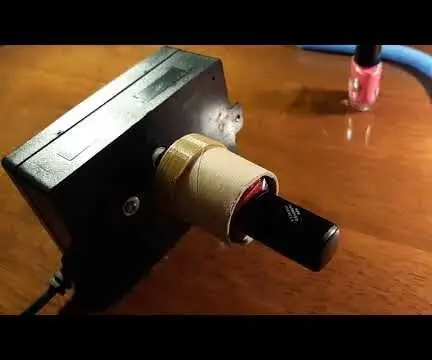
2025 Autore: John Day | [email protected]. Ultima modifica: 2025-01-23 14:49
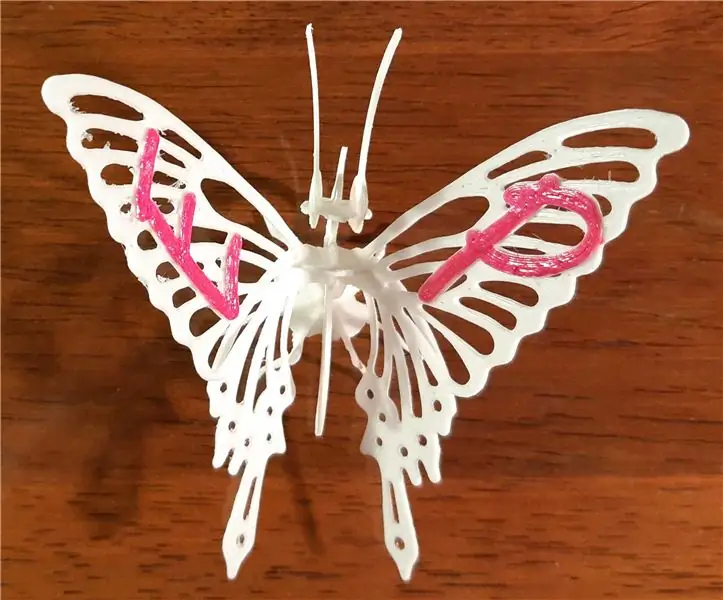

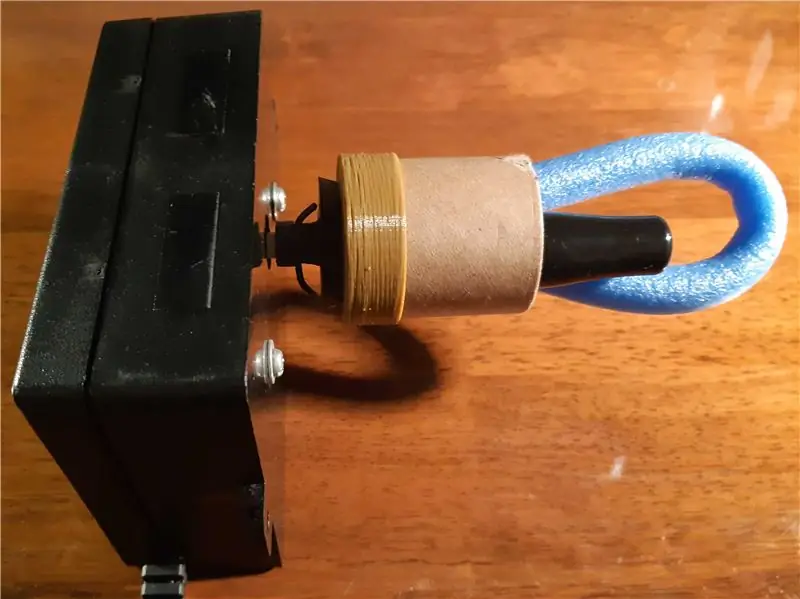
Una rapida costruzione di un delicato "agitatore" per smalto usando un motore per giradischi di un forno a microonde, un tubo, un involucro, un fusibile e un cavo…
Stavo stampando in 3D queste farfalle (nella foto) da Thingiverse (https://www.thingiverse.com/thing:178830) e ho deciso di fare alcuni disegni personalizzati. Ho "preso in prestito" un po' di smalto/vernice dal mio partner. Mi ha detto che dovevo arrotolare la bottiglia tra le mani per alcuni minuti e non scuotere la bottiglia, poiché introdurrà bolle. Ho cercato su eBay qualcosa per fare il lavoro, ma tutto quello che ho trovato sono stati shaker!
Avevo appena estratto alcune parti dal nostro forno a microonde defunto e ho notato che il motore del giradischi girava a 5/6 giri al minuto: perfetto!
Passaggio 1: Piano A:
Avevo bisogno di creare una canna da incollare al raccordo di plastica (su cui era precedentemente posizionata la lastra di vetro) che si attacca al motore, quindi ne ho modellato uno in Fusion360 (non mostrato).
La stampa avrebbe richiesto alcune ore e volevo che fosse finita in 2-3 ore, quindi mi sono guardato intorno e ho trovato un tubo di cartone duro (più duro del solito) da un distributore di fogli di alluminio…
Fase 2: Piano B:
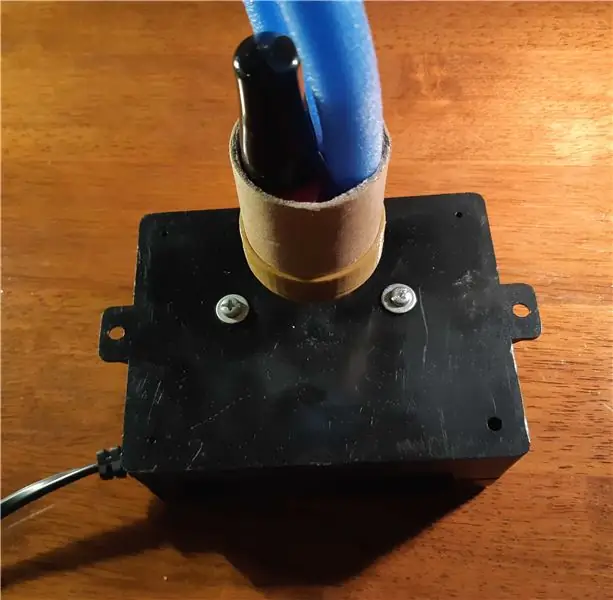
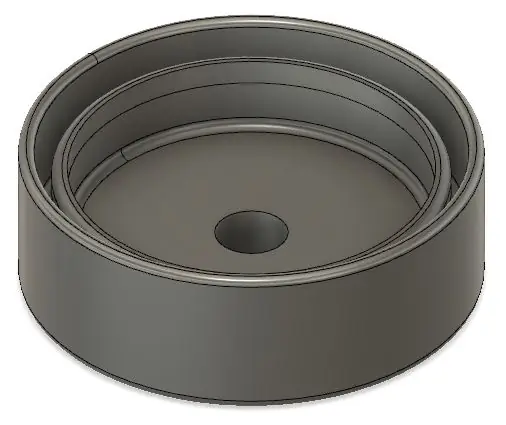
Ho modificato il mio modello 3D per diventare un adattatore per un pezzo corto di questo tubo, ho usato Repetier con l'affettatrice modello Slic3r Prusa Edition e ho iniziato a stampare l'adattatore.
Nel frattempo, ho tagliato e rifinito (smerigliato l'estremità tagliata) un pezzo corto del tubo, "dissotterrato" una spina di alimentazione a 3 pin con cavo, un involucro, un fusibile e un portafusibile. Il recinto aveva lati inclinati/inclinati, che consentivano al tubo di inclinarsi leggermente verso l'alto (come mostrato) quando posizionato su uno di questi lati.
Successivamente ho praticato i fori appropriati per montare il motore e il suo albero. Poi ho montato il motore sull'armadio.
ATTENZIONE: cablaggio di rete ahoy! Non eseguire il cablaggio di rete se non sai cosa stai facendo. Non pensare di sapere cosa stai facendo, PER FAVORE! Forse, invece, si potrebbe utilizzare un motore a bassissima tensione (meno di 50) e una fonte di alimentazione appropriata.
Il cavo di alimentazione aveva un passacavo che si adattava a un foro quadrato (potresti usare un pressacavo per impedire che il cavo si estragga e fulmini qualcuno), quindi ho praticato un foro vicino alla base della custodia (dove il coperchio incontra il resto della custodia) e archiviarlo con una lima quadrata fino a quando il passacavo non si adatta perfettamente.
L'isolamento esterno del cavo è stato spellato di ca. 100 mm e l'isolamento interno è stato spellato dai conduttori di ca. 15mm. Ho posizionato un dissipatore di calore su un filo (attivo (live) o neutro (ritorno)) e ho saldato il filo al portafusibile. Il dissipatore di calore è stato quindi ridotto al di sopra dell'unione. Per effettuare i collegamenti è possibile utilizzare una morsettiera, un giunto di filo isolato o un "punto blu".
L'altro filo (Attivo (Live) o Neutro (Ritorno)) è stato fatto in modo simile, ma è stato saldato al motore. Altri due pezzi di termoretraibile sono stati utilizzati per isolare le giunture di un pezzo corto (50 mm) di cavo isolato per alimentazione di rete, unendo il cavo motore rimanente all'estremità rimanente del portafusibile. Nel portafusibili è stato inserito un 0,5 A (500 mA) 250 VAC.
Il filo di terra era rigato e un terminale ad occhiello era crimpato su di esso. Uno dei bulloni di montaggio del motore è stato rimosso e reinstallato passando attraverso il terminale ad occhiello. Immagino che il filo di terra possa essere saldato direttamente al motore (se possibile) o che le teste dei bulloni esposte possano essere isolate con silicone per prevenire la minima possibilità di folgorazione.
Passaggio 3:
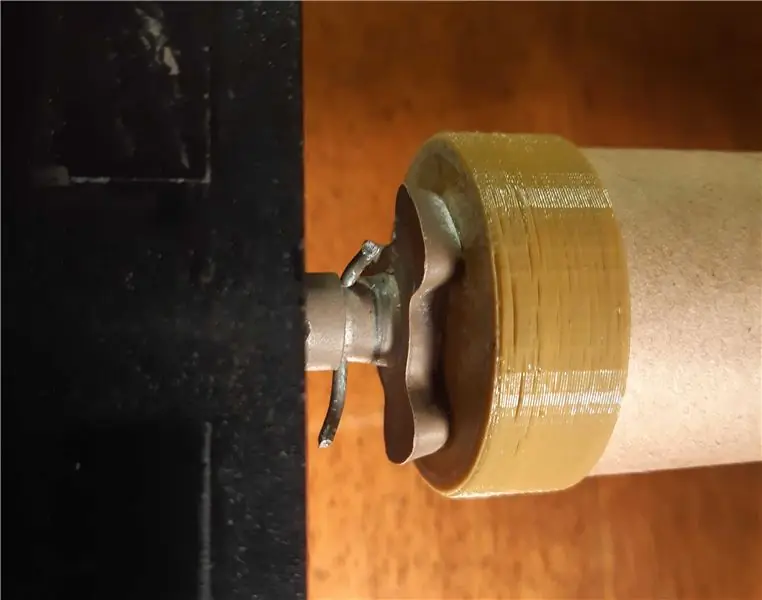
A questo punto la stampa 3D era completa, quindi ho incollato la canna all'adattatore stampato e ho incollato l'adattatore all'adattatore di plastica (lastra di vetro) che faceva parte del forno a microonde.
Ho praticato un foro attraverso l'albero del motore e l'adattatore originale e ho usato un filo "rigido" per impedire al gruppo della canna di separarsi dal gruppo della custodia. Questo passaggio non è realmente necessario, a causa dell'angolo della parete laterale dell'involucro (e della gravità) che impedisce al gruppo canna di cadere durante l'uso. Consentendo al gruppo del cilindro di essere facilmente rimosso dal gruppo della custodia, l'intera unità può essere imballata più piccola quando non è in uso!
Passaggio 4:
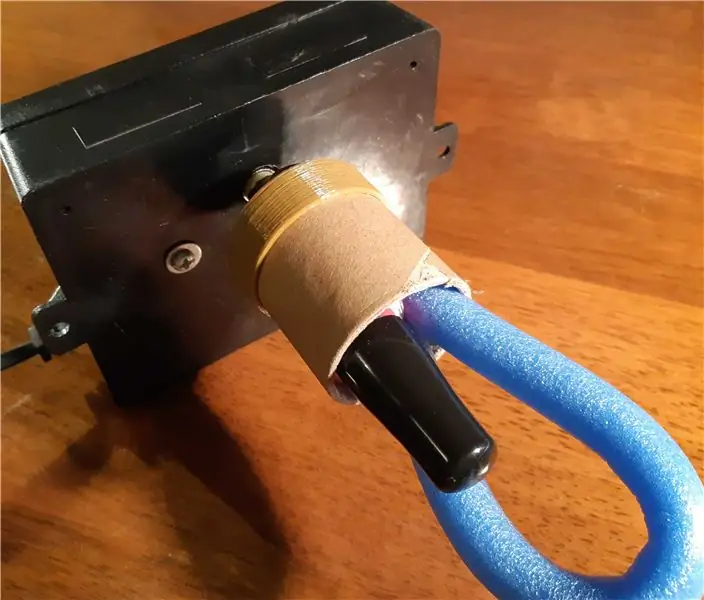
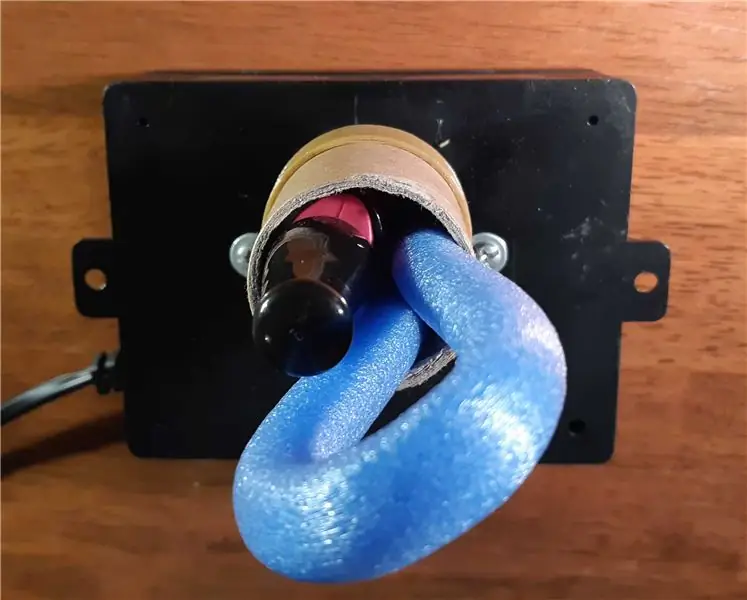
L'unità è stata accesa e testata.
Ha funzionato benissimo.
Alcune bottiglie (di forma strana) dovevano essere conservate meglio, quindi ho usato una sorta di cosa per capelli (la cosa blu).
Passaggio 5:
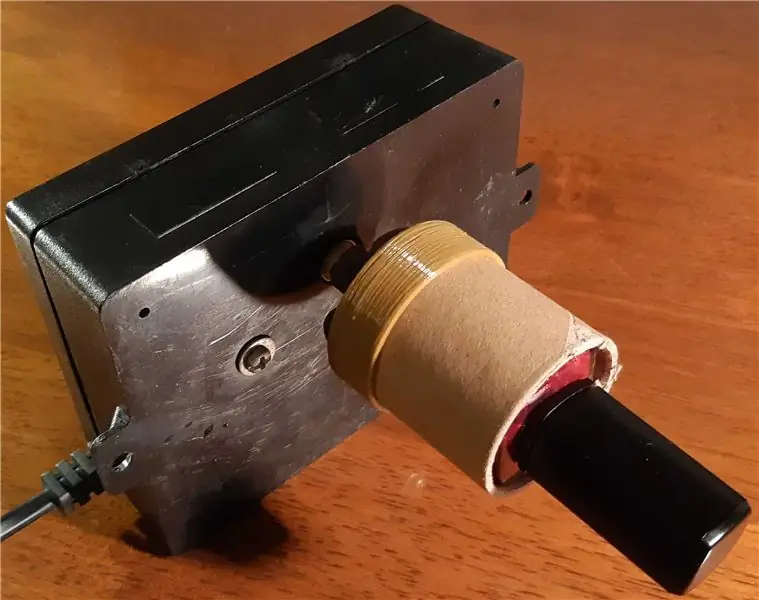
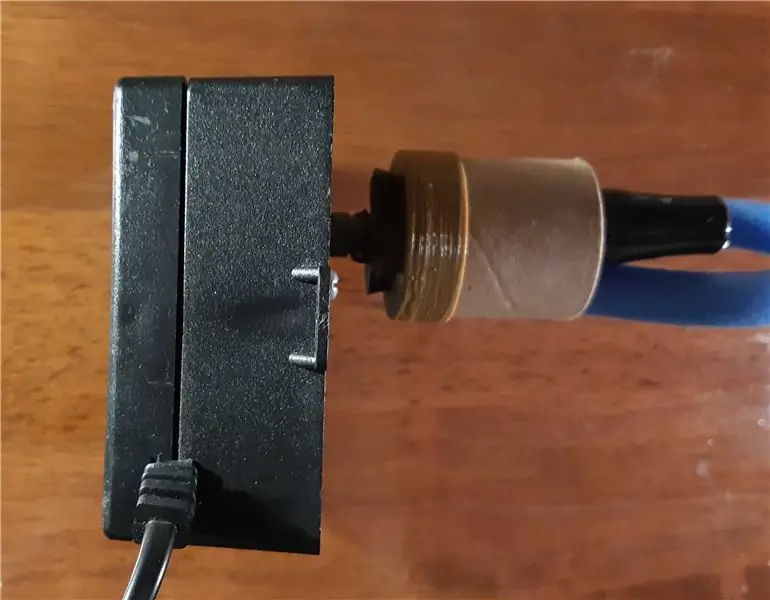
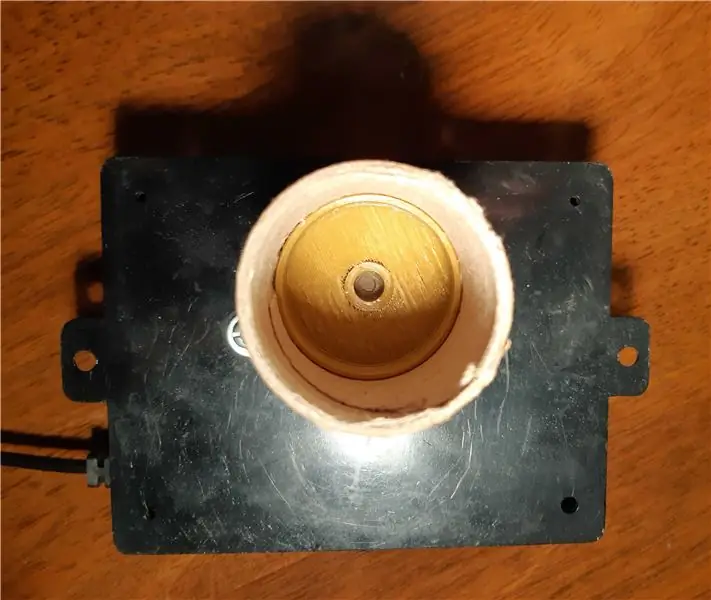
Lavoro completato!
Sono inclusi i file STL.
Divertiti!
Consigliato:
Agitatore magnetico controllato da Arduino: 8 passaggi (con immagini)
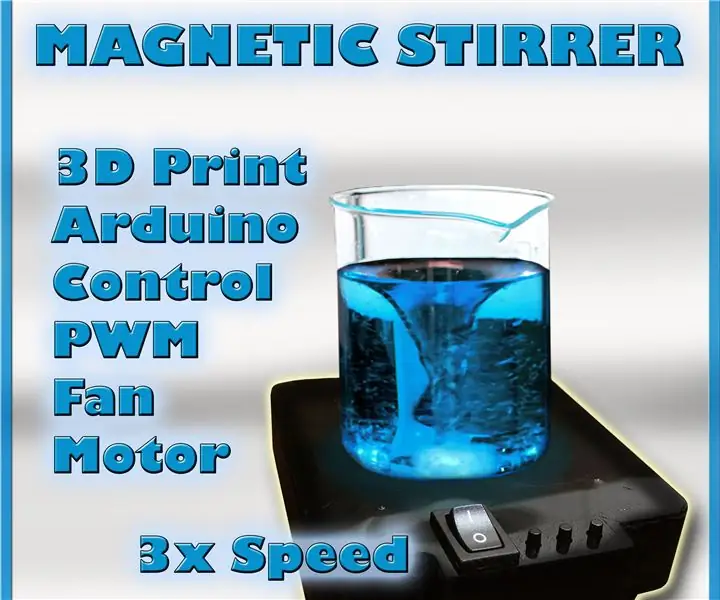
Agitatore magnetico controllato da Arduino: Ciao ragazzi & Ragazze. Ecco la mia versione di un "Super Slimline Magnetic Stirrer" stampato in 3D, creato per il "Magnets contest". Ha impostazioni di velocità 3x, (bassa, media e alta) ricavate da una vecchia ventola del computer e controllate con un
Agitatore per caffè HotOrNot: 5 passaggi
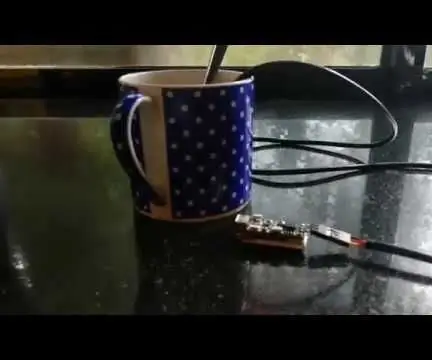
HotOrNot Coffee Stirrer: un intelligente agitatore per bevande per avvisare quando è sicuro bere senza scottarsi. L'ispirazione per questo progetto è stata mia. Tendo a bere il tè troppo velocemente, mi brucio o mi brucio le labbra o la lingua e poi devo aspettare un po' per
Agitatore per bevande: 5 passaggi (con immagini)
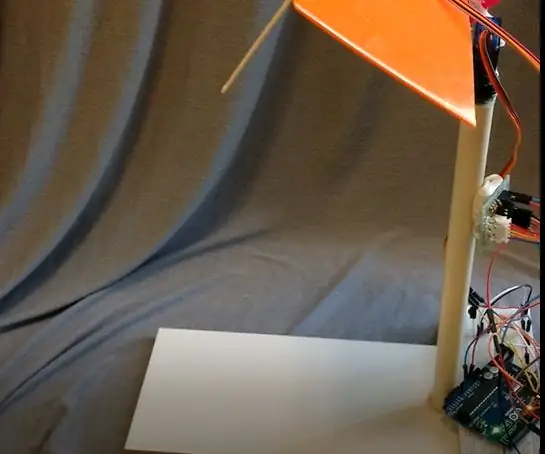
Drink Stirrer: questo istruttivo è stato creato in adempimento dei requisiti del progetto del Makecourse presso l'Università della Florida del sud (www.makecourse.com)
Agitatore magnetico semplice e piccolo: 8 passaggi (con immagini)
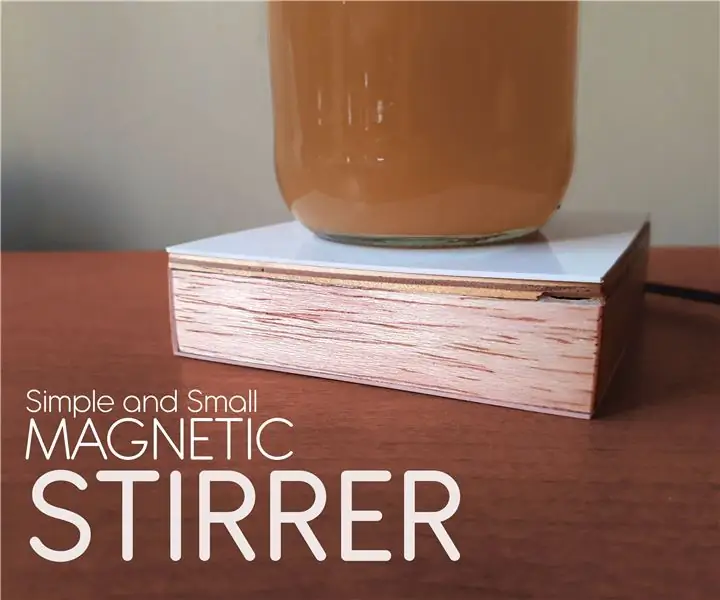
Agitatore Magnetico Semplice e Piccolo: Prima di tutto, l'inglese non è la mia lingua madre, quindi potresti trovare degli errori grammaticali nelle spiegazioni. Sarò grato se mi aiuti a correggere il mio Instructable. Detto questo, cominciamo. Un agitatore magnetico è un'attrezzatura da laboratorio, u
HC - 06 (modulo slave) Modifica "NOME" senza utilizzare "Monitor Serial Arduino" che "funziona facilmente": modo impeccabile!: 3 passaggi
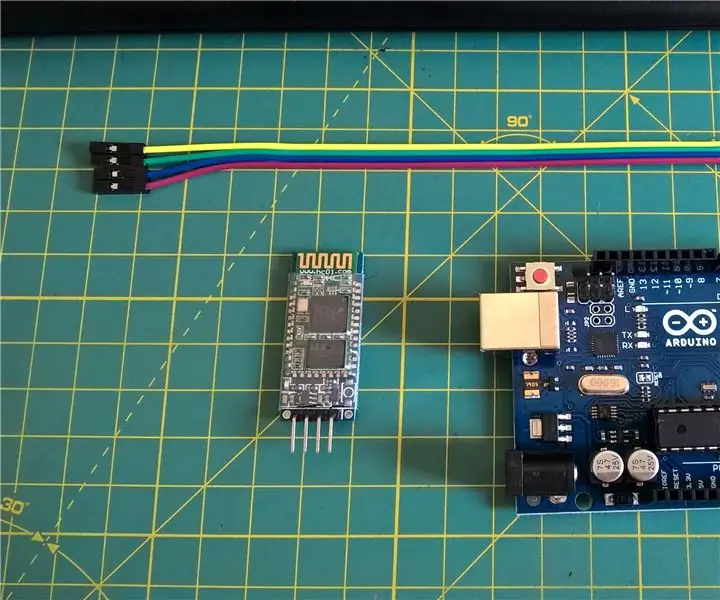
HC - 06 (Modulo Slave) Modifica di " NOME " senza utilizzare " Monitor Serial Arduino "… che " Funziona facilmente ": Modo impeccabile!: Dopo " Molto tempo " provando a cambiare nome su HC - 06 (modulo slave), utilizzando " monitor seriale di Arduino, senza " Successo ", ho trovato un altro modo semplice e lo sto condividendo ora! Buon divertimento amici