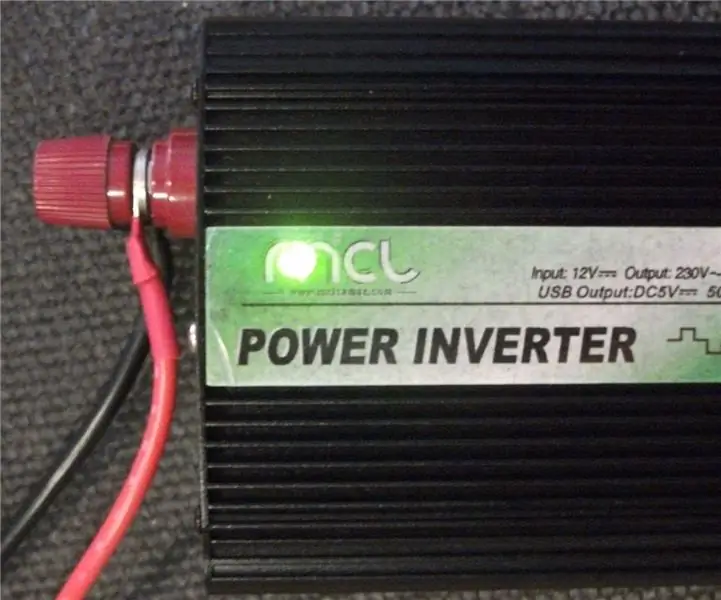
Sommario:
2025 Autore: John Day | [email protected]. Ultima modifica: 2025-01-23 14:50
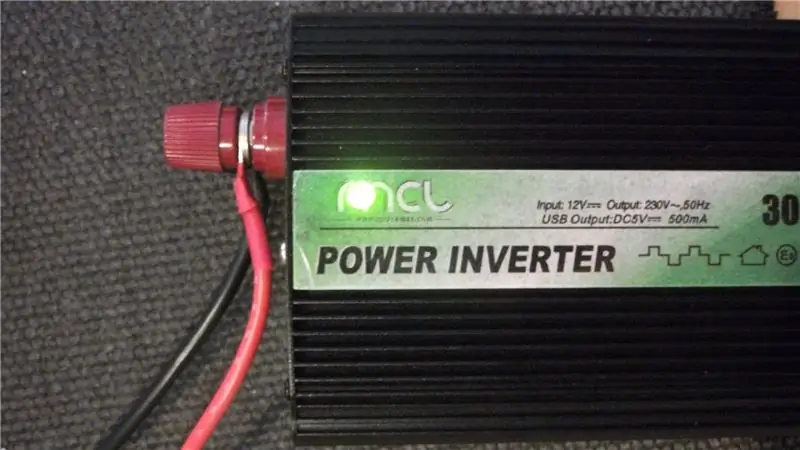
Questo è un progetto di aggiornamento dell'inverter da CC a CA.
Mi piace usare l'energia solare nella mia famiglia per l'illuminazione, l'alimentazione dei caricabatterie USB e altro ancora. Guido regolarmente strumenti a 230V con energia solare attraverso un inverter, utilizzando anche strumenti intorno alla mia auto alimentandoli dalla batteria dell'auto. Tutti questi scenari richiedono un inverter 12V-230V.
Tuttavia, uno svantaggio dell'utilizzo degli inverter è il rumore costante prodotto dalla ventola di raffreddamento integrata.
Il mio inverter è piuttosto piccolo con una potenza di uscita massima di 300 W. Eseguo carichi moderati da esso (ad esempio il mio saldatore, utensile rotante, faretti, ecc.) E l'inverter di solito non ha bisogno di un flusso d'aria costantemente forzato attraverso il suo involucro.
Quindi salviamoci da quel terribile rumore di una ventola che divide rabbiosamente l'aria con tutta la sua potenza e controlliamo la ventola con un sensore di temperatura!
Passaggio 1: caratteristiche
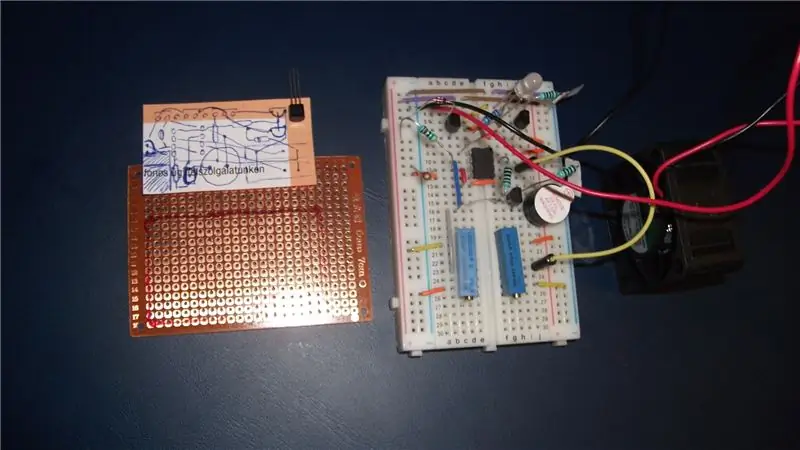
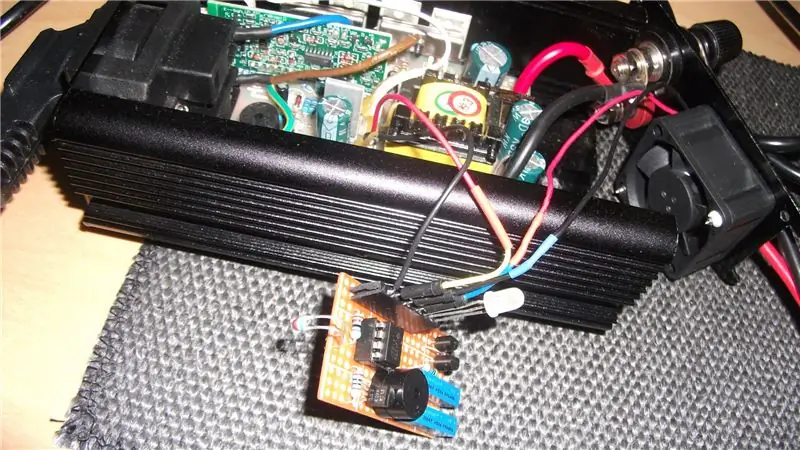
Ho sognato un circuito di controllo della ventola con 3 stati:
- L'inverter è freddo e la ventola funziona silenziosamente a un basso numero di giri (giri al minuto). L'indicatore LED personalizzato si illumina in verde.
- L'inverter si scalda. La ventola viene commutata alla massima velocità e il LED diventa giallo.
- L'inverter aumenta ulteriormente la sua temperatura. Un cicalino emette un segnale acustico, indicando che il livello del calore danneggerebbe l'inverter e che la ventola non può compensare la quantità di calore dissipato.
Non appena l'aumento dell'attività del ventilatore è in grado di raffreddare l'inverter, il circuito torna automaticamente allo stato 2 e successivamente allo stato di calma 1.
Nessun intervento manuale mai richiesto. Nessun interruttore, nessun pulsante, nessuna manutenzione.
Passaggio 2: componenti richiesti
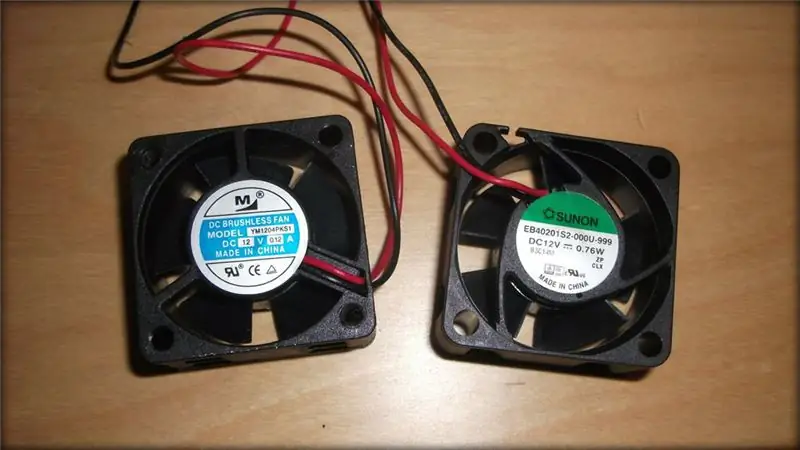
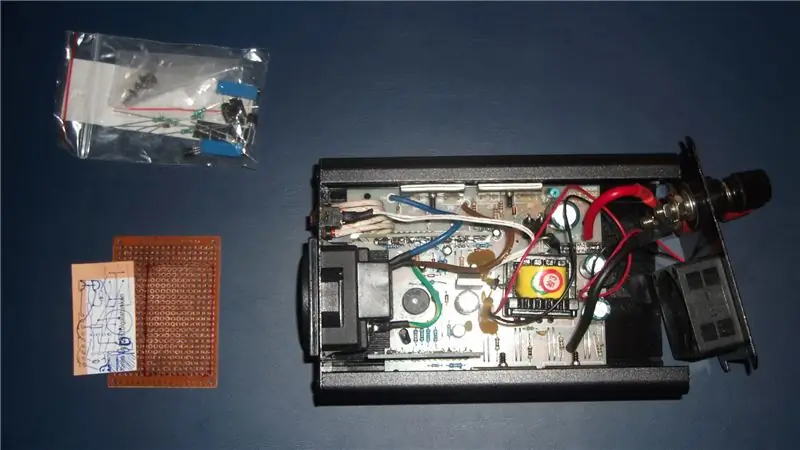
Sono necessari almeno i seguenti componenti per pilotare in modo intelligente la ventola dell'inverter:
- un chip amplificatore di funzionamento (ho usato un doppio amplificatore operazionale LM258)
- un termistore (6,8 KΩ) con una resistenza a valore fisso (4,7 KΩ)
- un resistore variabile (500 KΩ)
- un transistor PNP per pilotare la ventola e un resistore da 1 KΩ per preservare il transistor
- opzionalmente un diodo a semiconduttore (1N4148)
Con questi componenti puoi costruire un controller della ventola a temperatura controllata. Tuttavia, se vuoi aggiungere indicatori LED, hai bisogno di più:
- due LED con due resistori o un LED bicolore con un resistore
- hai anche bisogno di un transistor NPN per pilotare il LED
Se desideri anche la funzione di avviso di surriscaldamento, avrai bisogno di:
- un cicalino e un altro resistore variabile (500 KΩ)
- opzionalmente un altro transistor PNP
- opzionalmente due resistori a valore fisso (470 Ω per il buzzer e 1 KΩ per il transistor)
Il motivo principale per cui ho implementato questo circuito è disattivare l'audio della ventola. La ventola originale era sorprendentemente rumorosa, quindi l'ho sostituita con una versione a bassa potenza e molto più silenziosa. Questa ventola consuma solo 0,78 Watt, quindi un piccolo transistor PNP può gestirla senza surriscaldarsi, alimentando anche il LED. Il transistor PNP 2N4403 ha una corrente nominale di 600 mA massima sul suo collettore. La ventola consuma 60 mA durante il funzionamento (0,78 W / 14 V = 0, 06 A) e il LED consuma altri 10 mA. Quindi il transistor può gestirli in sicurezza senza un relè o un interruttore MOSFET.
Il cicalino può funzionare direttamente senza un resistore, ma ho trovato il suo rumore troppo forte e fastidioso, quindi ho applicato un resistore da 470 per rendere il suono più amichevole. Il secondo transistor PNP può essere omesso poiché l'amplificatore operazionale può pilotare direttamente il piccolo cicalino. Il transistor è lì per accendere/spegnere il cicalino in modo più fluido, eliminando un suono sbiadito.
Passaggio 3: progettazione e schema

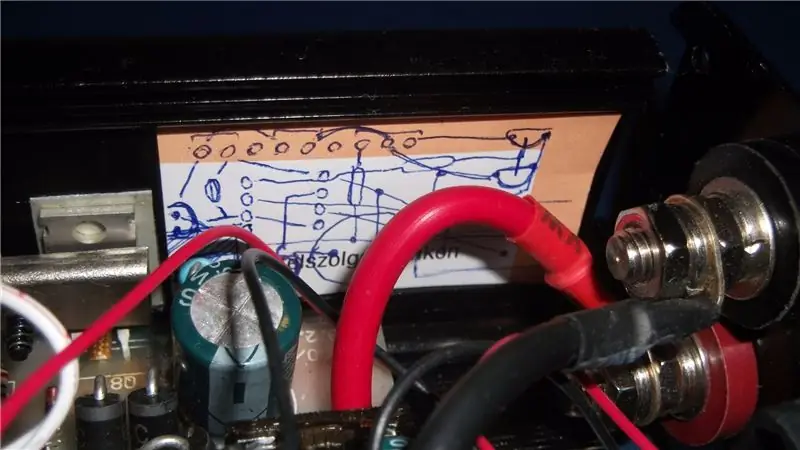
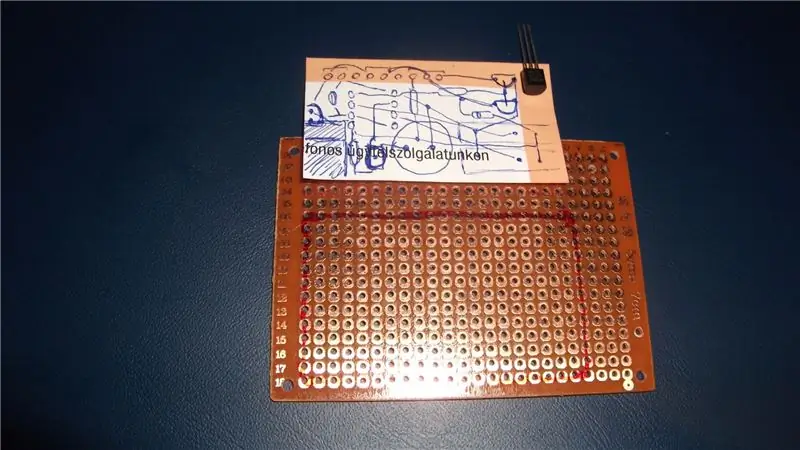
Ho posizionato il LED sulla parte superiore dell'alloggiamento dell'inverter. In questo modo può essere facilmente visto da qualsiasi angolo di visione.
All'interno dell'inverter ho posizionato il circuito aggiuntivo in modo tale che non blocchi il percorso del flusso d'aria. Inoltre, il termistore non dovrebbe trovarsi nel flusso d'aria, ma in un angolo non ben ventilato. In questo modo misura principalmente la temperatura dei componenti interni e non la temperatura del flusso d'aria. La principale fonte di calore in un inverter non sono i MOSTFET (la cui temperatura è misurata dal mio termistore) ma il trasformatore. Se vuoi che la tua ventola risponda rapidamente per caricare le modifiche sull'inverter, dovresti posizionare la testa del termistore sul trasformatore.
Per semplicità ho fissato il circuito alla custodia con del nastro biadesivo.
Il circuito è alimentato dal connettore della ventola di raffreddamento dell'inverter. In realtà l'unica modifica che ho fatto sui componenti interni dell'inverter è stato tagliare i fili della ventola, e inserire il mio circuito tra il connettore della ventola e la ventola stessa. (L'altra modifica è un foro praticato nella parte superiore dell'involucro per il LED.)
I potenziometri variabili possono essere di qualsiasi tipo, tuttavia sono preferibili i trimmer elicoidali perché possono essere regolati con precisione e molto più piccoli dei potenziometri a manopola. Inizialmente ho messo a punto il trimmer elicoidale che accende la ventola a 220 KΩ, misurata sul lato positivo. L'altro trimmer è stato preimpostato a 280 KΩ.
Il diodo a semiconduttore è lì per evitare che la corrente induttiva fluisca all'indietro quando il motore elettrico della ventola è appena spento ma il rotore è ancora ruotato dal suo momento. Tuttavia, l'applicazione del diodo qui è facoltativa poiché con un motore della ventola così piccolo l'induzione è così piccola che non può causare danni al circuito.
LM258 è un doppio chip op-amp composto da due amplificatori operativi indipendenti. Possiamo condividere la resistenza di uscita del termistore tra i due pin di ingresso degli amplificatori operazionali. In questo modo siamo in grado di accendere la ventola a una temperatura più bassa e il cicalino a una temperatura più alta utilizzando un solo termistore.
Userei una tensione stabilizzata per guidare il mio circuito e ottenere punti di temperatura on/off costanti che sono indipendenti dal livello di tensione della batteria su cui gira l'inverter, ma voglio anche mantenere il design del circuito il più semplice possibile, quindi Ho rinunciato all'idea di utilizzare un regolatore di tensione e un interruttore accoppiatore ottico per pilotare la ventola con la tensione non regolata per il massimo numero di giri.
Nota: il circuito presentato in questo schema copre tutte le caratteristiche menzionate. Se si desidera meno o altre caratteristiche rispetto al circuito deve essere modificato di conseguenza. Ad esempio tralasciando il LED e non modificando nient'altro si otterrà un malfunzionamento. Si noti inoltre che i valori delle resistenze e del termistore potrebbero essere diversi, tuttavia se si utilizza una ventola con parametri diversi dai miei è necessario modificare anche i valori delle resistenze. Infine, se la tua ventola è più grande e richiede più potenza, di quella che dovrai includere un relè o un interruttore MOSFET nel circuito: un piccolo transistor si brucerà a causa della corrente che la tua ventola scarica. Prova sempre su un prototipo!
AVVERTIMENTO! Pericoloso per la vita!
Inverter con alta tensione al loro interno. Se non hai familiarità con i principi di sicurezza della manipolazione dei componenti ad alta tensione NON DEVI APRIRE UN INVERTER!
Passaggio 4: impostazione dei livelli di temperatura
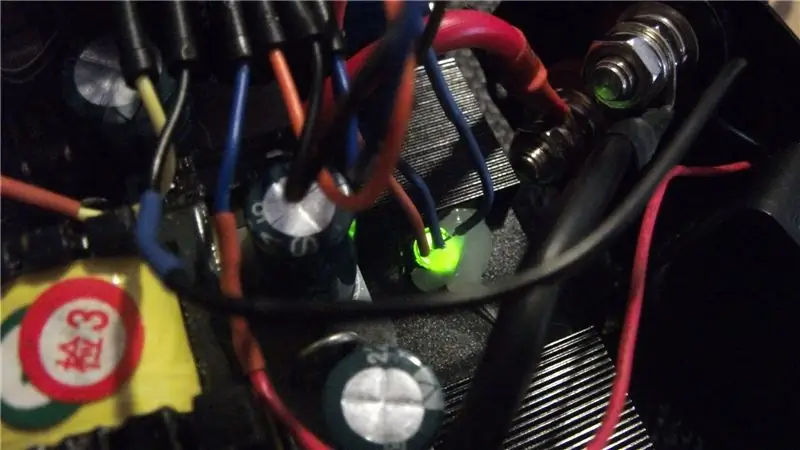
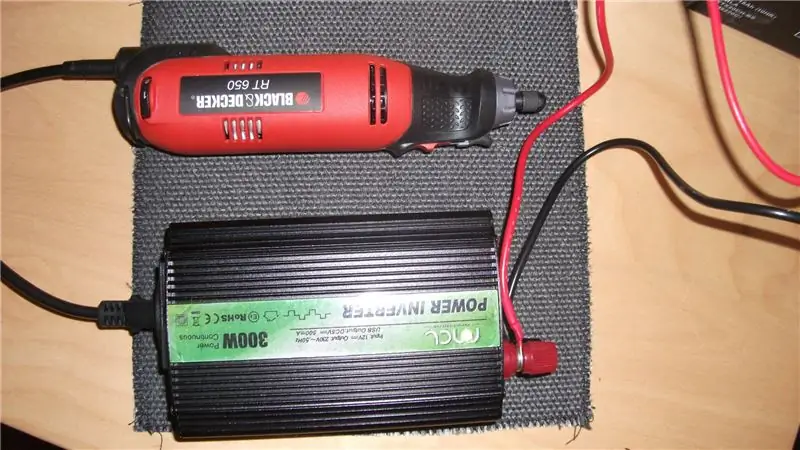
Con le due resistenze variabili (potenziometri, o trimmer elicoidali nel mio caso) si possono personalizzare i livelli di temperatura dove si attiva la ventola e il cicalino. Questa è una procedura per tentativi ed errori: devi trovare le impostazioni corrette per diversi cicli di tentativi.
Per prima cosa lascia raffreddare il termistore. Quindi imposta il primo potenziometro al punto in cui passa il LED da verde a giallo e la ventola da basso ad alto numero di giri. Ora tocca il termistore e lascialo scaldare con la punta delle dita, mentre aggiusti il potenziometro finché non si spegne di nuovo la ventola. In questo modo imposti il livello di temperatura a circa 30 gradi Celsius. Probabilmente vuoi una temperatura leggermente più alta (forse sopra i 40 gradi Celsius) per accendere la ventola, quindi accendi il trimmer e prova il nuovo livello di accensione/spegnimento dando un po' di calore al termistore.
Il secondo potenziometro che comanda il cicalino può essere impostato (ovviamente per un livello di temperatura più alto) con lo stesso metodo.
Uso il mio inverter a ventola con grande soddisfazione - e in silenzio.;-)
Consigliato:
Ventilatore medico con STONE HMI ESP32: 10 passaggi
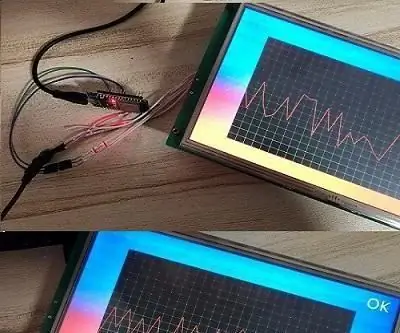
Ventilatore medico con STONE HMI ESP32: il nuovo coronavirus ha causato quasi più di 80mila casi confermati a livello nazionale e i respiratori e i respiratori scarseggiano negli ultimi mesi. Non solo, ma anche la situazione all'estero non è ottimista. Il numero cumulativo
Ventilatore da tavolo riciclabile (a prova di errore): 10 passaggi (con immagini)
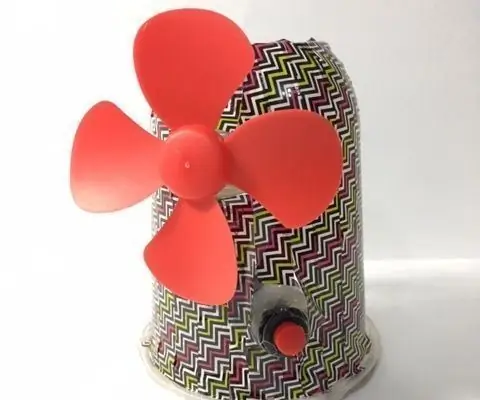
Ventilatore da tavolo riciclabile (a prova di errore): questo è un tutorial su come realizzare un mini ventilatore da tavolo estremamente semplice che viene riutilizzato da tutte le tazze per bevande che probabilmente butterai via (molto probabilmente tazze da tè Boba per me) e un'alternativa per rinfrescarti durante una calda giornata di sole. Questo con
$ 7,25 - Aggiungi il controllo vocale a qualsiasi ventilatore da soffitto: 4 passaggi (con immagini)
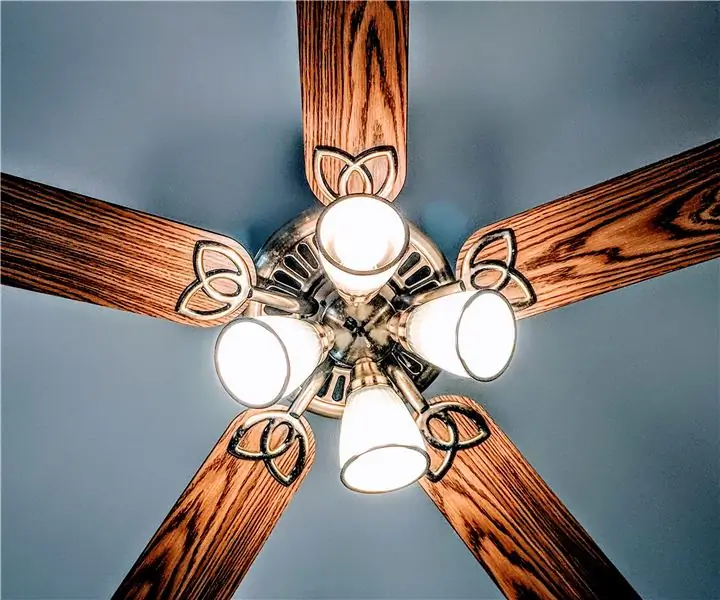
$ 7,25 - Aggiungi il controllo vocale a qualsiasi ventilatore da soffitto: in questo Instructable, ti guiderò attraverso il processo molto semplice per automatizzare il tuo ventilatore da soffitto in modo da poterlo controllare con i comandi vocali utilizzando un dispositivo Alexa. È possibile utilizzare queste istruzioni per controllare altri dispositivi elettronici (luci, ventilatore, TV, e
Ventilatore portatile Altoids Tin: 7 passaggi (con immagini)
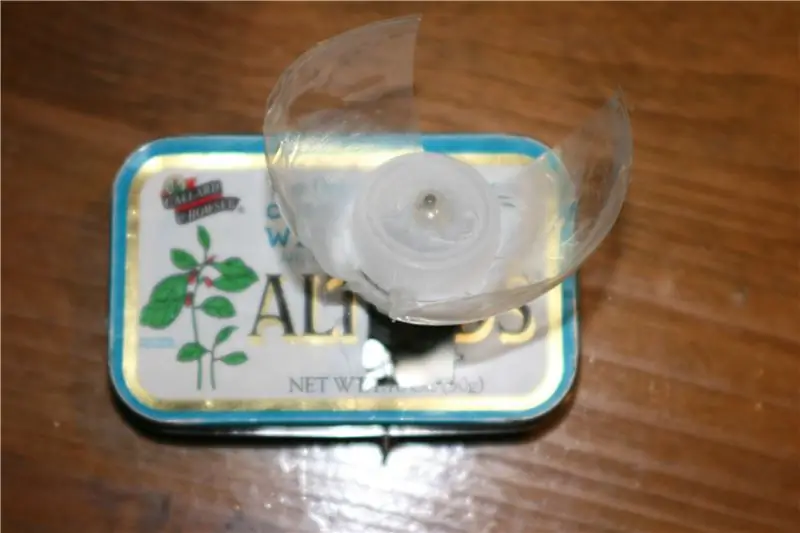
Ventilatore portatile Altoids Tin: abbiamo una latta Altoids e una bottiglia d'acqua. Cosa possiamo fare con quello? Perché non fare un fan? Questo è quello che ho fatto. Ho utilizzato la curva della bottiglia d'acqua per realizzare le pale della ventola e un vecchio motore per farlo girare. Ho usato il tappo della bottiglia dell'acqua
Display a LED per ventilatore da soffitto: 12 passaggi (con immagini)
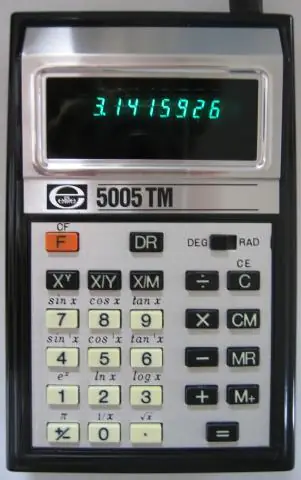
Display a LED per ventilatore a soffitto: vedere così tante idee di visione persistenti sul web era troppo allettante per non provarne una. Dopo aver considerato diversi motori per azionare un display, un ventilatore da soffitto sembrava funzionare alla giusta velocità, è fuori mano e molto silenzioso rispetto a