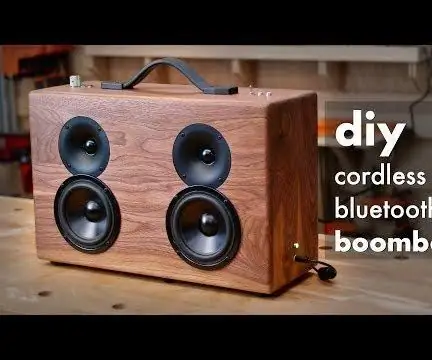
Sommario:
- Passaggio 1: strumenti e materiali
- Passaggio 2: fresatura
- Passaggio 3: ritaglio
- Passaggio 4: schede di orientamento
- Passaggio 5: incollaggio e fresatura
- Passaggio 6: fori per altoparlanti
- Passaggio 7: percorso
- Passaggio 8: divisore centrale
- Passaggio 9: modellatura finale
- Passaggio 10: saldatura
- Passaggio 11: perforazione
- Passaggio 12: porte
- Passaggio 13: finitura
- Passaggio 14: passaggi finali
2025 Autore: John Day | [email protected]. Ultima modifica: 2025-01-23 14:49
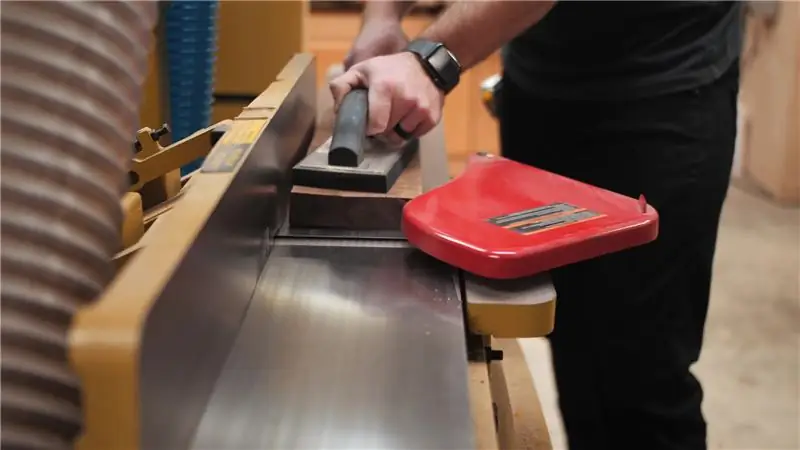
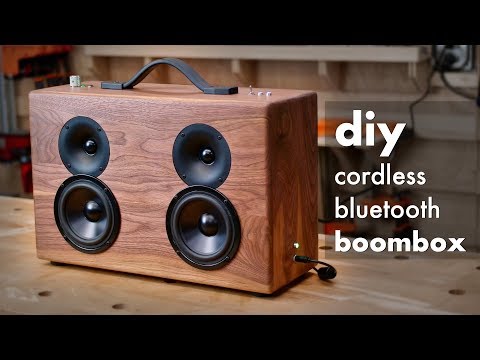
Ho costruito questo altoparlante boombox Bluetooth ricaricabile, alimentato a batteria e portatile utilizzando il kit di altoparlanti Parts Express C-Note più la loro scheda di amplificazione KAB (link a tutte le parti di seguito). Questa è stata la mia prima costruzione di altoparlanti e sono sinceramente stupito di quanto sia fantastico questa cosa.
Grazie a Kirby Meets Audio per aver aiutato con la pianificazione, controlla il suo canale qui.
Questo design boombox è fortemente ispirato a questo boombox di The Hifi Case, se vuoi acquistare un altoparlante come questo, dai un'occhiata qui.
Ottieni il tuo merch Build It Yourself!
Passaggio 1: strumenti e materiali
Materiali:
- Ricambi Kit altoparlanti da scaffale Express C-Note
- Scheda amplificatore Dayton Audio KAB-250v3
- Pacchetto cavi funzione Dayton Audio KAB-FC
- Dayton Audio KAB-BE 18650 Scheda di estensione della batteria
- Dayton Audio KAB-PMV3 Montaggio a pannello (questo non era disponibile quando ho costruito il mio stereo portatile, avrebbe semplificato le cose)
- Sonic Barrier 1/2 schiuma acustica (necessari 2 fogli)
- Crossover perforato bianco
- Viti Nere
- Jack CC per montaggio a pannello da 2,5 mm
- Manopola del volume
- 18650 batterie
- Alimentazione elettrica
- Piedini in gomma
- Terminali a crimpare
- Maneggiare
- Poliestere lavabile
Utensili:
- Troncatrice Festool Kapex
- Trapano avvitatore a batteria Festool CXS
- Trapano avvitatore a batteria Festool PDC 18/4
- Festool ETS EC 150/5 Levigatrice
- Festool OF 1400 Fresatrice
- Pialla Powermatic 15HH
- Giunto Powermatic PJ-882HH
- Inventables X-Carve
- Punta arrotondata con raggio da 3/8"
- Fresa a filo
- Morsetti Paralleli
- Punta svasata
- Sega a nastro Featherboard
- Sega da tavolo Featherboard
- Indicatore angolare digitale
Passaggio 2: fresatura
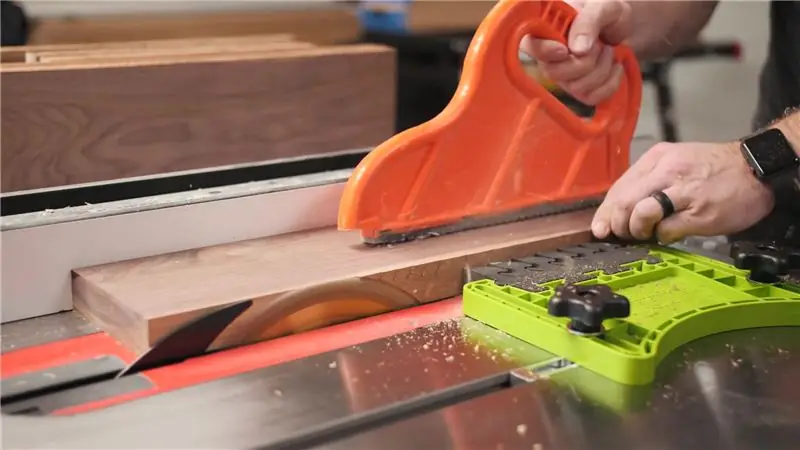
Ho costruito questo boombox in massello di noce, quindi ho iniziato scomponendo il mio legname grezzo nei singoli pezzi. Se si desidera semplificare questa costruzione, è possibile utilizzare prodotti in fogli come compensato o MDF o semplicemente acquistare legname prefresato.
Dopo aver tagliato le tavole a una lunghezza approssimativa con la troncatrice, le ho squadrate con la fresatrice, la piallatrice e la sega da banco.
Ho acquistato 6/4, o 1 ½ "di spessore, Walnut per questa build e volevo uno spessore finale di ½" su queste schede, quindi dopo ho dovuto segare tutte le mie schede, praticamente dividendole a metà.
Passaggio 3: ritaglio
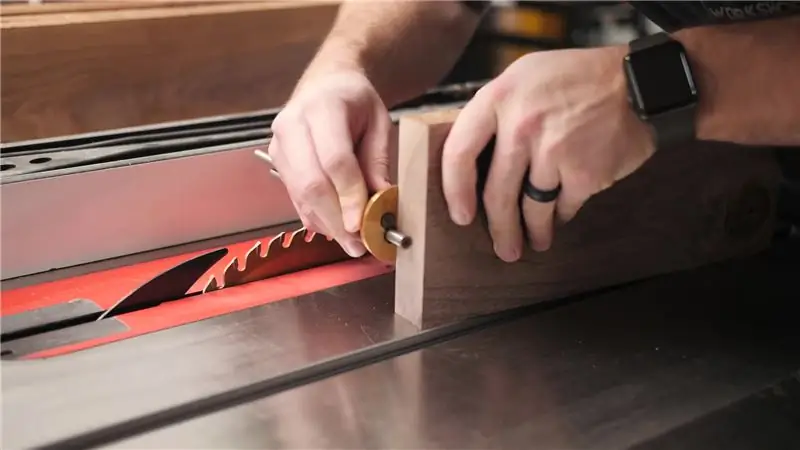
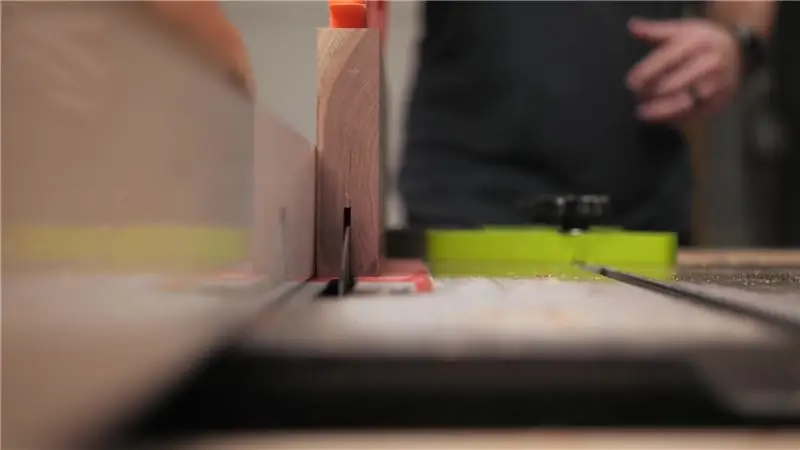
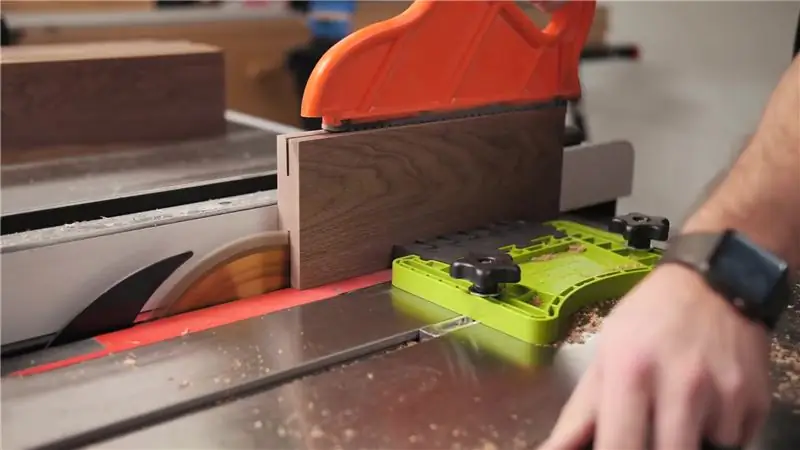
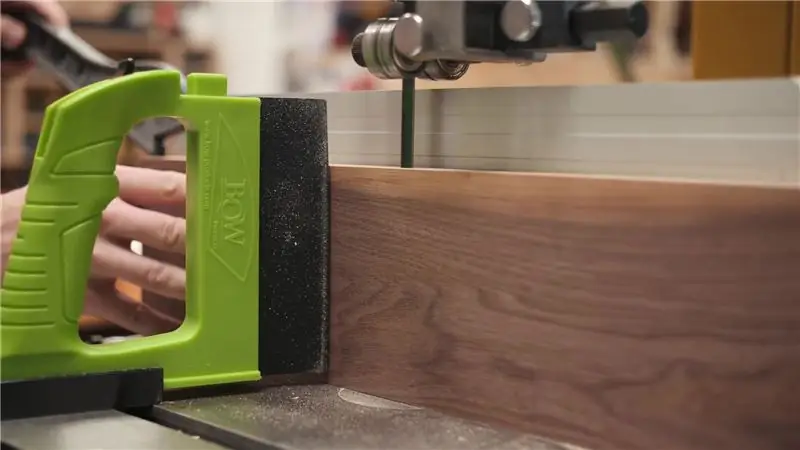
La lama della mia sega a nastro era estremamente smussata, quindi ho deciso di fare la maggior parte del lavoro di sega con la sega da tavolo. Per fare questo, ho prima segnato il centro della tavola usando un calibro e poi ho impostato la recinzione in modo che la lama passasse attraverso il centro della tavola. Ho anche aggiunto una tavola di piume per aiutare a mantenere la tavola spinta contro la recinzione.
Volevo fare questo taglio in più passaggi, quindi ho iniziato con la mia lama a circa un pollice dal tavolo e ho fatto il primo passaggio. Ho quindi capovolto il tabellone da un lato all'altro, assicurandomi che la stessa faccia fosse contro la recinzione, quindi ho effettuato il passaggio sull'altro bordo del tabellone.
Ho ripetuto questo processo per tutte le tavole, quindi ho alzato la lama abbastanza in alto in modo che circa ¾ di materiale rimanesse al centro delle tavole. Non volevo tagliare fino in fondo alla sega da tavolo, solo rimuovere la maggior parte dei rifiuti. Ho ripetuto i passaggi con la lama più alta e poi sono passato alla sega a nastro.
Ho posizionato un'altra tavola di piume sulla sega a nastro per aiutare a mantenere la pressione contro le tavole, e poi ho ricucito tutte le tavole, dividendole completamente.
Alla fine, alla pialla, ho potuto appiattire completamente le tavole e rimuovere la piccola cresta rimasta al centro delle tavole.
Prima di incollare i pannelli, avevo bisogno di tagliare alcune tavole e rimuovere alcune aree che non mi piacevano esteticamente, come queste aree di alburno.
Passaggio 4: schede di orientamento
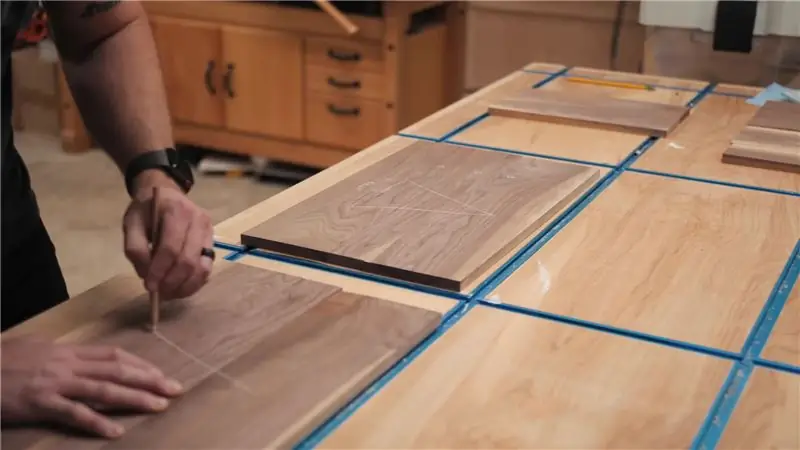
Una volta che tutte le tavole sono state tagliate a misura, le ho sistemate nell'orientamento che ritenevo fosse migliore e poi le ho etichettate in modo da non confonderle durante l'incollaggio.
L'ultimo passaggio prima dell'incollaggio è stato quello di unire ogni bordo, per assicurarmi di ottenere linee di colla perfette. Ho usato questo piccolo trucco che ho preso dal mio amico Jay Bates, dove unisci due assi di accoppiamento con la faccia opposta di ogni tavola contro la recinzione del jointer.
Puoi vedere che ho rivolto la mia linea di matita verso la recinzione sulla prima tavola, quindi lontano dalla recinzione sulla seconda tavola. Questo ha effettivamente annullato qualsiasi minimo errore nella perpendicolarità della mia recinzione e ha assicurato che finissi con uno schermo piatto.
Passaggio 5: incollaggio e fresatura
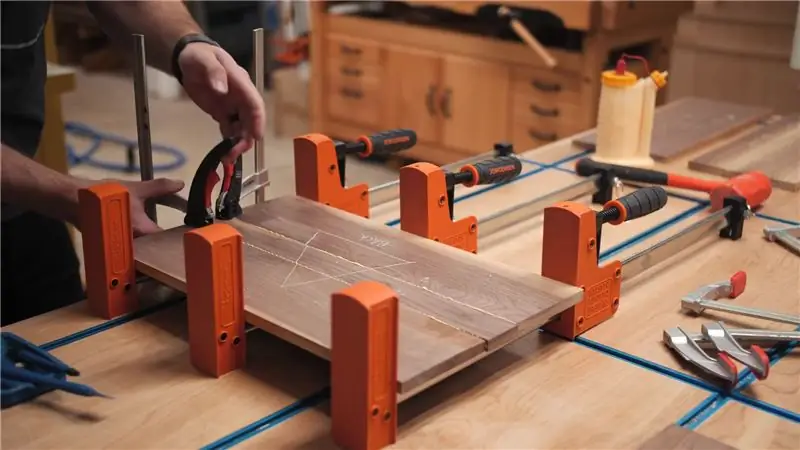
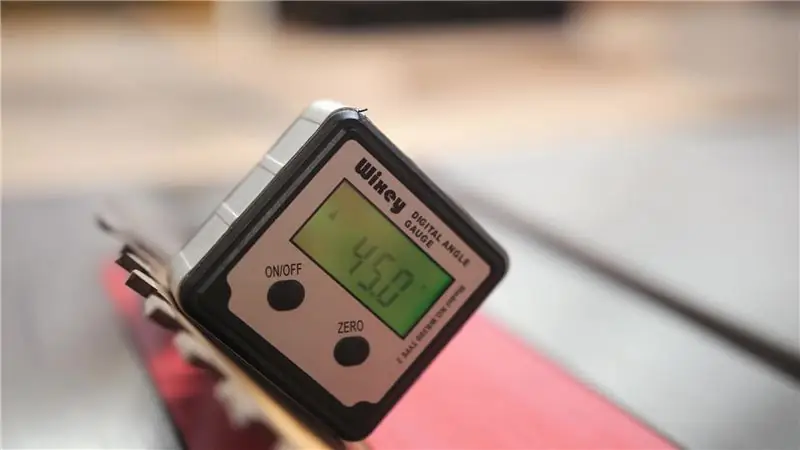
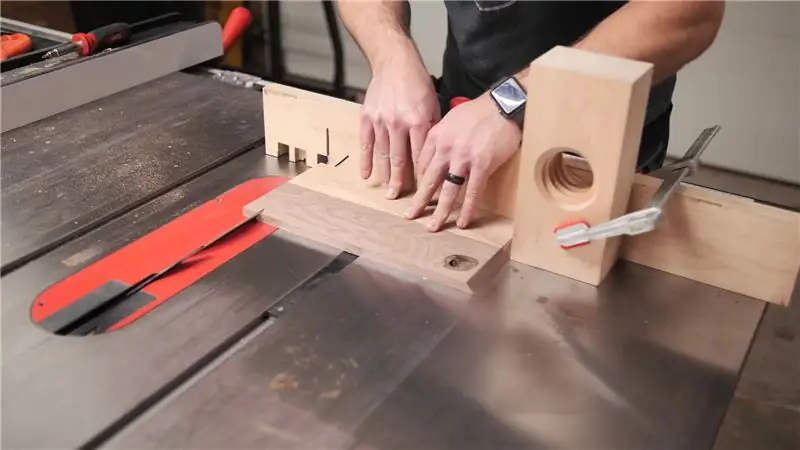
Finalmente ho potuto incollare i pannelli. Non ho usato nulla per l'allineamento su queste schede, soprattutto perché ce n'erano così tante, e mi sono assicurato di aggiungere morsetti alle estremità delle cuciture per mantenerle in linea.
Dopo aver lasciato riposare le tavole nei morsetti per alcune ore, ho raschiato via la colla e poi le ho passate attraverso la pialla per pulirle.
Con le assi ripulite, ho potuto strappare i pannelli superiore, inferiore e laterale alla larghezza finale della sega da tavolo, usando ancora una tavola di piume per aiutare a mantenere una pressione costante contro la recinzione.
Successivamente, ho impostato la mia lama a 45 gradi e ho iniziato a tagliare le mitra. Per prima cosa, ho tagliato una mitra su un'estremità di ciascuna delle assi che componevano il telaio della scatola.
Con un'estremità tagliata a 45 gradi, ho quindi impostato un blocco di arresto sul mio calibro per tagliare l'angolo sull'altra estremità delle tavole. Ciò ha assicurato che i miei pannelli superiore e inferiore, insieme ai pannelli laterali, fossero tutti esattamente della stessa lunghezza.
Alla fine, ho potuto incollare la scatola e ho usato una combinazione di morsetti per cinghie e morsetti per angoli per questo. Ho finito con una scatola perfettamente quadrata e mitra senza spazi vuoti, il che è sempre bello.
Con il telaio della scatola incollato, ho potuto tagliare i pannelli anteriore e posteriore alla dimensione finale in base alla dimensione finale del telaio, e l'ho fatto sulla troncatrice.
Passaggio 6: fori per altoparlanti
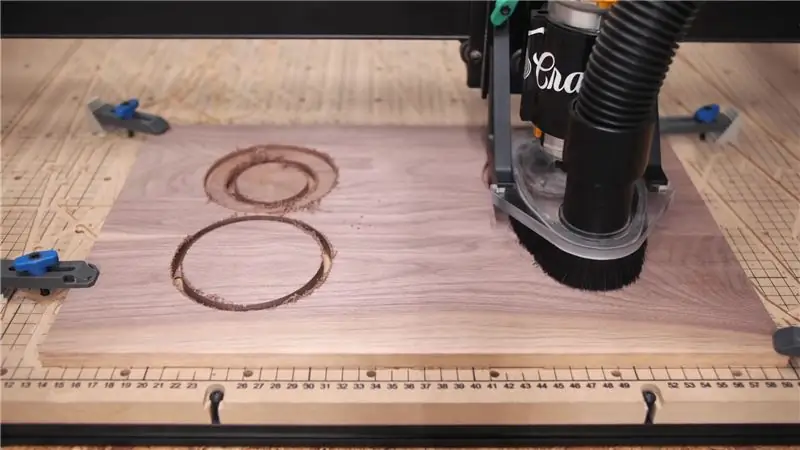
Successivamente, avevo bisogno di tagliare i fori per gli altoparlanti nel pannello frontale. Il kit di altoparlanti che ho usato, il kit C-Note di Parts Express, viene fornito con custodie in MDF e potresti facilmente usare una punta a filo e usare quelle custodie come modelli per tagliare questi fori, ma ho pensato di lasciare che X-Carve fai il lavoro per me.
Ho modellato un progetto rapido in Easel, il software CAM gratuito di Inventables, e ho fatto un taglio di prova su un pezzo di compensato da ½ "per assicurarmi che tutto si adattasse bene. Una volta che ho ottenuto che tutto si adattasse correttamente, ho effettuato il taglio finale sul pannello di noce. L'intera operazione ha richiesto solo circa 13 minuti, super veloce con un bit da ".
Dopo che l'X-Carve è finito, ho tagliato le linguette che tengono in posizione i pezzi rimanenti e poi ho pulito tutto con un rasoio e della carta vetrata.
Passaggio 7: percorso
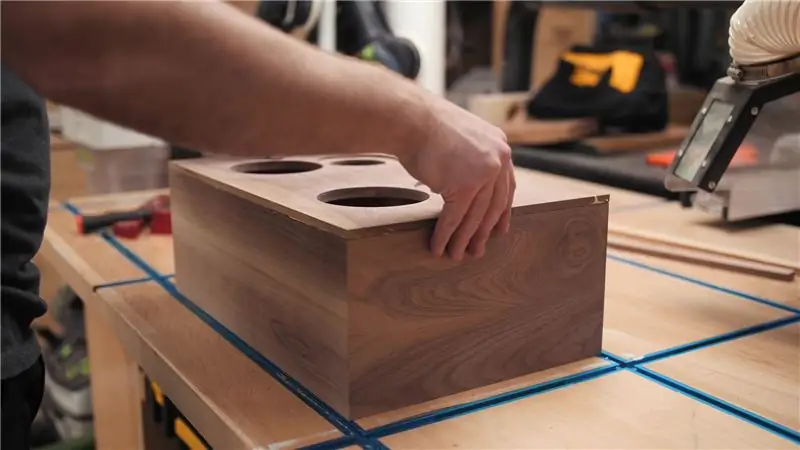
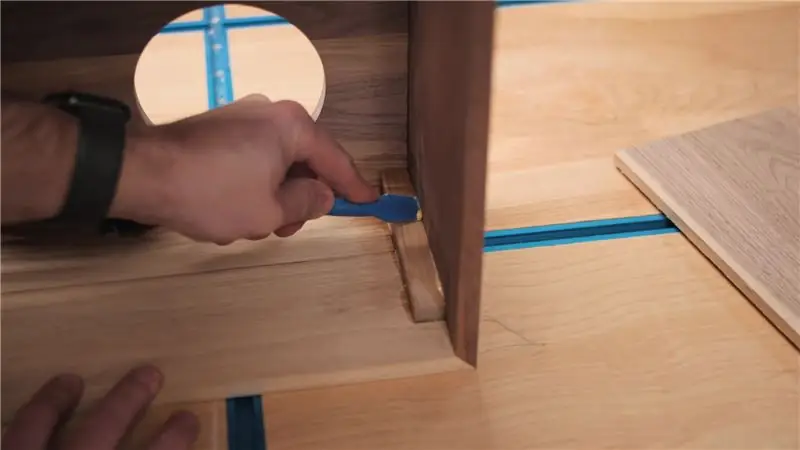
Volevo incassare leggermente i pannelli anteriore e posteriore nel telaio, per dare ai pannelli un kit più sicuro, quindi ho impostato il mio tavolo del router per tagliare una scanalatura di ½ "di larghezza per " di profondità. Ho tagliato queste scanalature su tutti e quattro i bordi dei pannelli anteriore e posteriore, assicurandomi di tagliare prima le scanalature sui bordi lunghi per aiutare a prevenire lo scoppio sul grano finale.
Successivamente, ho incollato il pannello frontale sul telaio e mi sono assicurato di usare molta colla e morsetti per questo. Vuoi una chiusura ermetica sulle casse degli altoparlanti, quindi non puoi davvero esagerare con i morsetti.
Sapevo di volere un pesante arrotondamento su tutti i bordi di questo diffusore, e ciò avrebbe significato rimuovere un bel po' di materiale dagli angoli. Per questo motivo, ho voluto rinforzare gli angoli e ho usato solo alcuni blocchi all'interno della cassa dell'altoparlante per farlo.
Ho usato una combinazione di colla CA e colla per legno per attaccare i blocchi, e la colla CA avrebbe sostanzialmente tenuto i blocchi in posizione mentre la colla per legno si asciugava.
Avevo anche bisogno di aggiungere altri blocchi all'interno dei pannelli superiore e inferiore, e questi sono i punti in cui si collegheranno le viti che fissano il pannello posteriore, che volevo fosse rimovibile.
Passaggio 8: divisore centrale
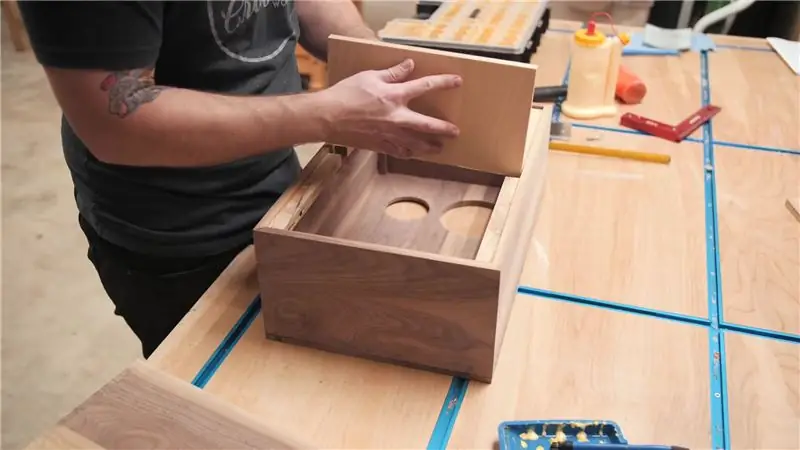

L'ultimo pezzo da aggiungere alla cassa dell'altoparlante è stato il divisorio centrale, di cui francamente mi sono dimenticato. Puoi vedere che avevo bisogno di intagliare i blocchi in alto e in basso per fare spazio al divisorio, che ho ritagliato dal compensato di betulla baltica da ½ . Ancora una volta, mi sono assicurato di usare molta colla qui, perché volevo una chiusura ermetica.
Avevo anche bisogno di aggiungere un'altra battuta al centro del pannello posteriore, in modo che non interferisse con il divisorio centrale, e l'ho tagliata alla sega da tavolo.
Ho bloccato il pannello posteriore in posizione, forato e svasato, quindi ho aggiunto viti da 1 per tenere il pannello posteriore in posizione.
Passaggio 9: modellatura finale
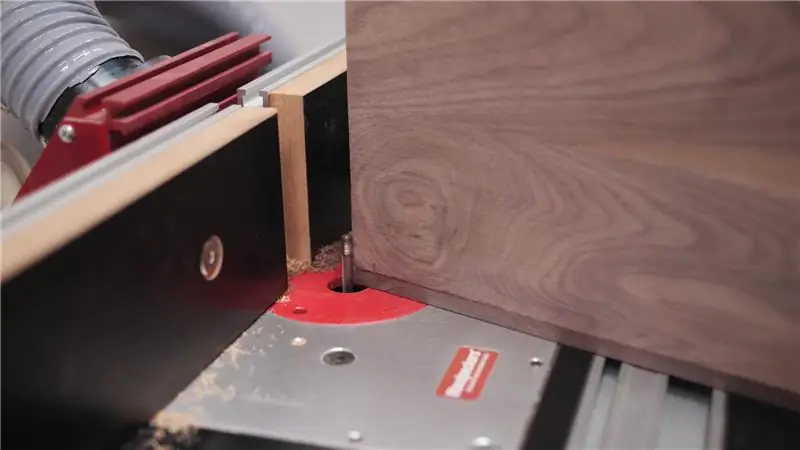
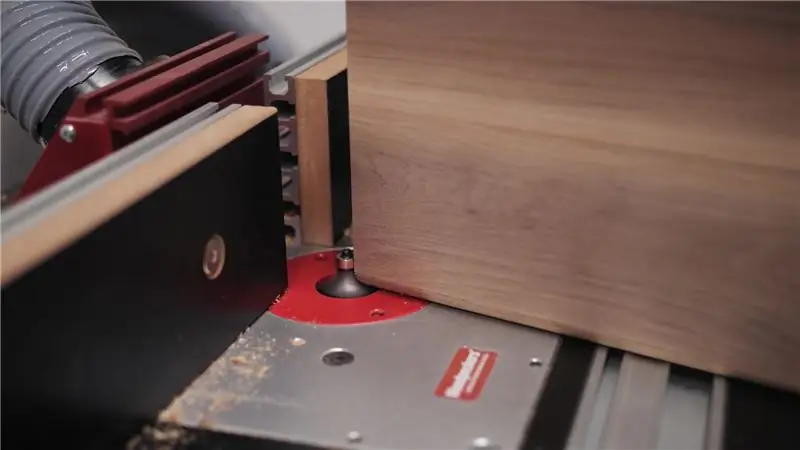
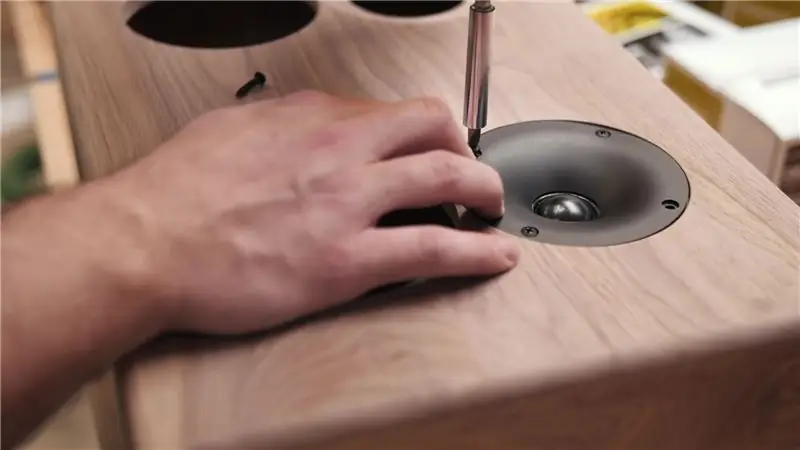
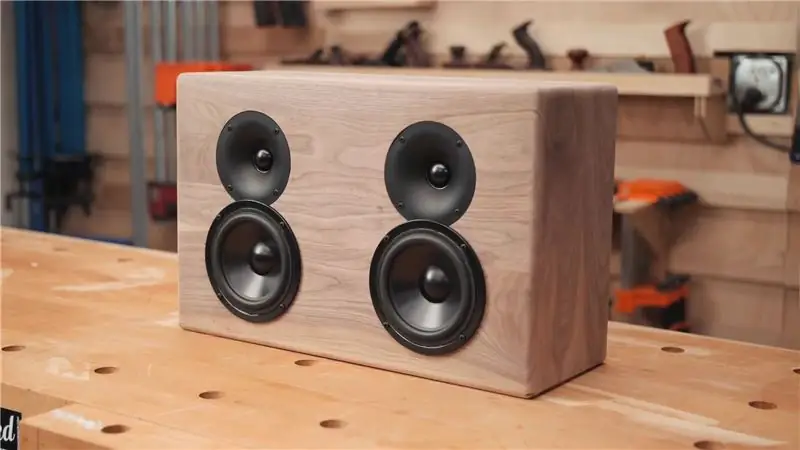
Con la scatola costruita, potrei passare a ripulirla. Per prima cosa, ho usato una punta a filo sulla tavola della fresatrice per pulire eventuali aree sporgenti sui pannelli anteriore e posteriore, che ho tagliato leggermente sovradimensionato.
Una volta che i bordi sono stati lavati, sono passato a una punta arrotondata con raggio di ⅜ e ho aggiunto un arrotondamento a tutti i bordi della scatola. Sono sempre stupito di quanta differenza faccia un profilo del bordo pesante come questo, e penso davvero che questo roundover abbia reso l'aspetto dell'altoparlante.
Infine, ho potuto installare gli altoparlanti, il che è stato semplice. Mi sono solo assicurato che i fori delle viti fossero quadrati rispetto all'armadio e ho usato una punta da trapano autocentrante per preforare i fori. Ho quindi utilizzato viti nere da per fissare gli altoparlanti e ho potuto ottenere uno scatto di bellezza per i miei social media.
Passaggio 10: saldatura
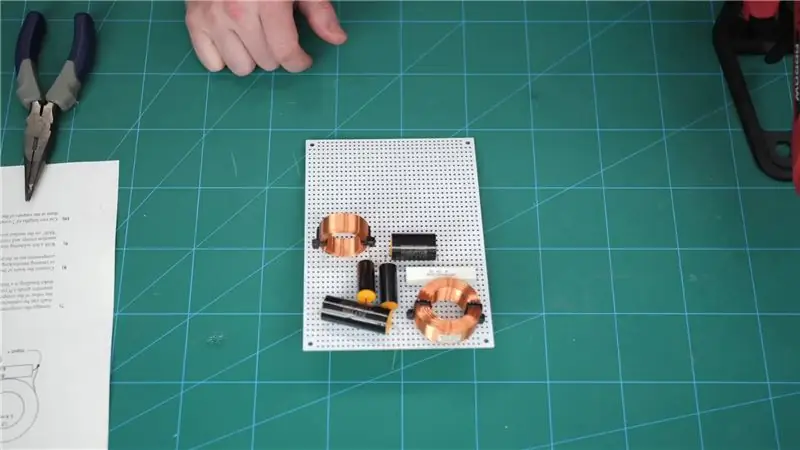
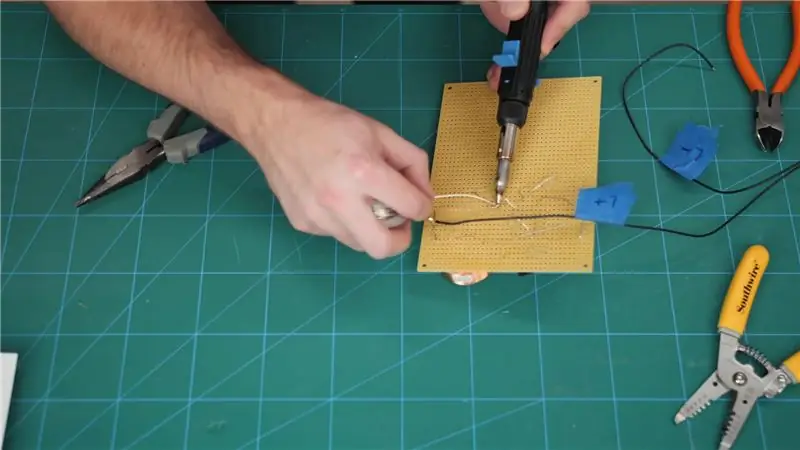
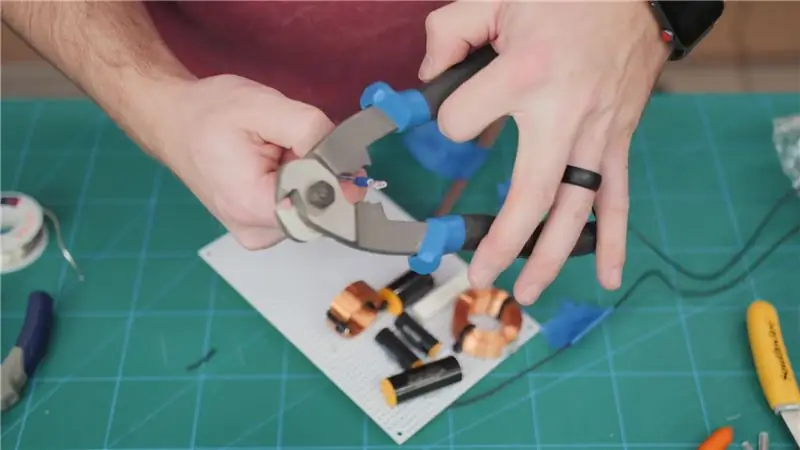
La fase successiva della costruzione è stata la parte per cui ero un po' nervoso, la costruzione dei crossover. Questa era la mia prima volta che saldavo e c'erano un sacco di connessioni da saldare qui. Nel caso non lo sapessi, i crossover dividono il segnale audio tra woofer e tweeter, inviando le frequenze più alte ai tweeter e le frequenze più basse ai woofer.
Di nuovo, questi crossover facevano parte del kit di altoparlanti C-Note che ho usato per questo progetto e ci sono istruzioni estremamente dettagliate su come cablare i crossover inclusi con quel kit. Fondamentalmente, avevo bisogno di collegare i diversi componenti del crossover stesso e anche aggiungere cavi per collegare i crossover agli altoparlanti e all'amplificatore.
Mentre sto saldando, parliamo dello sponsor del video di questa settimana, Bernzomatic.
Ho usato sia il saldatore cordless Bernzomatic ST500 che la torcia di dettaglio ST2200T su questo progetto, e sono entrambi perfetti per l'uso nei lavori di saldatura. Entrambe le torce sono alimentate a butano, il che significa che sono senza fili e completamente portatili, perfette se devi saldare qualcosa lontano da una presa.
Ho anche usato la saldatura elettrica del nucleo di colofonia Bernzomatic per questo progetto, che era estremamente semplice da usare, senza bisogno di flusso. Che tu sia un commerciante professionista, un bricolage, un artigiano, un artigiano o uno chef, Bernzomatic ha il prodotto giusto per innumerevoli progetti. Per saperne di più sulle torce di saldatura, la saldatura e gli altri prodotti Bernzomatic, controlla il link nella descrizione del video qui sotto e grazie ancora a Bernzomatic per aver sponsorizzato il video di questa settimana.
Dopo aver saldato il jack di alimentazione ai cavi della scheda dell'amplificatore, ho potuto spellare le estremità del cavo dell'altoparlante e aggiungere questi terminali a crimpare per collegare facilmente il cavo dell'altoparlante agli altoparlanti.
Passaggio 11: perforazione
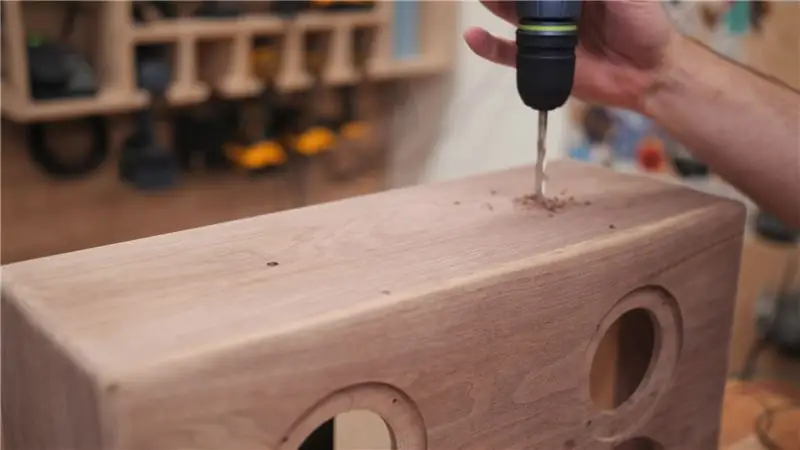
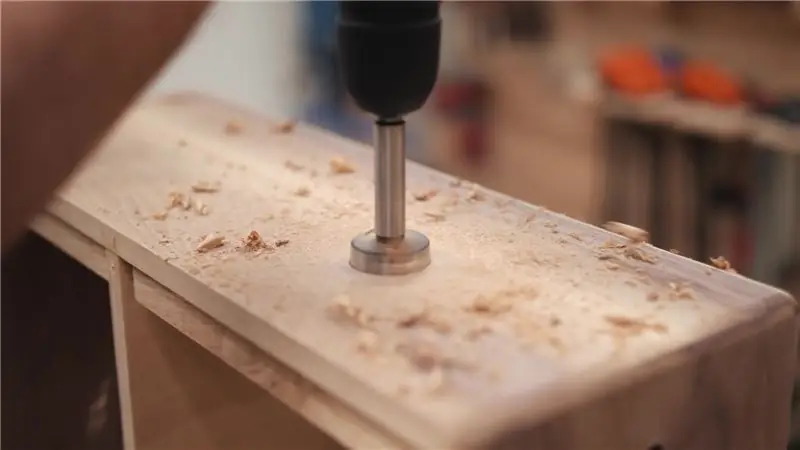
Con tutto il cablaggio completo, potrei passare all'aggiunta di fori per le varie porte, LED, interruttori e maniglia per il trasporto. Questa è stata una delle parti più noiose della costruzione, poiché molti di questi componenti avevano perni di dimensioni diverse, quindi ho dovuto usare un calibro per trovare la dimensione corretta della punta per preforare i fori.
Avevo anche bisogno di utilizzare una punta Forstner all'interno dell'armadio per consentire il passaggio dei componenti. La maggior parte di queste parti aveva solo un'area filettata di circa ¼ di lunghezza, quindi ho dovuto incassare questi fori per consentire alle aree filettate di sporgere attraverso l'armadio.
Ho anche aggiunto dei piedini in gomma alla parte inferiore del cabinet dell'altoparlante, per evitare che sferragliasse durante la riproduzione di musica.
Passaggio 12: porte
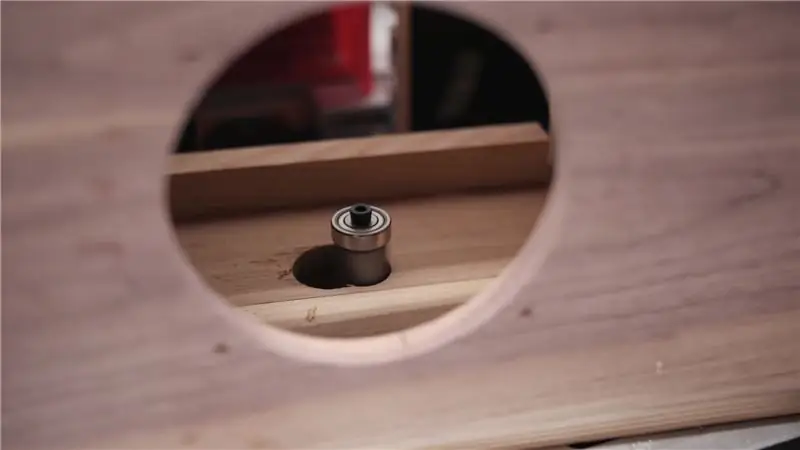
Gli ultimi fori che dovevo praticare erano per le porte sul fondo dell'armadio. Queste porte avevano un diametro di 1 "e non possiedo una punta da trapano da 1 ", quindi dovevo essere un po' creativo qui.
Per prima cosa, ho praticato un foro da 1 , la punta più vicina che avevo a portata di mano, con una punta Forstner, quindi ho usato l'X-Carve per tagliare una sagoma. Ho quindi montato una punta di rifinitura a filo nel mio tavolo del router, ho attaccato la sagoma alla parte inferiore dell'armadio con nastro biadesivo e ho instradato il foro.
Ovviamente, potresti semplicemente acquistare il bit Forstner delle dimensioni corrette, ma non sono riuscito a trovarne uno localmente, questo mi ha fatto risparmiare venti dollari e ho pensato che fosse una soluzione intelligente.
Passaggio 13: finitura
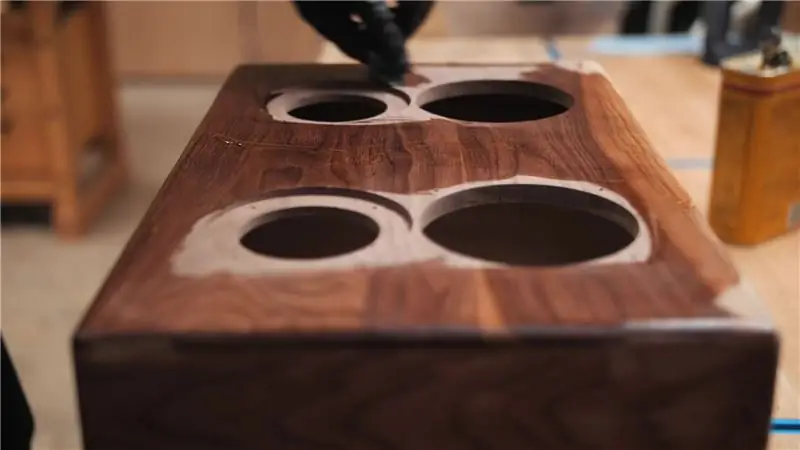
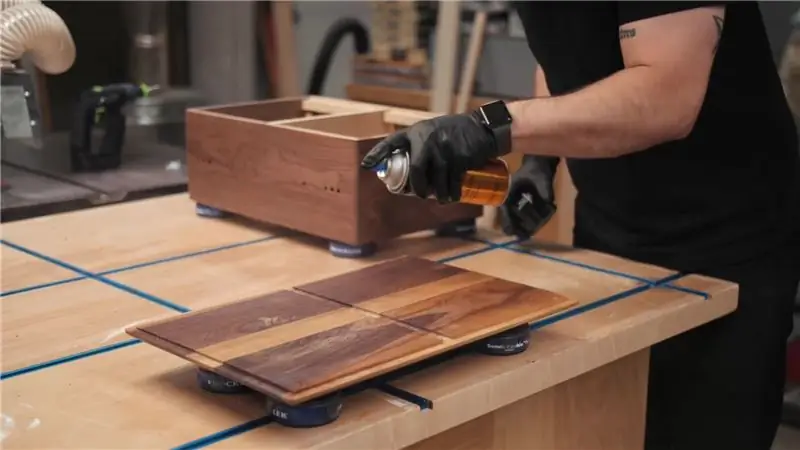
Con tutti i fori praticati nel cabinet dell'altoparlante, tutto ciò che restava da fare era levigare tutto fino a una grana 180 e prepararsi per la finitura.
Per finire, ho optato per una salvietta sul poliuretano, principalmente perché ne avevo lasciato abbastanza nella lattina per usarlo in questo progetto. Ho passato tre mani, lasciando asciugare la finitura per circa 6 ore tra una mano e l'altra. Adoro il modo in cui la finitura ha fatto schioccare la grana su questa noce, bellissima.
Ho anche sigillato l'interno dell'armadio con poliuretano spray, che non sarebbe stato necessario se avessi usato MDF o compensato per la scatola, ma ho pensato che questo avrebbe aiutato a ridurre l'espansione e la contrazione stagionale.
Una volta che la finitura si è asciugata, ho potuto arrivare all'assemblaggio finale del mobile. Innanzitutto, volevo assicurarmi che il pannello posteriore avesse una chiusura ermetica sul cabinet. Ho trovato questo isolamento in schiuma nel centro di casa che si è rivelato perfetto per questa build. È staccabile e incollato e mi sono assicurato di farlo scorrere lungo tutte le aree scanalate sul pannello posteriore.
Quando il pannello viene installato con viti, la schiuma si comprime e forma una perfetta tenuta.
Passaggio 14: passaggi finali
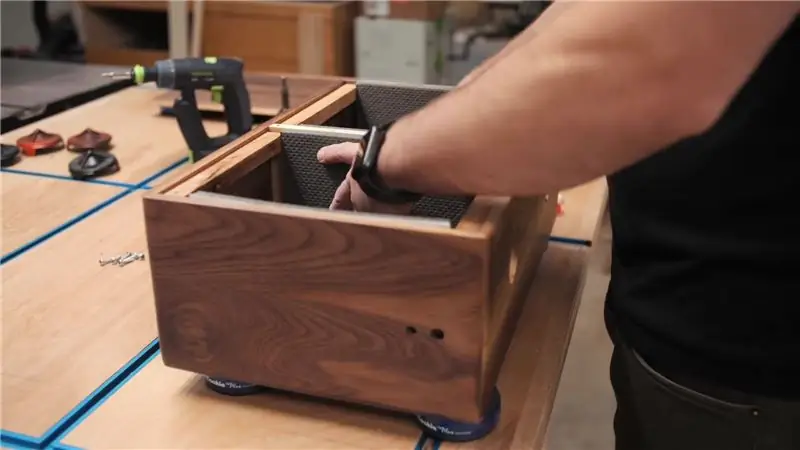
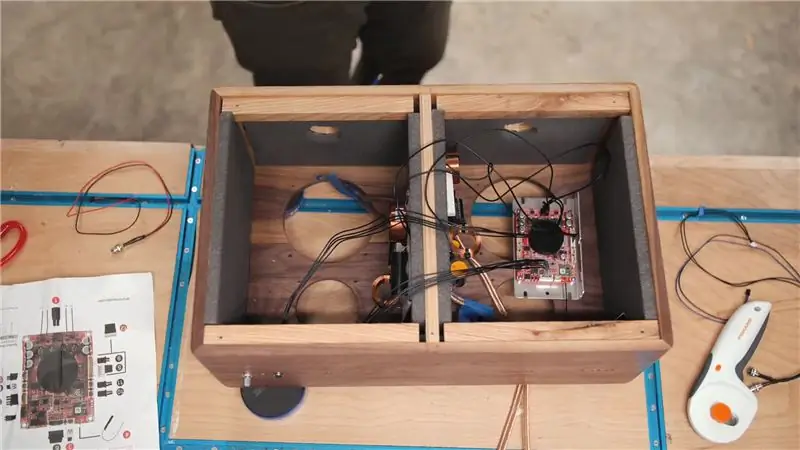
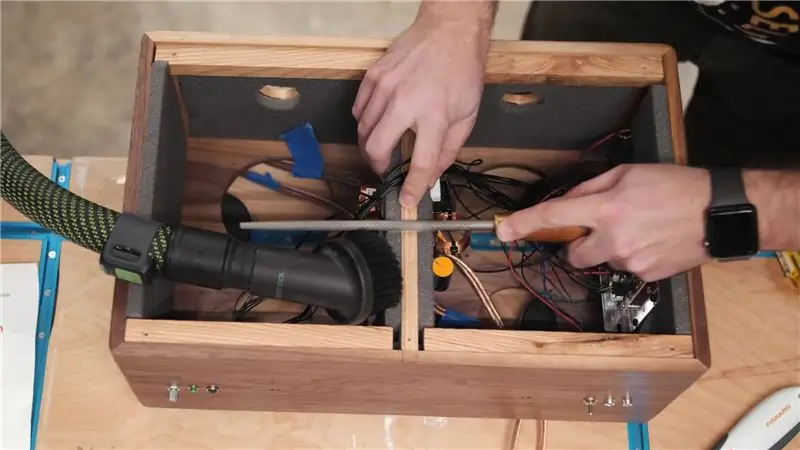
Successivamente, ho aggiunto questa schiuma fonoassorbente da ½ a tutte le facce interne del cabinet ad eccezione del deflettore anteriore. La schiuma ha una buccia e un supporto in stick e l'ho appena tagliata a misura con le forbici, assicurandomi di tagliare attorno a tutti i fori che avevo praticato in precedenza.
Potrei anche far montare i crossover e la scheda dell'amplificatore all'interno del cabinet. Ho usato le viti per farlo e le ho semplicemente avvitate nel divisorio centrale.
Avevo bisogno di aggiungere una scanalatura al divisorio centrale per consentire ai cavi di passare da un lato all'altro dell'armadio e ho semplicemente usato una raspa rotonda per tagliare la scanalatura.
Infine, ho potuto installare tutti gli interruttori, i LED, i piedini in gomma, la maniglia e le porte, collegare il pannello posteriore e quindi inserire gli altoparlanti.
Con gli altoparlanti installati, questo Boombox era finito e non restava che provarlo!
Consigliato:
Altoparlante Bluetooth Zebrano - Come costruire fai da te: 10 passaggi
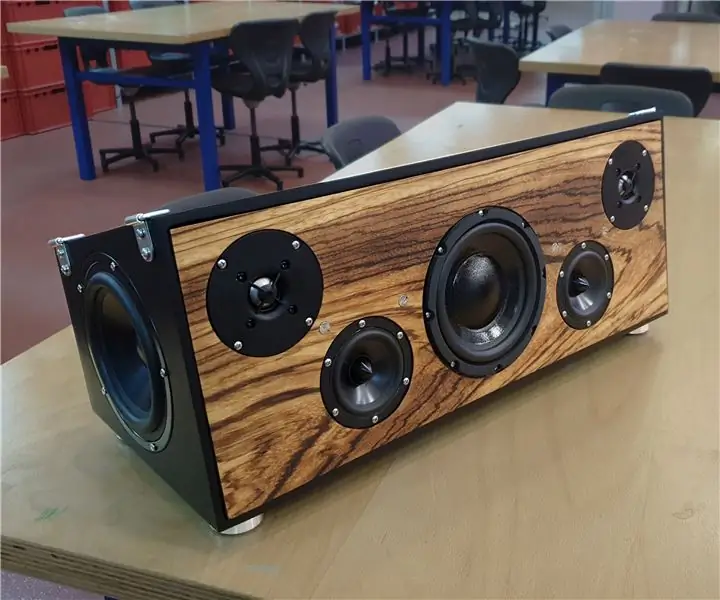
Altoparlante Bluetooth Zebrano - Come costruire fai da te: questo è un altoparlante bluetooth, un design completamente personalizzato con l'accento sulla qualità audio rispetto alla portabilità. Detto questo, se stai cercando un diffusore BT leggero da portare ovunque, questo non fa per te. È dotato di: Batteria 16V - 11700mAh Zebran
Altoparlante Bluetooth in legno fai da te: 8 passaggi (con immagini)
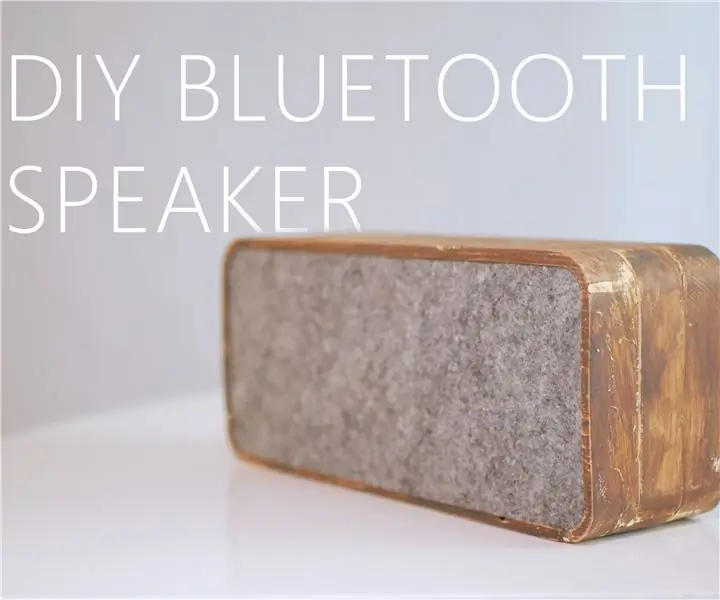
Altoparlante Bluetooth in legno fai-da-te: esistono già migliaia di versioni di questo progetto su Internet. Perché ne faccio uno? Perché voglio :) Ho la mia visione di un perfetto altoparlante Bluetooth (perfetto per me) e vorrei mostrarti il mio processo di progettazione e costruzione! Anche
Indicatore del livello della batteria fai-da-te/spegnimento automatico per batteria da 12 V: 5 passaggi (con immagini)
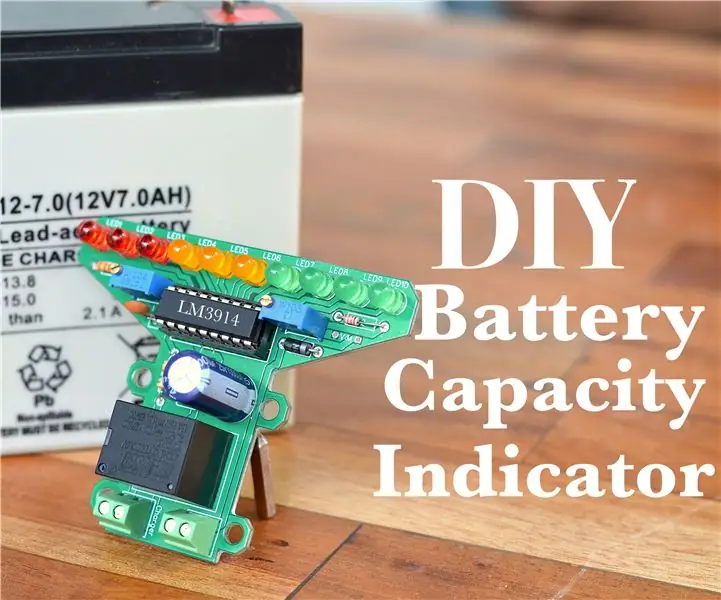
Indicatore del livello della batteria fai-da-te / spegnimento automatico per batteria da 12 V: fai-da-te … Abbiamo tutti attraversato la situazione in cui i nostri caricabatterie di fascia alta sono impegnati a caricare quelle batterie ai polimeri di litio, ma è ancora necessario caricare quella batteria al piombo da 12 V e l'unico caricabatterie che hai ottenuto è un cieco …. Sì un cieco in quanto
Bruciatore alimentato tramite USB! Questo progetto può bruciare attraverso plastica/legno/carta (il progetto divertente deve anche essere un legno molto fine): 3 passaggi
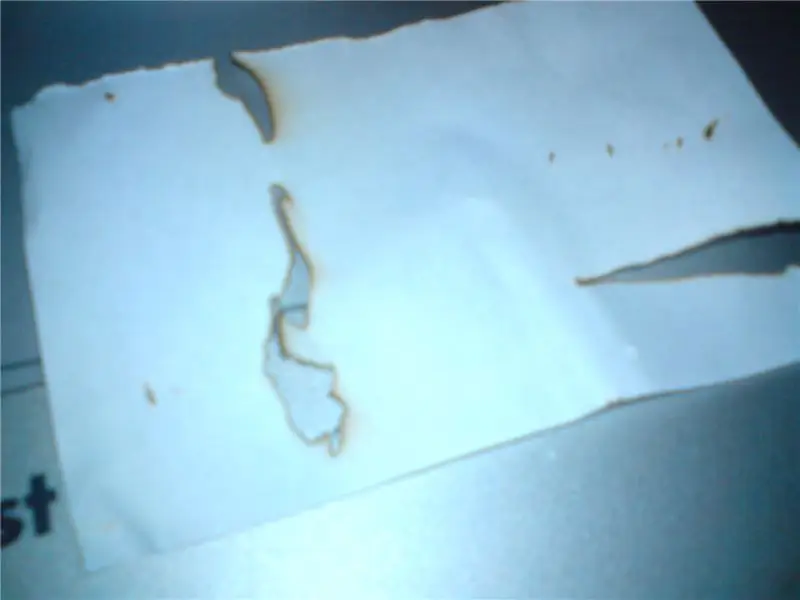
Bruciatore alimentato tramite USB! Questo progetto può bruciare attraverso plastica/legno/carta (il progetto divertente deve anche essere un legno molto fine): NON FARLO UTILIZZANDO USB!!!! ho scoperto che può danneggiare il tuo computer da tutti i commenti. il mio computer va bene comunque Utilizzare un caricabatterie per telefono da 600 mA 5 V. ho usato questo e funziona bene e nulla può essere danneggiato se usi una spina di sicurezza per interrompere l'alimentazione
Come utilizzare la batteria Nokia Bl-5c come batteria del gene HTC: 10 passaggi
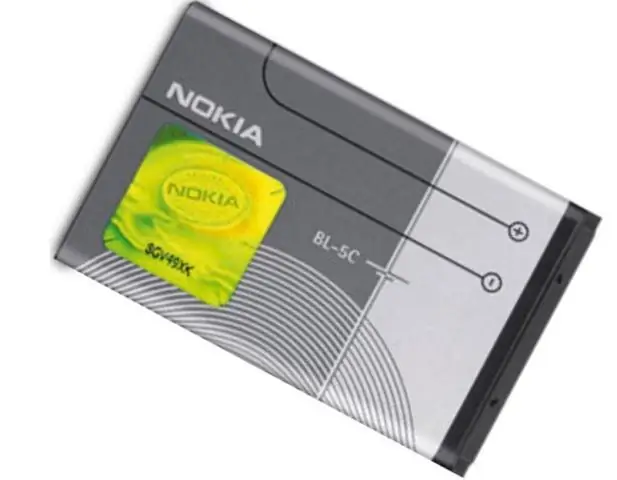
Come utilizzare la batteria Nokia Bl-5c come batteria Htc Gene: ragazzi questo è il mio primo tutorial … quindi per favore abbiate pazienza;) il mio gene di 2 anni aveva bisogno di una sostituzione della batteria in quanto potrebbe fornire un backup di soli 15 minuti. …e la nuova batteria costa circa INR 1000…..mentre frugavo tra le mie cianfrusaglie ho trovato un cellulare Nokia che ho