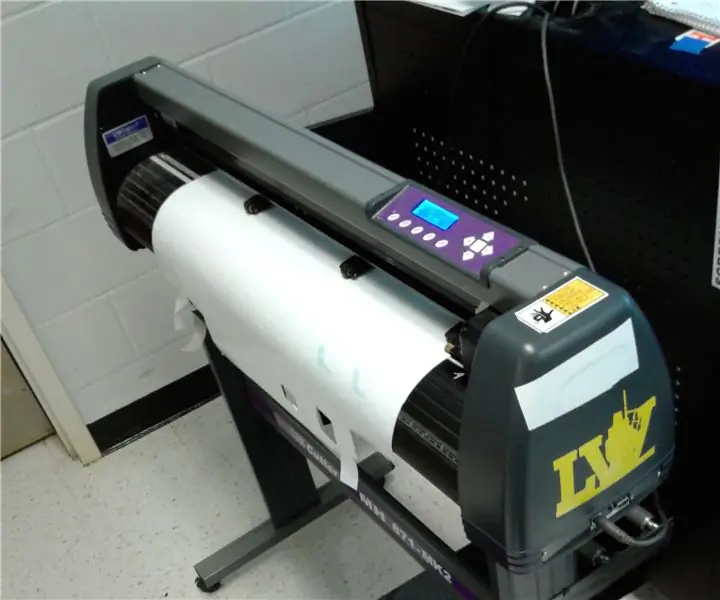
Istruzioni su come utilizzare un cutter per vinile MH871-MK2: Ciao, mi chiamo Ricardo Greene e ho creato istruzioni su come utilizzare un cutter per vinile MH871-MK2
Utilizzo di un cutter per vinile per creare uno stencil per aerografo: 5 passaggi
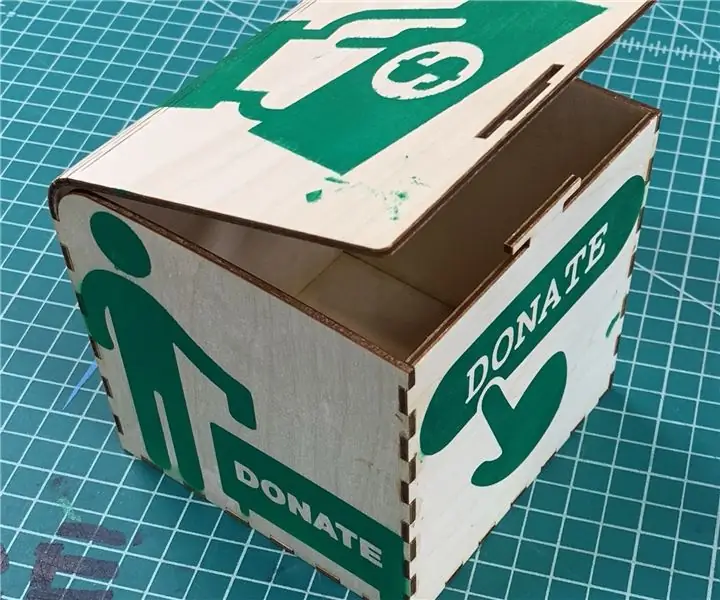
Utilizzo di un cutter in vinile per creare uno stencil per aerografo: in questo tutorial, darò una breve introduzione al processo di utilizzo di un cutter in vinile per creare stencil che puoi usare per dipingere con una configurazione aerografo o davvero, con qualsiasi tipo di vernice. In queste foto ho usato un aerografo boo
Vinile a trasferimento termico con design a doppio colore per t-shirt: 10 passaggi (con immagini)
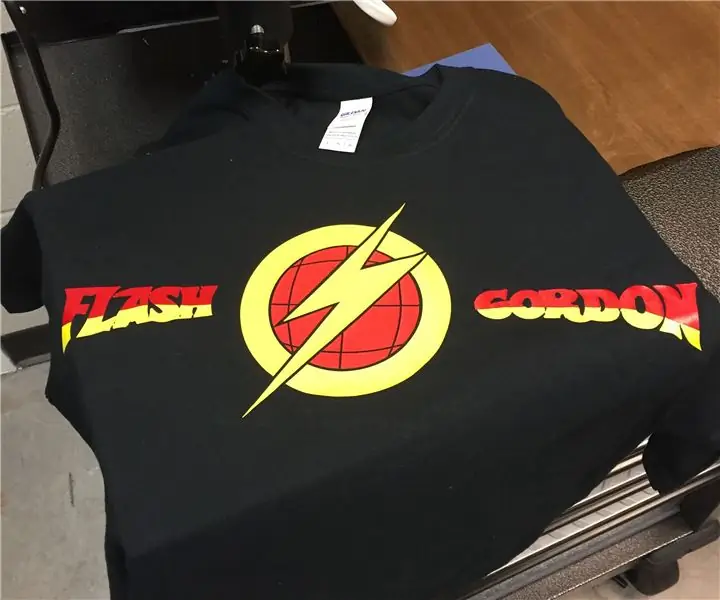
Vinile a trasferimento termico con design a due colori per t-shirt: questo tutorial ti insegnerà come realizzare una t-shirt con un design in vinile a due colori usando la pressa a caldo. Materiali: Vinile a trasferimento termico Taglierina per vinile Computer con programma Vinylmaster Pressa a caldoForbiciSarchiatriceT-shirtRulerX-ACTO Knife
Crea PCB per hobbysti con strumenti CAD professionali modificando le "Regole di progettazione": 15 passaggi (con immagini)
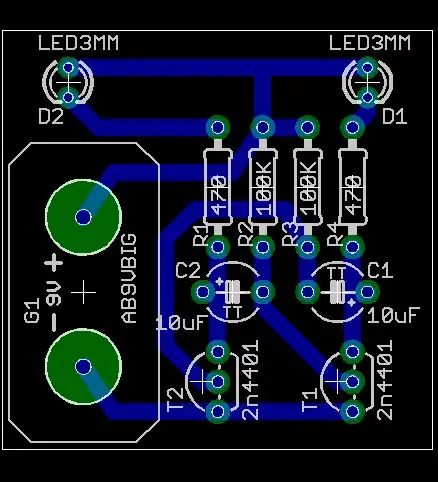
Crea PCB per hobbisti con strumenti CAD professionali modificando le "Regole di progettazione": è bello che ci siano alcuni strumenti per circuiti stampati professionali a disposizione degli hobbisti. Ecco alcuni suggerimenti per usarli per progettare schede che non hanno bisogno di un fabbricante professionista per REALIZZARLI
PCB professionali quasi più economici che realizzarli in casa: 14 passaggi
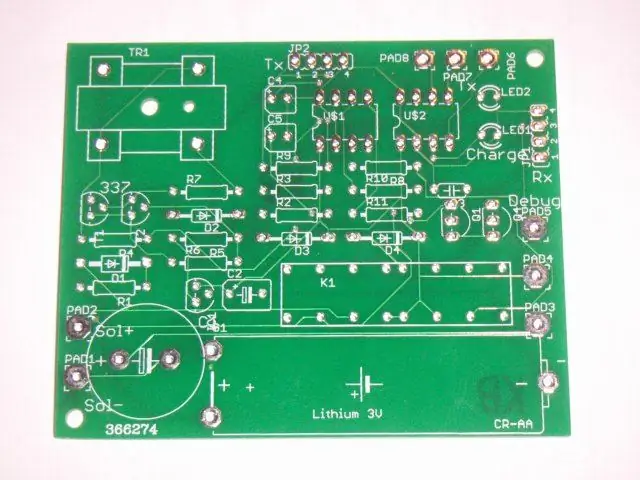
PCB professionali quasi più economici che realizzarli in casa: sebbene ci sia una grande soddisfazione nella costruzione di PCB a casa, sommando il costo del PCB vuoto, dell'etchant e delle punte da trapano arriva a oltre $ 4 per scheda. Ma per $ 6,25 a tavola l'intera cosa può essere realizzata in modo professionale. Questo Instructable ti porta attraverso