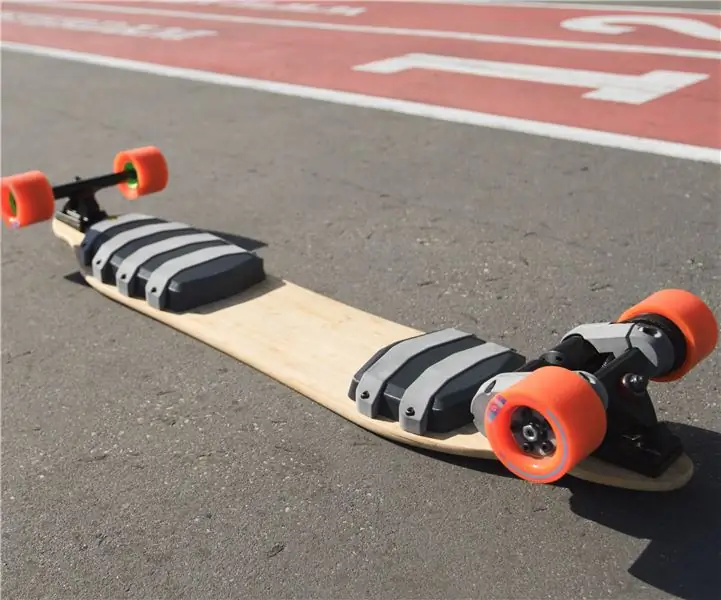
Sommario:
2025 Autore: John Day | [email protected]. Ultima modifica: 2025-01-23 14:49
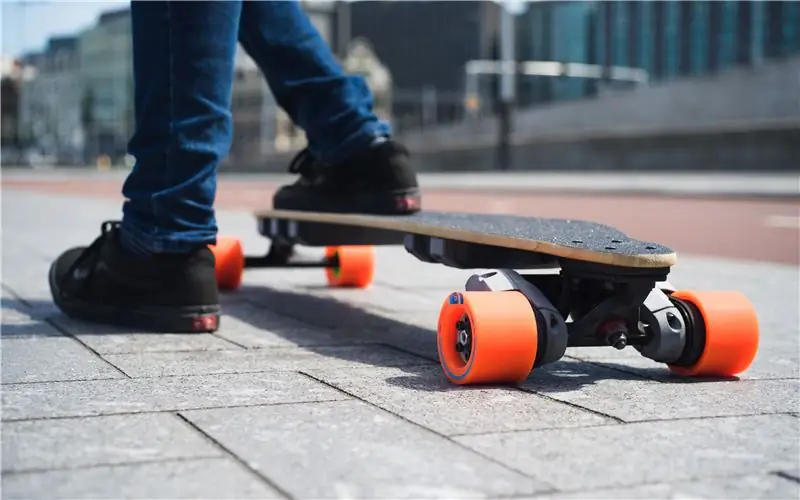
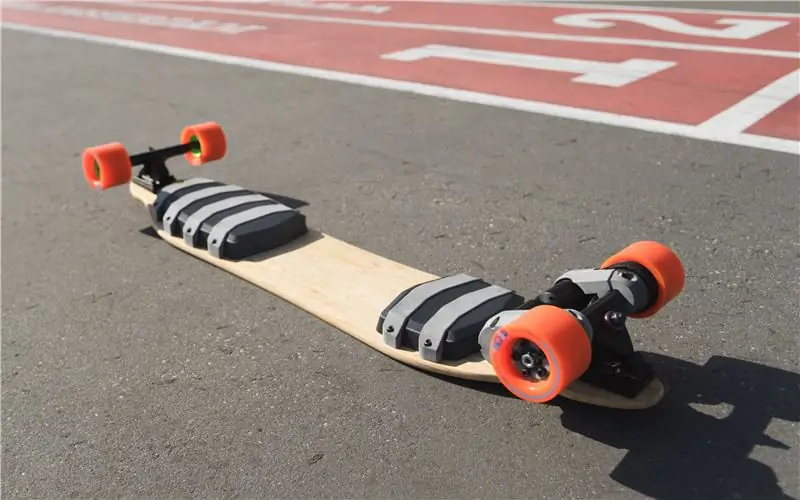
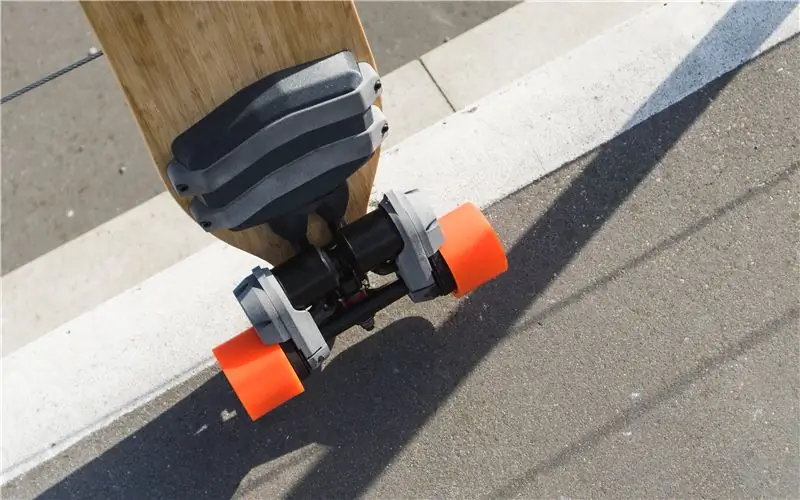
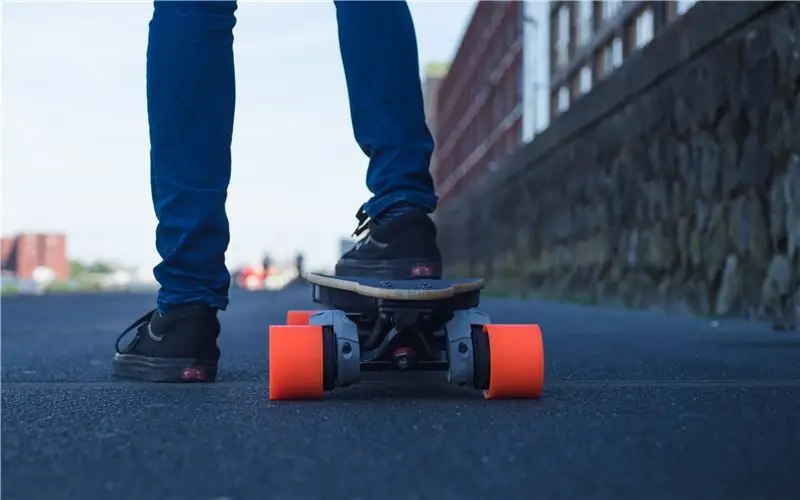
Questo Instructable è una panoramica del processo di costruzione della Fusion E-Board che ho progettato e costruito mentre lavoravo a 3D Hubs. Il progetto è stato commissionato per promuovere la nuova tecnologia HP Multi-Jet Fusion offerta da 3D Hubs e per mostrare più tecnologie di stampa 3D e come possono essere efficacemente combinate.
Ho progettato e realizzato un longboard motorizzato elettrico, che può essere utilizzato per tragitti brevi o moderati o abbinato ai mezzi pubblici per offrire un'autonomia di viaggio molto più ampia. Ha un'elevata velocità massima, è molto maneggevole ed è facilmente trasportabile quando non è in uso.
Passaggio 1: processo di progettazione
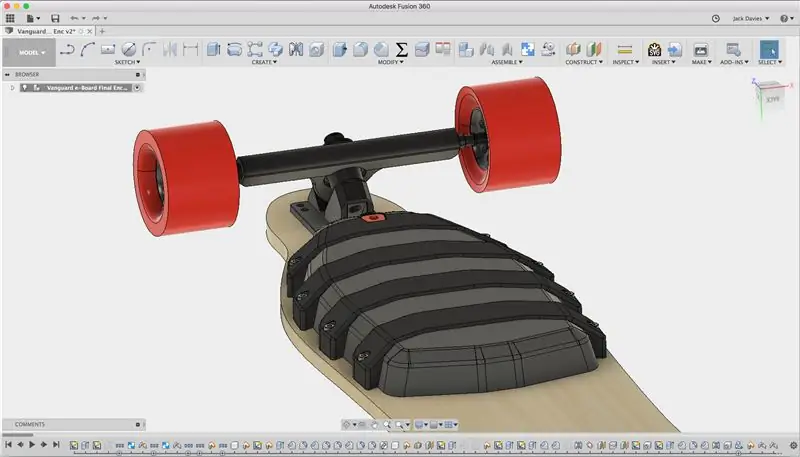
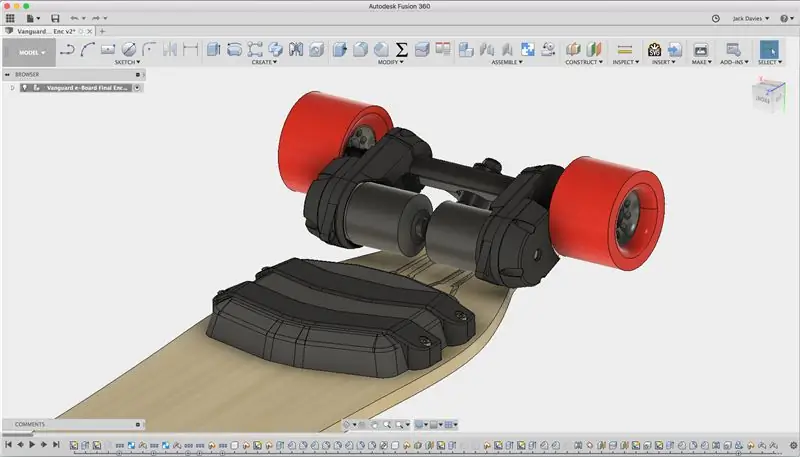
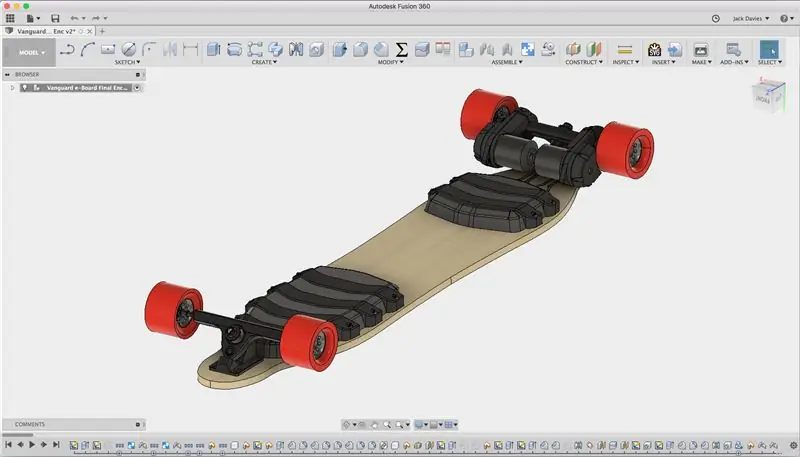
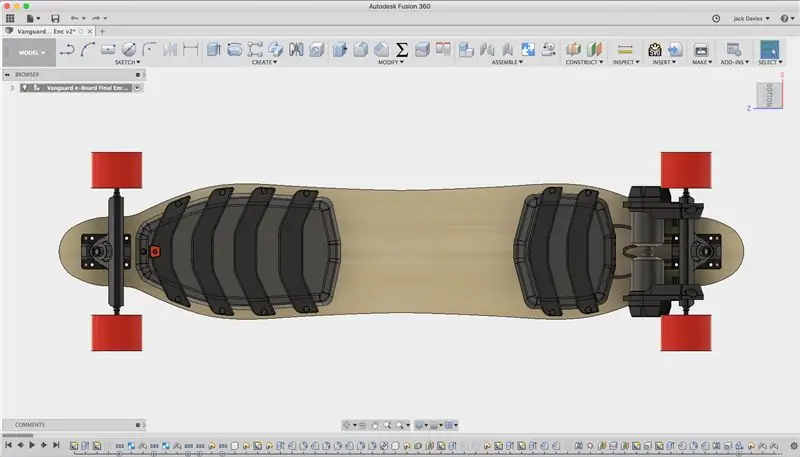
Ho iniziato il progetto individuando i principali componenti standard del longboard; camion, ponte e ruote. Queste erano parti standard, quindi le ho usate come punto di partenza del design. La prima fase è stata la progettazione della trasmissione, che include i supporti del motore, la configurazione degli ingranaggi e alcune modifiche ai camion. Le dimensioni e la posizione dei supporti del motore avrebbero dettato le dimensioni e la posizione delle custodie, quindi era importante che questo fosse completato per primo. Ho calcolato i requisiti di velocità massima e coppia desiderati che poi mi hanno permesso di selezionare i motori e la batteria per la scheda. È stato anche calcolato il rapporto di trasmissione e sono state selezionate le dimensioni della puleggia, insieme alla lunghezza della cinghia di trasmissione. Questo mi ha permesso di calcolare la dimensione corretta dei supporti del motore che hanno assicurato una cinghia ben tesa.
La fase successiva è stata quella di progettare gli alloggiamenti della batteria e del controller di velocità (ESC). Il mazzo selezionato è prevalentemente composto da bambù, quindi è abbastanza flessibile, piegandosi sostanzialmente nel mezzo. Questo ha i vantaggi di essere comodo da guidare, in quanto assorbe le asperità della strada e non le trasferisce al ciclista. Tuttavia, ciò significa anche che è necessario un involucro diviso per alloggiare la batteria e l'elettronica, poiché un involucro a lunghezza intera non sarebbe in grado di flettersi con la scheda e sarebbe in contatto con il suolo durante il funzionamento. I regolatori di velocità elettronici (ESC) sono stati posizionati più vicini ai motori a causa di vincoli elettrici. Poiché i motori sono collegati tramite i carrelli, la posizione cambia durante le svolte, quindi l'involucro doveva essere progettato per consentire lo spazio libero dei motori.
Il sistema di batterie era posto all'altra estremità del ponte e ospitava l'elettronica relativa alla potenza. Ciò includeva il pacco batteria, composto da 20 celle agli ioni di litio 18650, il sistema di gestione della batteria, l'interruttore di accensione/spegnimento e la presa di ricarica.
Ho utilizzato Autodesk Fusion360 per l'intero processo di progettazione, questo software mi ha permesso di modellare rapidamente i componenti all'interno dell'assieme principale, il che ha accelerato notevolmente i tempi di sviluppo. Ho anche utilizzato le funzionalità di simulazione in Fusion360 per assicurarmi che le parti fossero abbastanza resistenti, in particolare i supporti del motore. Ciò mi ha permesso di ridurre effettivamente le dimensioni dei supporti poiché ho potuto verificare i requisiti di resistenza e deflessione e rimuovere il materiale pur mantenendo un fattore di sicurezza appropriato. Dopo che il processo di progettazione è stato completato, è stato molto facile esportare le singole parti per la stampa 3D.
Passaggio 2: trasmissione
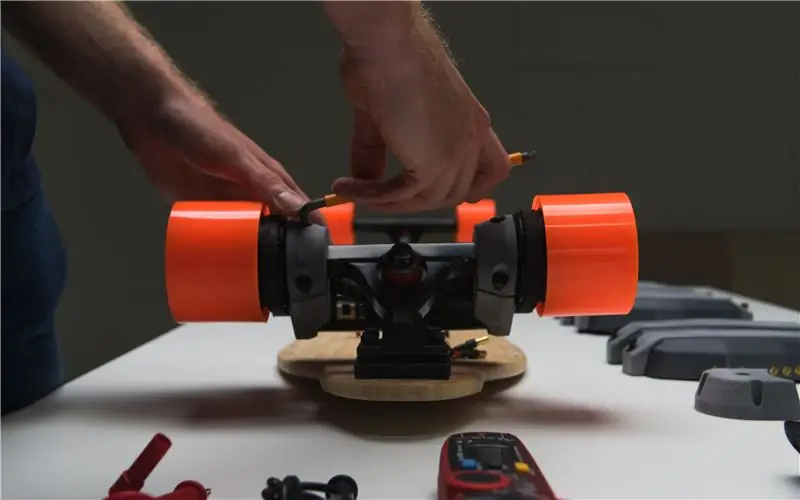
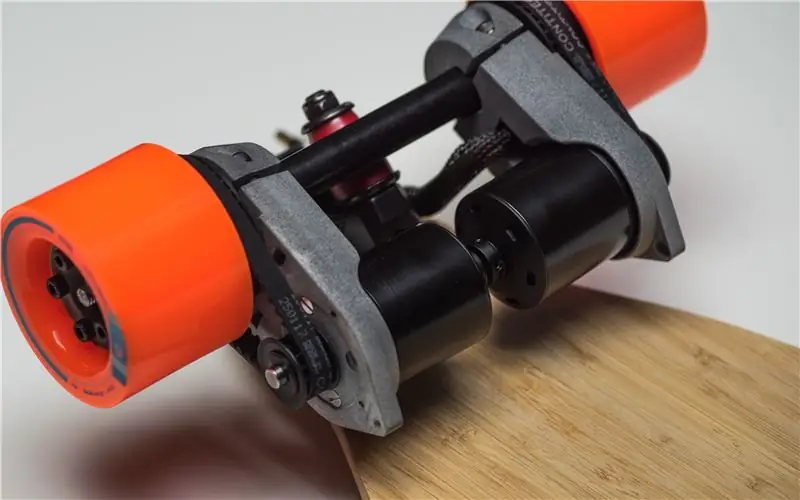
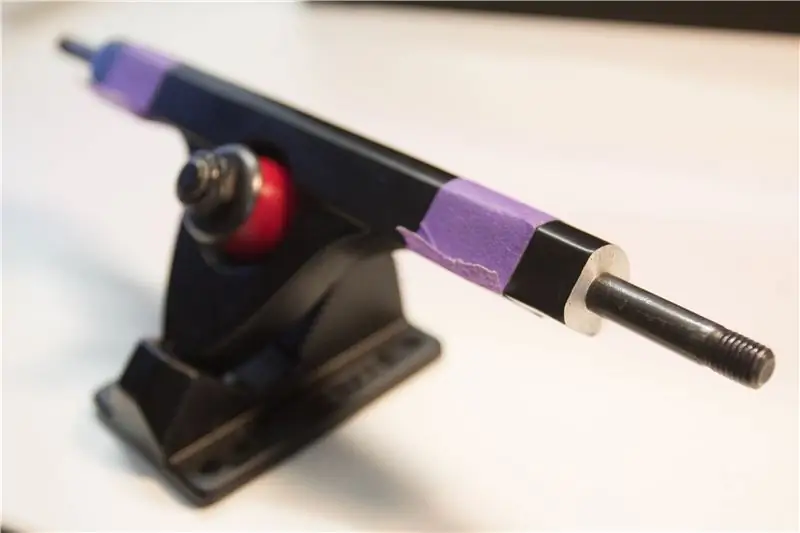
Ho completato prima la costruzione della trasmissione, per garantire uno spazio adeguato per l'alloggiamento dell'elettronica. Ho selezionato i camion Calibre da utilizzare in quanto hanno un profilo quadrato perfetto per il fissaggio dei supporti del motore. Tuttavia, l'asse era leggermente troppo corto per consentire l'utilizzo dei due motori sullo stesso camion, quindi avevo bisogno di estenderlo per consentire il montaggio delle ruote.
Ho raggiunto questo obiettivo tagliando parte del corpo del gancio del camion in alluminio, esponendo più assale in acciaio. Ho quindi tagliato la maggior parte dell'asse, lasciando circa 10 mm che avrei potuto filettare con un dado M8.
Un accoppiatore potrebbe quindi essere avvitato e un altro perno filettato aggiunto a quello, estendendo efficacemente l'asse. Ho usato il composto di fissaggio Loctite 648 per fissare in modo permanente l'accoppiatore e il nuovo asse per assicurarmi che non si svitasse durante l'uso. Ciò ha permesso ai due motori di adattarsi al camion e ha fornito molto spazio per le ruote.
La trasmissione è stata principalmente stampata utilizzando la tecnologia HP Multi-Jet Fusion, per garantire rigidità e resistenza durante le accelerazioni e le frenate elevate, dove sarebbero state trasferite le forze maggiori.
Per il bloccaggio delle ruote posteriori è stata progettata una puleggia speciale, che è stata poi collegata alla puleggia del motore con una cinghia HTD 5M. È stata aggiunta una copertura stampata in 3D per fornire protezione al gruppo della puleggia.
Passaggio 3: custodie per nervature
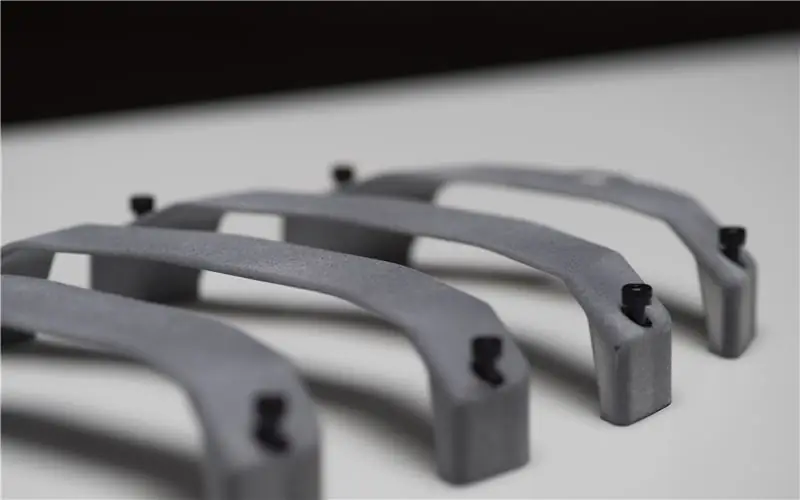
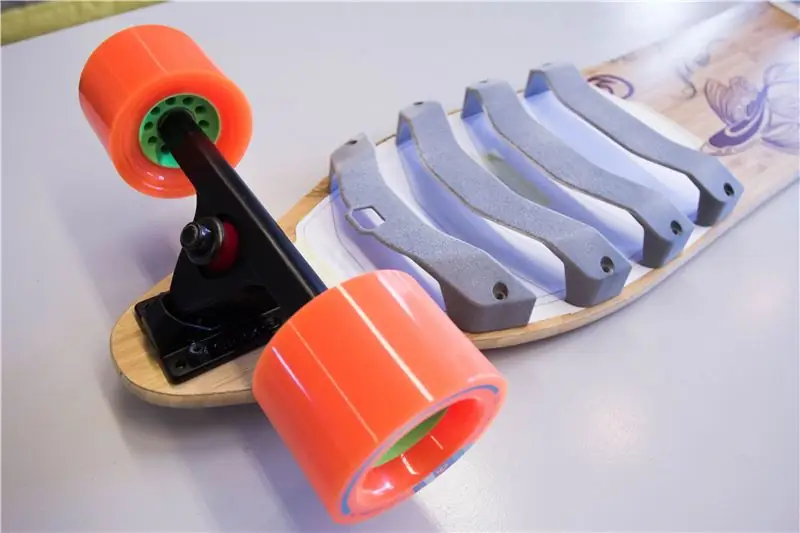
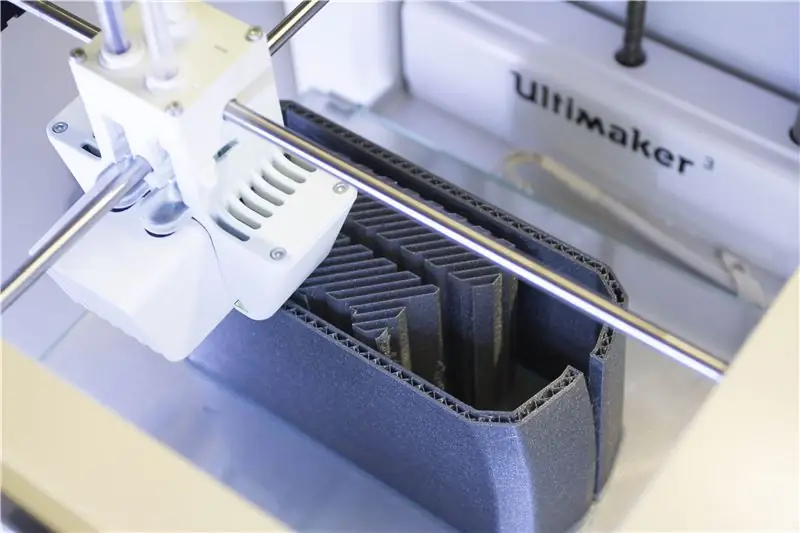
Una delle principali decisioni progettuali che ho preso è stata quella di separare le custodie, il che ha portato a un aspetto pulito e ha consentito al ponte flessibile di funzionare senza alcuna rigidità aggiuntiva dalle custodie. Volevo trasmettere gli aspetti funzionali della tecnologia HP Multi Jet Fusion, quindi ho deciso di stampare in FDM il corpo principale delle custodie riducendo i costi, quindi ho utilizzato le parti HP per supportarle e fissarle al ponte. Ciò ha fornito un'estetica interessante pur essendo molto funzionale.
Le custodie stampate FDM sono state divise a metà per facilitare la stampa poiché il materiale di supporto potrebbe essere eliminato dalla superficie esterna. La splitline è stata posizionata con cura per garantire che fosse nascosta dalla parte HP quando fissata alla scheda. Sono stati aggiunti i fori per le connessioni del motore e i connettori a proiettile placcati in oro sono stati incollati in posizione per
Gli inserti filettati sono stati incorporati nel ponte di bambù per fissare le recinzioni alla tavola e sono stati levigati a filo con la superficie della tavola per garantire che non vi fosse spazio tra il ponte e il recinto.
Passaggio 4: elettronica
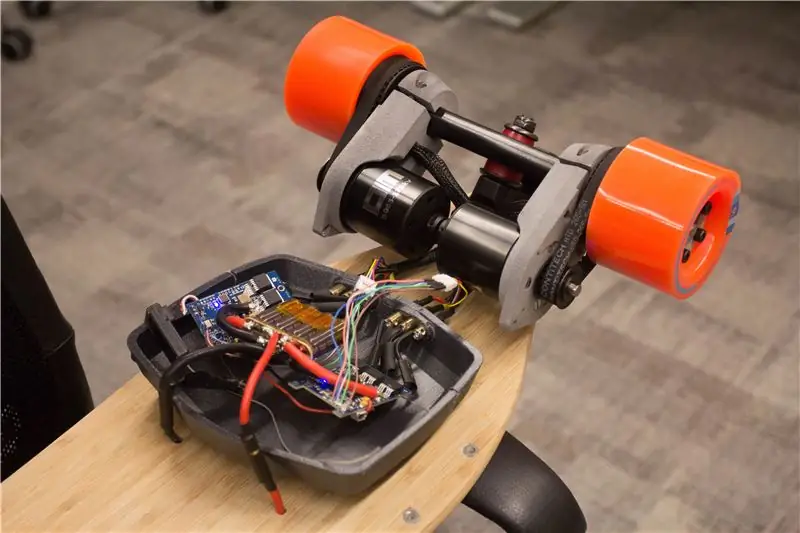
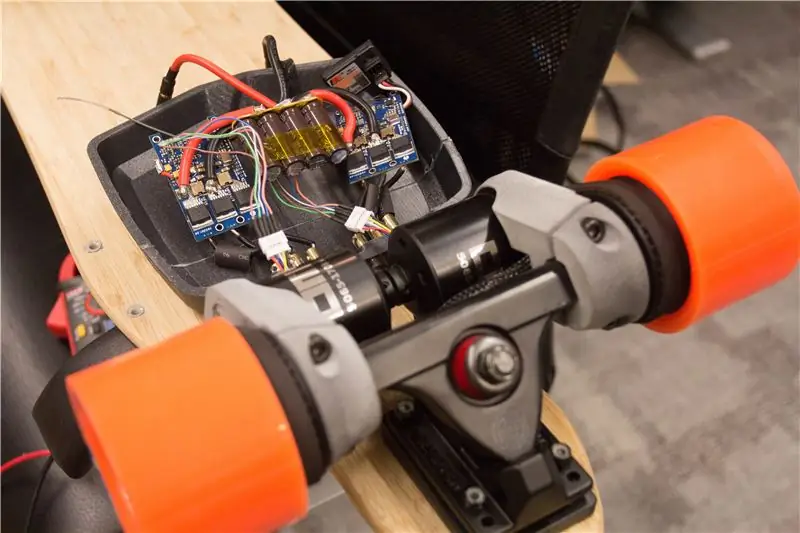
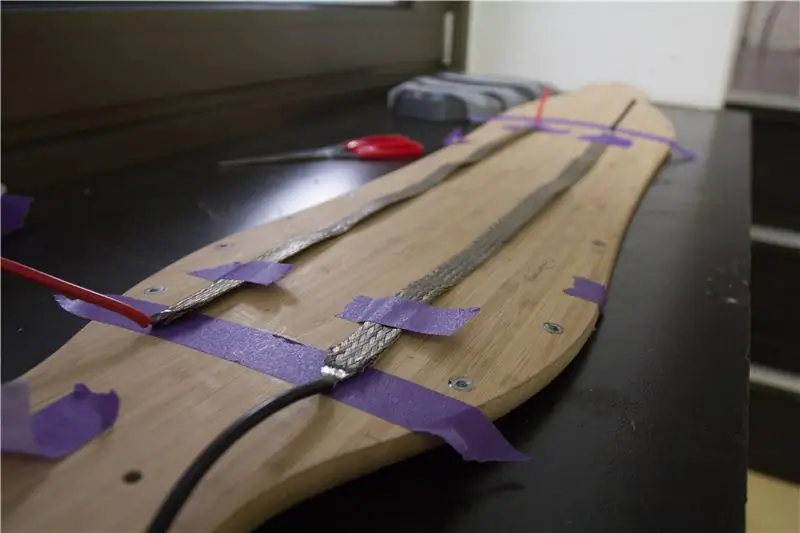
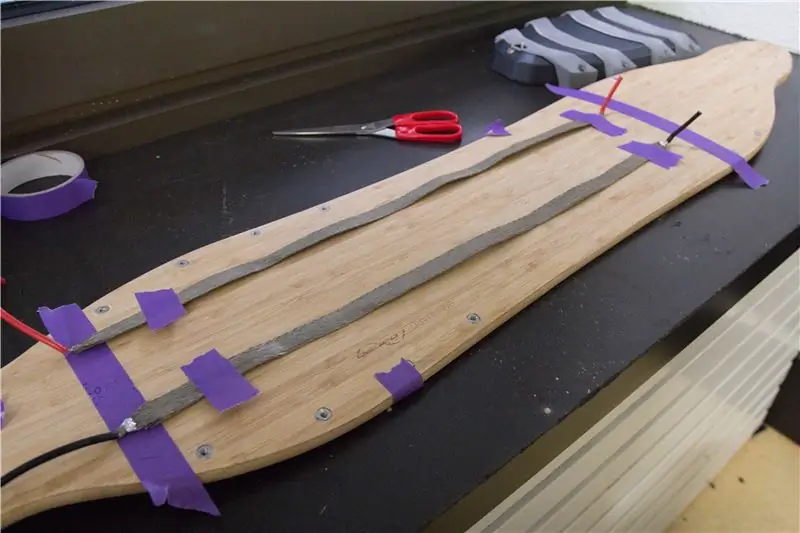
L'elettronica è stata scelta con cura per garantire che la scheda fosse potente ma anche intuitiva da usare. Questa scheda potrebbe essere potenzialmente pericolosa in caso di malfunzionamenti, quindi l'affidabilità è un fattore molto importante.
Il pacco batteria è composto da 20 singole celle 18650 agli ioni di litio che sono saldate a punti insieme per formare un pacco 42v. 2 celle sono saldate in parallelo e 10 in serie; le celle che ho usato erano Sony VTC6. Ho usato una saldatrice a punti per saldare le linguette di nichel per formare il pacco, poiché la saldatura crea troppo calore che può danneggiare la cella.
L'energia dal vano batteria è stata trasferita alla scatola del regolatore di velocità utilizzando un cavo intrecciato piatto che è stato fatto passare appena sotto il nastro adesivo sul lato superiore del ponte. Ciò ha permesso ai cavi di essere "nascosti" ed ha eliminato la necessità di far passare i cavi sul lato inferiore che sarebbe sembrato brutto.
Poiché si tratta di una scheda a doppio motore, sono necessari due controller di velocità per controllare in modo indipendente ciascun motore. Ho usato il controller di velocità VESC per questa build, che è un controller progettato specificamente per skateboard elettrici che lo rende molto affidabile per questo uso.
I motori utilizzati sono outrunner 170kv 5065 che possono produrre 2200W ciascuno, che è molta potenza per questa scheda. Con l'attuale configurazione del cambio, la velocità massima della scheda è di circa 35 MPH e accelera molto rapidamente.
L'ultima fase è stata quella di creare un telecomando per controllare la scheda. Si è preferito un sistema wireless per la facilità d'uso. Tuttavia, era importante garantire un'elevata affidabilità della trasmissione poiché un calo della comunicazione potrebbe avere gravi problemi di sicurezza, soprattutto alle alte velocità. Dopo aver testato alcuni protocolli di trasmissione radio, ho deciso che la frequenza radio a 2,4 GHz sarebbe stata la più affidabile per questo progetto. Ho usato un trasmettitore per auto RC standard, ma ho ridotto significativamente le dimensioni trasferendo l'elettronica in una piccola custodia portatile che è stata stampata in 3D.
Passaggio 5: scheda finita e video promozionale
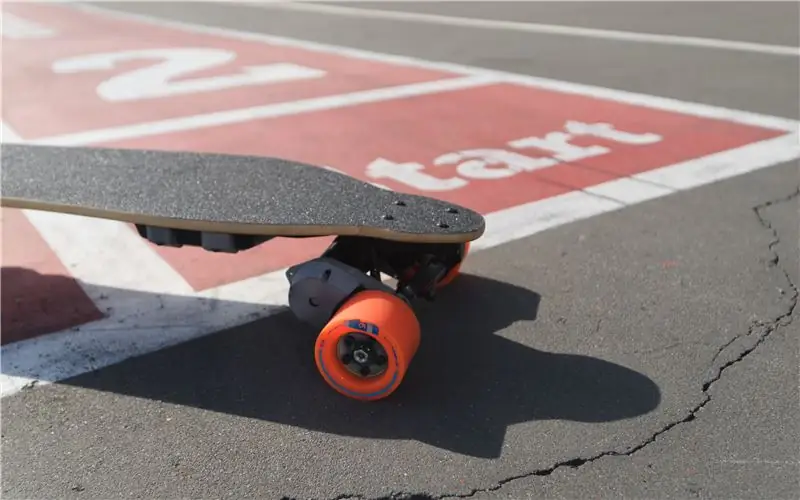
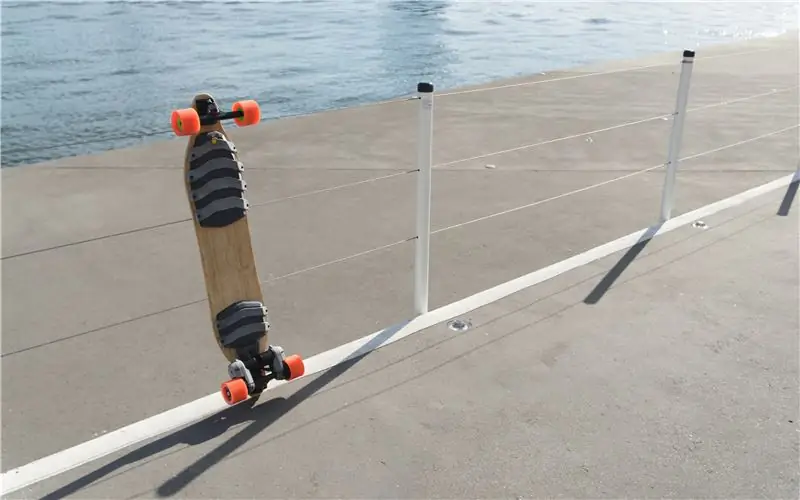
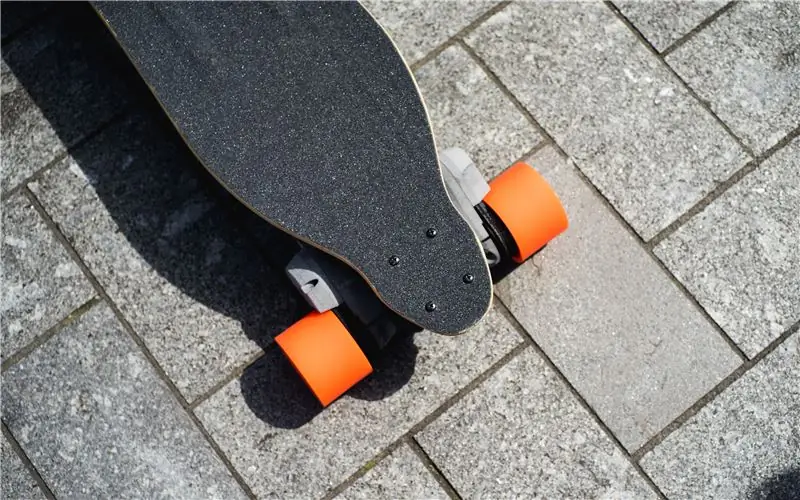
Il progetto è ora finito! Abbiamo creato un video davvero fantastico della lavagna in azione, puoi guardarlo qui sotto. Grazie mille a 3D Hubs per avermi permesso di realizzare questo progetto: dai un'occhiata qui per tutte le tue esigenze di stampa 3D! 3dhubs.com
Consigliato:
Un amplificatore stampato in 3D di uno strumento musicale elettrico.: 11 passaggi (con immagini)
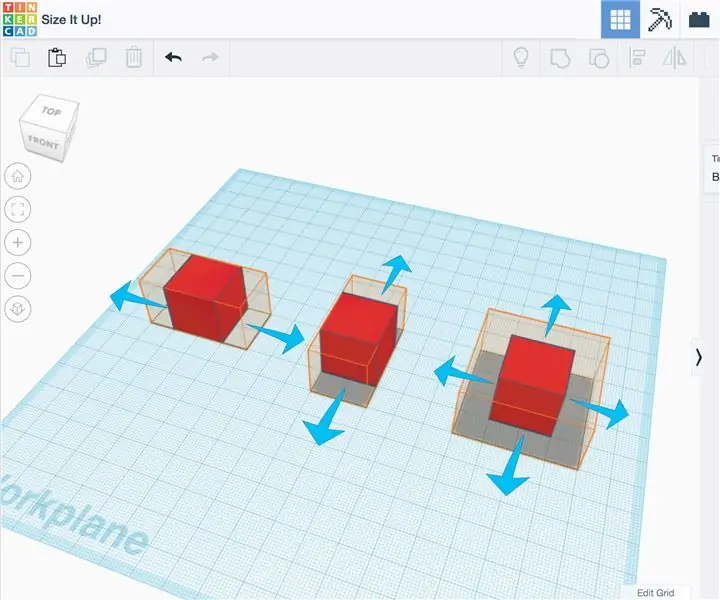
Un amplificatore stampato in 3D per strumenti musicali elettrici.: Definizione del progetto. Spero di realizzare un amplificatore stampabile da utilizzare con un violino elettrico o qualsiasi altro strumento elettrico. amplificatore attivo e mantienilo piccolo.Ele
Light Painter telescopico di dimensioni enormi realizzato con condotto EMT (elettrico): 4 passaggi (con immagini)
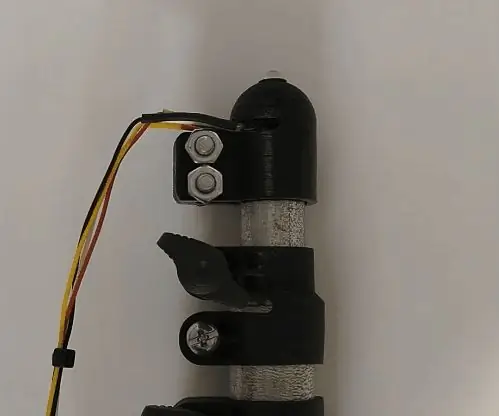
Light Painter telescopico di dimensioni enormi realizzato con condotto EMT (elettrico): la fotografia di light painting (scrittura leggera) viene eseguita scattando una fotografia a lunga esposizione, tenendo ferma la fotocamera e spostando una fonte di luce mentre l'apertura della fotocamera è aperta. Quando l'apertura si chiude, le scie luminose sembreranno congelate
GorillaBot, il robot quadrupede con Arduino stampato in 3D: 9 passaggi (con immagini)
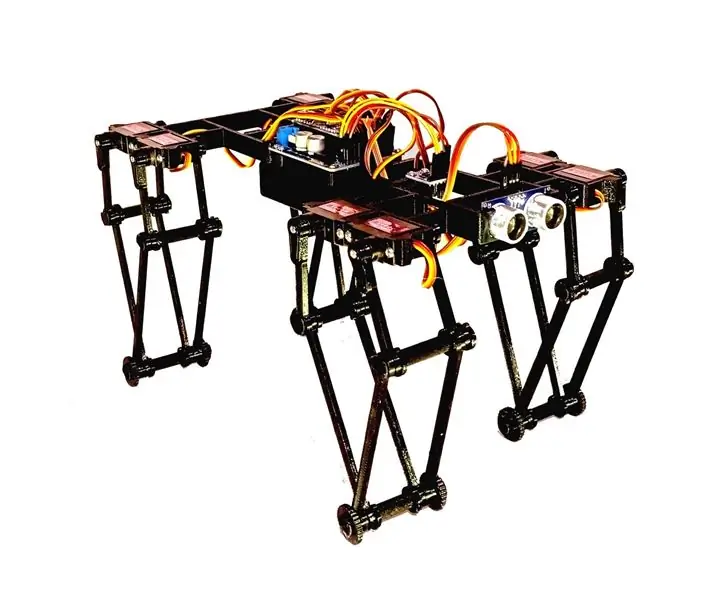
GorillaBot, il robot quadrupede con Arduino stampato in 3D: ogni anno a Tolosa (Francia) c'è la Toulouse Robot Race #TRR2021La gara consiste in uno sprint autonomo di 10 metri per robot bipedi e quadrupedi. Il record attuale che raccolgo per i quadrupedi è di 42 secondi per un Sprint di 10 metri. Quindi con quello in m
Interruttore elettrico a scorrimento stampato in 3D (usando solo una graffetta): 7 passaggi (con immagini)
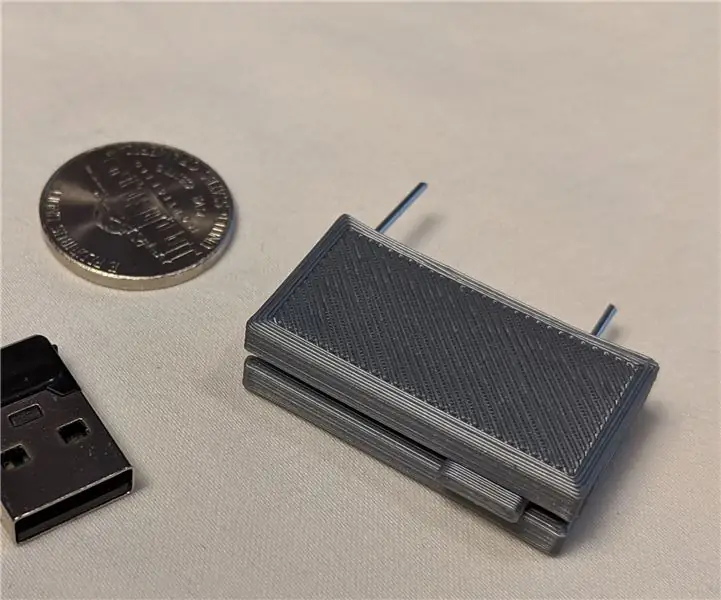
Interruttore elettrico a scorrimento stampato in 3D (usando solo una graffetta): nel corso degli anni mi sono dilettato nel cablaggio dei miei piccoli progetti elettrici, principalmente sotto forma di graffette, fogli di alluminio e cartone messi insieme con la colla a caldo. Di recente ho acquistato una stampante 3D (la Creality Ender 3) e sono andato a cercare
Penny Board elettrico V1: 8 passaggi (con immagini)
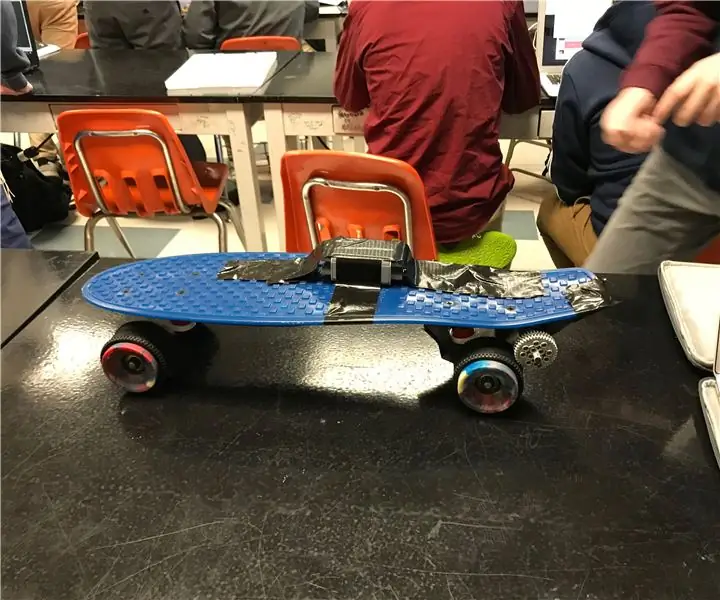
Electric Penny Board V1: questa penny board elettrica è un prototipo per uno skateboard inculato