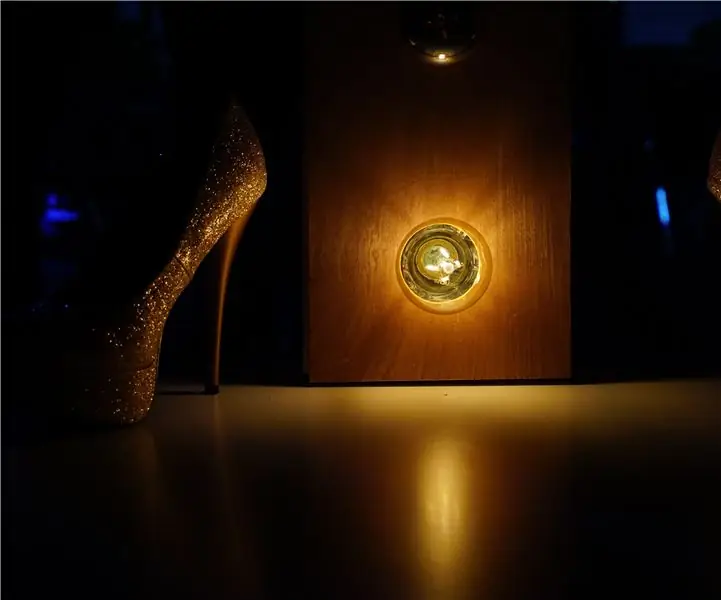
Sommario:
- Forniture
- Passaggio 1: Circuito 5V: Arduino
- Passaggio 2: progettare la scatola
- Passaggio 3: costruire la scatola
- Passaggio 4: installazione delle prese nella scatola
- Passaggio 5: saldatura dell'elettronica a bassa tensione
- Passaggio 6: collegamento dei componenti 220V
- Step 7: Magnetic Snapper (opzionale)
- Passaggio 8: cosa farei diversamente
2025 Autore: John Day | [email protected]. Ultima modifica: 2025-01-23 14:49
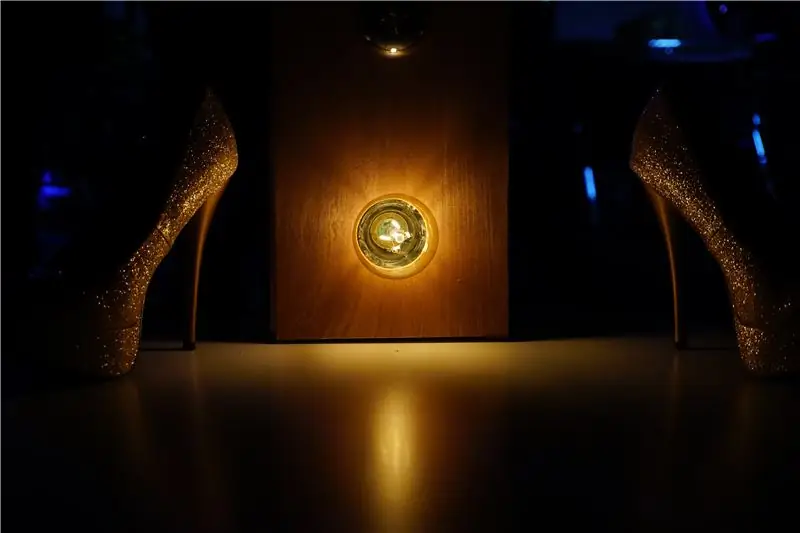
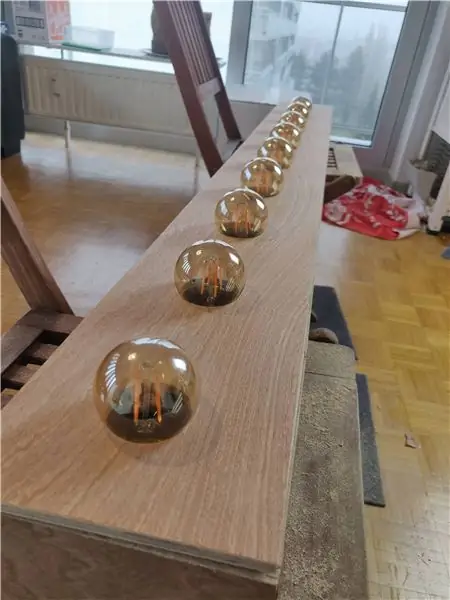
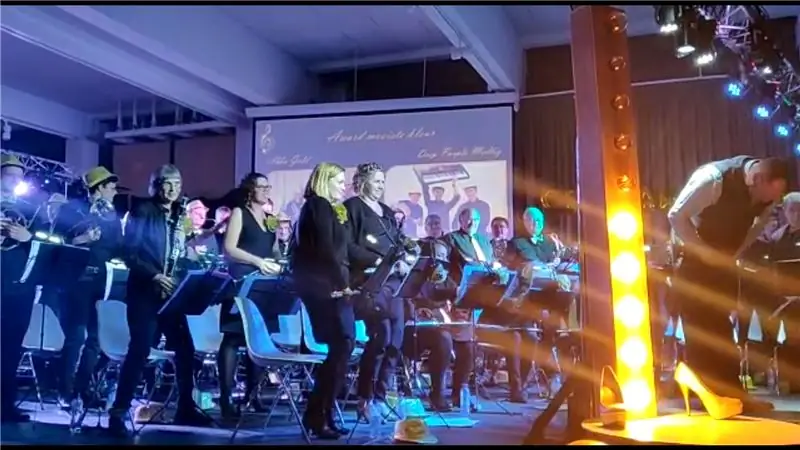
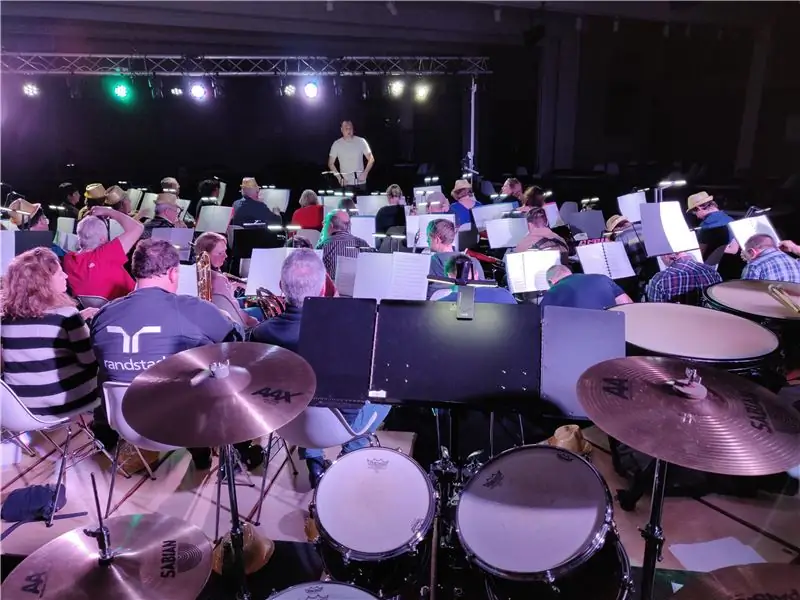
Da qualche parte intorno all'anno 2001 ho iniziato a prendere lezioni di batteria. Dopo dieci anni, nel 2011, sono entrato a far parte della mia prima band da concerto e ne sono rimasto affascinato. Fare musica insieme e suonare a un concerto è esaltante. Ora sono in un'altra band da più di 5 anni. Abbiamo due concerti all'anno e diverse commissioni sul lato.
Come tema del nostro concerto di Capodanno abbiamo voluto tenere una cerimonia di premiazione per le migliori canzoni che abbiamo suonato. L'impostazione era che abbiamo suonato due canzoni in ogni categoria. Ad esempio "Ghiaccio contro fuoco" per il quale abbiamo suonato un medley di "Frozen" e uno di "Come addestrare il tuo drago". Il pubblico dovrebbe quindi votare per la migliore canzone, che poi riceverà un premio stampato in 3D personalizzato.
Durante il brainstorming durante i preparativi, abbiamo avuto molte idee su come far votare il pubblico, dai voti cartacei alle app. Ma tutti questi suggerimenti richiedono che lo spettacolo venga interrotto per ogni premio, mentre distrae seriamente il pubblico. Quando è stato suggerito un metro di applausi, sapevamo tutti di aver raggiunto l'oro. Ma alcune ricerche online non hanno rivelato una vera soluzione pronta per l'uso. Quindi mi sono coraggiosamente alzato in piedi, mi sono dichiarato un creatore alle prime armi e ho affermato che avrei potuto facilmente costruirne uno da zero per un budget piuttosto ridotto.
Oh ragazzo ero impreparato per la tana del coniglio in cui sarei caduto.
Forniture
Utensili
- Il tuo trapano a batteria preferito
- Punta da trapano circolare e altre punte
- cacciaviti
- Stampante 3D (opzionale)
Caso
- compensato. (Scelgo multiplex da 8 mm ma con il senno di poi avrei dovuto optare per 12 mm o anche più spesso)
- 4 x chiusura magnetica per porta (opzionale col senno di poi)
- viti
Elettronica (5V)
- Arduino Nano
- Amplificatore microfonico electret - MAX4466 con guadagno regolabile (o simile, secondo le tue esigenze)
- Modulo relè 2 X 5V 8 canali
- Trasformatore da 220V a 5V
- cavi, molti corti, e un cavo a quattro fili di diversi metri per il controllo 'remoto'
- due interruttori
Elettronica (220V)
- cavi elettrici standard (gli avanzi della costruzione della casa sono ideali, ma meglio flessibili)
- Presa di alimentazione CA con fusibile (opzionale ma altamente consigliata)
- Lampadine a scelta
- Portalampada
Passaggio 1: Circuito 5V: Arduino
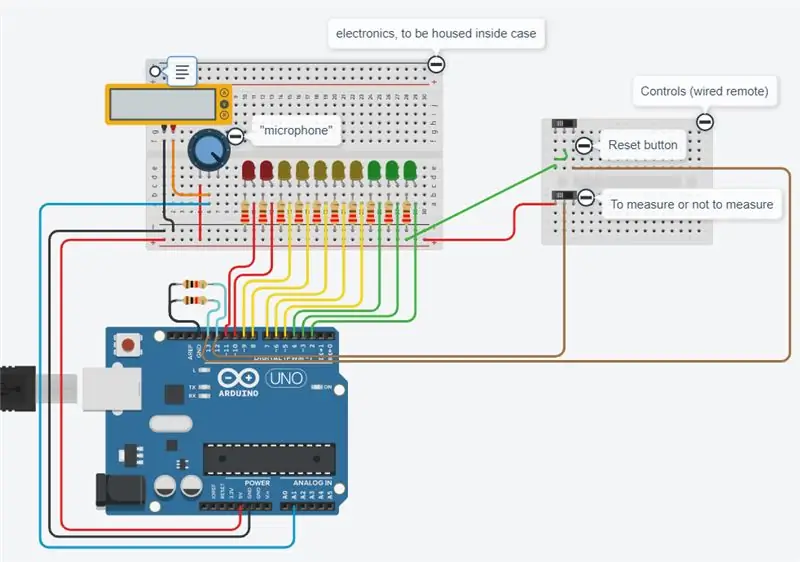
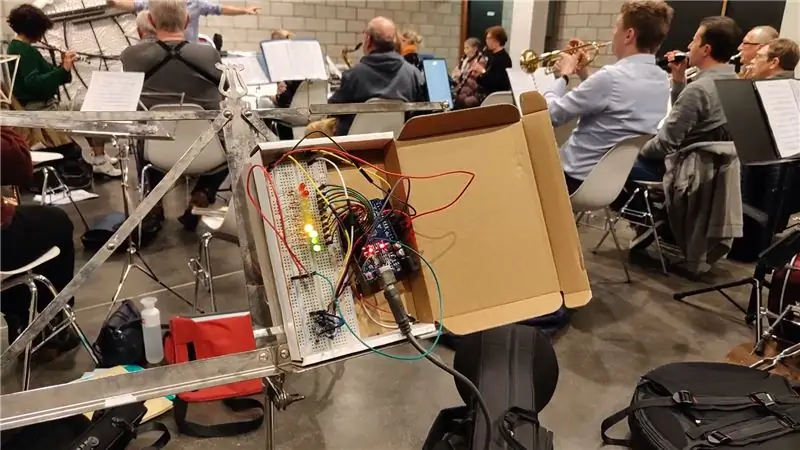
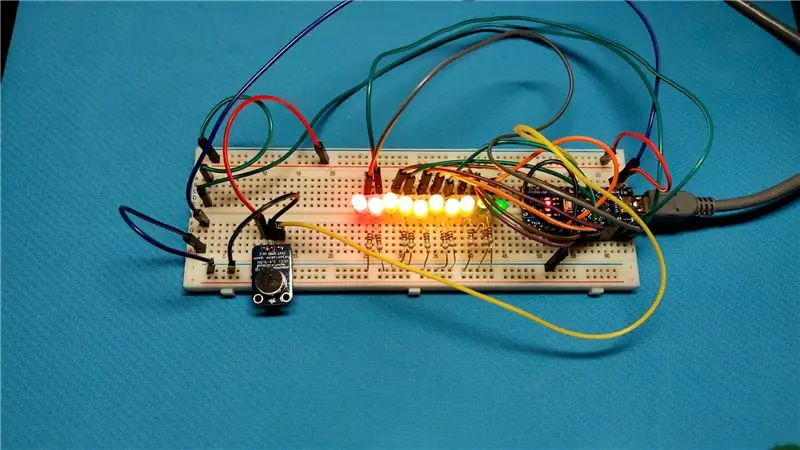
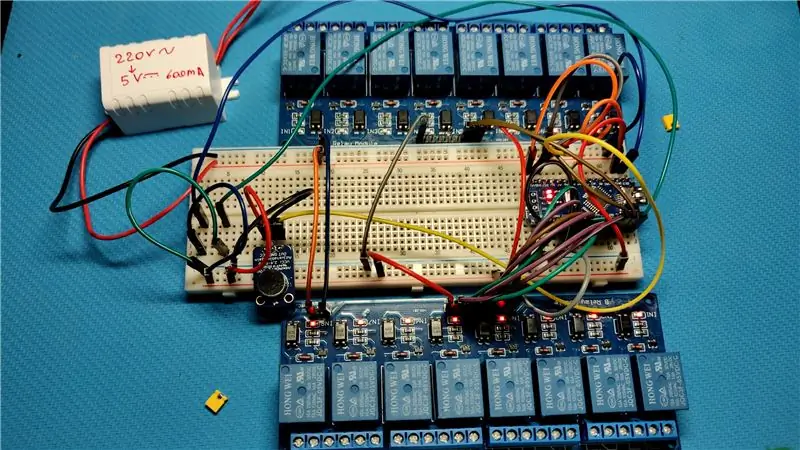
Ci sono tre parti principali in questa build: (1) l'elettronica 5V che farà il "pensiero duro": ascoltare e decidere quando e quali luci accendere; (2) l'involucro per adattarsi bene a tutto, nasconde tutti i "crimini" e (3) il circuito a 220 V che è controllato dal circuito a 5 V.
Cominciamo con il circuito 5V poiché possiamo costruirlo su piccola scala.
Non è stato un compito facile trovare risorse online. Ho immaginato dieci luci, che si accendevano in base al volume degli applausi, ma nessuno sembrava averlo fatto prima. Quindi, ho iniziato in piccolo; Su tinkerCAD ho costruito una simulazione online di come volevo che fossero le parti elettroniche a 5V. Puoi trovare il mio design molto rudimentale con il codice qui: https://www.tinkercad.com/things/8mnCXXKIs9M o sotto su questa pagina come file "Applause_1.0.ino".
Realizzare una bozza online e testare diversi codici Arduino su questa simulazione mi ha davvero aiutato a ottenere una visione migliore di ciò che era necessario per questa build. In questo modo ho provato ad aggiungere un modo per controllare il comportamento del programma: ho finito con due interruttori. Un interruttore accende e spegne la misurazione, l'altro riporta il punteggio a 0/10.
Ho raccolto tutti i componenti necessari: alcuni LED, resistori, un Arduino e, soprattutto, un microfono compatibile con Arduino.
Ho costruito il circuito e testato tutto alla prossima prova, solo per rendermi conto che il microfono che ho comprato era molto sensibile per il mio uso. Un solo applauso a una distanza ragionevole, o solo la band che suona, saturerebbe il microfono dando un punteggio di 10/10. Questo mi ha spinto a cercare un microfono con guadagno variabile. Alla fine ho optato per l'amplificatore per microfono Electret - MAX4466. Ha una vite molto piccola sul retro con cui è possibile impostare il guadagno. (nota a margine: ho anche cambiato Arduino uno per un Arduino Nano senza alcun motivo particolare).
Il MAX4466 si è comportato meglio ma ha anche raggiunto il massimo quando si batte le mani a stretto contatto, quindi ho deciso di includere anche il tempo di applauso come variabile della formula invece del solo volume dell'applauso. Ho anche scritto un codice un po' più elegante per questa versione 2.0 del software (anche se lo dico io stesso). In caso di superamento di una soglia di volume si accendeva solo la prima luce seguita da una breve pausa durante la quale nessuna luce poteva accendersi. Dopo aver atteso, Arduino ascolterebbe se il suono fosse ancora abbastanza forte da far accendere la seconda luce, in tal caso la luce si accende e si attiva il successivo periodo di attesa. Il tempo di attesa aumentava ogni volta che si accendeva una nuova luce. Un applauso dovrebbe durare 22,5 secondi a tutto volume perché le luci mostrino 10/10. Puoi trovare il codice su tinkerCAD https://www.tinkercad.com/things/lKgWlueZDE3 o sotto come file "Applause_2.0.ino"
Un rapido test con i moduli relè collegati invece dei LED mi ha insegnato che i relè erano ON quando il segnale era BASSO e OFF quando il segnale era ALTO. Nessun problema, bastava disattivare alcuni ON e OFF nel codice ed eravamo pronti per partire.
Con tutto questo risolto. Potrei iniziare a saldare tutto insieme. Ma avevo bisogno di sapere quanto dovrebbero essere lunghe tutte le connessioni all'interno della scatola. Quindi costruiamo prima la scatola esterna e sistemiamo tutti i componenti al suo interno.
Passaggio 2: progettare la scatola
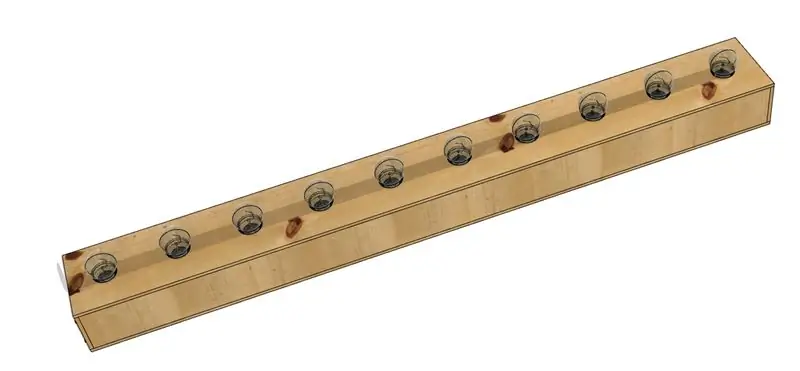
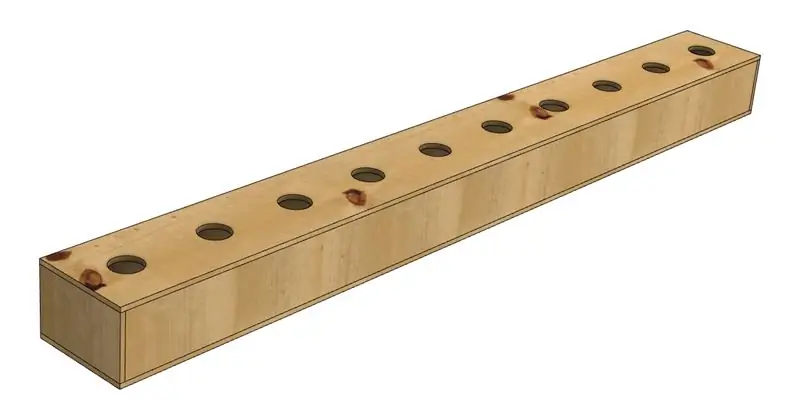
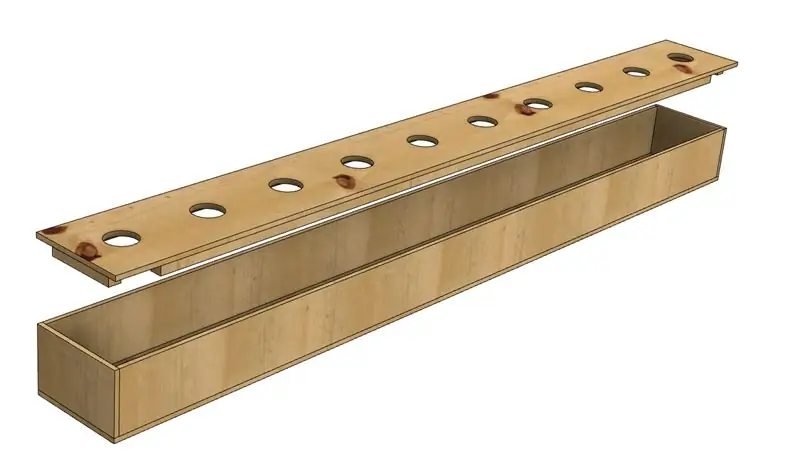
Un secondo aspetto di questa costruzione era la sua estetica. Il misuratore degli applausi sarebbe stato al centro dell'attenzione, quindi doveva almeno avere un bell'aspetto. Ho scelto di costruire una scatola di legno poiché ho gli strumenti di base per farlo ed è relativamente facile.
Avendo appreso su tinkerCAD che sperimentare nel mondo digitale è altamente educativo, ho anche progettato la scatola del misuratore di applausi nel popolare programma 3D-CAD Fusion360 prima di acquistare uno dei materiali necessari.
Nel corso di diverse iterazioni ho finalmente optato per questo design (vedi foto). È una semplice scatola rettangolare con le luci che sporgono dai fori circolari nel pannello frontale.
Le brutte viti nel pannello frontale sono state evitate aggiungendo alcune barre di supporto all'interno del pannello frontale, dove in seguito sarebbero stati avvitati i ganci magnetici delle porte. Il sistema di chiusura magnetica, col senno di poi, è più una caratteristica di sicurezza che davvero necessaria, dal momento che le barre trattengono la piastra anteriore solo per attrito, bene.
Ho anche aggiunto l'elettronica al mio progetto digitale. Questo ha cambiato alcune cose, quindi stava già dando i suoi frutti il fatto che l'ho progettato per la prima volta in Fusion360. Ad esempio, la scatola doveva essere leggermente più larga dei 15 cm iniziali affinché i relè si adattassero lateralmente. Ho anche finito per modellare e stampare in 3D supporti in plastica per le prese della luce che a loro volta avrebbero tenuto le luci in posizione. Questa mi sembrava essere l'opzione che mi avrebbe dato abbastanza "spazio di manovra" per errori futuri. (So che questi supporti possono anche essere acquistati come tali, ma questo mi è costato tre volte di più e avevo un budget limitato)
Ho aggiunto qui il file F360 del mio progetto finale perché tu possa fare riferimento e giocare.
Passaggio 3: costruire la scatola
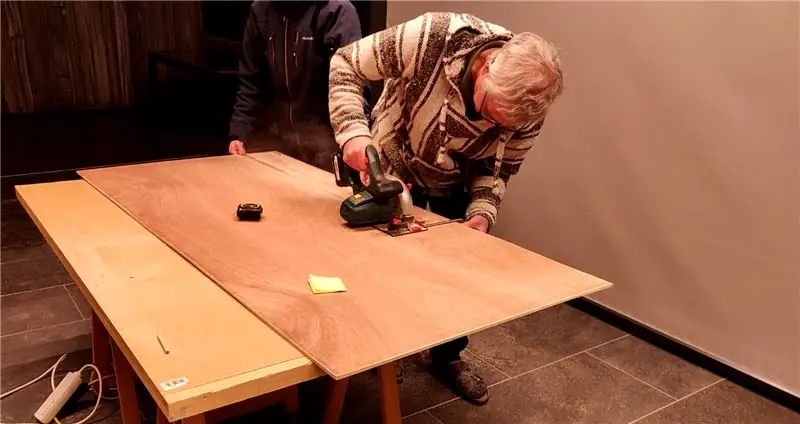
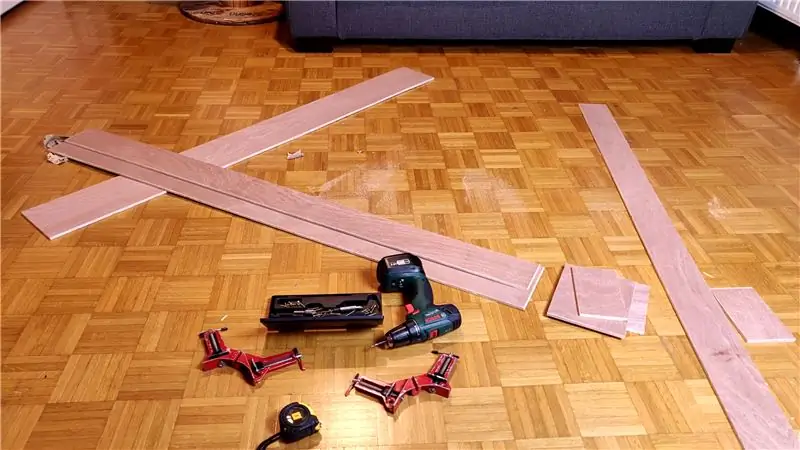
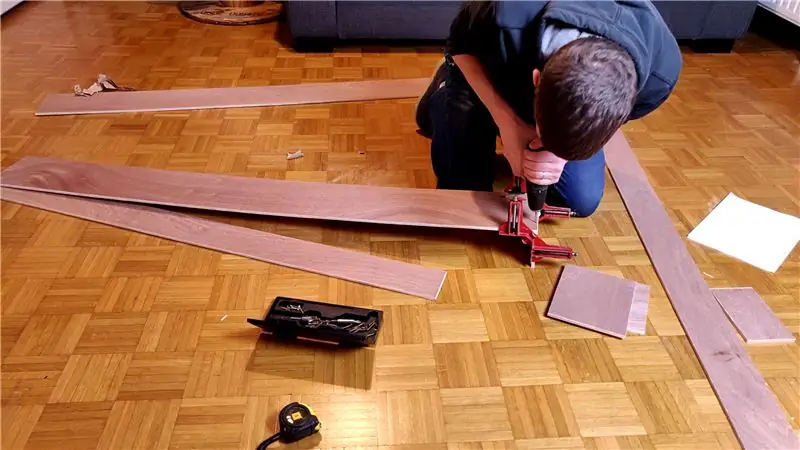
Con il design digitale finalizzato era ora di andare al negozio di ferramenta, comprare un grosso foglio di compensato e iniziare a tagliare. Dato che non possedevo strumenti così "fantasiosi", sono andato a casa dei miei genitori un fine settimana e ho tagliato il legno a misura lì.
Tuttavia, il mio progetto ha finito per produrre un foglio tagliato piuttosto esotico:
- 2 volte 16,6x150 cm per la parte anteriore e posteriore
- 2 volte 16,6x10,2 cm per la parte superiore e inferiore
- 2 volte 10,2x148,4 cm per i lati
Le barre di supporto all'interno del pannello frontale erano degli avanzi e venivano utilizzate come tali altrimenti la lunghezza preferita sarebbe stata di 134 cm e 12 cm.
Una volta a casa, ho disposto tutte le parti sul pavimento e con l'aiuto di alcuni morsetti angolari (presi in prestito), ho iniziato a praticare i fori e ad avvitare le assi. Ricorda che le viti vanno solo nella parte superiore, inferiore e posteriore del misuratore per pura reazione estetica.
Il pilota perforare i fori e avvitare tutte le schede è stato reso un compito precario a causa del fatto che il compensato è sottile solo 8 mm, spesso mi sono maledetto per aver pensato che 8 mm sarebbero stati abbastanza spessi.
Il pannello frontale necessitava di fori accuratamente distanziati di circa 5 cm di diametro. Ho segnato la linea centrale del tabellone anteriore e ho iniziato da un lato. Il centro del primo foro era di 8 mm (lo spessore del materiale) + 75 mm (metà di 150 mm) dal bordo della tavola. Tutti gli altri fori sono distanti 150 mm. Alla fine ero fuori solo di 2 mm quando ho segnato la decima buca… è stata una buona giornata!
L'unica punta circolare che potevo prendere in prestito era di 51 mm, più che abbastanza vicina da permettermi di iniziare felicemente a perforare.
Le guide della piastra anteriore sono state incollate in posizione all'interno della piastra anteriore con semplice colla per legno.
Passaggio 4: installazione delle prese nella scatola
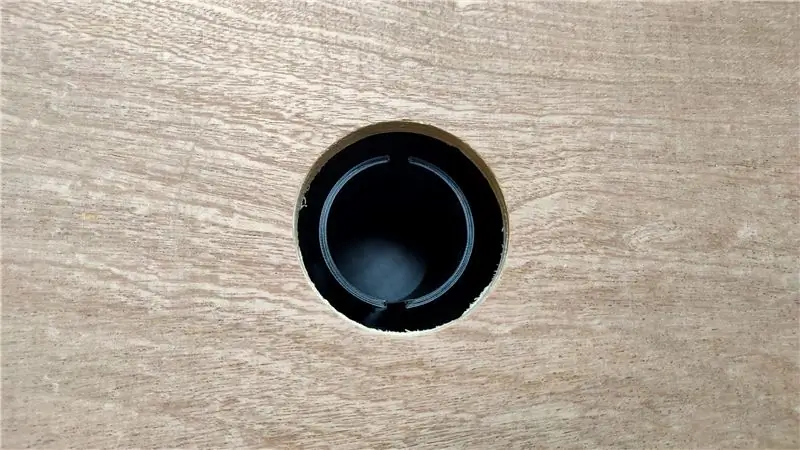
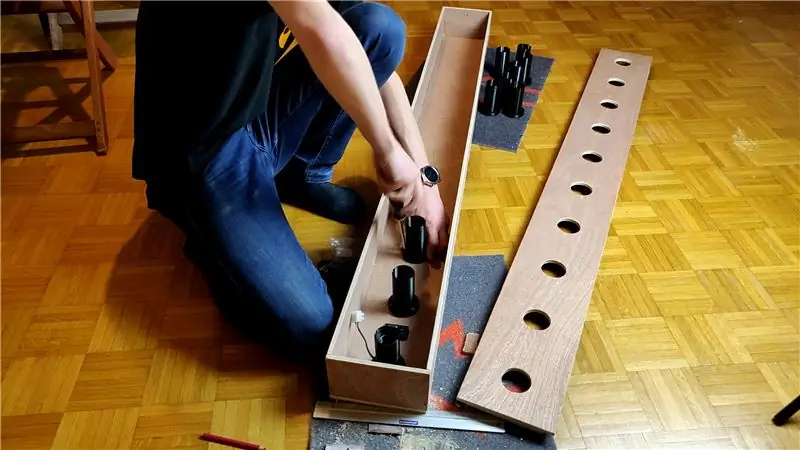
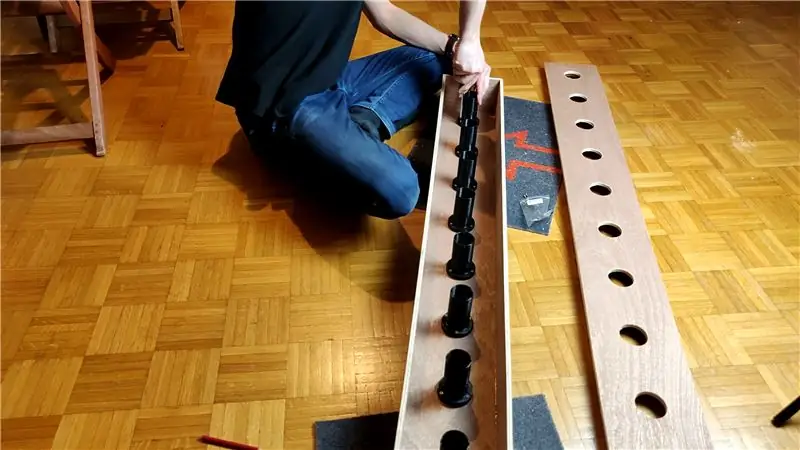
I primi componenti che vengono montati nella nostra scatola di nuova costruzione, sono i portalampada. La ragione di ciò è che i supporti devono essere posizionati centrati sotto ogni foro nella piastra frontale. Perché il supporto tiene in posizione i portalampada, che a loro volta avranno le lampadine avvitate, e le lampadine sono letteralmente l'unica cosa che fuoriesce dal pannello frontale e quindi sono l'unica cosa che non può essere spostata un'altra posizione all'interno della nostra scatola. Dato che la loro posizione è fissa, dovrebbero entrare per primi, per essere sicuri che non commetta uno stupido errore in seguito.
Come dicevo prima, in commercio esistono prese luce con staffa integrata per montarle perpendicolarmente a una parete, ma costano 4 volte di più di quelle semplici che si fanno solo per appendere al soffitto senza nemmeno fare un debole tentativo di sembra carina. Quindi, ho optato per un supporto economico e stampato in 3D per le prese. (file STL sotto). Quando ho realizzato il design 3D, mi sono assicurato che ci fosse abbastanza spazio per posizionare le prese a una varietà di profondità.
Ho stampato un solo supporto per verificare il design. Successivamente ho stampato 9 supporti contemporaneamente, riempiendo completamente tutta la mia piastra di costruzione e finendo per durare più di 50 ore.
Ho segnato arbitrariamente la parte superiore e inferiore della piastra frontale e della scatola (ricorda che ho ottenuto un'enorme deviazione di 2 mm tra il design digitale e la realtà). Quindi ho iniziato il noioso processo di centraggio di un supporto con il coperchio in posizione, sollevando con cura la parte anteriore, segnando la sua posizione con una matita e passando al supporto successivo. Quando tutto è stato detto e fatto, ho ricontrollato ogni posizione prima di avvitarli definitivamente nella piastra posteriore.
Una nota sulle viti: il design del mio supporto ha una base piuttosto spessa, questo è fatto apposta per assicurarmi che le mie viti lunghe 16 mm non sporgano dal retro della mia piastra posteriore da 8 mm. Un motivo in più per scegliere un compensato più spesso. (Dimentica "vivi, ama, ridi" è "vivi, ama e impara").
Comunque, le prese della luce erano le prossime. Ho scelto l'altezza preferita in cui volevo che le lampadine sporgessero sopra il pannello frontale, quindi ho misurato la profondità a cui dovrebbero essere le prese, sempre posizionando con cura tutto mentre la parte anteriore è chiusa e sollevandola e misurando. Un piccolo dettaglio: ho dovuto prima svitare e rompere un pezzo dell'estremità del cavo di tutte le prese che servivano da serracavo per i cavi quando pendevano orribilmente dal soffitto, ma poiché li stavo montando in supporti stampati personalizzati, non mi servivano affatto. Ancora peggio, il pressacavo ha fatto sì che i cavi resistessero alla curva stretta in cui li stavo forzando, facendo così perfettamente il suo lavoro, … quindi il pressacavo doveva essere eliminato affinché le prese si adattassero ai supporti come volevo.
Ho incollato tutte le prese nei supporti e l'ho lasciato fissare durante la notte con degli elastici che tengono la pressione. Ovviamente ho dimenticato favolosamente di aver comprato 9 lampadine normali e una grossa per la decima luce, questa luce più grande è più sferica invece che a forma di pera, richiedendo una presa che sia posizionata più vicino alla parte anteriore della scatola rispetto a tutte le altre luci.(Vivere e imparare)
Sono stato quindi costretto a rompere la colla, (rompendo solo leggermente la mia stampa 3D) per liberare lo zoccolo e riposizionarlo. Dopo abbondanti quantità di ulteriore colla sia per fissare il supporto che per unirlo alla presa alla giusta altezza, il montaggio delle prese è stato effettuato.
Ho anche avvitato i connettori delle prese della luce a uno dei lati della piastra posteriore.
Passaggio 5: saldatura dell'elettronica a bassa tensione
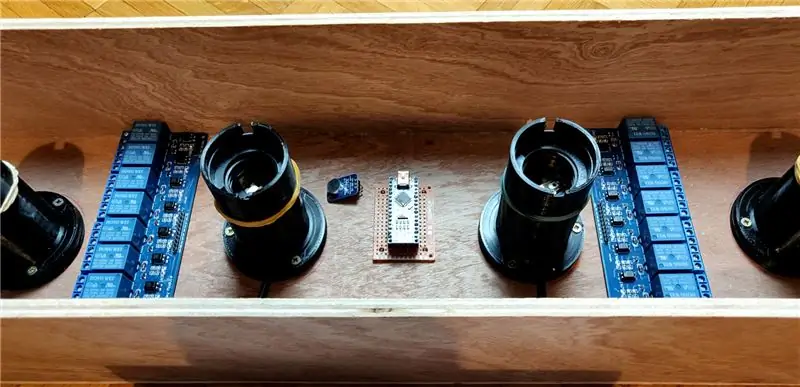
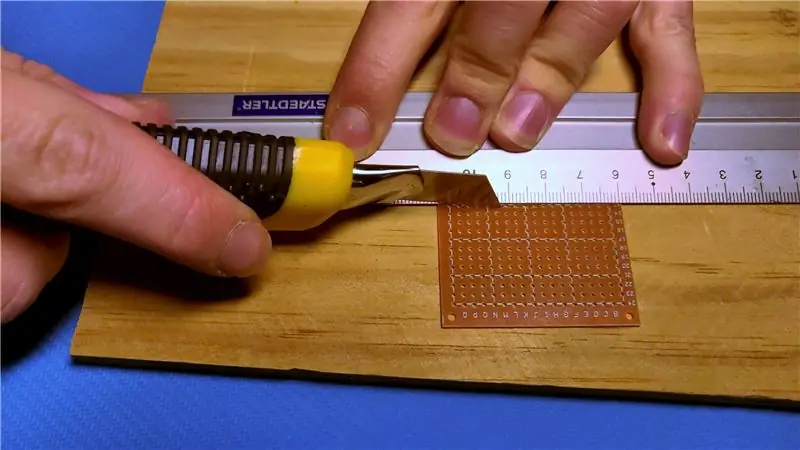
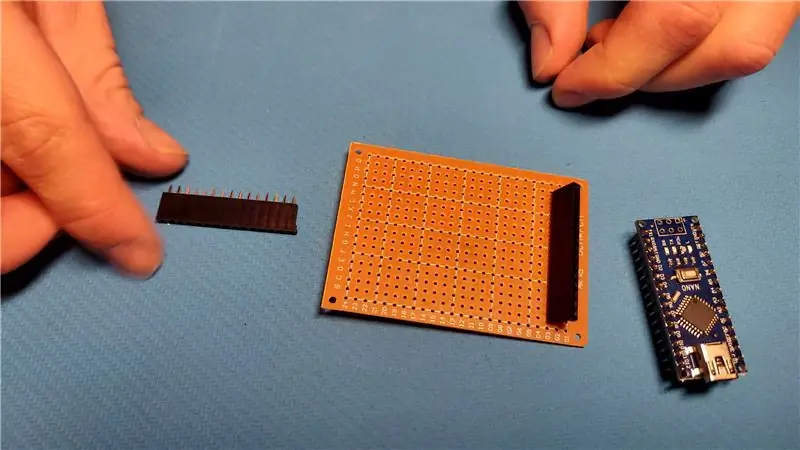
Il prossimo ordine del giorno è "montare a secco" tutta l'elettronica a bassa tensione nella scatola per avere un'idea di quanto dovrebbero essere lunghe le connessioni saldate tra le parti.
Ho iniziato posizionando l'Arduino nel mezzo tra la luce 5 e la 6 e disponendo i relè nei punti adiacenti sopra e sotto.
Mi sono reso conto che nessuna vite da legno sarebbe entrata nei fori di Arduino nano. Questo viene rapidamente risolto saldando alcune intestazioni femminili su una breadboard saldabile. Le intestazioni terranno l'Arduino e alcuni fori praticati nel circuito accetteranno le viti per legno senza lamentele. Questa scheda saldabile ospiterà anche le intestazioni per il microfono da collegare, i connettori (con cavi) per andare ai relè e il cavo lungo per la scatola del telecomando.
Informazioni sulla scatola remota; Avevo bisogno di due interruttori all'estremità di un cavo molto molto lungo. Sono molto in fondo al palco come percussionista, mentre il metro sarebbe nella parte anteriore del palco. Ho acquistato 20 m di cavo a 4 trefoli che di solito viene utilizzato per saldare le strisce LED. Per ospitare i due interruttori, ho progettato e stampato in 3D una semplice scatola (file STL e F360 di seguito) ma qualsiasi scatola rettangolare con alcuni ritagli per i componenti e i cavi farà il lavoro.
Dopo aver misurato la distanza tra i componenti e aver preso un generoso eccesso su quella distanza, ho riscaldato il saldatore e ho iniziato a saldare.
Saldare tutte le connessioni richiede un po' di pazienza e soprattutto un po' di concentrazione per farlo bene. Ho incluso lo schema di cablaggio che ho usato per effettuare tutti i collegamenti, ma tieni presente che il cablaggio potrebbe essere leggermente diverso se utilizzi componenti diversi. (O se ho commesso un errore nel mio diagramma)
Alla fine il mio cablaggio sembrava come se un uccello stesse cercando di nidificare lì. Tuttavia, miracolosamente non sono stati commessi errori e nulla ha iniziato a fumare all'accensione.
Con tutto collegato potrei avvitare ogni circuito al pannello posteriore su distanziali stampati in 3D. Questi distanziatori servivano a due funzioni: (1) è sempre una buona idea lasciare un po' di spazio tra i circuiti stampati e la piastra su cui li monti. E (2) mi sono già lamentato del fatto che ho viti da 16 mm e compensato da 8 mm e che quindi corro costantemente il rischio di avvitare le viti direttamente nel legno? Sì, i distanziatori hanno anche assicurato che le mie viti non raggiungessero l'altra estremità della scatola di compensato.
[NOTA] Col senno di poi, consiglierei di utilizzare 5 relè per modulo relè. La mia idea di utilizzare due moduli relè a 8 canali era quella di consentire un relè rotto, in quel caso avrei semplicemente dovuto cambiare le connessioni e il misuratore degli applausi sarebbe stato di nuovo attivo. Questo dividerebbe un po' meglio anche le connessioni a 220V sui due moduli, rendendo la gestione dei cavi un po' più… gestibile. (Vivere e imparare)
Passaggio 6: collegamento dei componenti 220V
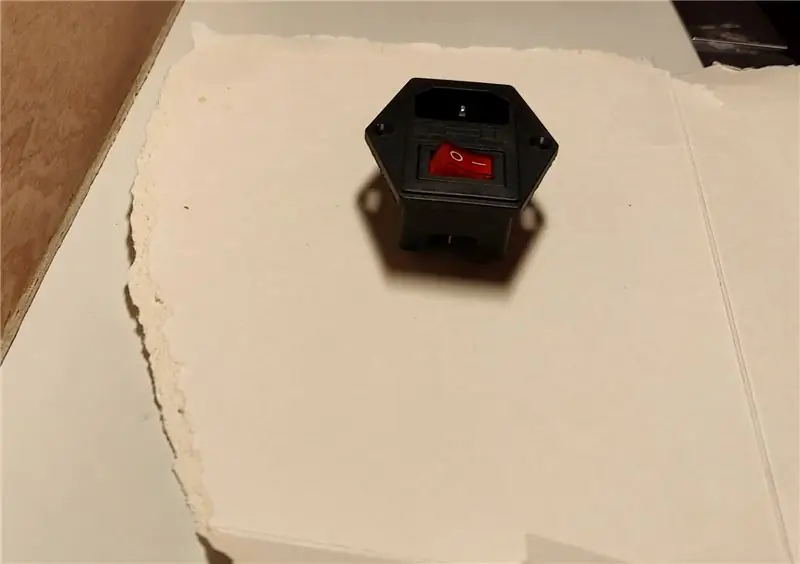
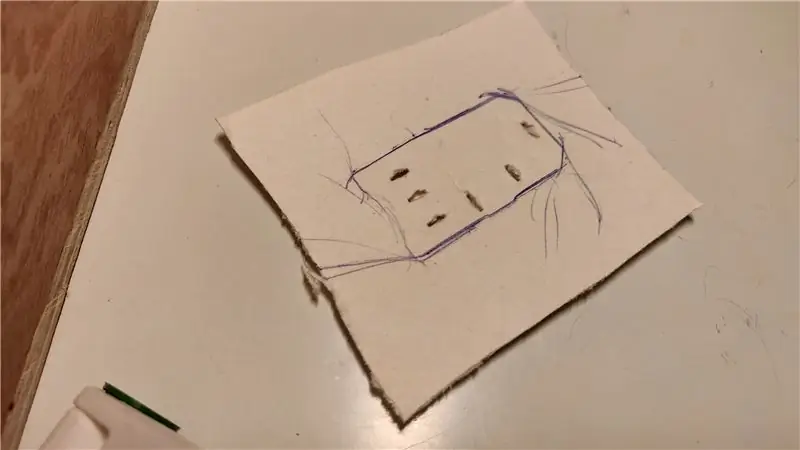
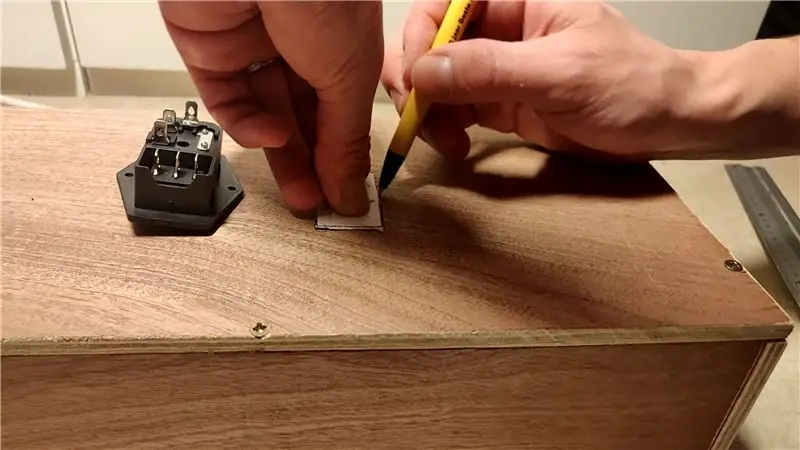
Con tutti i componenti a bassa tensione a posto, è il momento per il lavoro serio e installare il circuito di tensione principale.
Va da sé che mentre si lavora con i fili NON li si collega, in nessun caso, alla rete !!!!!
Insieme al tecnico che avrebbe installato e controllato le luci dello spettacolo per il nostro prossimo concerto, abbiamo deciso di utilizzare una presa di corrente con fusibile come ingresso di alimentazione per il misuratore degli applausi. Ciò ha assicurato che qualsiasi cavo di qualsiasi lunghezza sarebbe stato in grado di adattarsi e fornire alimentazione al nostro contatore.
Inoltre, ciò aggiungerebbe un livello di sicurezza alla nostra configurazione: questi connettori sono dotati di un fusibile che si brucia al di sopra di un certo amperaggio, assicurandosi che nulla si accenda nella cache se non dovrebbe.
Per installare questa spina avevamo bisogno delle sue misure esatte. Ha però una forma piuttosto complessa. Quindi, la cosa più semplice che mi è venuta in mente è premere la spina di alimentazione su un pezzo di cartone e tracciare i contorni della spina. Le linee di contorno possono quindi essere ritagliate producendo una sagoma che può essere trasferita sul legno.
Quando si contrassegna e si ritaglia la posizione per la spina, tenere presente che ci sono già componenti installati all'interno del contatore che non possono più essere spostati, limitando le possibili posizioni in cui la spina può fuoriuscire dalla scatola. Lo stesso vale per il foro di uscita del cavo lungo 20 m per il 'telecomando'.
Normalmente avresti tagliato il buco con un seghetto alternativo, ma non possiedo un dispositivo del genere ed ero impaziente, quindi ho semplicemente praticato dei fori lungo i contorni e ho semplicemente ritagliato il foro con una lama affilata. Funziona, ma non posso consigliarlo perché mi sono quasi tagliato le dita.
Ora si tratta solo di collegare tutto insieme. Ho realizzato uno schema elettrico del circuito 220v per un facile riferimento. Il filo caldo è collegato a tutte le luci in parallelo mentre il filo neutro è interrotto dai relè prima del collegamento alle luci. È così semplice. Assicurati solo di collegare la luce corretta al relè corretto, o dovrai ricollegare l'estremità di controllo a 5 V o i cavi a 220 V per correggere il tuo errore.
C'è un Instructable su come collegare i cavi alla presa di corrente con fusibile che spiega tutto meglio di quanto io abbia mai potuto fare, quindi salta lì, ma ricorda di tornare qui (https://www.instructables.com/id/Wire- Up-a-Fused-AC-maschio-presa di alimentazione/)
[NOTA] Per collegare i fili neutri ai relè posizionati centralmente, ho collegato un filo alla presa con fusibile e l'ho diviso in dieci prima di collegarlo ai relè. Stavo progettando di passare attraverso i cavi neutri ai relè, collegando ogni ingresso relè in parallelo tra loro. Tuttavia, i terminali del relè non accettavano più di un cavo costringendomi a trovare un'altra soluzione. Per effettuare questa suddivisione si consiglia di utilizzare un connettore di qualche tipo. Non ce l'avevo (ed ero impaziente) e ho semplicemente legato tutti i cavi insieme in un grande nodo prima di isolarlo. Non consiglio questo "nodo" per motivi di sicurezza elettrica. SOPRATTUTTO per la sua vicinanza alla scheda Arduino. Comunque sembra funzionare bene.
Step 7: Magnetic Snapper (opzionale)
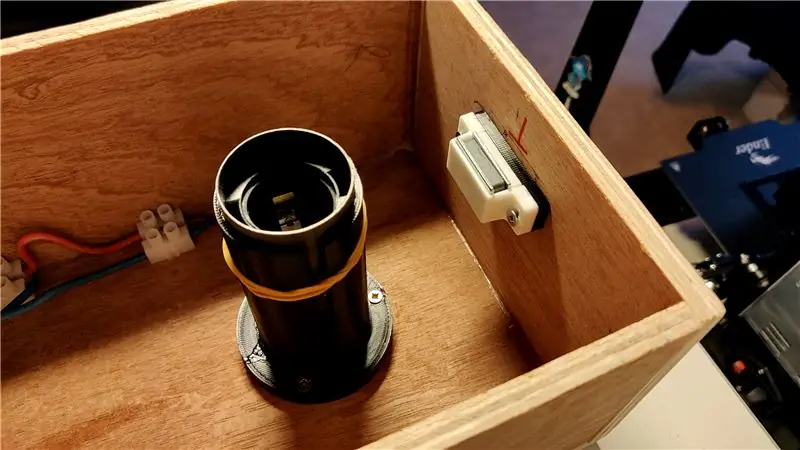
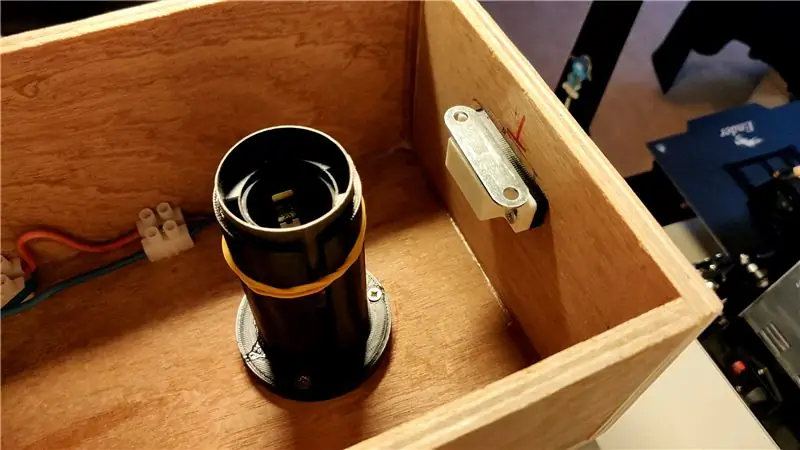
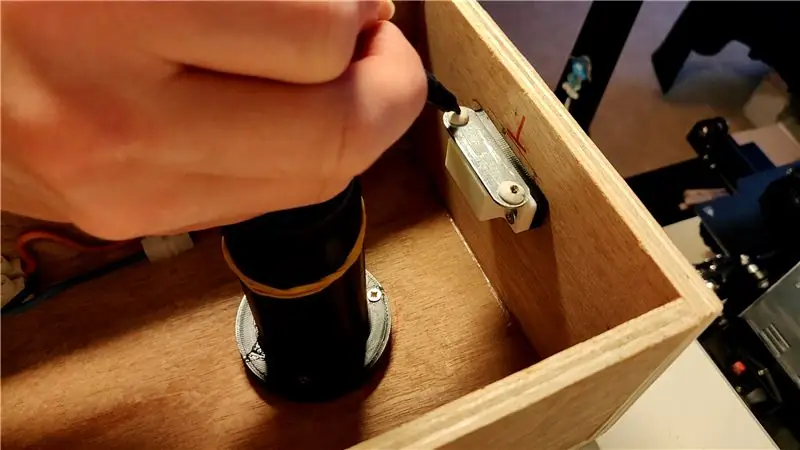
Questo passaggio è del tutto facoltativo, poiché le guide del pannello frontale trattengono sufficientemente la piastra frontale solo per attrito. Ho deciso di includere gli snapper solo come caratteristica di sicurezza, in modo che il pannello frontale non si staccasse senza che io volessi che si staccasse
Rimasi sveglio molte notti pensando a quale sarebbe stato il metodo migliore per tenere il pannello frontale della scatola a cui apparteneva. Alla fine, ho pensato di usare chiudiporta magnetico. Dubito che sia il termine ufficiale per questi eleganti dispositivi, ma li riconoscerete subito. Gli snapper magnetici sono più comunemente usati per tenere chiuse le porte dell'armadio senza usare una serratura.
Ho attaccato la parte magnetica al guscio esterno del misuratore di applausi (pannello superiore, inferiore, sinistro o destro). Questo è stato fatto per mezzo di distanziatori e viti stampati in 3D personalizzati (yadda yadda yadda, viti lunghe, legno sottile, ormai conosci la storia ☺)
Le piastre metalliche sono state avvitate al legno delle guide. Questa è stata anche la prima volta che il legno era abbastanza spesso da non utilizzare alcuno spazio (yay). Ho avuto alcuni problemi con la determinazione della posizione delle piastre metalliche. mi è venuta una soluzione:
- Attacca la parte magnetica alla scatola
- posizionare la piastra metallica sul magnete nella sua posizione perfetta
- sui fori del piatto, posiziona una pallina di "Pritt-buddy" (una sorta di colla da masticare per attaccare poster alle pareti senza puntine, probabilmente andrebbe bene anche una normale gomma da masticare)
- con un pennarello ad alcool fai un punto sulla palla Pritt-buddy nel punto in cui ci sono i fori
- chiudere il coperchio, trasferendo così parte dell'inchiostro del pennarello sul legno
- Solleva il coperchio e tadaa! Hai fatto un piccolo segno dove dovrebbero andare le tue viti
- rimuovere i compagni e la piastra e avvitarlo nella sua posizione corretta, prima provare
- passo 8: profitto
Ho messo quattro snapper magnetici nella scatola: uno in basso, uno in alto, uno al centro a sinistra, uno al centro a destra.
I dentici che ho scelto avevano una forza di tenuta di 6 kg. Con quattro di questi, hanno fornito una forza sufficiente per sollevare quasi l'intera scatola dal solo pannello frontale.
Passaggio 8: cosa farei diversamente
Mentre facevo questo misuratore di applausi ho spesso maledetto il mio passato per aver preso decisioni stupide, elencherò qui le lezioni più importanti che ho imparato:
-
UTILIZZARE COMPENSATO PI SPESSO. Seriamente, realizzare una scatola con compensato da 8 mm è possibile, ma pone molte sfide e impone alcuni compromessi da fare.
- Primo, la perforazione pilota di tutti i fori per le viti è una sfida perché non c'è tolleranza per punte da trapano angolate in modo errato.
- In secondo luogo, le viti che avevo erano da 16 mm (l'ho già detto prima?). Questo mi ha costretto a fare alcuni distanziatori durante l'avvitamento nel legno per evitare che le viti uscissero dall'altro lato, ma allo stesso tempo ciò significava che le viti non penetravano abbastanza in profondità da ottenere una trazione sufficiente per trattenere alcuni componenti.
- ….
- usa solo legno più spesso
Consigliato:
Come fare applauso? Interruttore ON/OFF -- Senza alcun circuito integrato: 6 passaggi
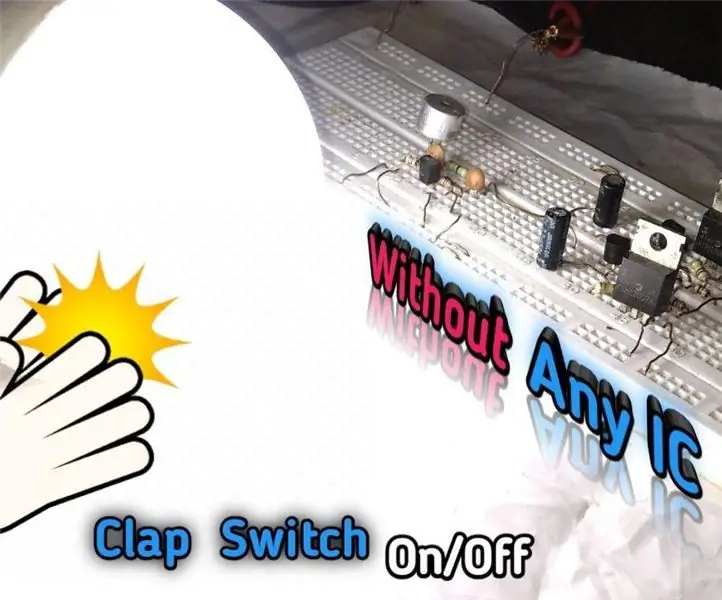
Come fare applauso? Interruttore ON/OFF || Senza alcun IC: questo è un applauso dell'interruttore senza alcun IC. Puoi applaudire? Prima volta poi la lampadina? ACCENDI E batti la seconda volta la lampadina? SPENTO. Questo circuito è basato su flip-flop SR. Componenti 1. Transistor NPN BC547 (4 pezzi) 2. Resistori 10k (5 pezzi)3. 1K di resistenza
Fai da te -- Luce ambiente controllata da applauso: 3 passaggi
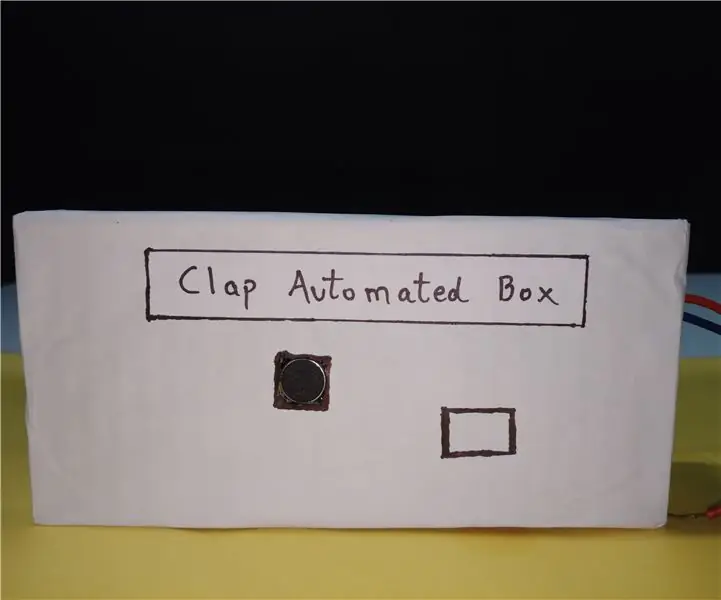
Fai da te || Clap Controlled Room Light: ti sei mai chiesto di controllare i tuoi elettrodomestici con un CLAP? Allora sei nel posto giusto! Qui, ti mostrerò come puoi controllare qualsiasi elettrodomestico sia esso: luci della stanza, ventilatore, televisione o sistema audio con un semplice battito di mani. Questo progetto si basa su
Interruttore di applauso con transistor BC547: 14 passaggi
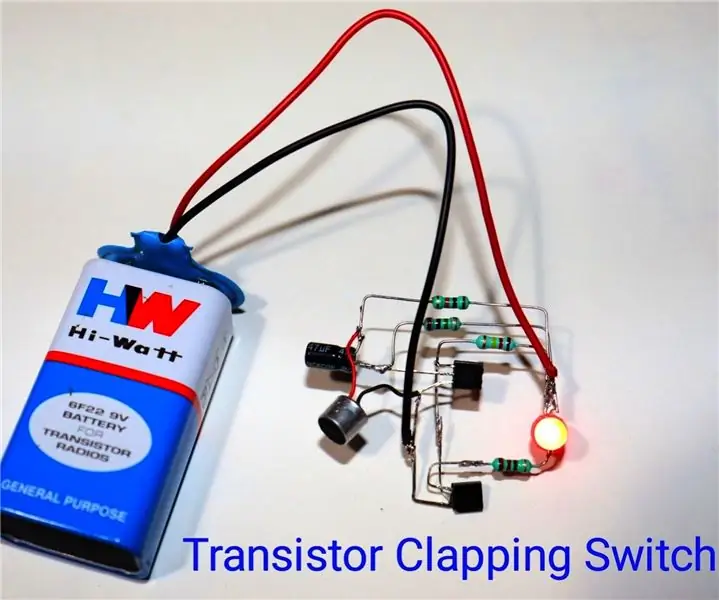
Interruttore di applauso con transistor BC547: Ciao amico, oggi realizzerò un circuito di interruttore di battitura con transistor BC547. In precedenza abbiamo realizzato un interruttore di applauso utilizzando LM555 IC. Cominciamo
Come Realizzare un Circuito di Interruttori ad Applauso: 12 Passaggi (con Immagini)
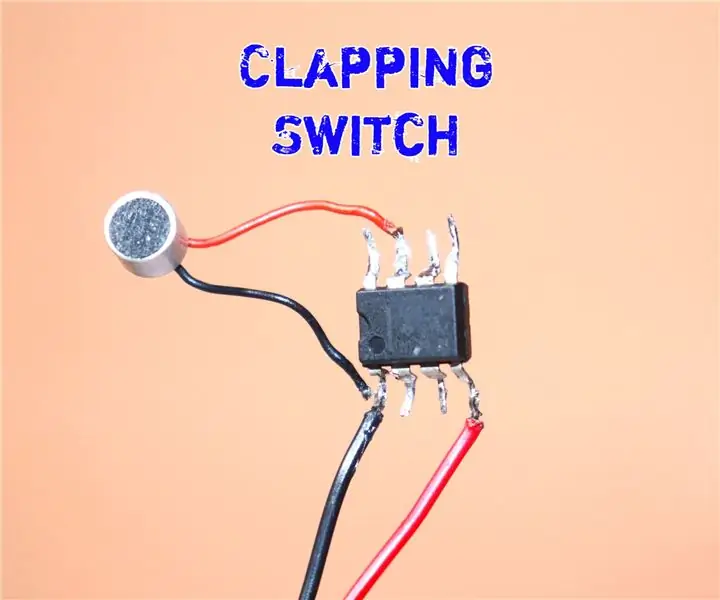
Come realizzare un circuito di commutazione ad applausi: Ciao amico, oggi realizzerò un circuito di interruttore ad applauso. Quando applaudiremo, il LED si illuminerà. Questo circuito è fantastico. Per realizzare questo circuito userò LM555 IC e transistor C945. Facciamo iniziare
Due circuiti dell'interruttore di applauso transitorio: 3 passaggi
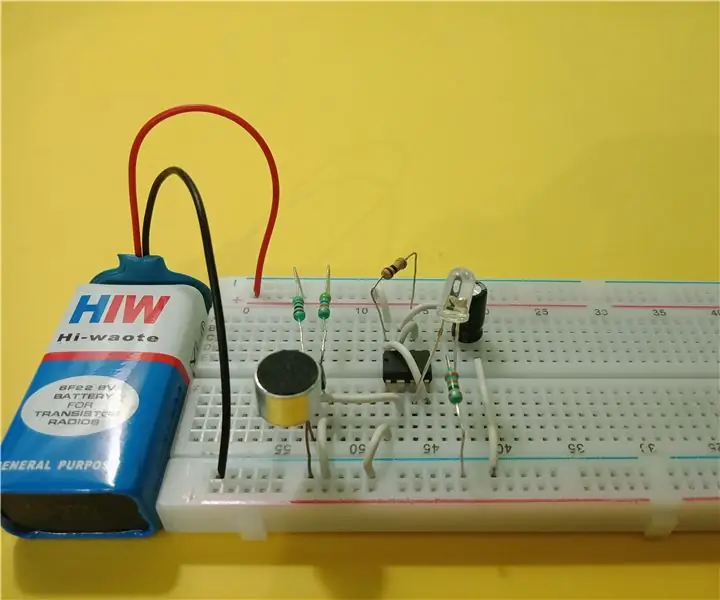
Due circuiti dell'interruttore di clap transitorio: Il circuito dell'interruttore di clap transitorio è il circuito che si accende con un suono di applauso. L'uscita rimane ON per un po' di tempo e poi si spegne automaticamente. Il tempo di attività può essere controllato variando il valore della capacità del condensatore. Più il ca