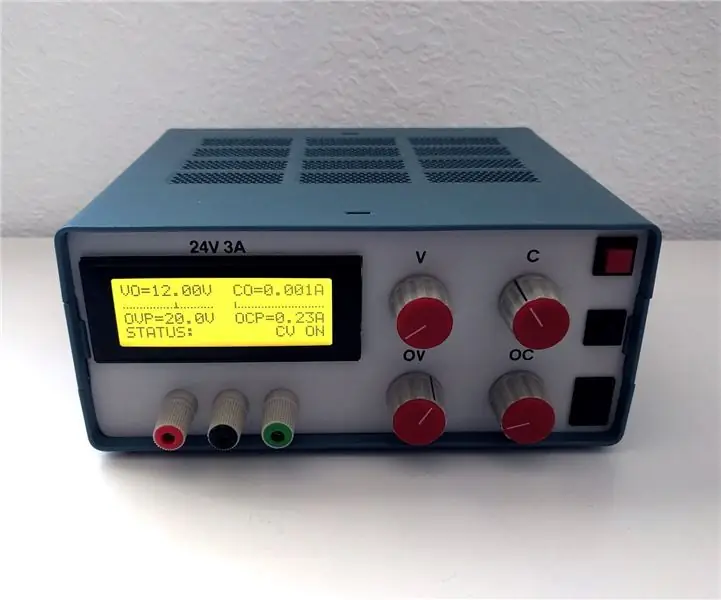
Sommario:
- Passaggio 1: parti e schema elettrico
- Passaggio 2: kit circuito di alimentazione
- Passaggio 3: assemblaggio del kit del circuito di alimentazione
- Passaggio 4: progettazione e schema del circuito del misuratore
- Passaggio 5: PCB del circuito del misuratore
- Passaggio 6: assemblaggio del circuito del misuratore
- Passaggio 7: codice Arduino
- Passaggio 8: problemi termici
- Passaggio 9: allegato
- Passaggio 10: meccanizzazione del pannello frontale
- Passaggio 11: meccanizzazione del pannello posteriore
- Passaggio 12: assemblaggio del pannello frontale
- Passaggio 13: assemblaggio del pannello posteriore
- Passaggio 14: assemblaggio finale e cablaggio
- Passaggio 15: miglioramenti e ulteriore lavoro
2025 Autore: John Day | [email protected]. Ultima modifica: 2025-01-23 14:50

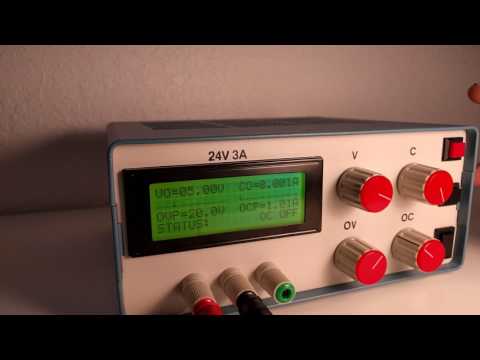

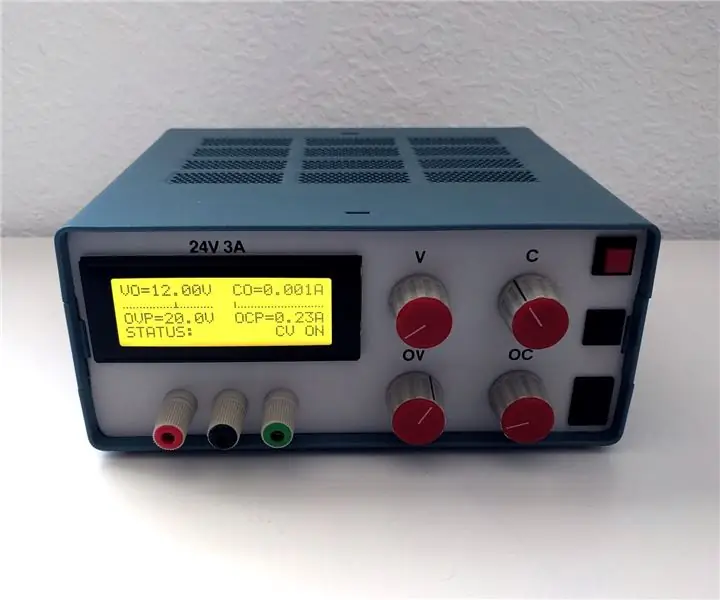
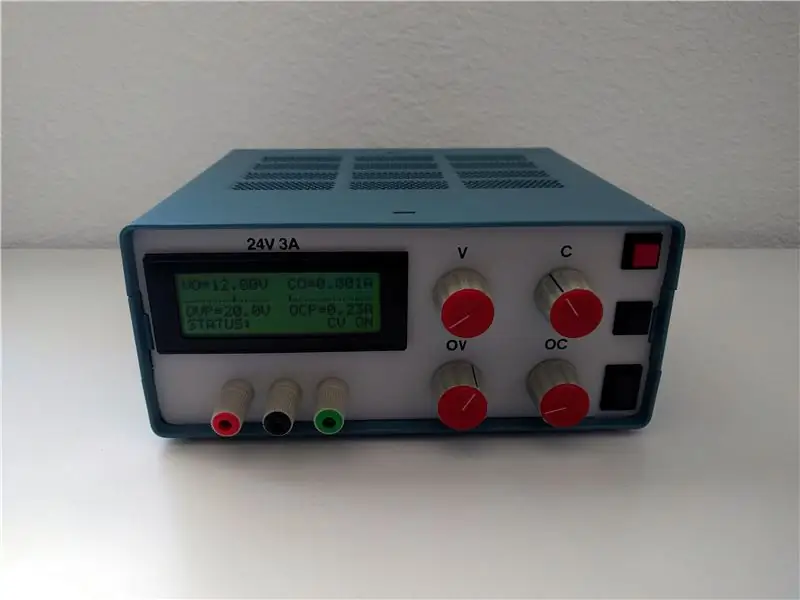
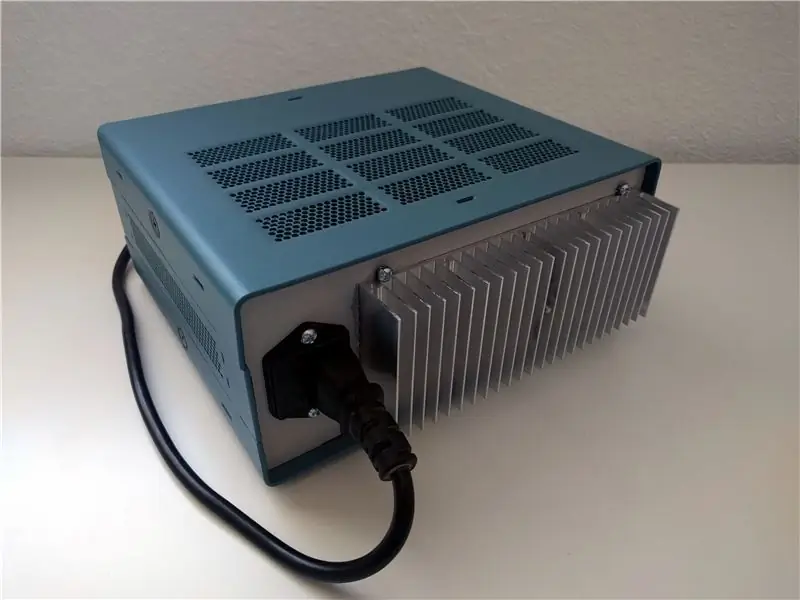
Dal mio punto di vista, uno dei modi migliori per iniziare con l'elettronica è costruire il proprio alimentatore da laboratorio. In questo tutorial ho cercato di raccogliere tutti i passaggi necessari affinché chiunque possa costruirne uno proprio.
Tutte le parti dell'assieme sono ordinabili direttamente in digikey, ebay, amazon o aliexpress tranne il circuito del contatore. Ho realizzato un circuito shield personalizzato per Arduino in grado di misurare fino a 36V - 4A, con una risoluzione di 10mV - 1mA che può essere utilizzato anche per altri progetti.
L'alimentatore ha le seguenti caratteristiche:
- Tensione nominale: 24V.
- Corrente Nominale: 3A.
- Ripple della tensione di uscita: 0,01% (secondo le specifiche del kit del circuito di alimentazione).
- Risoluzione di misurazione della tensione: 10 mV.
- Risoluzione misurazione corrente: 1mA.
- Modalità CV e CC.
- Protezione da sovracorrente.
- Protezione da sovratensione.
Passaggio 1: parti e schema elettrico

Oltre all'immagine, ho allegato il file WiringAndParts.pdf a questo passaggio. Il documento descrive tutte le parti funzionali, compreso il link per l'ordinazione, dell'alimentatore da banco e come collegarle.
La tensione di rete entra attraverso un connettore da pannello IEC (10) che ha un portafusibile incorporato, nel pannello frontale (11) è presente un interruttore di alimentazione che interrompe il circuito formato dal connettore IEC al trasformatore (9).
Il trasformatore (9) emette 21VAC. I 21 VAC vanno direttamente al circuito di alimentazione (8). L'uscita del circuito di alimentazione (8) va direttamente al terminale IN del circuito contatore (5).
Il terminale OUT del circuito del contatore (5) è collegato direttamente ai morsetti positivo e negativo (4) dell'alimentatore. Il circuito del contatore misura sia la tensione che la corrente (high side) e può abilitare o disabilitare la connessione tra ingresso e uscita.
Cavi, in genere utilizzano cavi di scarto che avete in casa. È possibile controllare su Internet il calibro AWG appropriato per 3A ma, in generale, la regola empirica di 4A/mm² funziona, specialmente per cavi corti. Per il cablaggio della tensione di rete (120V o 230V) utilizzare cavi opportunamente isolati, 600V in USA, 750V in Europa.
Il pass transistor in serie del circuito di alimentazione (Q4) (12) è stato cablato anziché saldato per consentire una facile installazione del dissipatore (13).
I potenziometri originali da 10K del circuito di alimentazione sono stati sostituiti con modelli multigiro (7), questo rende possibile una regolazione precisa della tensione e della corrente di uscita.
La scheda arduino del circuito del contatore è alimentata tramite un cavo jack di alimentazione (6) che proviene dal circuito di alimentazione (8). La scheda di alimentazione è stata modificata per ottenere 12V invece di 24V.
Il pin positivo del LED CC dal circuito di alimentazione è collegato al connettore di modalità del circuito del contatore. Ciò gli consente di sapere quando visualizzare la modalità CC o CV.
Ci sono due pulsanti collegati al circuito del contatore (3). Il pulsante Off “rosso” disconnette la tensione di uscita. Il pulsante On “nero” collega la tensione di uscita e ripristina gli errori OV o OC.
Ci sono due potenziometri collegati al circuito del contatore (2). Uno imposta la soglia OV e l'altro imposta la soglia OC. Questi potenziometri non devono essere multigiro, ho usato i potenziometri originali del circuito di alimentazione.
Il display LCD alfanumerico 20x4 I2C (1) è collegato al circuito del contatore. Mostra le informazioni attuali sulla tensione di uscita, la corrente di uscita, il setpoint OV, il setpoint OC e lo stato.
Passaggio 2: kit circuito di alimentazione
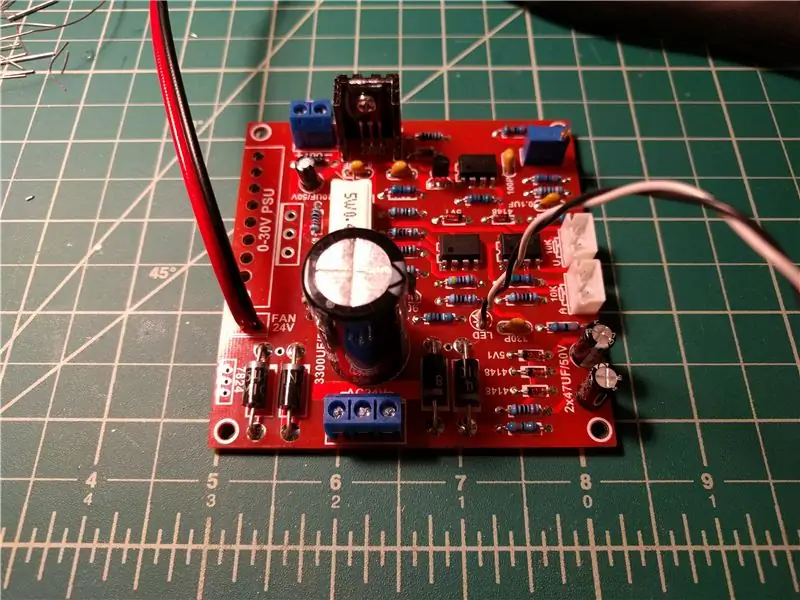
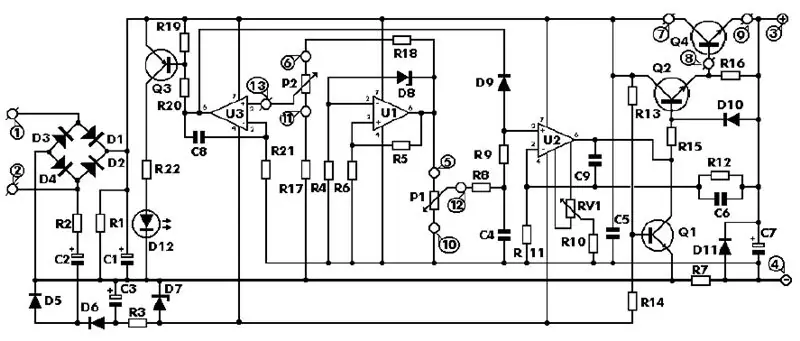
Ho comprato questo kit che è valutato come 30V, 3A:
Allego una guida di montaggio che ho trovato in Internet e un'immagine dello Schematic. Brevemente:
Il circuito è un alimentatore lineare.
Q4 e Q2 sono un array Darlington e formano il pass transistor in serie, è controllato dagli amplificatori operazionali per mantenere la tensione e la corrente al valore desiderato.
La corrente viene misurata da R7, sommando questa resistenza nel lato basso si rende diversa la massa del circuito di alimentazione e la massa di uscita.
Il circuito pilota un LED che si accende quando è attiva la modalità a corrente costante.
Il circuito incorpora il ponte Graeth per rettificare l'ingresso AC. L'ingresso CA viene anche utilizzato per generare una tensione di polarizzazione negativa per raggiungere 0V.
Non c'è protezione termica in questo circuito, quindi è molto importante un dimensionamento appropriato del dissipatore.
Il circuito dispone di un'uscita a 24V per un ventilatore “opzionale”. Ho sostituito il regolatore 7824 con un regolatore 7812 per ottenere 12V per la scheda Arduino del circuito del contatore.
Non ho montato il led, invece ho utilizzato questo segnale per indicare al circuito del contatore se l'alimentazione è in CC o CV.
Passaggio 3: assemblaggio del kit del circuito di alimentazione
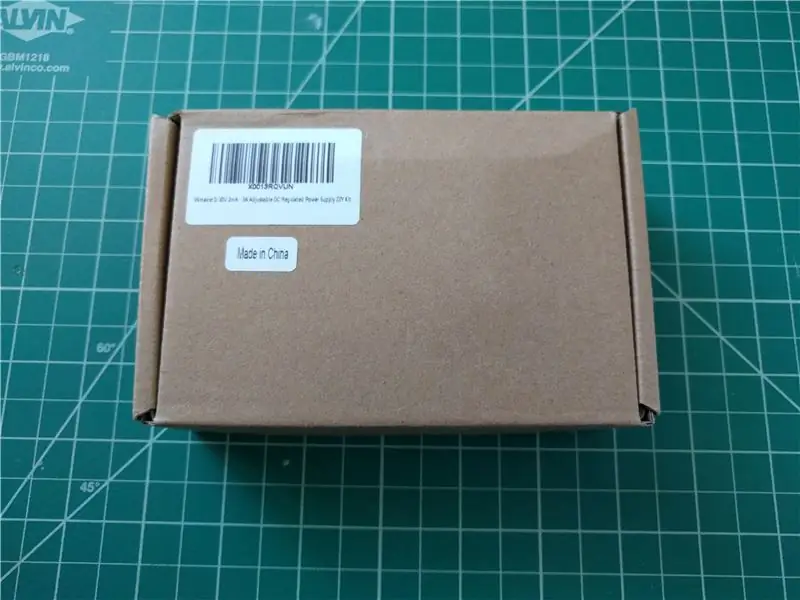
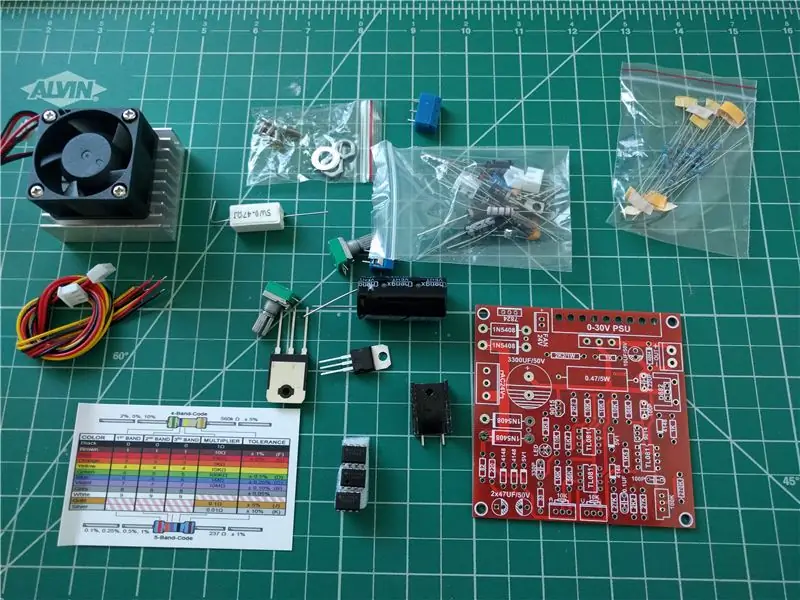
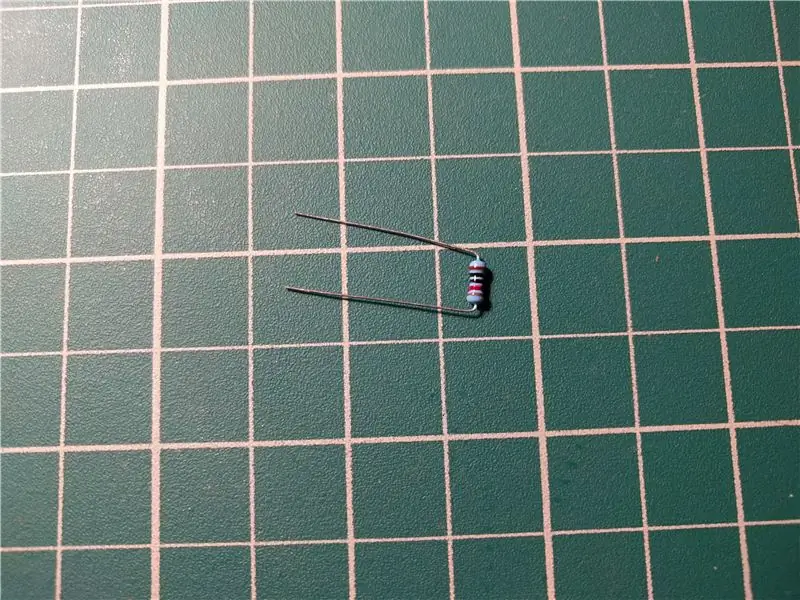
In questo circuito tutte le parti sono passanti. In generale devi iniziare con quelli più piccoli.
- Saldare tutte le resistenze.
- Saldare il resto dei componenti.
- Utilizzare le pinze quando si piegano i cavi dei diodi per evitare di romperli.
- Piega i cavi degli amplificatori operazionali DIP8 TL081.
- Utilizzare il composto del dissipatore di calore durante l'assemblaggio dei dissipatori di calore.
Passaggio 4: progettazione e schema del circuito del misuratore
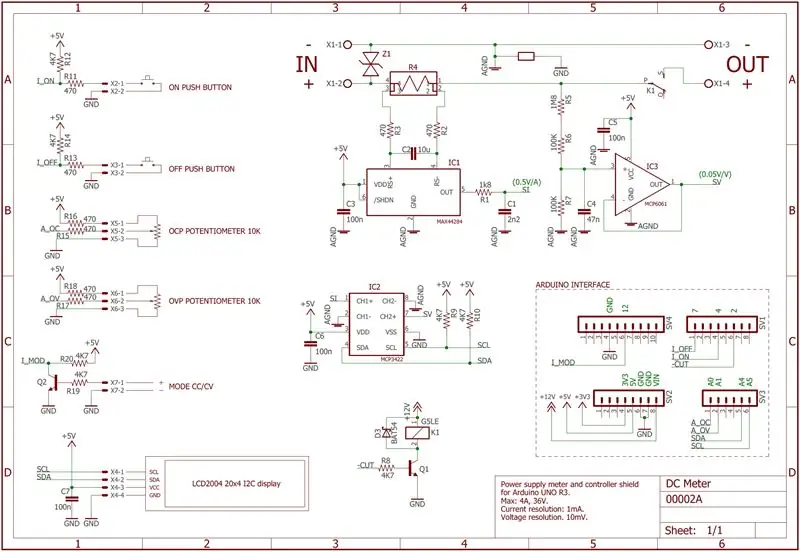
Il circuito è uno shield per Arduino UNO compatibile con le versioni R3. L'ho progettato con parti disponibili su digikey.com.
L'uscita del kit del circuito di alimentazione vkmaker è collegata alla morsettiera IN e la morsettiera OUT va direttamente ai morsetti dell'alimentatore.
R4 è un resistore di shunt nel binario positivo valutato 0,01 ohm, ha una caduta di tensione proporzionale alla corrente in uscita. La tensione differenziale R4 è collegata direttamente ai pin RS+ e RS- di IC1. La caduta di tensione massima all'uscita di corrente massima è 4A*0.01ohm = 40mV.
R2, R3 e C2 formano un filtro ~15Hz per evitare il rumore.
IC1 è un amplificatore di corrente high side: MAX44284F. Si basa su un amplificatore operazionale sminuzzato che lo rende in grado di ottenere una tensione di offset in ingresso molto bassa, 10uV al massimo a 25ºC. A 1mA la caduta di tensione in R4 è 10uV, uguale alla massima tensione di offset in ingresso.
Il MAX44284F ha un guadagno di tensione di 50V/V quindi la tensione di uscita, segnale SI, alla corrente massima di 4A, varrà 2V.
La tensione di ingresso di modo comune massima di MAX44284F è 36V, questo limita l'intervallo di tensione di ingresso a 36V.
R1 e C1 formano un filtro per sopprimere i segnali indesiderati a 10 KHz e 20 KHz che possono apparire a causa dell'architettura del dispositivo, si consiglia a pagina 12 della scheda tecnica.
R5, R6 e R7 sono un partitore di tensione ad alta impedenza di 0,05 V/V. R7 con C4 forma un filtro ~5Hz per evitare il rumore. Il partitore di tensione è posto dopo R4 per misurare la reale tensione di uscita dopo la caduta di tensione.
IC3 è un amplificatore operazionale MCP6061T, forma un inseguitore di tensione per isolare il partitore di tensione ad alta impedenza. La massima corrente di polarizzazione in ingresso è di 100pA a temperatura ambiente, tale corrente è trascurabile rispetto all'impedenza del partitore di tensione. A 10 mV la tensione all'ingresso di IC3 è 0,5 mV, molto più grande della sua tensione di offset in ingresso: 150 uV al massimo.
L'uscita di IC3, segnale SV, ha una tensione di 2V a una tensione di ingresso di 40V (il massimo possibile è 36V a causa di IC1). I segnali SI e SV sono collegati a IC2. IC2 è un MCP3422A0, un ADC sigma delta I2C a doppio canale. Ha un riferimento di tensione interno di 2.048V, guadagno di tensione selezionabile di 1, 2, 4 o 8V/V e numero selezionabile di 12, 14, 16 o 18 bit.
Per questo circuito sto usando un guadagno fisso di 1V/V e una risoluzione fissa di 14 bit. I segnali SV e SI non sono differenziali, quindi il pin negativo di ciascun ingresso deve essere messo a terra. Ciò significa che il numero di LSB disponibili sarà la metà.
Poiché il riferimento di tensione interno è 2.048V e il numero effettivo di LSB è 2^13, i valori ADC saranno: 2LSB per ogni 1mA in caso di corrente e 1LSB per ogni 5mV in caso di tensione.
X2 è il connettore per il pulsante ON. R11 impedisce all'ingresso del pin Arduino di scariche statiche e R12 è un resistore di pull-up che produce 5 V quando non viene premuto e ~ 0 V quando viene premuto. Segnale I_ON.
X3 è il connettore per il pulsante OFF. R13 impedisce all'ingresso del pin Arduino di scariche statiche e R14 è un resistore di pull-up che produce 5 V quando non viene premuto e ~ 0 V quando viene premuto. Segnale I_OFF.
X5 è il connettore per il potenziometro del setpoint di protezione da sovracorrente. R15 impedisce al pin di ingresso Arduino di scariche statiche e R16 impedisce il cortocircuito del binario +5V. Segnale A_OC.
X6 è il connettore per il potenziometro del setpoint di protezione da sovratensioni. R17 impedisce al pin di ingresso Arduino di scariche statiche e R18 impedisce il cortocircuito del binario +5V. Segnale A_OV.
X7 è un ingresso esterno che viene utilizzato per ottenere la modalità corrente costante o tensione costante dell'alimentatore. Poiché può avere molte tensioni di ingresso, è realizzato utilizzando Q2, R19 e R20 come traslatore di livello di tensione. Segnale I_MOD.
X4 è il connettore dell'LCD esterno, è solo una connessione delle linee 5V rail, GND e I2C SCL-SDA.
Le linee I2C, SCL e SDA, sono condivise da IC2 (l'ADC) e l'LCD esterno, sono tirate su da R9 e R10.
R8 e Q1 formano il pilota della staffetta K1. K1 collega la tensione di uscita quando è alimentato. Con 0V in -CUT il relè è disalimentato, e con 5V in -CUT il relè è alimentato. D3 è il diodo a ruota libera per sopprimere le tensioni negative quando si taglia la tensione della bobina del relè.
Z1 è un soppressore di tensioni transitorie con una tensione nominale di 36V.
Passaggio 5: PCB del circuito del misuratore
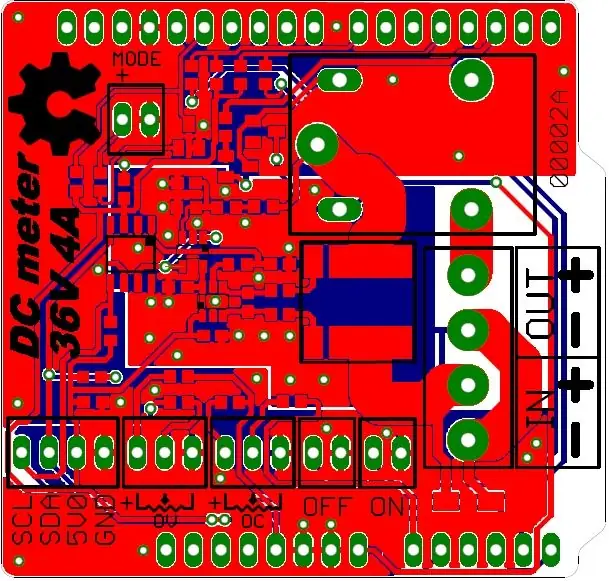
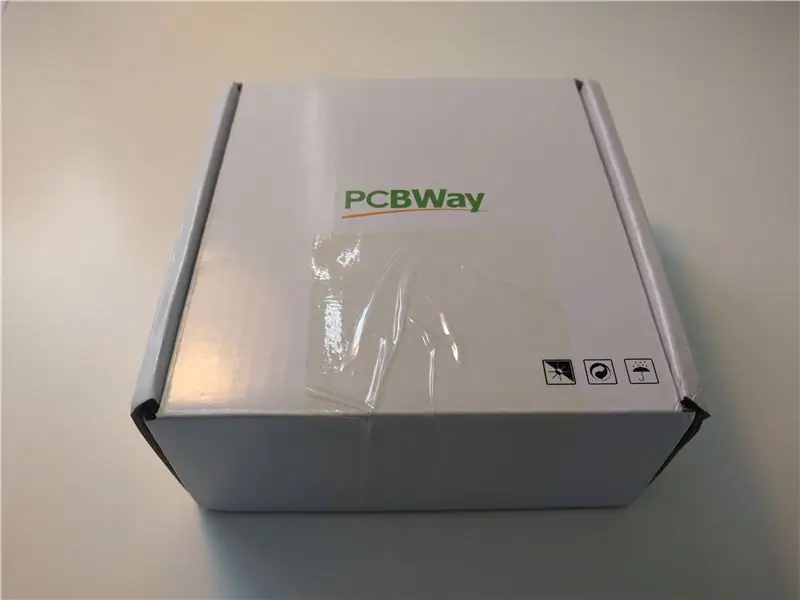
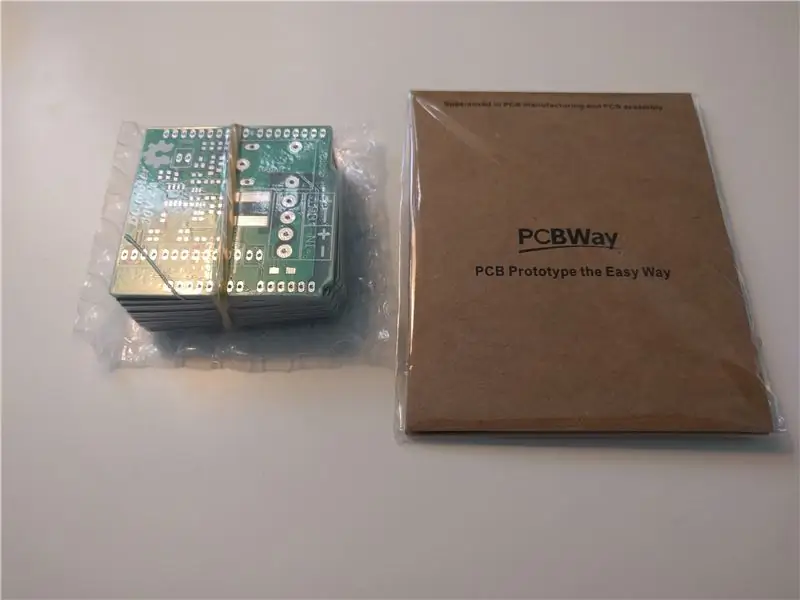
Ho usato la versione gratuita di Eagle sia per lo schema che per il PCB. Il PCB ha un design a doppia faccia spesso 1,6 che ha un piano di massa separato per il circuito analogico e il circuito digitale. Il design è piuttosto semplice. Ho preso da Internet un file dxf con le dimensioni del contorno e la posizione dei connettori pinhead di Arduino.
Inserisco i seguenti file:
- File eagle originali: 00002A.brd e 00002A.sch.
- File Gerber: 00002A.zip.
- E la BOM (Bill Of Materials) + guida all'assemblaggio: BOM_Assemby.pdf.
Ho ordinato il PCB a PCBWay (www.pcbway.com). Il prezzo era sorprendentemente basso: 33 dollari, spedizione inclusa, per 10 tavole arrivate in meno di una settimana. Posso condividere le schede rimanenti con i miei amici o utilizzarle in altri progetti.
C'è un errore nel design, ho messo un via toccando la serigrafia nella legenda 36V.
Passaggio 6: assemblaggio del circuito del misuratore
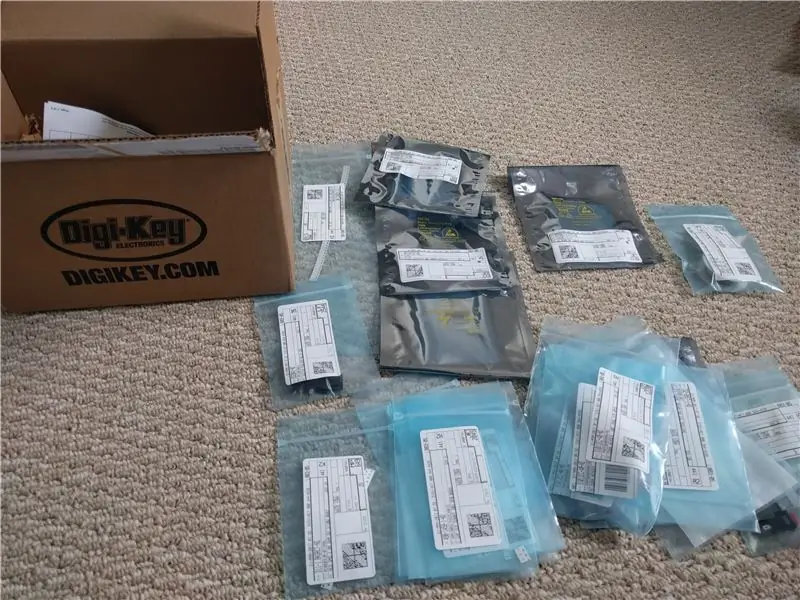
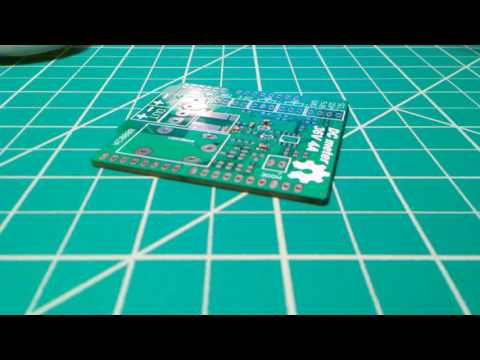
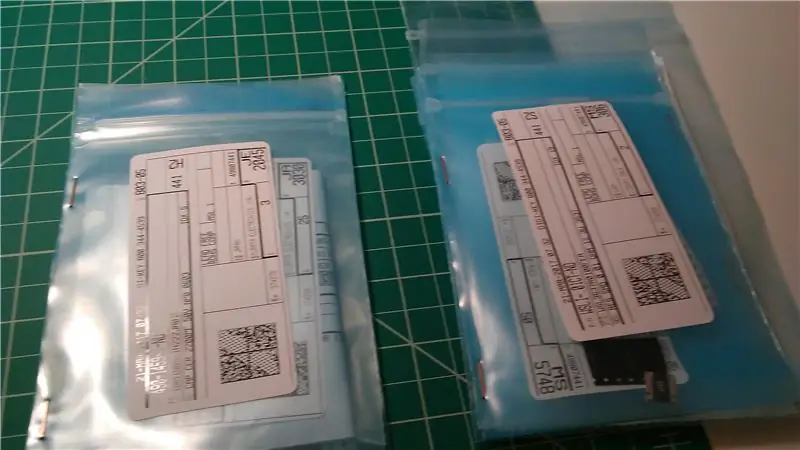
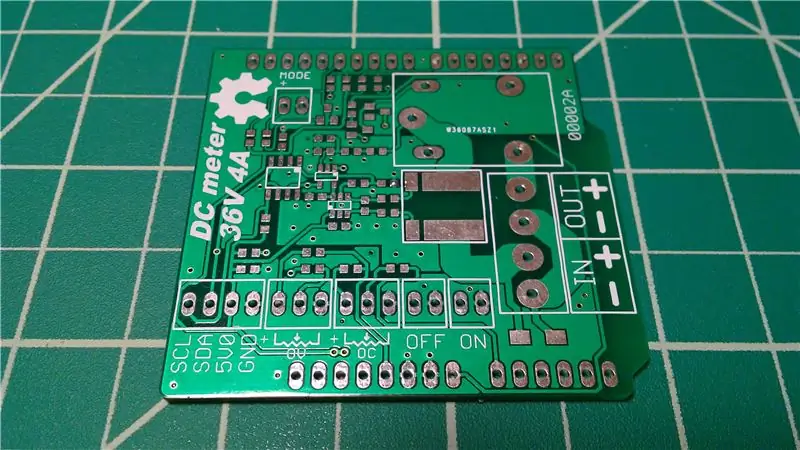
Sebbene la maggior parte delle parti siano SMT in questa scheda, può essere assemblata con un normale saldatore. Ho usato un Hakko FX888D-23BY, pinzette a punta fine, uno stoppino per saldatura e una saldatura da 0,02.
- Dopo aver ricevuto le parti, l'idea migliore è quella di ordinarle, ho ordinato condensatori e resistenze e pinzato le buste.
- Per prima cosa assemblare le piccole parti, iniziando da resistori e condensatori.
- Assemblare R4 (0R1) iniziando da uno dei quattro conduttori.
- Saldare il resto delle parti, in generale per SOT23, SOIC8, ecc. Il modo migliore è applicare prima la saldatura in un pad, saldare la parte al suo posto e quindi saldare il resto dei cavi. A volte la saldatura può unire molti pad insieme, in questo caso puoi usare il flusso e lo stoppino per saldatura per rimuovere la saldatura e pulire gli spazi vuoti.
- Assemblare il resto dei componenti del foro passante.
Passaggio 7: codice Arduino
Ho allegato il file DCmeter.ino. Tutto il programma è incluso in questo file tranne la libreria LCD “LiquidCrystal_I2C”. Il codice è altamente personalizzabile, in particolare la forma delle barre di avanzamento e i messaggi visualizzati.
Come tutti i codici arduino ha la funzione setup() eseguita la prima volta e la funzione loop() eseguita continuamente.
La funzione di configurazione configura il display, inclusi i caratteri speciali per la barra di avanzamento, avvia la macchina a stati MCP4322 e imposta per la prima volta il relè e la retroilluminazione LCD.
Non ci sono interruzioni, in ogni iterazione la funzione loop esegue i seguenti passaggi:
Ottenere il valore di tutti i segnali di ingresso I_ON, I_OFF, A_OC, A_OV e I_MOD. I_ON e I_OFF sono antirimbalzo. A_OC e A_OV vengono letti direttamente dall'ADC di Arduino e filtrati utilizzando la parte mediana delle ultime tre misurazioni. I_MOD viene letto direttamente senza antirimbalzo.
Controlla il tempo di accensione della retroilluminazione.
Eseguire la macchina a stati MCP3422. Ogni 5ms interroga l'MCP3422 per vedere se l'ultima conversione è terminata e in caso affermativo inizia la successiva, ottiene successivamente il valore di tensione e corrente presenti in uscita.
Se sono presenti nuovi valori di tensione e corrente in uscita dalla macchina a stati MCP3422, aggiorna lo stato dell'alimentazione in base alle misurazioni e aggiorna il display.
C'è un'implementazione del doppio buffer per aggiornare più velocemente il display.
Le seguenti macro possono essere regolate per altri progetti:
MAXVP: OV massimo in unità 1/100V.
MAXCP: OC massimo in unità 1/1000A.
DEBOUNCEHARDNESS: Numero di iterazioni con un valore consecutivo da indovinare corretto per I_ON e I_OFF.
LCD4x20 o LCD2x16: Compilazione per display 4x20 o 2x16, l'opzione 2x16 non è ancora implementata.
L'implementazione 4x20 mostra le seguenti informazioni: Nella prima riga la tensione di uscita e la corrente di uscita. Nella seconda riga una barra di avanzamento che rappresenta il valore di uscita relativo al setpoint di protezione sia per tensione che per corrente. Nella terza riga il setpoint di corrente per la protezione da sovratensione e la protezione da sovracorrente. Nella quarta riga lo stato attuale dell'alimentatore: CC ON (acceso in modalità corrente costante), CV ON (acceso in modalità tensione costante), OFF, OV OFF (spento indicando che l'alimentazione è andata via a causa di un OV), OC OFF (Off indica che l'alimentazione si è interrotta a causa di un OC).
Ho creato questo file per progettare i caratteri delle barre di avanzamento:
Passaggio 8: problemi termici
L'uso del dissipatore giusto è molto importante in questo assemblaggio perché il circuito di alimentazione non è autoprotetto contro il surriscaldamento.
Secondo la scheda tecnica, il transistor 2SD1047 ha una giunzione alla resistenza termica della custodia di Rth-j, c = 1.25ºC/W.
Secondo questo calcolatore web: https://www.myheatsinks.com/calculate/thermal-resi… la resistenza termica del dissipatore che ho acquistato è Rth-hs, aria = 0,61ºC/W. Suppongo che il valore effettivo sia inferiore perché il dissipatore di calore è collegato al case e anche il calore può essere dissipato in questo modo.
Secondo il venditore ebay, la conduttività termica del foglio isolante che ho acquistato è K = 20,9 W/(mK). Con questo, con uno spessore di 0,6mm, la resistenza termica è: R = L/K = 2,87e-5(Km2)/W. Quindi, il caso della resistenza termica al dissipatore di calore dell'isolatore per la superficie di 15 mm x 15 mm del 2SD1047 è: Rth-c, hs = 0,127ºC/W. Puoi trovare una guida per questi calcoli qui:
La potenza massima consentita per 150ºC nella giunzione e 25ºC nell'aria è: P = (Tj - Ta) / (Rth-j, c + Rth-hs, aria + Rth-c, hs) = (150 - 25) / (1,25 + 0,61 + 0,127) = 63 W.
La tensione di uscita del trasformatore è 21VAC a pieno carico, che fa una media di 24VDC dopo i diodi e il filtraggio. Quindi la dissipazione massima sarà P = 24V * 3A = 72W. Tenendo conto che la resistenza termica del dissipatore di calore è leggermente inferiore a causa della dissipazione dell'involucro metallico, ho pensato che fosse sufficiente.
Passaggio 9: allegato
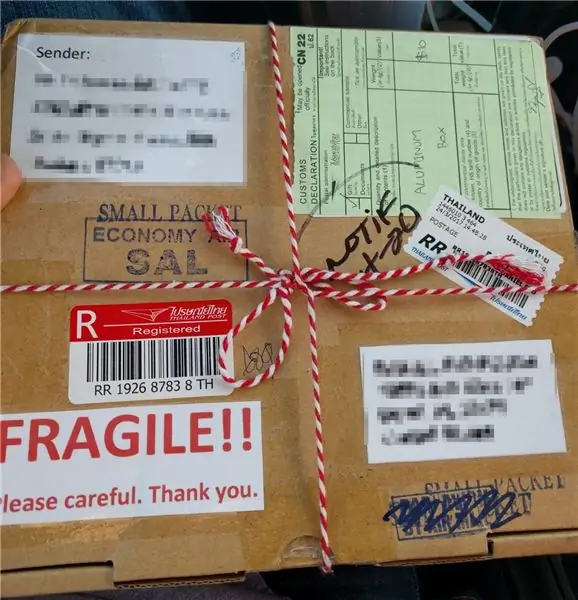
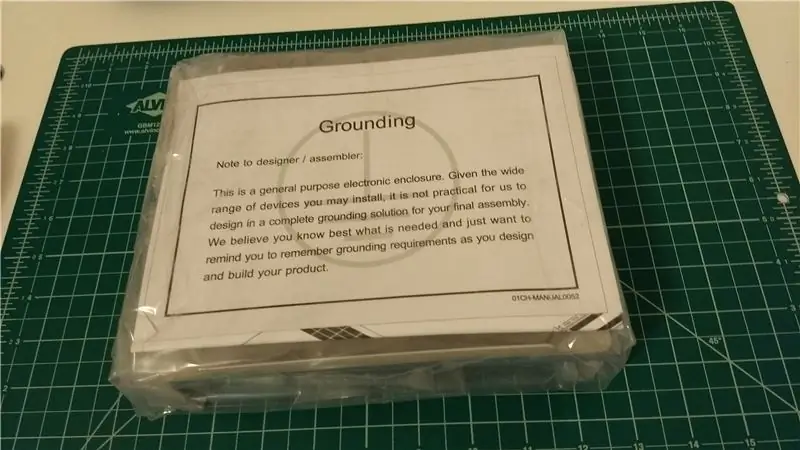
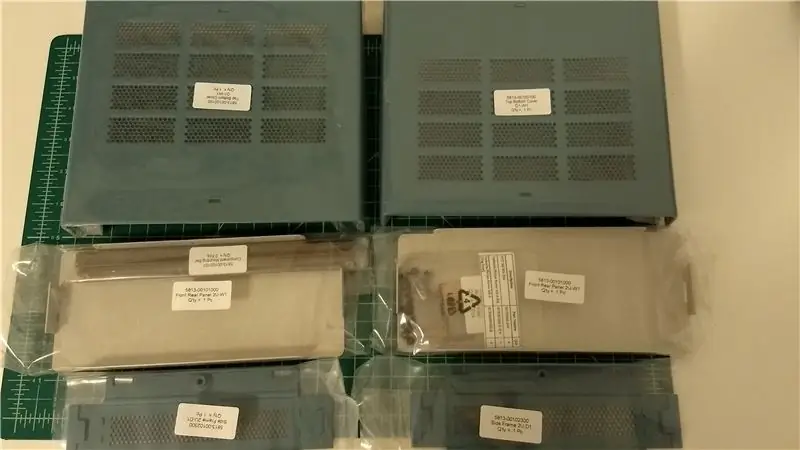
La custodia, inclusa la spedizione, è la parte più costosa dell'alimentatore. Ho trovato questo modello su ebay, da Cheval, un produttore Thay: https://www.chevalgrp.com/standalone2.php. In effetti, il venditore ebay era thailandese.
Questa scatola ha un ottimo rapporto qualità-prezzo ed è arrivata abbastanza ben confezionata.
Passaggio 10: meccanizzazione del pannello frontale
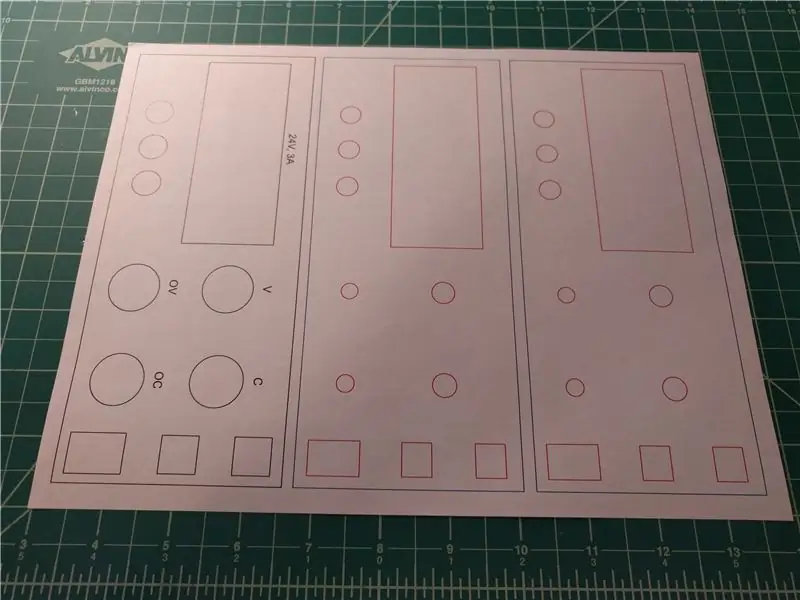
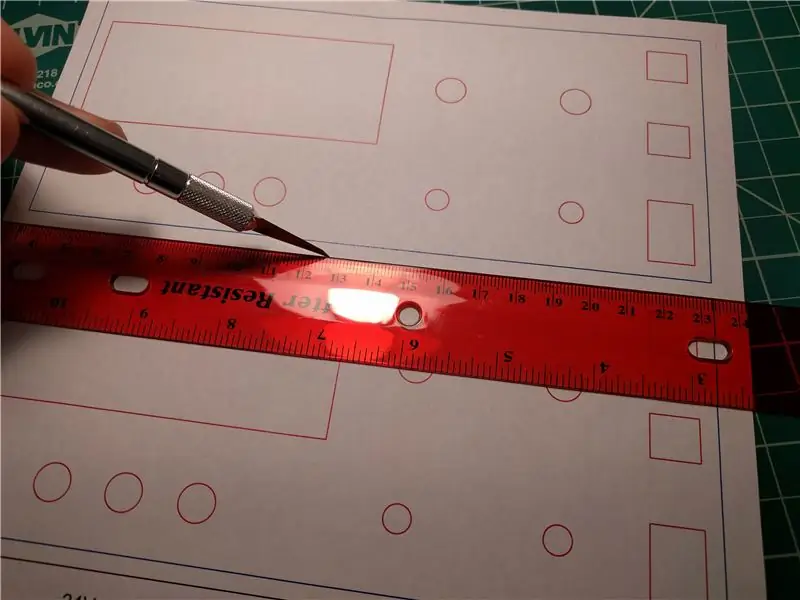
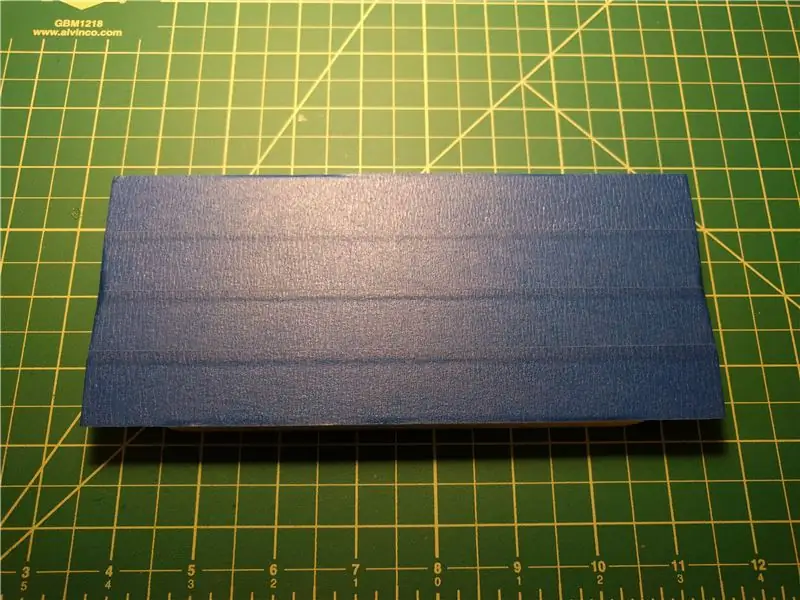
L'opzione migliore per meccanizzare e incidere il pannello frontale è utilizzare un router come questo https://shop.carbide3d.com/products/shapeoko-xl-k… o realizzare una copertura di plastica personalizzata con PONOKO, ad esempio. Ma siccome non ho il router e non volevo spendere molti soldi ho deciso di farlo alla vecchia maniera: tagliando, rifilando con file e usando lettere di trasferimento per il testo.
Ho allegato un file Inkscape con lo stencil: frontPanel.svg.
- Taglia lo stampino.
- Coprire il pannello con nastro adesivo.
- Incolla lo stencil sul nastro del pittore. Ho usato una colla stick.
- Segna la posizione dei trapani.
- Praticare dei fori per consentire al seghetto da traforo o alla lama della sega da traforo di entrare nei tagli interni.
- Taglia tutte le forme.
- Taglia con un file. Nel caso di fori tondi per potenziometri e morsetti non è necessario utilizzare la sega prima della limatura. Nel caso del foro di visualizzazione il taglio del file deve essere il migliore possibile perché questo bordo si vedrà.
- Rimuovi lo stencil e il nastro adesivo.
- Segna la posizione dei testi con una matita.
- Trasferisci le lettere.
- Rimuovi i segni a matita con una gomma.
Passaggio 11: meccanizzazione del pannello posteriore

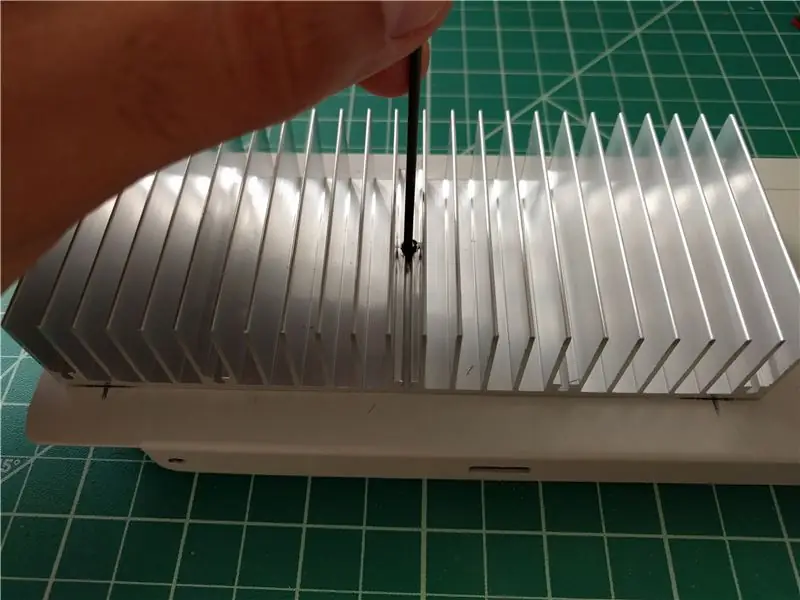
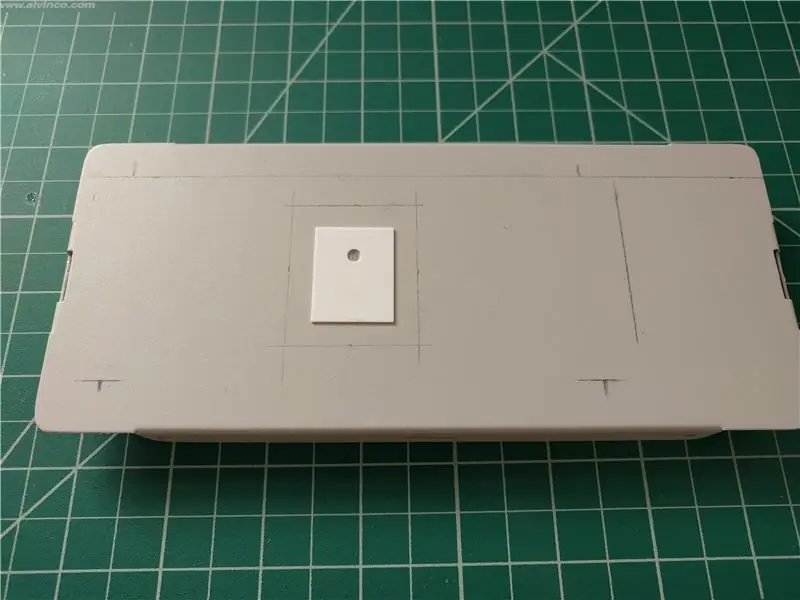
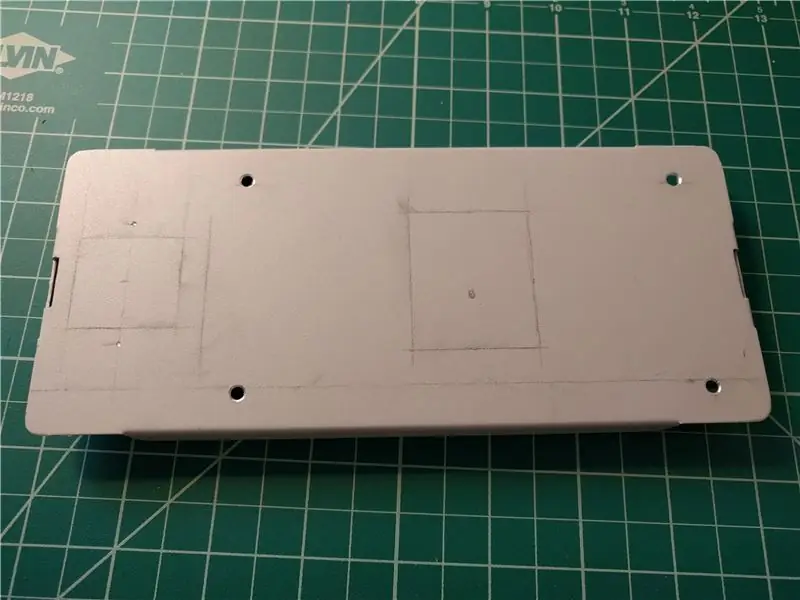
- Segna la posizione del dissipatore, compreso il foro per il transistor di potenza e la posizione delle viti di fissaggio.
- Segnare il foro per l'accesso al dissipatore dall'interno dell'involucro dell'alimentatore, ho usato l'isolante come riferimento.
- Segna il foro per il connettore IEC.
- Forare il contorno delle forme.
- Praticare i fori per le viti.
- Tagliare le forme con le pinze da taglio.
- Ritaglia le forme con un file.
Passaggio 12: assemblaggio del pannello frontale
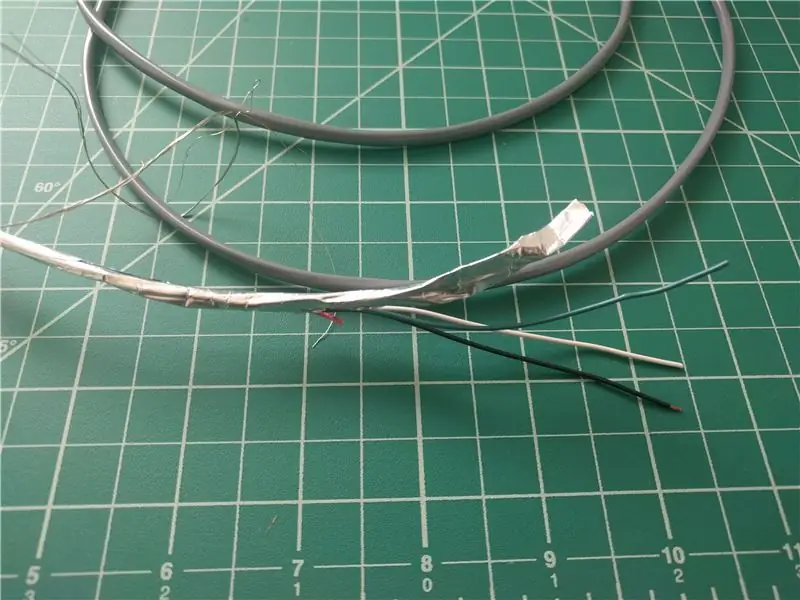
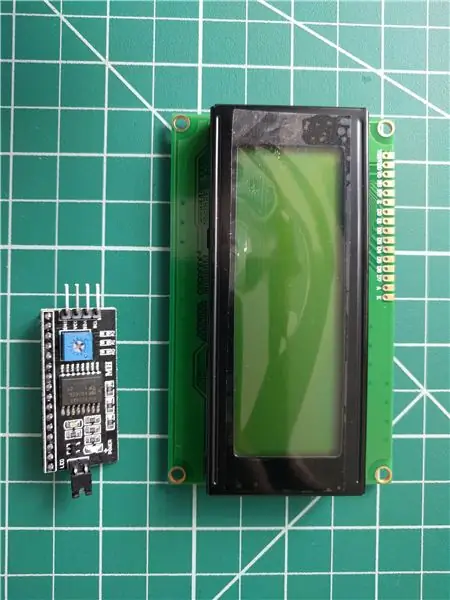
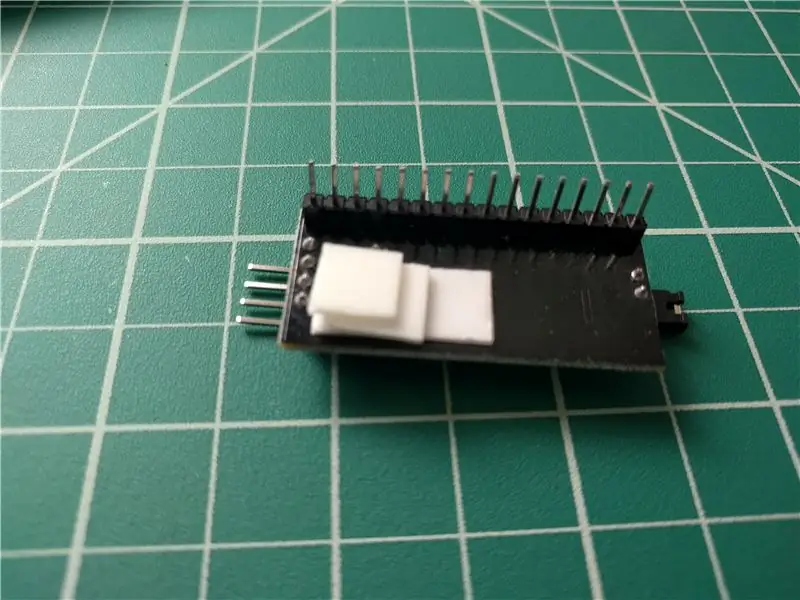
- Estrarre un cavo multiconduttore da rottami per ottenere cavi.
- Costruisci il gruppo LCD saldando l'I2C all'interfaccia parallela.
- Costruisci il "connettore molex", il cavo e il tubo termoretraibile per: potenziometri, pulsanti e LCD. Rimuovere qualsiasi protuberanza nei potenziometri.
- Rimuovere l'anello di indicazione delle manopole.
- Tagliare l'asta dei potenziometri alla dimensione della manopola. Ho usato un pezzo di cartone come misuratore.
- Collegare i pulsanti e il pulsante di accensione.
- Assemblare i potenziometri e installare le manopole, i potenziometri multigiro che ho acquistato hanno un albero da di pollice e i modelli a un giro hanno un albero da 6 mm. Ho usato le rondelle come distanziatori per tagliare la distanza dei potenziometri.
- Avvitare i pali di rilegatura.
- Metti del nastro biadesivo nell'LCD e attaccalo al pannello.
- Saldare i fili positivo e negativo ai morsetti.
- Assemblare il capocorda del terminale GND nel morsetto verde.
Passaggio 13: assemblaggio del pannello posteriore
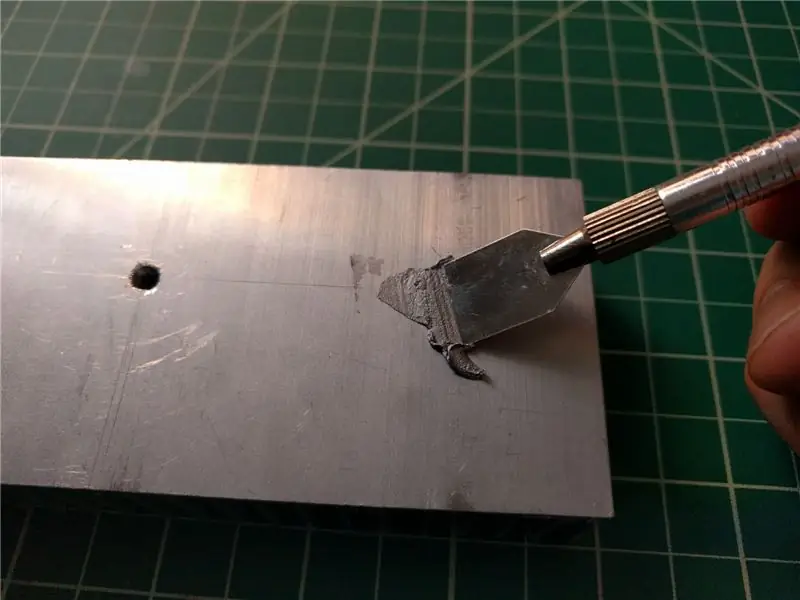
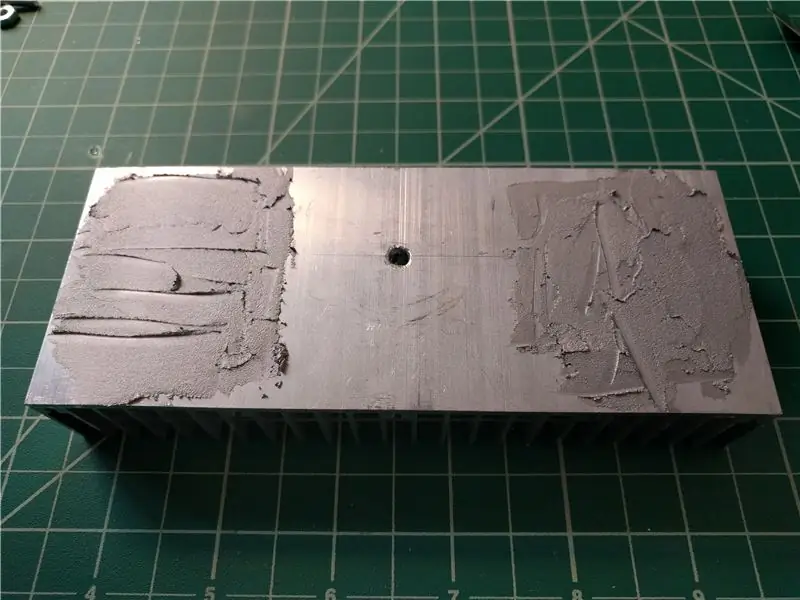
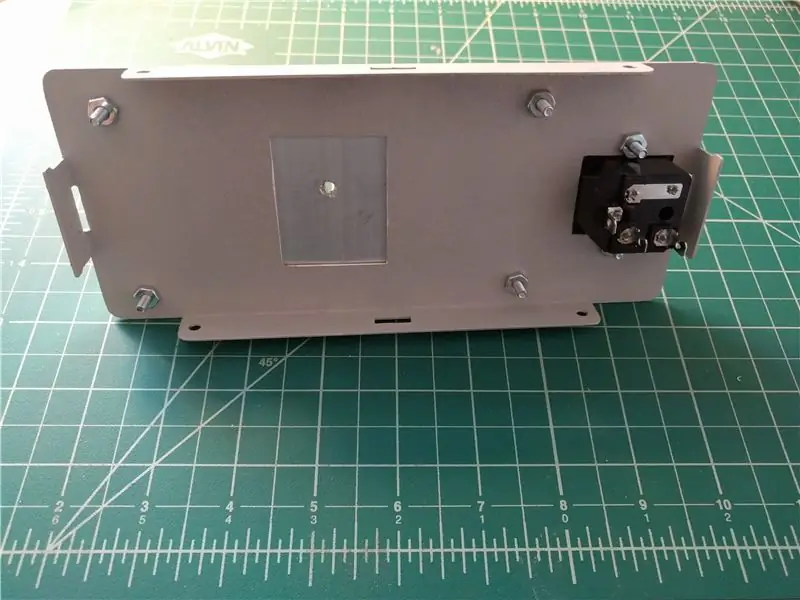
- Avvitare il dissipatore di calore al pannello posteriore, sebbene la vernice sia un isolante termico, ho messo del grasso per dissipatore di calore per aumentare il trasferimento di calore dal dissipatore di calore all'involucro.
- Assemblare il connettore IEC.
- Posizionare i distanziali adesivi utilizzando il circuito del kit di alimentazione.
- Avvitare il transistor di potenza e l'isolatore, deve esserci grasso termico su ogni superficie.
- Assemblare il 7812 per alimentare l'arduino, è rivolto verso il case per consentire la dissipazione del calore, utilizzando una delle viti che trattengono il dissipatore. Avrei dovuto usare una rondella di plastica come questa https://www.ebay.com/itm/100PCS-TO-220-Transistor-… ma ho finito per usare lo stesso isolante del transistor di potenza e un pezzo piegato del case.
- Collegare il transistor di potenza e il 7812 al circuito di alimentazione.
Passaggio 14: assemblaggio finale e cablaggio
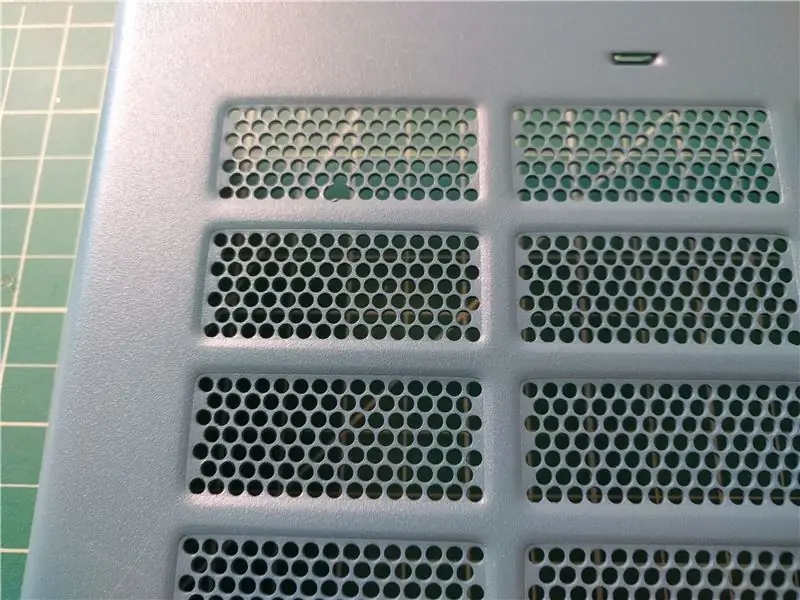
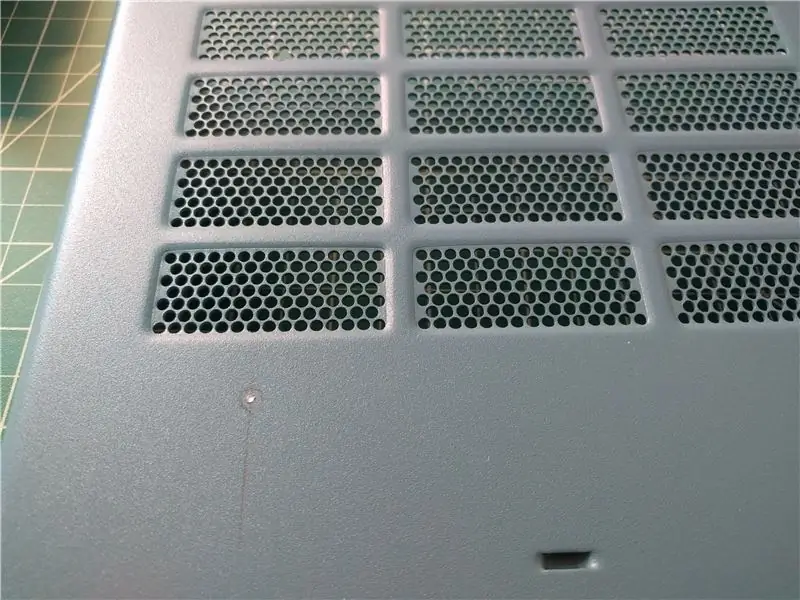
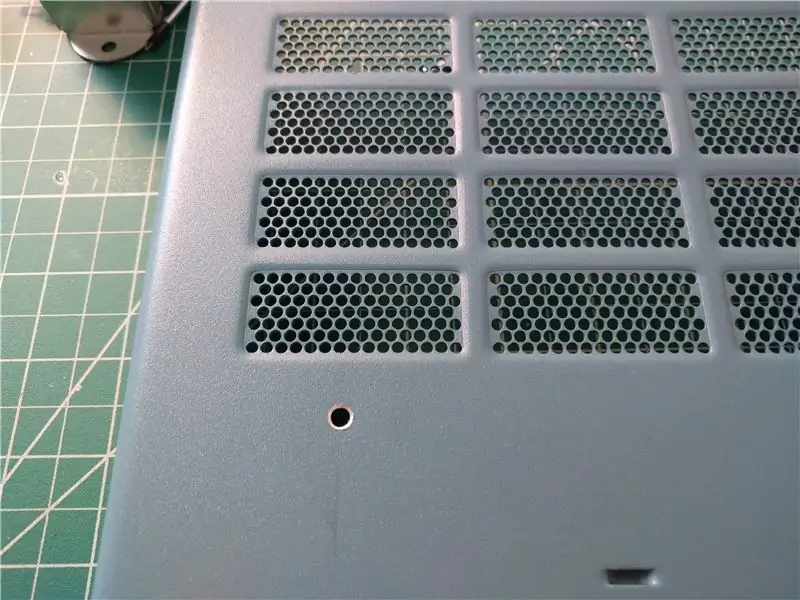
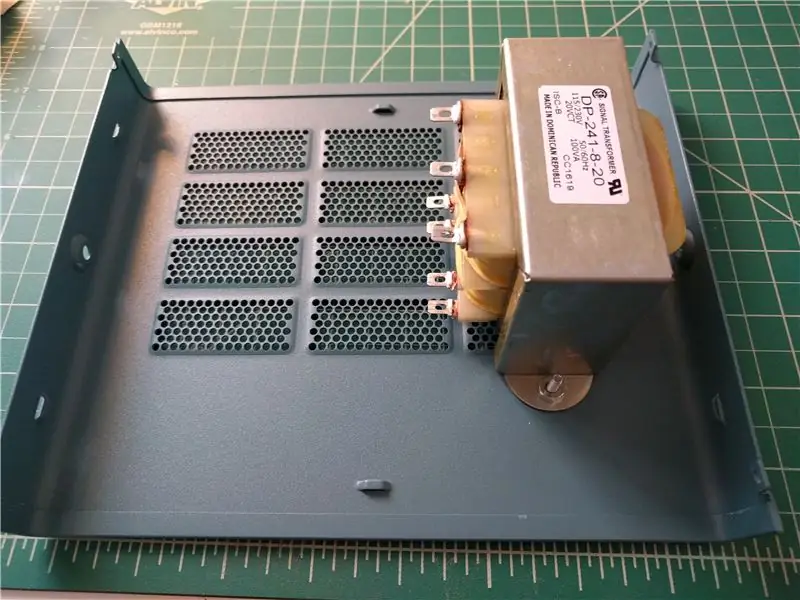
- Segna e fai i fori per il trasformatore.
- Assemblare il trasformatore.
- Attacca le gambe adesive della custodia.
- Attaccare il circuito del misuratore CC utilizzando distanziatori adesivi.
- Raschiare la vernice per avvitare il capocorda GND.
- Realizzare i cavi assemblati della tensione di rete, tutte le terminazioni sono Faston da 3/16”. Ho usato un tubo termoretraibile per isolare le terminazioni.
- Tagliare la parte anteriore del supporto della custodia sul lato destro per ottenere spazio per il pulsante di accensione.
- Collegare tutti i cavi secondo la guida di montaggio.
- Installare il fusibile (1A).
- Posizionare il potenziometro della tensione di uscita (potenziometro VO), al minimo CCW e regolare la tensione di uscita il più vicino possibile a zero volt utilizzando il potenziometro di regolazione fine multigiro del circuito di alimentazione vkmaker.
- Assemblare la custodia.
Passaggio 15: miglioramenti e ulteriore lavoro
Miglioramenti
- Utilizzare rondelle in stile coltivatore per evitare che le viti si allentino con le vibrazioni, in particolare le vibrazioni del trasformatore.
- Dipingi il pannello frontale con vernice trasparente per evitare che le lettere vengano cancellate.
Ulteriore lavoro:
- Aggiungi un connettore USB come questo: https://www.ebay.com/itm/Switchcraft-EHUSBBABX-USB-… nel pannello posteriore. Utile per aggiornare il codice senza smontare o per fare un piccolo ATE controllando le funzioni On Off, ottenere lo stato e misurare tramite PC.
- Effettua la compilazione del codice LCD 2x16.
- Realizzare un nuovo circuito di alimentazione, anziché utilizzare il kit vkmaker, con controllo digitale della tensione e della corrente di uscita.
- Eseguire i test adeguati per caratterizzare l'alimentazione.
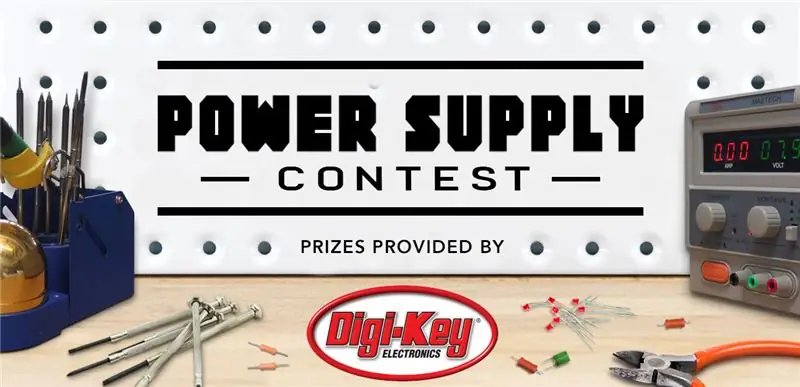
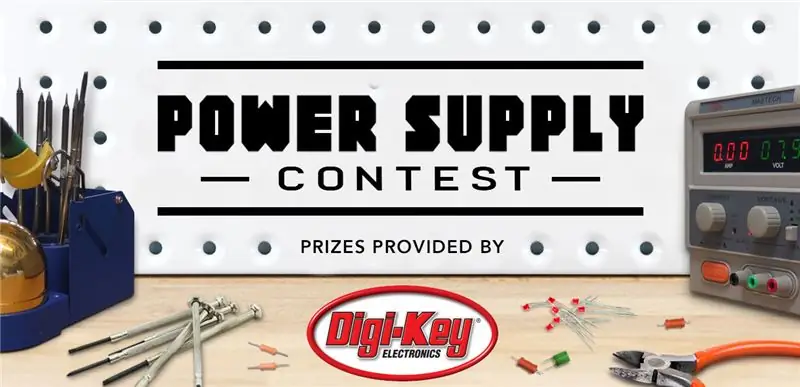
Primo Premio al Concorso Alimentatori
Consigliato:
Alimentatore da banco da laboratorio fai-da-te [Build + Test]: 16 passaggi (con immagini)
![Alimentatore da banco da laboratorio fai-da-te [Build + Test]: 16 passaggi (con immagini) Alimentatore da banco da laboratorio fai-da-te [Build + Test]: 16 passaggi (con immagini)](https://i.howwhatproduce.com/images/002/image-4655-j.webp)
Alimentatore da banco da laboratorio fai-da-te [Build + Test]: in questo tutorial / video ti mostrerò come creare il tuo alimentatore da banco variabile che può fornire 30 V 6 A 180 W (10 A MAX sotto il limite di potenza). Limite di corrente minimo 250-300 mA. Inoltre vedrai precisione, carico, protezione e altri
Costruisci il tuo alimentatore da banco variabile da laboratorio: 4 passaggi (con immagini)
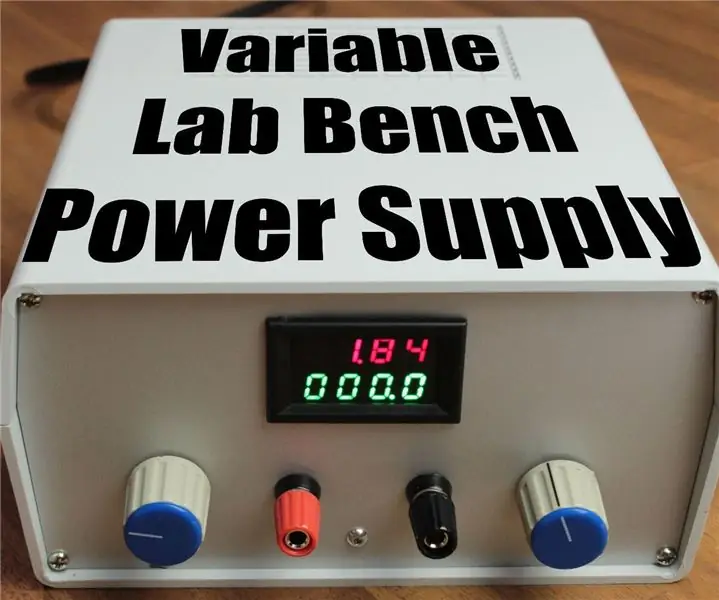
Costruisci il tuo alimentatore variabile per banco da laboratorio: in questo progetto ti mostrerò come ho combinato un LTC3780, che è un potente convertitore Step Up/Step Down da 130 W, con un alimentatore da 12 V 5 A per creare un alimentatore da banco regolabile (0,8 V-29,4 V | 0,3 A-6 A). Le prestazioni sono abbastanza buone in compa
Alimentatore da laboratorio dal vecchio ATX: 8 passaggi (con immagini)
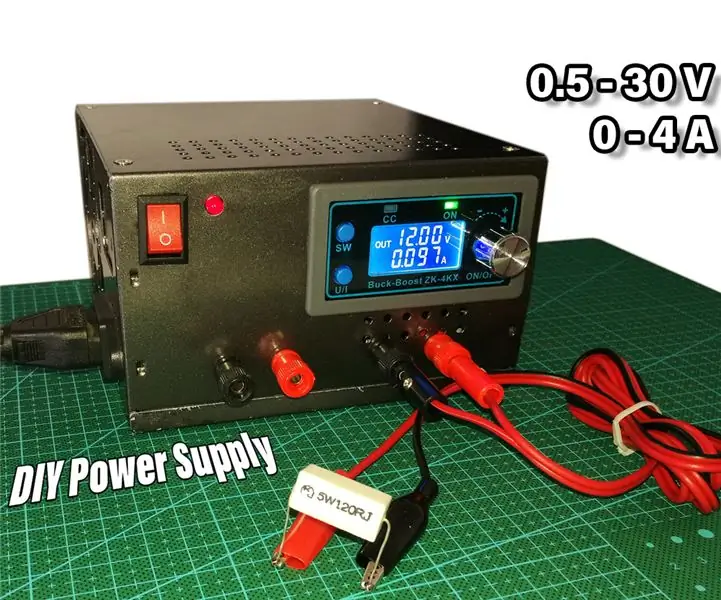
Alimentatore da laboratorio dal vecchio ATX: non ho un alimentatore per il laboratorio da molto tempo, ma a volte sarebbe stato necessario. Oltre alla tensione regolabile è molto utile anche limitare la corrente di uscita, ad es. in caso di test di PCB di nuova creazione. Così io decisi
Alimentatore da banco da laboratorio fai da te: 9 passaggi (con immagini)
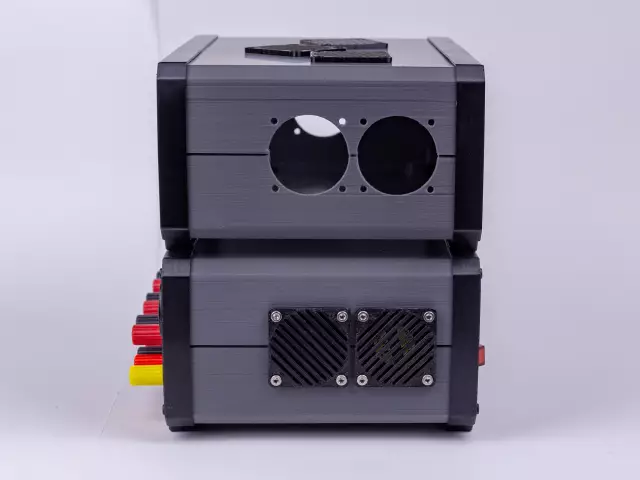
Alimentatore da banco da laboratorio fai-da-te: ciao a tutti! Benvenuti in questo Instructable, dove vi mostrerò come ho realizzato questo alimentatore dall'aspetto semplice ma fantastico! Ho un video sull'argomento e consiglierei di guardarlo. Contiene passaggi chiari e tutte le informazioni necessarie per fare
Convertire un alimentatore per computer in un alimentatore da laboratorio variabile da banco: 3 passaggi
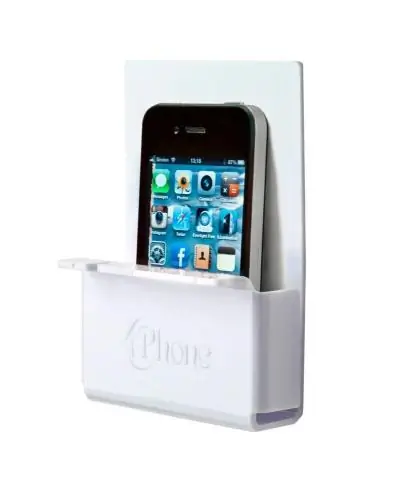
Conversione di un alimentatore per computer in un alimentatore da laboratorio variabile da banco: i prezzi oggi per un alimentatore da laboratorio superano ben $ 180. Ma si scopre che un alimentatore per computer obsoleto è invece perfetto per il lavoro. Con questi ti costano solo $ 25 e hanno protezione da cortocircuito, protezione termica, protezione da sovraccarico e