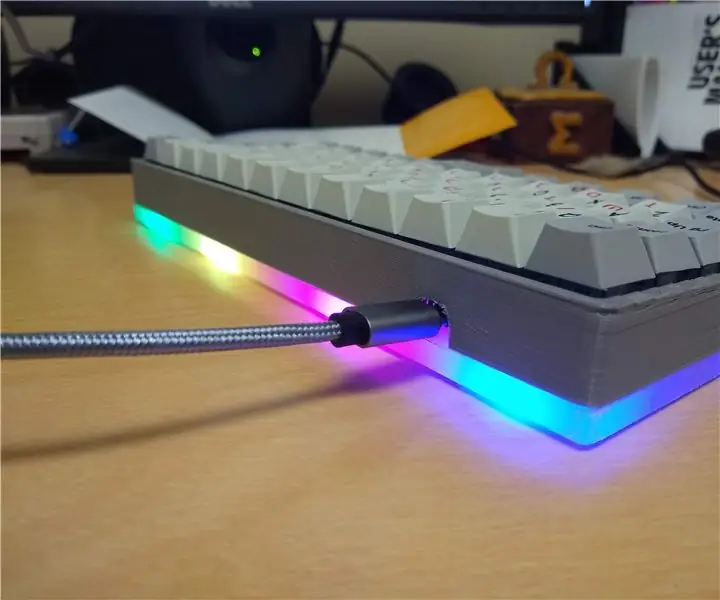
Sommario:
- Passaggio 1: 507 movimenti meccanici
- Passaggio 2: progettazione e modello 3D
- Passaggio 3: AGGIORNAMENTO 01/12/2020
- Passaggio 4: hardware
- Passaggio 5: elettronica e programmazione
- Passaggio 6: assemblare la base
- Passaggio 7: aggiungi interruttori momentanei
- Passaggio 8: aggiungere la piastra di montaggio e i finecorsa
- Passaggio 9: aggiungere motori passo-passo e ingranaggi
- Passaggio 10: aggiungere i rack
- Passaggio 11: aggiungi le barre delle ore e dei minuti
- Passaggio 12: aggiungi lenti di ingrandimento
- Passaggio 13: lezioni apprese
2025 Autore: John Day | [email protected]. Ultima modifica: 2025-01-23 14:49
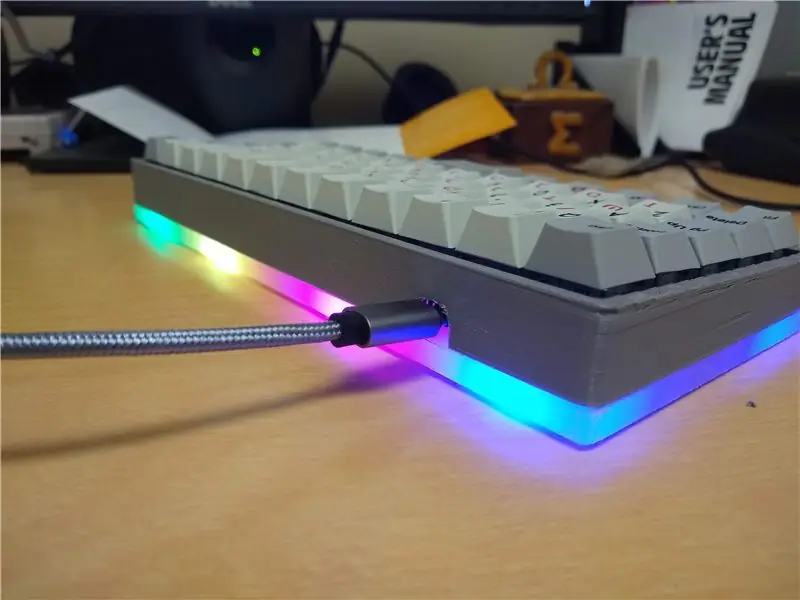
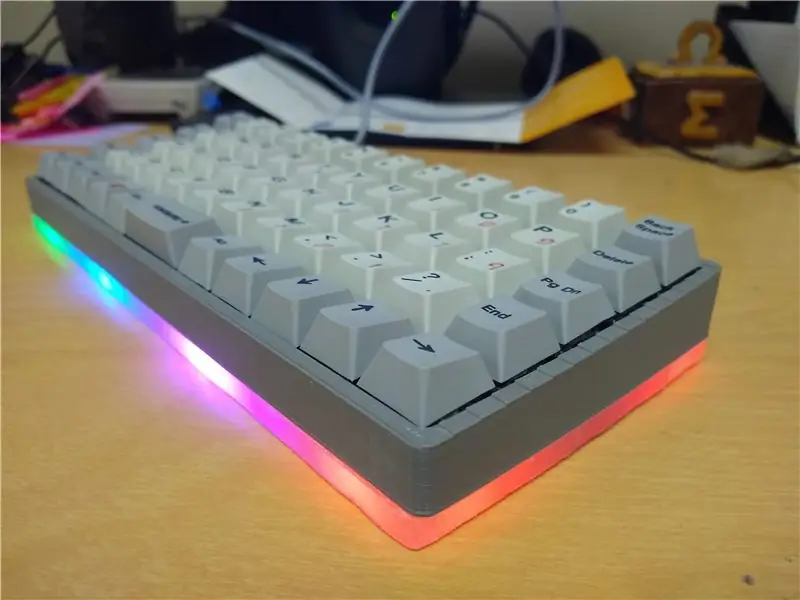
Progetti Fusion 360 »
Non importa quello che ti dice Deepak Chopra, il tempo è lineare. Speriamo che questo orologio sia un po' più vicino alla realtà rispetto a quelli circolari a cui siamo tutti abituati. Gli intervalli di cinque minuti sembrano meno nevrotici rispetto all'essere precisi al minuto, e ogni numero viene ingrandito, ricordandoti di concentrarti sul presente.
L'ho realizzato utilizzando quasi tutte le macchine al Pier 9 (getto d'acqua, sabbiatrice, taglierina laser, stampante 3D, laboratorio di elettronica, ecc.). È realizzato in alluminio 6061, hardware in acciaio (viti, dadi, cuscinetti), ingranaggi stampati in 3D, un Arduino Uno e i pannelli delle ore e dei minuti sono in compensato tagliato/inciso al laser.
Ovviamente so che questo progetto non è accessibile a quasi tutti coloro che non hanno la folle fortuna di avere accesso a un negozio come questo, ma spero che lo troverai stimolante.
Fusion 360 è gratuito per studenti e hobbisti e c'è un sacco di supporto educativo su di esso. Se vuoi imparare a modellare in 3D il tipo di lavoro che faccio, penso che questa sia la scelta migliore sul mercato. Clicca sui link sottostanti per iscriverti:
Studente/Educatore
Hobbista/Startup
Ho anche condotto una serie di corsi di webinar relativi a progetti di modellazione 3D con parti in movimento. In questi webinar imparerai le funzionalità di Fusion 360 come gli assiemi meccanici avanzati (ovvero l'interazione di due o più giunti) e il rendering. L'ultimo webinar si è concentrato sulla modellazione di questo design dell'orologio in Fusion 360. Puoi guardare l'intero video qui:
Se sei interessato, dai un'occhiata agli altri due webinar di questa serie in cui imparerai a progettare una lampada con manopola gigante e un orologio perpetuo con Arduino.
Passaggio 1: 507 movimenti meccanici
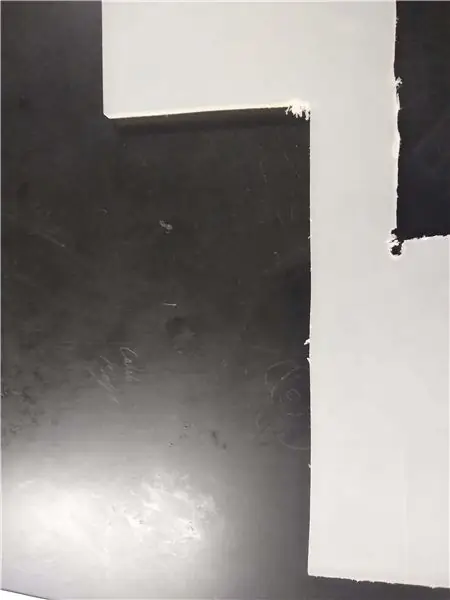
507 Mechanical Movements è un'enciclopedia di meccanismi comuni del 1860 che funge da buon riferimento per questo genere di cose. Questo meccanismo è basato sul Movimento 113, "Rack and Pinion". Questo sarà un progetto lungo, quindi se hai un meccanismo specifico che vorresti che realizzassi, sentiti libero di fare una richiesta nei commenti!
Passaggio 2: progettazione e modello 3D
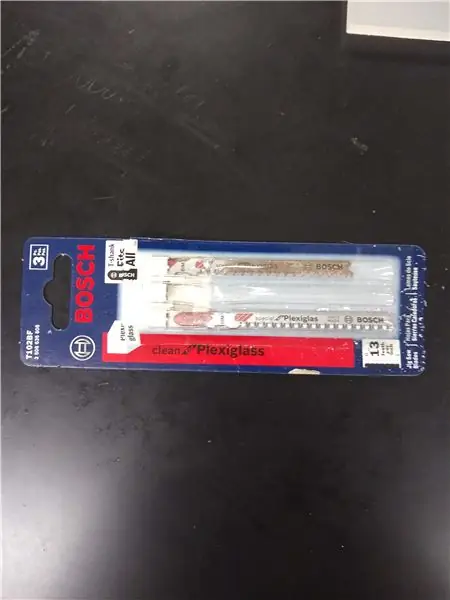
Il video sopra è una registrazione di un webinar che ho fatto per la parte del progetto relativa alla progettazione di pignone e cremagliera.
La parte più difficile del progetto da capire era il gruppo pignone e cremagliera. La matematica per la progettazione degli ingranaggi può diventare piuttosto complicata (in effetti, ci sono ingegneri che fondamentalmente progettano solo assiemi di ingranaggi proprio per questo motivo), ma sulla base di un ottimo tutorial su Youtube di Rob Duarte, ho creato il mio modello che funziona con l'ultima versione del componente aggiuntivo Spur Gear per Fusion.
Il video qui sopra ti guida attraverso il processo di creazione dell'assemblaggio di cremagliera e pignone, ma se vuoi un tutorial più approfondito, per favore unisciti a me per il webinar Design Now Hour Of Making in Motion il 5 aprile. Se ti perdi il webinar, è Verrò registrato e posterò il video qui.

Il modello (link sotto) ha tutti i parametri mostrati sopra già inseriti. Non entrerò nella matematica qui, ma se segui le istruzioni, dovrebbe funzionare per te.
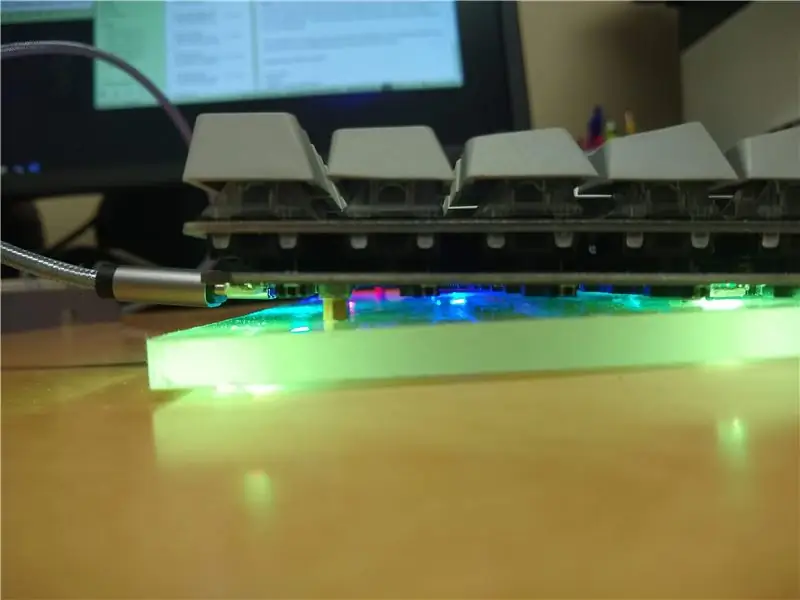
Usa il componente aggiuntivo Spur Gear andando su ADD-INS > Script e componenti aggiuntivi… > Spur Gear > Esegui. Quando ottieni la finestra mostrata sopra, inserisci i parametri. Number of Teeth non ti consente di utilizzare un parametro per il valore, quindi assicurati che corrisponda al valore teethNum se lo cambi. Devi anche moltiplicare i parametri nominati per 1 come mostrato sopra.
Tieni presente che una volta creato l'ingranaggio, puoi modificarlo come qualsiasi altro oggetto in Fusion.
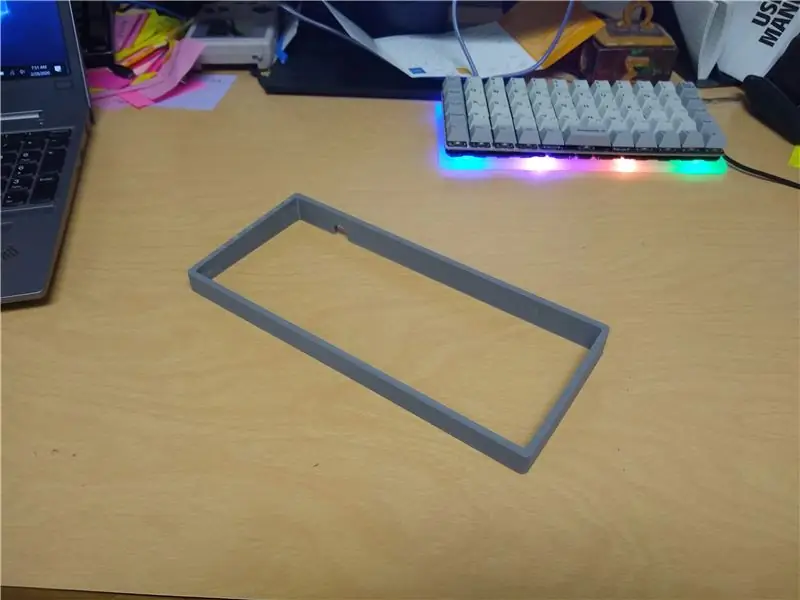
Come mostrato nel video dimostrativo, questo è un esempio di come costruiresti un profilo dentale utilizzando i parametri.
Ecco i collegamenti al modello che puoi utilizzare per creare la tua cremagliera e pignone in Fusion:
Modello con parametri:
Dopo aver capito la cremagliera e il pignone, ho passato molto tempo a modellare motori, interruttori e altre parti elettroniche, quindi a capire tutti i dettagli. Con il collegamento di movimento descritto sopra, sono stato in grado di ottenere una buona immagine di come sarebbe apparso in movimento.
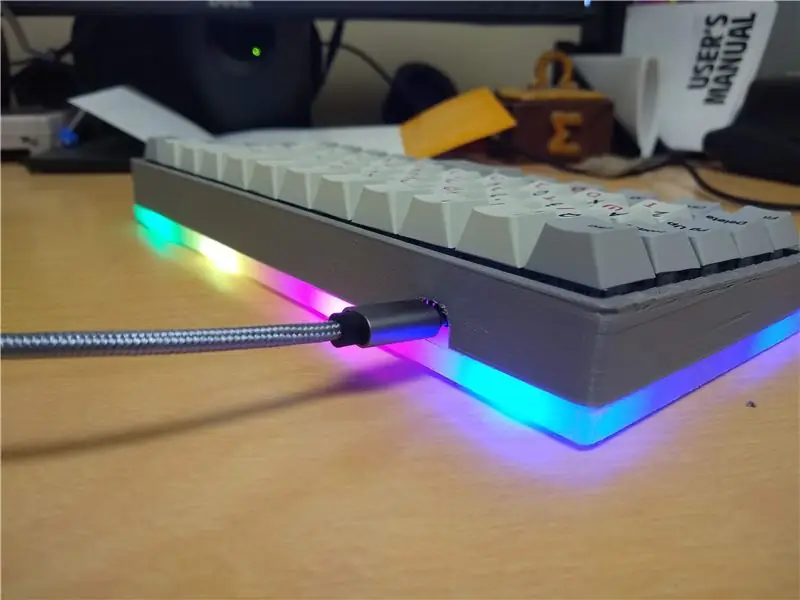
Puoi accedere al file tramite il link sottostante e giocarci o persino provare a creare la tua versione dal file. C'è stato un bel po' di ritocchi e modifiche dopo che le parti sono state realizzate, quindi non aspettarti di essere in grado di tagliare al laser tutte le parti e avere un prodotto finito. Questo progetto è stato costoso e ha richiesto molto tempo! Se sei seriamente intenzionato a farcela e hai bisogno di aiuto, commenta qui sotto e farò del mio meglio per farti andare avanti.
Design dell'orologio finito:
Se non sei già un utente Fusion 360, iscriviti alla mia lezione di stampa 3D gratuita. È un corso accelerato di Fusion per la creazione e la Lezione 2 contiene tutte le informazioni necessarie per ottenere Fusion gratuitamente.
Passaggio 3: AGGIORNAMENTO 2020-12-01
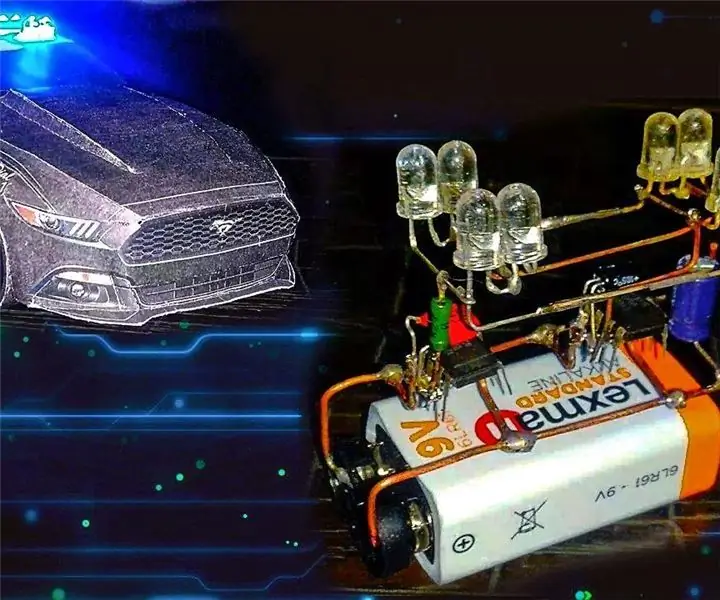
Dopo aver realizzato il primo prototipo ho ricominciato con alcune migliorie al design. Uno dei miei colleghi del team di Elettronica ha progettato un circuito personalizzato per azionare i motori e ci sono sensori magnetici che aiutano a rilevare la posizione (indicizzati dai magneti inseriti a pressione nei binari).
Tutti i componenti del modello hanno numeri di parte, la maggior parte proviene da McMaster Carr o DigiKey. Questo è un design molto migliore perché evita il problema del racking dovuto al peso della guida quando è completamente esteso e perché l'indicizzazione del sensore magnetico garantisce la posizione corretta ogni volta che i motori si muovono.
Assemblaggio completo di Fusion 360:
Passaggio 4: hardware
- Pannelli: alluminio 6061 di spessore 6 mm (presumibilmente andrebbe bene anche il compensato)
- Pannello numerico: compensato da 3 mm
- Arduino Uno:
- Scudo motore Adafruit:
- Motori passo-passo 5V: https://www.adafruit.com/products/858 (consiglierei di utilizzare motori a 12V invece di questi)
- Finecorsa (4):
- Interruttori momentanei (2):
Passaggio 5: elettronica e programmazione
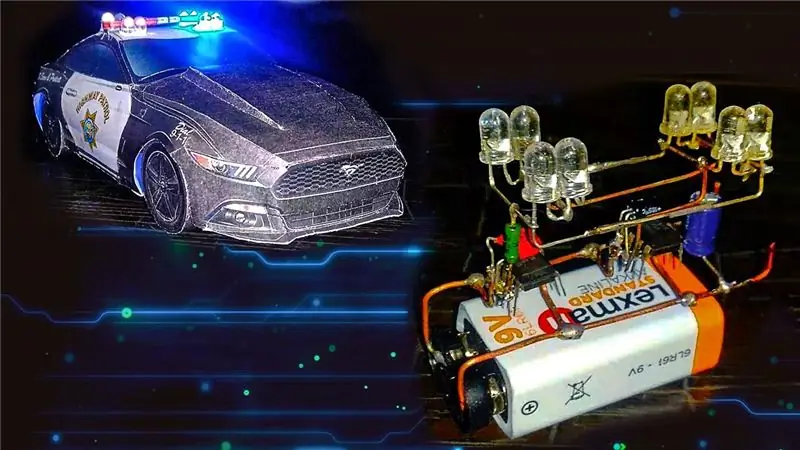

L'elettronica è tutta realizzata con un Arduino Uno e un Adafruit Motor Shield.
Ecco l'idea di base di come voglio che funzioni:
- Quando l'unità viene accesa, gli stepper fanno tornare indietro i rack fino a quando non vengono attivati i finecorsa sul lato sinistro. Questo imposta la posizione a zero. Gli stepper quindi fanno avanzare i rack finché 1 non è centrato sul pannello delle ore e 00 è centrato sul pannello dei minuti.
- Una volta centrati l'ora e i minuti, le rastrelliere avanzano nel tempo. Un movimento di posizione completa in basso alla massima velocità ogni 5 minuti e un movimento di posizione completa in alto ogni ora.
- Gli interruttori momentanei (pin 6-7) fanno avanzare i rack di una posizione (circa 147 passi), quindi continuano con il conteggio dell'orologio.
- I movimenti delle ore e dei minuti hanno contatori che rimandano le barre ai finecorsa di sinistra e le azzerano una volta trascorse le 12 e i minuti passati i 55.
Non mi è ancora chiaro cosa devo fare esattamente con il codice. Ho funzionato in teoria con il codice qui sotto che ha ricevuto da Randofo. Questo codice sposta la barra dei minuti in avanti di un passo ogni 200 ms (credo) una volta attivato uno dei finecorsa. Funziona, ma sono abbastanza rapidamente fuori dalla mia profondità oltre il lavoro di base che ho fatto qui. Questo sembra un problema abbastanza facile per un utente esperto di Arduino, ma faccio un progetto solo con uno forse una volta all'anno, e ogni volta che lo faccio, ho praticamente dimenticato tutto ciò che ho imparato nell'ultimo progetto.
/*************************************************************
Demo di Motor Shield Stepper di Randy Sarafan
Per ulteriori informazioni, vedere:
www.instructables.com/id/Arduino-Motor-Shi…
*************************************************************/
#include #include #include "utility/Adafruit_MS_PWMServoDriver.h"
// Crea l'oggetto scudo motore con l'indirizzo I2C predefinito
Adafruit_MotorShield AFMS = Adafruit_MotorShield(); // Oppure, crealo con un indirizzo I2C diverso (ad esempio per lo stacking) // Adafruit_MotorShield AFMS = Adafruit_MotorShield(0x61);
// Collega un motore passo-passo con 200 passi per giro (1,8 gradi)
// alla porta motore n. 2 (M3 e M4) Adafruit_StepperMotor *myMotor1 = AFMS.getStepper(300, 1); Adafruit_StepperMotor *myMotor2 = AFMS.getStepper(300, 2);
int delaylegnth = 7;
void setup() {
//avvia connessione seriale Serial.begin(9600); //configura il pin2 come input e abilita il resistore di pull-up interno pinMode(2, INPUT_PULLUP);
// Serial.begin(9600); // imposta la libreria seriale a 9600 bps
Serial.println("Prova passo passo!");
AFMS.begin(); // crea con la frequenza predefinita 1.6KHz
//AFMS.begin(1000); // OPPURE con una frequenza diversa, diciamo 1KHz myMotor1->setSpeed(100); // 10 giri al minuto }
ciclo vuoto(){
//legge il valore del pulsante in una variabile int sensorVal = digitalRead(2); sensoreVal == BASSO; int ritardoL = 200; if (sensorVal == LOW) { Serial.println("Minuti ++"); //mioMotore1->passo(1640, INDIETRO, DOPPIO); for (int i=0; i step(147, BACKWARD, DOUBLE); //analogWrite(PWMpin, i); delay(delayL); } Serial.println("Ore ++"); myMotor1->step(1615, AVANTI, DOPPIO);
//myMotor2->step(1600, BACKWARD, DOUBLE);
myMotor2->step(220, AVANTI, DOPPIO); //ritardo(ritardoL); } altro {
//Serial.println("Passi a doppia bobina");
mioMotore1->passo(0, AVANTI, DOPPIO); mioMotore1->passo(0, INDIETRO, DOPPIO); } }
Passaggio 6: assemblare la base
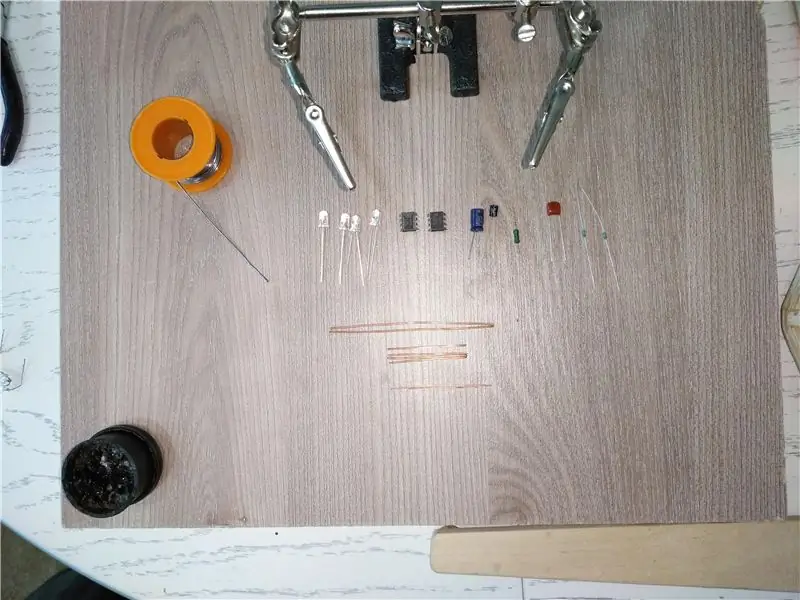
La base è composta da due piastre con distanziali che le tengono insieme. Le viti si fissano alla piastra attraverso fori filettati. Il numero di parte 6 su questo disegno è un'altra parte stampata in 3D: un distanziatore che è anche una base per il terminale di alimentazione per i motori passo-passo.
Passaggio 7: aggiungi interruttori momentanei
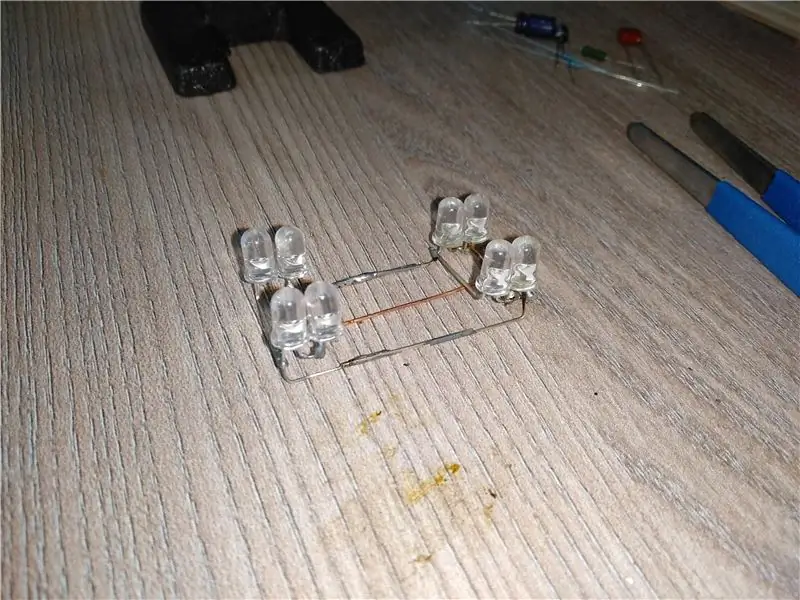
Gli interruttori momentanei, Arduino e gli interruttori di limite si fissano tutti alla piastra anteriore, quindi accedere all'elettronica per apportare modifiche è facile: basta togliere la piastra posteriore e puoi raggiungere tutto.
Passaggio 8: aggiungere la piastra di montaggio e i finecorsa
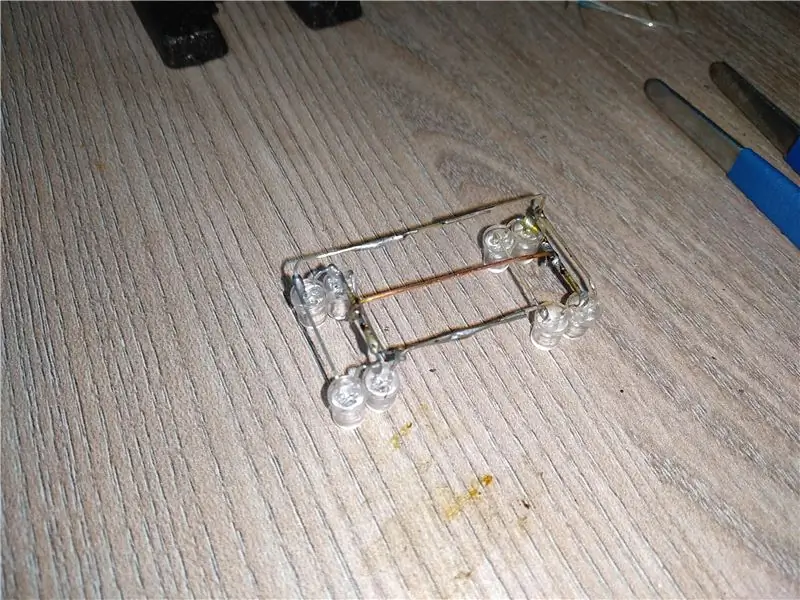
La piastra di montaggio contiene i finecorsa e il gruppo cuscinetti per le cremagliere. Questa parte può anche stare insieme durante la modifica dell'elettronica.
Passaggio 9: aggiungere motori passo-passo e ingranaggi
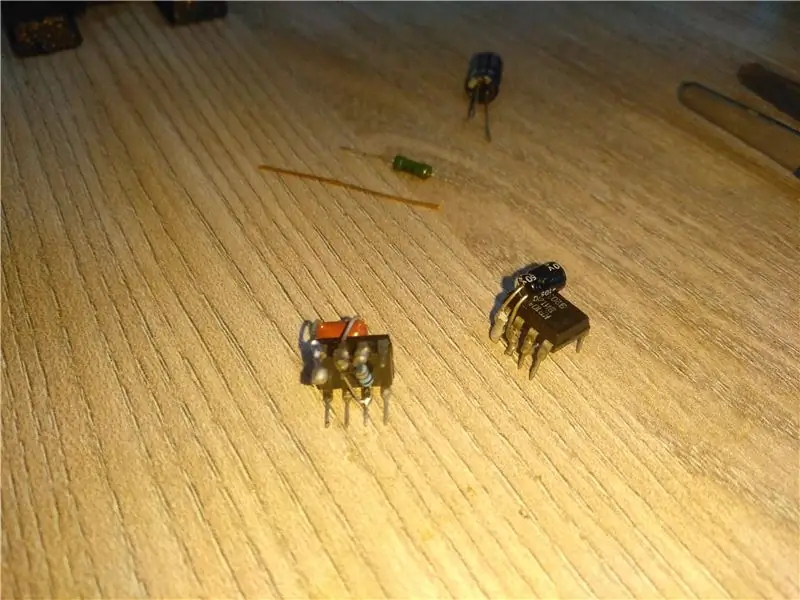
I motori passo-passo si fissano al pannello con viti M4 attraverso fori filettati e gli ingranaggi stampati in 3D sono inseriti a pressione sui montanti del motore. Ho usato un morsetto a grilletto per farli aderire e allineare.
Passaggio 10: aggiungere i rack
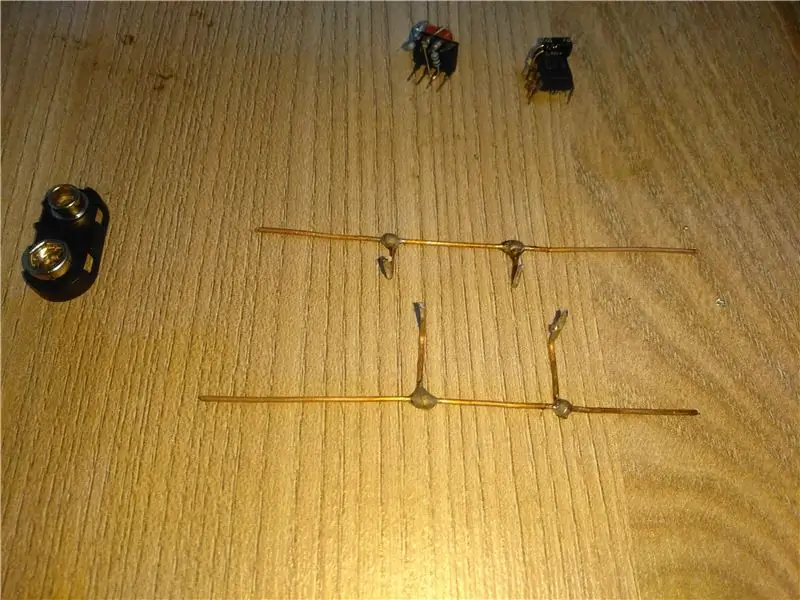
Le cremagliere hanno delle scanalature che si appoggiano sui due cuscinetti a sfera. C'è un piccolo spazio (0,1 mm) tra i cuscinetti e le fessure, che consente al rack di muoversi liberamente.
I cuscinetti sono inseriti tra distanziali stampati in 3D personalizzati per ottenere la misura esatta di cui avevo bisogno. C'è una piastra per rack sulla parte anteriore che funge da rondella che tiene i rack in posizione.
Passaggio 11: aggiungi le barre delle ore e dei minuti
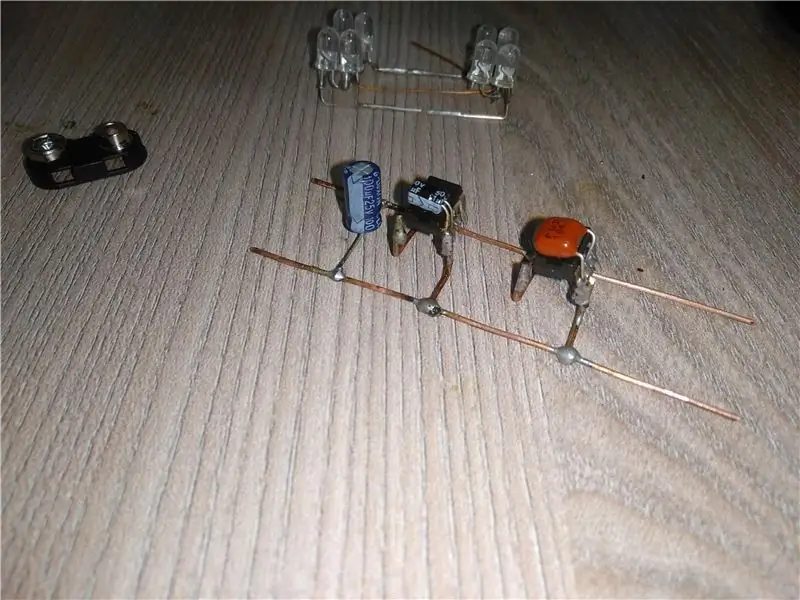
Le barre delle ore e dei minuti si fissano alle cremagliere con distanziali da 12 mm creando uno spazio che consente lo spazio tra le barre e le cremagliere.
Passaggio 12: aggiungi lenti di ingrandimento
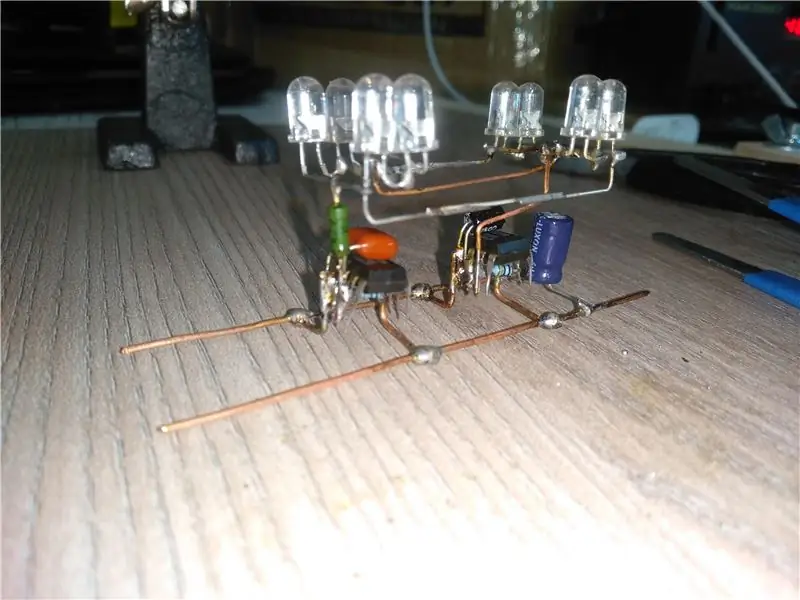
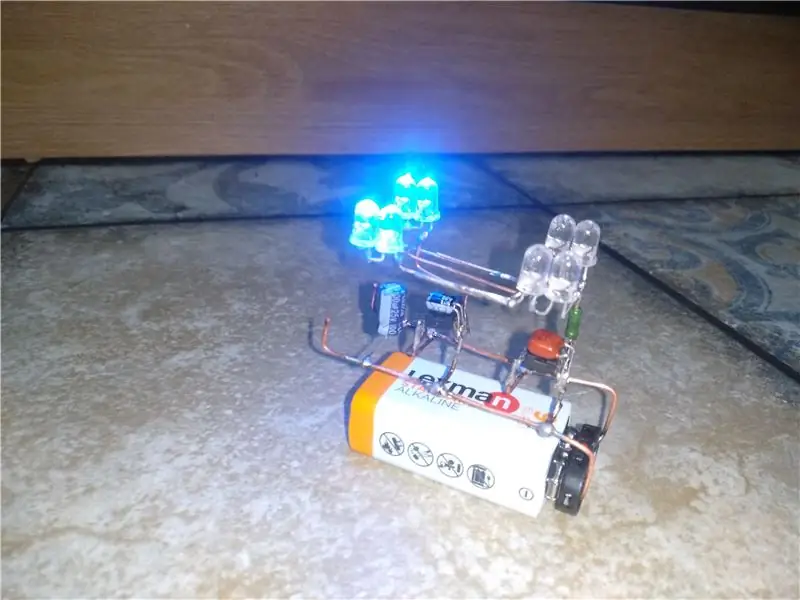
Le lenti d'ingrandimento sono lenti d'ingrandimento tascabili economiche che ho trovato su Amazon. Sono sfalsati dalla parte anteriore delle barre con distanziali da 25 mm.
Passaggio 13: lezioni apprese
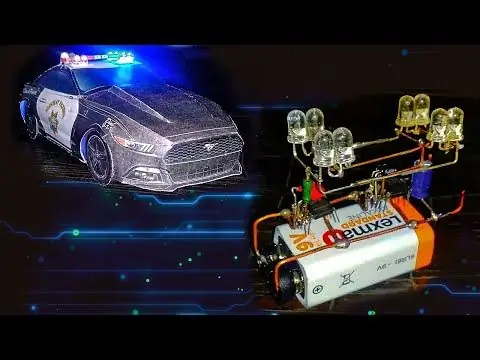
Ho imparato molto sul movimento lineare con questo progetto. La tolleranza che ho usato tra i cuscinetti e le fessure sui rack era un po' eccessiva, quindi se dovessi rifarlo penso che probabilmente lo taglierei a metà. Anche il divario ai lati delle lacune era un po' troppo grande.
I motori funzionano, ma più il cantilever si allunga, più devono lavorare. Probabilmente andrei con stepper da 12V invece di quelli da 5V.
Anche il gioco avrebbe dovuto essere maggiore, forse 0,25 mm. Gli ingranaggi stavano spingendo troppo forte sulle cremagliere con le prime marce che ho provato.
Consigliato:
Orologio di posizione "Weasley" con 4 lancette: 11 passi (con immagini)
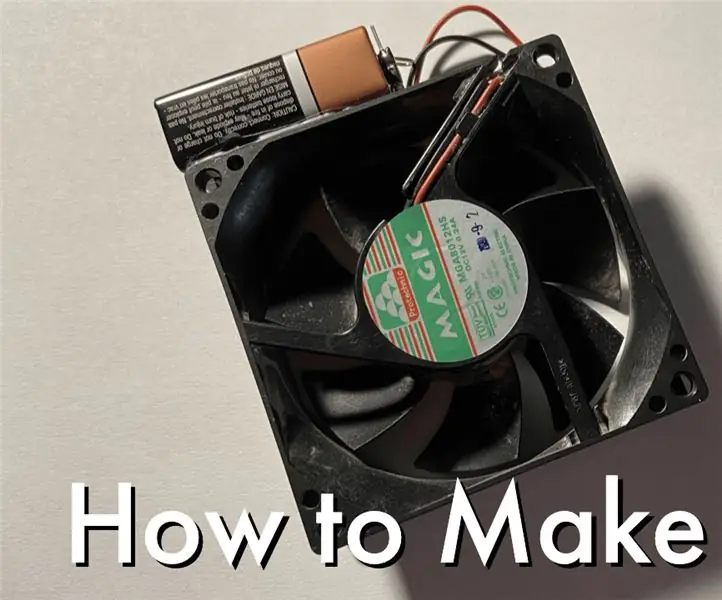
Orologio di posizione "Weasley" a 4 lancette: quindi, con un Raspberry Pi che funzionava da un po', volevo trovare un bel progetto che mi permettesse di sfruttarlo al meglio. Mi sono imbattuto in questo fantastico Instructable Build Your Own Weasley Location Clock di ppeters0502 e ho pensato che
Orologio per il pensionamento / Orologio con conteggio su/giù: 4 passaggi (con immagini)
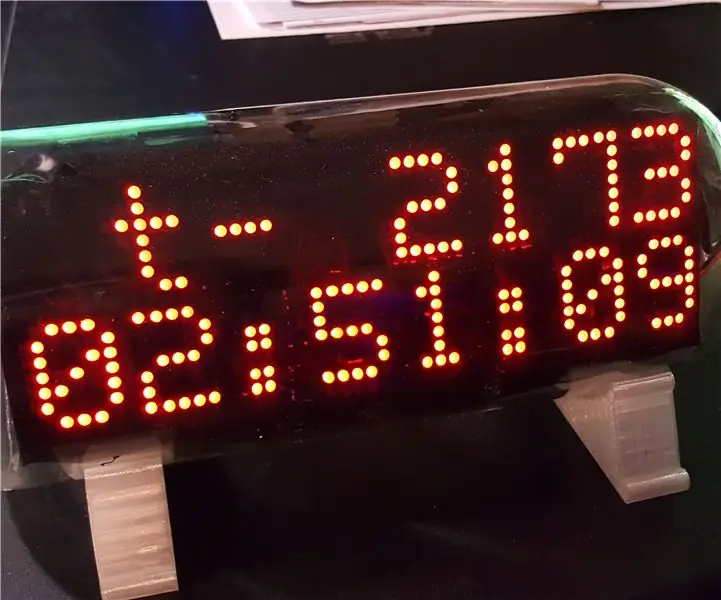
Orologio per la pensione / Orologio per conteggio su/giro: avevo alcuni di questi display a matrice di punti a LED 8x8 nel cassetto e stavo pensando a cosa farne. Ispirato da altre istruzioni, ho avuto l'idea di costruire un display per il conto alla rovescia per il conto alla rovescia per una data/ora futura e se il tempo target p
C51 Orologio elettronico a 4 bit - Orologio in legno: 15 passi (con immagini)
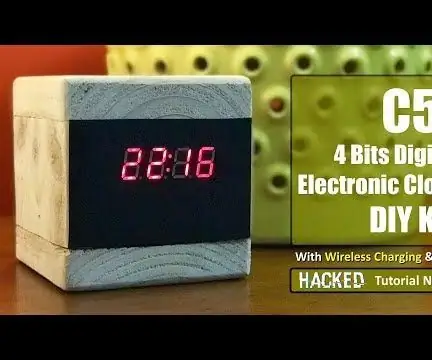
C51 Orologio elettronico a 4 bit - Orologio in legno: ho avuto un po' di tempo libero questo fine settimana, quindi sono andato avanti e ho assemblato questo orologio digitale elettronico fai-da-te a 4 bit da AU $ 2,40 che ho acquistato da AliExpress qualche tempo fa
Orologio lineare con Arduino + DS1307 + Neopixel: riutilizzare un po' di hardware.: 5 passaggi
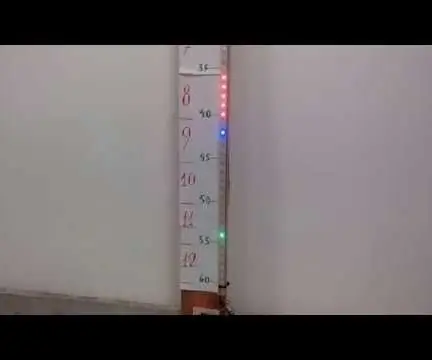
Orologio lineare con Arduino + DS1307 + Neopixel: riutilizzare un po' di hardware.: dai progetti precedenti mi erano rimasti un Arduino UNO e una striscia LED Neopixel e volevo fare qualcosa di diverso. Perché la striscia Neopixel ha 60 luci LED, pensata per usarla come un grande orologio. Per indicare le Ore viene utilizzato un segmento a 5 LED rossi (60 LED
Microdot - Orologio da polso con motivo a LED Orologio: 7 passaggi (con immagini)
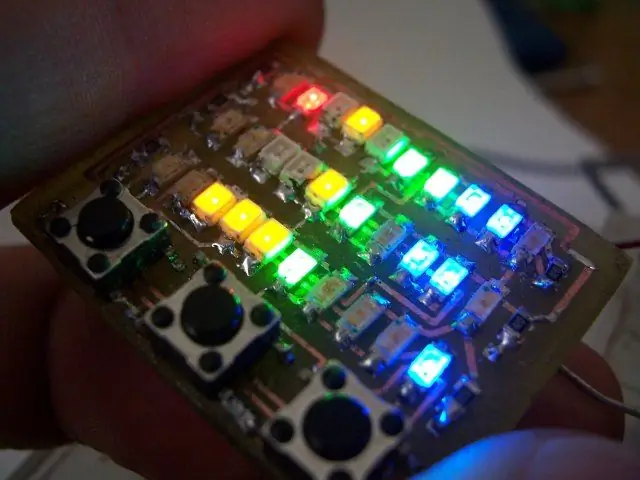
Microdot - Orologio da polso con motivo a LED: un'altra produzione RGB Sunset Productions! funzioni più applicabili a un dispositivo portatile. UN